Solution
Stamping or Punching Service
Masion offers Vertical Integration of Six Manufacturing Facilities. We’ve 17+ years of experience in sheet metal stamping. We are experts in customizing Precision Stamping Parts, Components, and Assemblies. Besides this,
● Produce over 7 Million Precision Stamped Parts Annually
● Have assembly Capability of Integrating Plastic, and Other Components with Stamping Parts.
● Self-design and Manufacture Stamping Dies (Including Progressive Dies and Compound Dies, etc.)
● Provide Rationalized Design Suggestions and Guidance for Stamped Parts.



+86-18969433502

sales@sheetmetalmasion.com
Masion - Offering the Finest Sheet Metal Stamping Manufacturing in China
Masion has 17+ years of experience in stamping. We are masters of OEM manufacturing complex metal precision stamping services. Besides this, we produce other assembly parts. Masion provides custom designing solutions to all sizes of clients. We also have worked with numerous automotive OEMs. They may include LiXiang, Tesla, etc. We independently design and manufacture metal precision stamping dies in our factory. Our facility has professional stamping die craftsmen, precision wire-cutting equipment, CNC machining centers, milling machines, and other high-precision equipment. Additionally, we maintain strict control over stamping die design and the quality of precision stamping parts. Besides this, we are also equipped with injection molding machines, material feeding robots, and spot welding robots,
Sheet Metal Stamping Solutions
Masion gives precise stamping parts services. So, we assist you in the design of stamped components and producing high-quality stamped parts based on your requirements. Masion is equipped with advanced machinery, It may include CNC automatic stamping presses, automatic welding robots, and robotic feeding systems. So, our intelligent facilities guarantee efficient and precise production. Besides this, our team comprises skilled designers, engineers, and mechanics. They ensure meeting the production deadlines and quality standards. We also meet the blueprint specifications for every precision-stamped part.
With 17+ years of experience, we are capable of handling various materials. These may include stainless steel, aluminum, brass, copper, titanium alloys, etc. Moreover, we can work with maximum thicknesses of up to 20mm. Additionally, we possess the capability for in-house metal stamping design. For this, we use advanced metal stamping dies such as Progressive Dies and Compound Dies.
Besides the initial manufacturing of stamped parts. We provide secondary processing services. I.e. riveting, bending, laser cutting, and various surface treatments. These surface treatment options may include electrostatic spraying, polishing, brushing, and silk screening. Below is a detailed list of the services we provide:
Materials
– Aluminum
A1100P-O,A1050P,AL2024, A5052H32P,AL5083, AL6061T6,AL6063T5, AL7075, AL1050, AL1060
– Carbon Steel
(SPCC, CRS, SAPH440, SPCD, SPCE)
– Stainless Steel
(SUS301, SUS302, SUS303, SUS304, SUS316, SUS420, SUS430)
– Cold Galvanized Steel
Q195, Q215, Q235, Q255, Q275
– Brass
C28000, C27400, C27000, C26800
– Copper
C1100, C1020, C1221
– Titanium
TC4, TA1, TA2
Stamping Dies
● Compound Dies
● Progressive Dies
● Simple Stamping Dies
● Combination
● Compound Dies
● Progressive Dies
● Simple Stamping Dies
● Combination
Thickness
0.1mm-20mm
Secondary Processes
● Assembly Services
● TIG and MIG Welding
● CNC Sheet Metal Bending
● Riveting
● PEM
● Laser Cutting
● Robotic Welding
● Manual Spot Welding
● Laser Welding
Stamping Presses
Total 75 machines
● 1 unit of 500 tons,
● 1 unit of 400 tons,
● 5 units of 250 tons,
● 1 unit of 200 tons,
● 12 units of 160 tons,
● 10 units of 110 tons,
● 25 units of 80 tons,
● 14 units of 60 tons,
● 3 units of 45 tons,
● 2 units of hydraulic presses.
Additionally, there are 20 robots for automatic feeding.
Surface Finish
● Powder Coating
● Anodizing
● Electroplating
● Trivalent Zinc Plating
● Hot-Dip Galvanizing
● Passivation
● QPQ (Quench-Polish-Quench)
● Dacromet Coating
● Sandblasting
● Polishing
● Silk Screening
● Phosphating
● Baking Paint
● Heat Treatment
● Electrophoretic Coating (E-Coating)
● Physical Vapor Deposition Coating (PVD Coating)
Why Choose Our Custom Sheet Metal Stamping
Masion provides top-quality sheet metal stamping manufacturing services in China. We’re an ISO16949-certified enterprise. We are experts in dealing with multiple automotive OEMs, i.e. Geely, Lixiang Auto, and Tesla. Since 2007, we have been dedicated to providing technical support services for precision stamping parts at various stages of customer projects. So, if you’re looking for a reliable supplier for complex precision stamping parts. Or if you want to change your stamping parts supplier. You can directly contact us. We will help you deal with all the matters effectively. As a trusted custom metal stamping supplier, we are committed to producing various complex precision stamping parts with scalable production capabilities. Here are the reasons to choose us:
1. Quality Management System
Masion has ISO16949 and ISO9001 quality management certifications. So, we can assist customers in getting certifications, i.e. AS9100 and NIST 800-171. We consistently consider quality as our mission.
2. In-house DFM and Mold Design:
Masion has 6 manufacturing plants. So, we’re dedicated to designing and producing high-quality molds. Moreover, we have 20 experienced mold engineers. They are responsible for designing specialized molds. Besides this, we utilize a powerful ERP system to increase supplier control, cost control, and production lead time control.
3. Large Project Support:
We’ve years of experience in dealing with large projects. Moreover, we’ve collaborated with renowned clients such as Greely, Li Xiang Auto, Tesla, TUO PU, and XuSheng. Besides this, we have worked on rich design and have wide experience in production.
4. Material and Thickness Diversity:
We have extensive experience working using different materials. These may include stainless steel, aluminum, titanium, brass, copper, etc. They all will help meet diverse requirements. The thickness for material stamping ranges from 0.1mm to 20mm.
5. Comprehensive Processing Capability:
In addition, to producing precision stamping parts. Masion also provides secondary processing. It may include sheet metal bending, riveting, welding, and surface treatment. So, we’re your one-stop solution for stamping needs.
6. Flexible and Adaptive Solutions:
We have clients that need bulk orders and some clients with small orders. Our flexibility and adaptability can help you meet any project requirements.
7. Vertical Integration:
We use all processes, i.e. welding, riveting, bending, laser cutting, assembly, surface treatment, etc. It gives us better control over costs. Moreover, it provides cost-effective production solutions.
8. Advanced Stamping Equipment:
Masion is equipped with China’s most advanced machinery. Moreover, we can produce high-precision stamping parts with exceptional accuracy. It makes us able to handle different complex projects.
9. Progressive Mold Monitoring:
We generally use mold monitors to detect the stamping parts. It helps us deal with producing large quantities with precision. This protects the molds from damage.


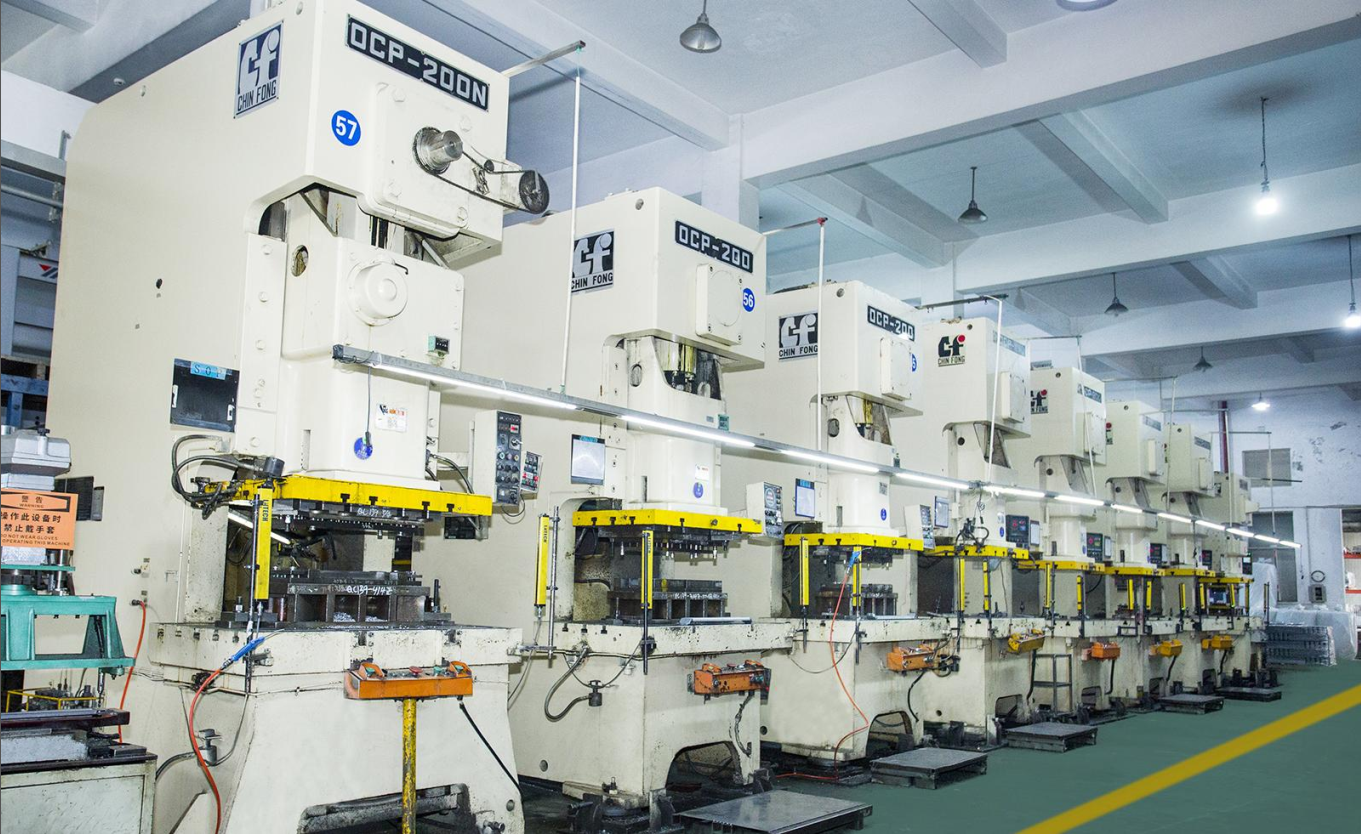
Multiple Dies Options for Precision Stamping Parts
Masion independently designs and manufactures Precision Stamping Dies. It may include progressive dies and compound dies. Although we also use single dies, that is not the main focus of what we want to introduce. So, below is a brief outline of the differences between these two types of dies we offer.
Structural Principle: A single station with multiple stamping processes. It can complete processes like stamping and blanking within the die cavity. However, it cannot simultaneously perform multiple processes like bending and curling, which require additional molds. Moreover, Compound dies are commonly used for the stamping of simple-designed parts. They work surprisingly well with medium to small-scale production.
Application: Compound dies work for relatively simple and smaller stamped parts. These parts may include washers and gaskets. Moreover, they perform a single stamping operation for processes like blanking or bending.
Production Efficiency: A single mold station performs multiple stamping actions. However, it cannot simultaneously fulfill the requirements of multiple stamping processes for a single part. Therefore, it works well for small-scale stamping. Its efficiency is lower compared to progressive dies.
The complexity of the Mold: The structure is simpler, with only one station for processes, i.e. blanking or bending. This simplicity lowers costs and less time for design and production.
Compound Dies:
Structural Principle: Multi-station molds mainly comprised of various stamping stations. These stations may help complete the entire stamping process within a die cavity. These processes include blanking, stamping, bending, shearing, drawing, curling, threading, etc. It is commonly used for continuous stamping. So, it is suitable for large-scale production and compatible with automatic punch press processing.
Application: Progressive dies are suitable for producing large quantities of identical stamped parts. Because they’re a continuous process. They have wide applications in the electronics industry such as connectors, terminals, and plugs.
Production Efficiency: The design of multi-station molds enables the efficient completion of various stamping processes. Moreover, it significantly increases the production efficiency.
The complexity of the Mold: Progressive dies with more stations are more complex. They require precision equipment for manufacturing. On the other hand, the design and production demands higher costs and time.
Progressive Dies
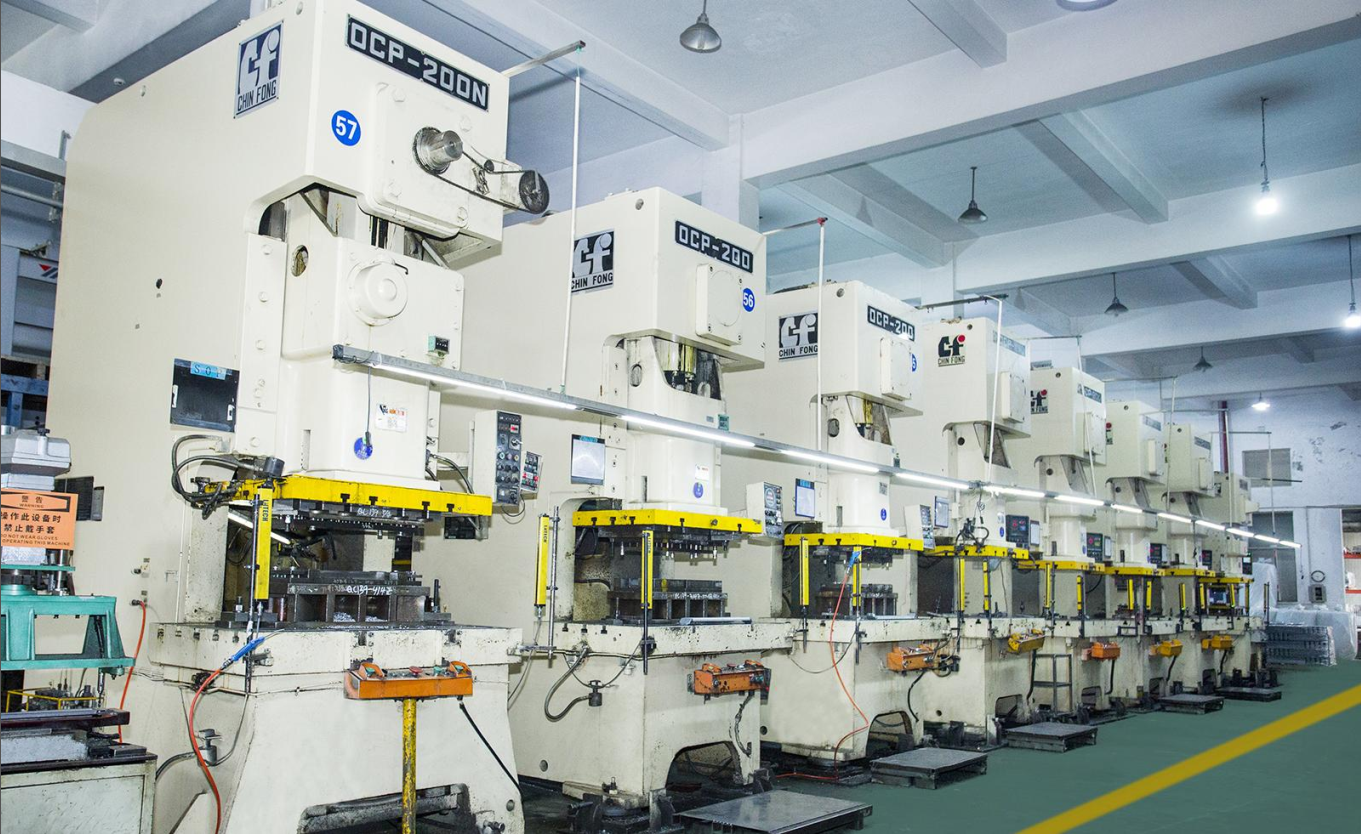
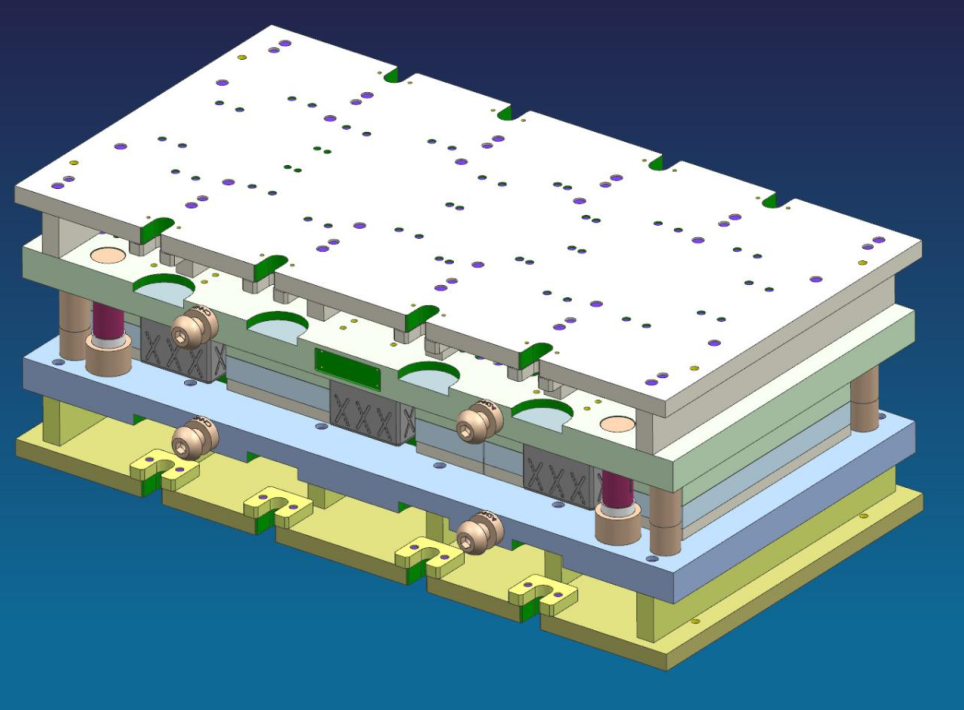
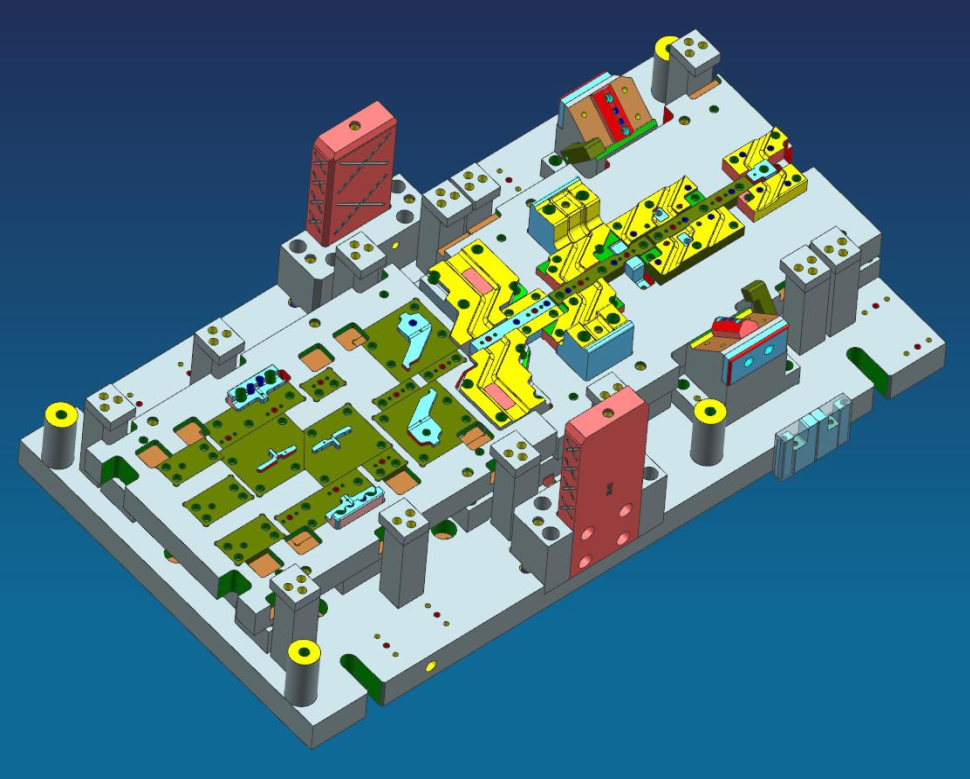
Certificate of Precision Stamping Parts
● ISO9001 Quality Management System
● ISO14001 Environment Management System Certification.
● TS16949 Automotive Industry Quality Management System
● FSC Forest Stewardship Council
● Patent 47 patents of invention
● CE CONFORMITE EUROPEENNE(As you need we could apply)
● RoHS Restriction of Hazardous Substances(As you need we could apply)
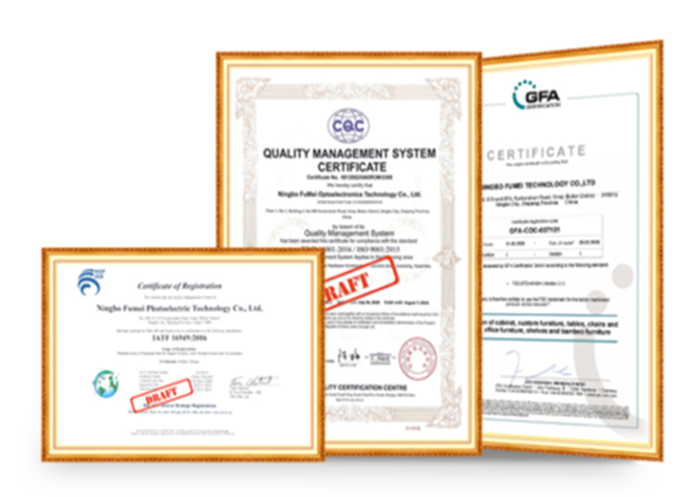
Explore our Precision Stamping Parts Gallery
Diverse Applications of Precision Stamping in Industries
Precision-stamped parts have a wide scope of applications in multiple industries. I.e. automotive industry, aviation industry, defense industry, maritime industry, and other high-end industries. Moreover, precision-stamped parts are generally found in everyday life in industries like telecommunications, robotics, fitness equipment, construction, machinery, consumer goods, and more. Below are some common applications for precision stamped parts in these industries.
● Hull exterior panels, keel, bow, stern
● Deck plates, hatch structures, deck supports
● Interior bulkheads, cabin structures, and compartmental partitions
● Deck equipment supports
● Hatch and window frames
● Oil tanks, cargo holds
● Propulsion system components, propellers
● Oil rig platforms, wind power platforms
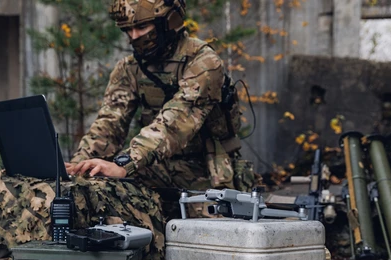
- Outer panels, inner doors, outer panels, roofs, front and rear bumpers
- Chassis frame, chassis support components • Hood, transmission system cover, engine assembly
- Suspension system support components, suspension arms
- Dashboard, inner door trim panels, seat structures
- Fuel tank casing and bracket
- Exhaust pipes and exhaust system support components
- Metal bracket supporting the vehicle’s battery
- Seat slides, hood inner panels, trunk inner and outer panels

- Aircraft fuselage outer panels, wings, tail wings, vertical tail fins
- Wings and wing beams
- Engine hood and casing
- Landing gear struts, hubs, tire brackets
- Aircraft doors and window frames
- Aircraft fuel tanks
- Supporting structures for engine accessories
- Seat structures, dashboard frames
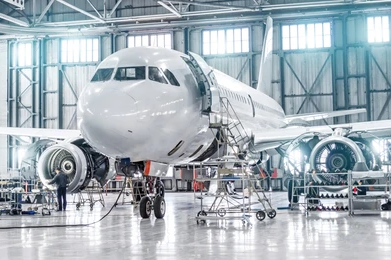
- Hull exterior panels, keel, bow, stern
- Deck plates, hatch structures, deck supports
- Interior bulkheads, cabin structures, and compartmental partitions
- Deck equipment supports
- Hatch and window frames
- Oil tanks, cargo holds
- Propulsion system components, propellers
- Oil rig platforms, wind power platforms
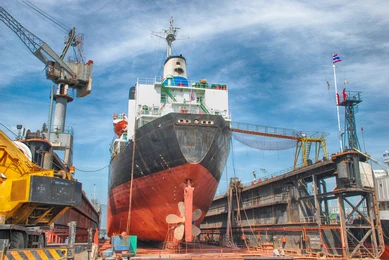
Other Manufacturing Solutions

Sheet Metal Assembly
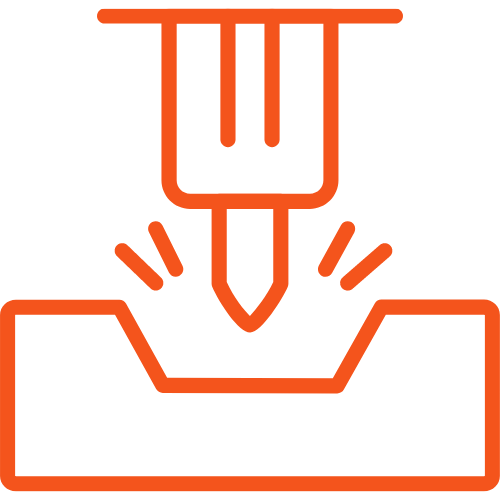
Metal Tube Fabrication

Laser Cutting
We provide sheet metal parts assembly services, suitable for large, small, various projects complex sheet metal parts assembly.
We’re offering custom processing service solutions for various circular, square, and special-shaped metal pipes
Our services cater to all custom solutions for precision laser cutting services for various materials and complex shapes.
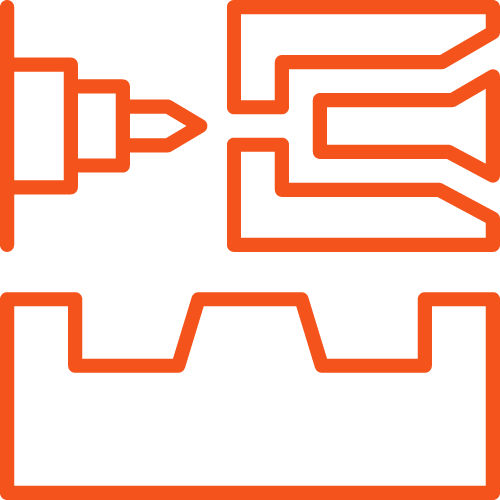
Plastic Injection

Stamping

Contract Manufacturing
Masion provides manufacturing solutions for assembly injection molding parts and supporting processing services.
We’re providing manufacturing solutions for progressive and compound molds, providing precision stamping parts production services
Masion provides vertical production and assembly solutions for sheet metal parts services
Resources
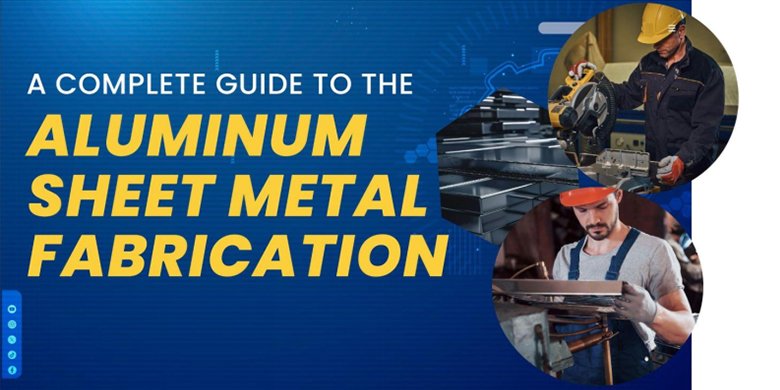
Aluminum sheet metal fabrication converts long sheets into specific shape. So, in this article, we will give you a complete guide to this process and its demands in the manufacturing industry.
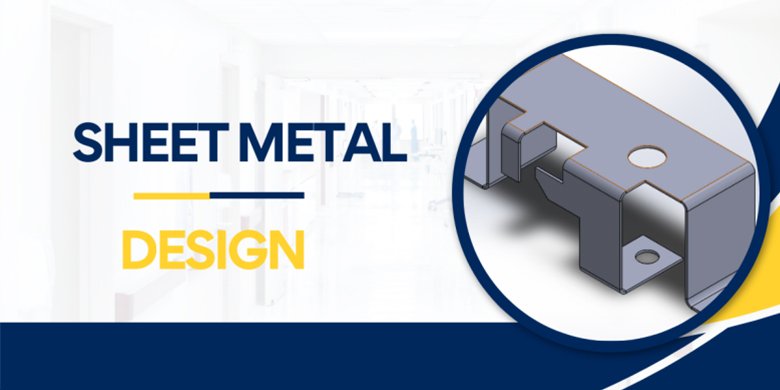
You can learn some tips for sheet metal design from this article. Understand the need, importance, and why the sheet metal design is crucial to play a key role in diverse industries.
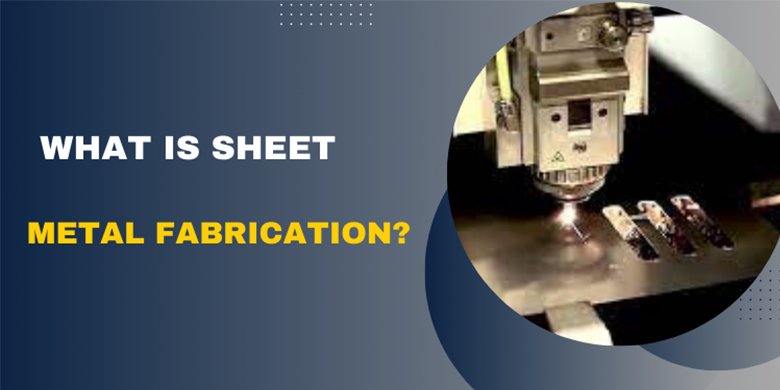
This guide allows you to create good sheet metal parts. We will start with the basics then discuss design best practices. Sounds exciting? Let’s delve in deeper to uncover facts.
FAQs
Q: Have you got certifications from ISO/TS 16949?
A: Yes, we have got ISO/TS 16949 certifications. We have collaborated with different automotive OEMs for the development of precision stamping components. Some of our partners include Ideal, Geely Automotive, Tesla, CRRC, etc.
Q: What advanced technologies do you use in precision stamping besides advanced equipment production to guarantee cost control?
A: We provide multiple technologies to address this issue
- Automation in Production
We are using robotic technologies, i.e. automated spot-welding robots, and robotic stamping feeders for efficient production. They help reduce the manufacturing cost of precision stamping components.
- Simulation and Modeling
We optimize the best production workflow through simulation and modeling software. They reduce defect rates and control the cost of precision stamping components.
- Real-time Monitoring
We apply real-time monitoring technology to track production data. So. It promptly identifies production issues. Besides this, it optimizes the manufacturing process and reduces defect rates. These advanced technologies help us effectively control the costs of precision stamping components.
Q: Do you offer customized precision stamping design services to meet specific customer demands?
A: Absolutely Yes, we offer customized precision stamping design and production services. Our team of expert designers can help customers optimize the design of stamping components to meet their specific needs.
Q: Do you provide on-site technical support or engineer services for large-scale precision stamping projects?
A: Absolutely Yes, we have a professional technical team for large-scale precision stamping projects. We typically assign technical engineers to work on-site with the customer’s project development department. The guarantee that the manufacturing process meets the specified requirements. Moreover, it helps maintain the quality of precision stamping components.
Q: How do you address fluctuations in the raw material supply chain during the production of precision stamping components to guarantee sustainability?
A: We follow these rules to address the fluctuations in the raw materials supply chain.
- Diverse Supplier Base:
We collaborate with major reputable material factories in China. These may include stainless steel plate factories, galvanized plate factories, and aluminum plate factories. Moreover, we work with multiple long-term suppliers to compare material prices. They guarantee flexibility to respond to unforeseen circumstances. Additionally, we avoid dependency on a single supply chain.
- Inventory Management:
Our cooperating customers typically have annual planned order purchases. We maintain an appropriate inventory of raw materials based on the customer’s annual order quantity. It is usually referred to as safety stock. This buffer helps us respond flexibly to market price fluctuations or supplier disruptions. So, it guarantees uninterrupted production.
Q: Does the quality of your precision stamping parts production comply with industry quality standards?
A: Yes, our precision stamping parts are strictly processed by relevant industry standards. Below are some of the standards and specifications we adhere to:
- ISO9001 Quality Management System:
Our precision stamping parts production process strictly follows the ISO 9001 Quality Management System. We track raw materials through a material procurement management system. Besides this, we conduct regular 6S environmental monitoring. It helps us clean and orderly production environment. We provide regular employee training. So, our employees get a better understanding and compliance with the requirements of the quality management system. Additionally, we create and properly store relevant production process documents. We also regularly track inspection reports for continuous compliance with standards.
- ISO16949 Quality Management System:
We have obtained ISO16949 quality management certification. It helps us get a higher quality requirement on precision stamping parts. Besides this, ISO9001 increases error prevention. It adds error-proofing measures in tooling and molds. During the Advanced Product Quality Planning (APQP) phase, we conduct multiple product validations. They guarantee precision stamping parts meet drawing and production requirements.
Furthermore, we can obtain additional quality control certifications based on customer requirements for different industries. They may include ISO13485 certification, AS9100 certification, NIST 800-171 certification, and more.
Q: How do you get consistency and stability of products during the production of precision stamping parts?
A: During the production of precision stamping parts, we take a series of measures for consistency and stability of product quality. We follow the following steps;
- Automated Production Line:
We use automated equipment, i.e. stamping and feeding robots, welding robots, and other intelligent devices. They can precisely control the stamping process. Moreover, they reduce the likelihood of human errors and guarantee quality compliance.
- Advanced Die Design:
We design and produce Progressive Dies and Compound Dies in-house. They guarantee the precision of the molds. Moreover, they help us meet strict dimensional requirements for precision stamping parts. This strategy maintains product consistency and reduces production errors.
- Regular Equipment Maintenance:
We conduct regular maintenance on stamping equipment. We use responsible personnel signing off on maintenance records. This helps us avoid equipment failures. Moreover, it prevents production interruptions and ultimately increases production stability.
- Real-time Monitoring:
Masion tracks key data of stamped parts to identify and correct issues promptly. We use real-time monitoring and data analysis of the stamping process. So, it confirms the stability of product quality.
- Strict Quality Control Procedures:
We strictly adhere to the content of the ISO16949 Quality Management System. Our new projects for precision stamping parts undergo Advanced Product Quality Planning (APQP) and Failure Mode and Effects Analysis (FMEA) stages. So, once testing is successful, we move on to the Production Part Approval Process (PPAP) stage. We implement quality control during the testing phase. These may include initial inspection, in-process inspection, and final product inspection. Only stamped parts that pass all inspections are deemed qualified products.
- Employee Training and Skill Development:
Precision stamping parts require highly skilled employees. Therefore, we have strict controls over employee skills. It only selects those with proficient operational skills who can take up positions. We provide systematic skill training for new employees. They can assess their skills during the process continuously. Moreover, it allows them to continue operations only if they pass the assessments.
- Customized Special Inspection Fixtures:
Masion provides services to customize specific product inspection fixtures. It is totally according to the inspection standards of precision stamping parts. That helps us get the consistency of dimensional inspections.
Q: Do you have an independent quality control team responsible for overseeing and improving quality issues in the production process of precision stamping parts?
A: Absolutely Yes, our company has a dedicated quality management team. It mainly consists of 14 members. This team is responsible for supervising, tracking, and improving quality issues in the production process of precision stamping parts. Moreover, it meets high-quality standards. Here are some of their responsibilities:
- Establishing Quality Standards:
The quality department is generally responsible for document customization. It helps in standardizing and recording the quality management system. This includes the Quality Manual, procedure documents, work instructions, inspection standards and specifications, record forms, calibration records, employee training records, non-conforming product handling records, and more.
- Performing Quality Checks and Testing
We conduct initial sample inspections of precision stamping parts and record the inspection results. During the stamping process, regular inspections are carried out. We collect relevant data and record it. We conduct thickness checks on the coating of spray-coated stamped parts. It guarantees compliance with specified requirements. Finally, comprehensive inspections are conducted on the finished stamped parts. It helps meet their quality high standards.
- Regularly Auditing the Production Process:
Our quality department conducts regular audits of the entire production process. They review the daily production plan. So, it aligns with customer order numbers. Moreover, they inspect the production site. It verifies if the production of precision stamping parts is consistent with the plan. If any inconsistencies are found, i.e. production dates exceeding delivery times or deviations from the production plan. We take corrective actions. They also audit the man-machine-material-method-environment regularly. It is usually done to identify any discrepancies. Performance reviews of the production process are conducted, analyzing completion rates. Moreover, it manufactures qualification rates along with corrective actions for any non-compliance.
- Providing Regular Employee Training:
We regularly train employees about basic stamping processes, equipment tool usage, and maintenance. We teach them about material selection and usage in stamping, press operation and safety precautions, mold installation and removal, equipment operation training, process parameter adjustment and control, and common issues and resolutions in the stamping process. Moreover, our training is also based on product dimension and shape measurement and inspection, and analysis and solutions for quality issues in the stamping process.
- Implementing Error-Prevention Measures
Our team takes error-prevention measures. They may include first-piece inspections. It helps production to proceed only when the inspection is successful. Moreover, we conduct Material inspections. They prevent us from using the wrong materials. Besides this, we carry out Inspections of stamping molds. They check if limit columns are correctly installed and if molds are fully closed during stamping.
Q: Can you use high-speed stamping to process precision stamping parts?
A: We manufacture progressive and compound dies in-house. Besides this, we have more than 10 sets of high-speed stamping equipment. We can confidently handle high-speed stamping for automotive parts or other precision stamping projects. So, you can trust us with your precision stamping part projects.
Q: Do you have the capability to design and manufacture progressive dies?
A: Absolutely yes. We have over 20 mold engineers and a well-established mold development and manufacturing chain. It consists of advanced CNC precision wire EDM, CNC precision turning centers, EDM machines, precision grinding machines, and other equipment. Our in-house mold development capabilities are at a leading level in the domestic industry. Moreover, we can assist in designing and manufacturing progressive dies and arrange production. So, it helps us save time and costs for your precision stamping part production.
Q: What confidentiality measures do you have for new precision stamping projects?
We take the following measures;
1. Technical Measures
To make sure of technical measures, we are opting for the following strategies
- Encryption Technology: We use encrypted documents, emails, communications, and other relevant information for new precision stamping projects. They help us avoid unauthorized access and information theft.
- Access Control: We create a strict access control management system. They restrict employees from accessing only project information relevant to their job responsibilities. Moreover, they guarantee that only authorized personnel can access the data.
- Data Backup: We regularly perform data backups. They help us take appropriate measures. Besides this, it provides the security of backup data. So, it prevents data loss or leaks.
2. Management Measures
We are taking the following management measures;
- Build a Confidentiality Responsibility System: We Clearly define employees’ confidentiality obligations and responsibilities. It guarantees that employees fully understand and comply with the confidentiality system.
- Project Team Record Management: We record and manage individuals involved in the project. Besides this, we clearly define their permissions and responsibilities and conduct information clearance and permission revocation for departing personnel.
- Monitoring and Auditing: We create information monitoring and auditing mechanisms. They supervise employee behavior. Moreover, it identifies abnormal situations and takes corresponding measures.
Legal Measures
We take legal measures using the following strategy.
Sign Confidentiality Agreements: We first sign a confidentiality agreement with project partners, suppliers, and employees. It clearly defines the confidentiality obligations and responsibilities of both parties for leaking project information and getting legal responsibilities accordingly.
Intellectual Property Protection: We make sure to protect relevant rights. They may include patents, trademarks, and copyrights. It eventually safeguards the technological and innovative aspects of the project under legal protection.
Accountability Mechanism: We make a mechanism to hold individuals accountable for violating the confidentiality system. Besides this we implement penalties.