Everything You Must Know About Metal Sandblasting
Table of Contents
ToggleMetal sandblasting is a process, in the world to achieve a smooth and flawless surface finish on metal parts. Modern blasting techniques have made this task easier with methods to clean and prepare metal surfaces. Metal sandblasting in particular has revolutionized the way metals are cleaned by enhancing texture and mechanical properties.
What is Bead Blasting Processing?
Metal sandblasting is a used method that involves cleaning, preparing and deburring metal surfaces using pressure abrasive particles like sand. While sand is commonly used other materials are also employed for their ability to clean and deburr metal surfaces effectively without posing health risks. Sandblasting is commonly used for purposes, such, as removing corrosion, rust, grease, oil and deburring. It is also employed to metal surfaces for welding, coating and painting. This technique not enhances the look of metal surfaces. Also improves their overall properties.
In metal sandblasting, abrasive particles and compressed air are used to clean and prepare the target metal surface. Initially a compressor generates pressurized air ranging from 30 to 100 psi. This compressed air is then carefully introduced into the stream using a hopper or valve. The focused stream of compressed air is directed at the metal surface through a blasting nozzle allowing abrasive particles to strike the surface at velocity for thorough cleaning and preparation. Following this process the metal surface is primed for treatments like painting and welding coating. To maintain safety and cleanliness during sandblasting operations any generated dust can be collected using a vacuum or dust collector.
What Role does Metal Sandblasting Play, in Enhancing Processes?
Metal sandblasting has gained importance in today’s era within industrial settings. Let’s delve into its significance, in depth.
Preparation of metal surfaces;
Metal sandblasting plays a role in preparing metal surfaces. By utilizing this technique the metal is treated to eliminate debris particles and impurities like corrosion and rust resulting in a surface that’s ready for various treatments such as painting and welding.
Improving durability and longevity;
The process of metal sandblasting is highly valuable as it enhances the durability of treated metals. By removing particles from the surface it shields the metal from damage ultimately extending its lifespan and strengthening components.
Achieving a finish;
Metal sandblasting holds importance in achieving a polished surface finish. Smoothing out edges on targeted metals not enhances their visual appeal but also contributes to an attractive appearance overall.
Efficient surface cleaning;
Metal sandblasting stands out as a preferred method for swiftly cleaning a range of metals. It effectively eliminates dirt, rust and corrosion without causing any harm, to the metal surface. Cleaned parts not function better. Also have an extended functional life span.
Enhancing Adhesion;
Using metal sandblasting can improve how well adhesive particles stick to a metal surface. The clean surface allows paints and adhesives to bond effectively creating a finish after coating, painting or welding.
Cost Effective and Versatile;
Metal sandblasting can be used on types of metals. It is a cost effective option compared to other cleaning methods. Its versatility and affordability make it a popular choice, for applications.
Difference Between Shot Blasting and Sandblasting;
While shot blasting and sandblasting may sound similar they are techniques with differences in their medium and how the media is transported onto the surface. Shot blasting uses abrasive ‘shot’, like carbon grit or aluminum oxide whereas sandblasting uses sand as its medium.
On the other side metallic shots or gentle abrasives are typically used in sandblasting. However, gentle abrasives, like glass or organic media are often the choice. Silica sand has been an option in the past but its use has significantly declined due to health risks, particularly respiratory issues as awareness grows.
Regarding media transportation to the surface;
In surface preparation shot blasting and sandblasting employ methods of transporting media to the surface. Shot blasting utilizes a wheel for media transport propelling it directly onto the surface at speeds within a closed chamber under controlled conditions. On the hand sandblasting doesn’t involve a wheel; instead compressed air or water is commonly used as the medium, for directing high speed media onto the surface. However sandblasting operates at a speed compared to shot blasting.
Shot blasting and sandblasting are both methods, for surface preparation suitable for a variety of surfaces. They are commonly employed to surfaces for a range of materials based on their unique characteristics and needs.
How can you Select the Material for Sandblasting?
Types and choices of abrasives for sandblasting equipment
Abrasives
Abrasives utilized in sandblasting machines are categorized by gravity ranging from high to low. They fall into groups, including metal abrasives (such as steel sand, steel shot, steel wire cut shot) alumina (like corundum white corundum, black corundum, zirconium corundum, chromium corundum) silicon carbide (such as green silicon carbide, black silicon carbide, emery) glass sand, quartz sand, walnut sand and resin sand. Below is an overview of some used abrasives.
Metal Abrasives
Metal abrasives encompass steel sand, steel shot, steel wire cut shot—divided into carbon steel and stainless steel varieties—which are predominantly used as abrasives in both sandblasting machines and shot blasting machines. Stainless steel abrasives are less common due, to their cost.Stainless steel abrasives are commonly used for refining ferrous metal and alloy parts requiring an abrasive diameter of, about φ0.2~0.4mm.
Carbon Steel Abrasives
On the hand carbon steel abrasives are preferred for treating castings and structural parts made of carbon steel needing an abrasive diameter between φ0.6~1.2mm. Carbon steel abrasives are especially suitable for sandblasting machines utilized in sandblasting rooms. Details regarding the grade, particle size, mechanical properties and chemical composition of carbon steel abrasives can be found in the provided table.
Aluminum Oxides
Aluminum oxide (Al2O3) serves as the component in corundum which is categorized into artificial corundum types. Natural corundum consists of crystalline alumina while artificial corundum is predominantly used in the market today. The two common variants of corundum are brown and white corundum with granular sizes typically ranging from 12#, to 30#.
Brown corundum is crafted through a process involving iron filings and coke melted together in an electric arc furnace; white corundum is formed by melting aluminum oxide powder in a setting; other types of corundum incorporate varying levels of alumina.
During the process of melting additional oxides are introduced to create the desired content. These oxides are detailed below.
Brown Corundum
It is a type of abrasive made from iron filings and coke, as its ingredients. It is processed in an electric arc furnace at temperatures than 2000°C.
Its key chemical components include AL2O3, TiO2, SiO2 Fe2O3 among others. Known for its hardness toughness, sharp particles, potent grinding force, efficiency and resistance to temperatures.
Brown corundum serves as a notch refractory material. Its allure lies in its cost effectiveness; it boasts toughness than silicon carbide at a price point. Brown corundum stands out as the cost widely used artificial corundum abrasive. It offers hardness and cutting efficiency surpassing that of glass beads and quartz sand.
When utilized as a sandblasting abrasive brown corundum finds applications such as;
- Cutting silicon wafers;
- Removing adhesive from components;
- Treating mold surfaces for texture enhancement;
- Pre treating workpieces prior to electroplating and painting;
- Enhancing the appeal of crafts and gold jewelry, through atomized processing.
White corundum is crafted from top notch aluminum oxide powder undergoing smelting and crystallization in an electric arc furnace, at temperatures exceeding 2000°C to produce an abrasive. Its primary chemical components include AL2O3, Na2O, SiO2, CaO, MgO Fe2O3 among others. With a particle density of 3.95 3.97 g/cm3 and a bulk density of 1.59 1.97 g/cm3 this material boasts low toughness, exceptional purity, self sharpening properties and potent grinding capabilities.
Applications
This premium abrasive serves as a material for grinding and polishing purposes well as a top tier refractory material. Its applications range from precision grinding in devices to super precision grinding in the realms of electronics and precision instrumentation. Moreover it finds suitability in grinding tasks involving high carbon steel, high speed steel and various types of steel.
White corundum plays a role in sandblasting processes that mandate avoidance of iron powder residue. Notably versatile as a sandblasting agent its applications span across tasks such, as cutting silicon wafers and eliminating excess adhesive from electronic components.
Sand,
Sans also known as low aluminum corundum sand iron sand powder is a newly developed polishing material that undergoes crushing and classification using specialized equipment. It is crafted from three water type and one water type bauxite, which are subjected to high temperature smelting and cooling in an electric arc furnace.
Black corundum abrasive boasts composition, robust cutting capabilities, optimal toughness a hardness softness blend and excellent wear resistance ensuring high efficiency. Primarily utilized for sandblasting on steel, metal items, optical glass, bamboo products, wood items; it serves as an abrasive, for producing resin grinding wheels and emery cloths.
Zirconium Corundum
In essence zirconium corundum brick denotes sintered zirconium corundum brick formed through batching and shaping processes followed by firing at temperatures ranging from 1700 1750°C. These sintered bricks exhibit resistance to glass melt erosion with thermal shock resistance compared to fused zirconium corundum bricks. They find applications predominantly as linings in glass kilns and induction furnaces as slide rails, in steel heating furnaces.
Chrome Corundum
It is created by introducing 22% chromium into corundum and melting it in an electric arc furnace. It displays a hue, with a hardness slightly surpassing that of brown corundum, akin to white corundum.
The microhardness ranges from 2200 to 2300/mm2. Its toughness exceeds that of corundum. Falls slightly below that of brown corundum. This abrasive material is ideal for grinding high carbon steel, high speed steel and delicate components. Additionally it finds utility in grinding and polishing applications precision casting sand, spray materials, chemical catalyst carriers, specialized ceramics, advanced refractory materials, among others.
Silicon Carbide
It exists naturally as moissanite ( known as moissanite) albeit rarely found as a crystal. In settings silicon carbide (commonly referred to as carborundum) is utilized as a material. The inception of this mineral on a scale dates back to Edward G Achesons synthesis in the United States in 1891; subsequently discovered in Kimberley. Although traces have been detected in Kimberlite (also known as brecciated mica olivine) its mining value remains negligible due, to content. Presently all silicon carbide employed across industries is man made.
Silicon carbide is manufactured through a high temperature smelting process in a resistance furnace utilizing materials, like quartz sand, petroleum coke (or coal coke) and wood chips (the addition of salt is necessary when producing green silicon carbide). Currently the industrial production of silicon carbide in my country yields two variants;
Black Silicon Carbide and Green Silicon Carbide
Both types exhibit crystal structures with a gravity ranging from 3.20 to 3.25 and a microhardness between 2840, to 3320 kg/mm2.
1) The green silicon carbide contains a minimum of 99% silicon carbide with crystals that exhibit a shiny appearance. Its production process mirrors that of black silicon carbide. It utilizes materials of higher purity. Manufactured in a resistance furnace, at temperatures reaching around 2200°C, this type of silicon carbide boasts a hue and distinctive hexagonal crystal structure. With a Sic content compared to black silicon carbide its physical properties are akin to its counterpart. With slight differences in brittleness. Notably it excels in conductivity and semiconductor attributes.
2) The black silicon carbide comprises at 98.5% silicon carbide showcasing crystals that are deep black and lustrous in nature. Often referred to as moissanite silicon carbide stands out among oxide high tech refractory materials like C, N and B for its widespread usage and cost effectiveness. It is commonly known as emery sand or refractory sand.
3) Emery is categorized into two types; synthetic varieties.
Natural emery, also recognized as garnet is a mineral primarily used as a material produced through meticulous hydraulic screening processes along, with mechanical processing steps involving screening and classification.
The categorization consists of three groups; mesh, medium mesh and fine mesh. The meshes come in sizes, with particle sizes and shapes multi angular crystals, sharp edges and strong grinding capabilities.
Synthetic emery, also referred to as silicon carbide (SiC) is an abrasive produced by heating sand and a precise amount of carbon in a furnace. Typically it appears as colorless powdery particles with a density ranging from 3.06 to 3.20 g/cm³. It boasts a level of approximately 9.5 on the Mohs scale.
Which Materials are Suitable for Sandblasting?
Sandblasting can be performed on an array of materials. Lets explore materials that can have their surfaces prepared or cleaned using this method.
Metals;
Sandblasting metal is an used technique for cleaning and prepping types of metals. It efficiently eliminates debris particles, corrosion and rust from metals like aluminum and steel. Moreover it readies them for applications such as painting and welding while offering the flexibility to create textures and shapes.
Glass;
Glass surfaces are well suited for sandblasting as it allows for the etching of patterns and designs, on them.
Furthermore it aids in refining the glasss edges resulting in a polished look and enhancing the overall finish.
Plastic;
Similar, to metals plastic materials can benefit from sandblasting treatment. Sandblasting plays a role in cleansing. Prepping the surface of plastic by eliminating debris particles and previous coatings. This process readies the surface for coatings and surface enhancements.
Wood;
The method of sandblasting can also be applied to wood like with materials. It works to smoothen the woods surface and reduce roughness allowing for the creation of patterns and textures on the wood surface.
Sandblasting is a process which is versatile across the world and different materials such as stone, brick, concrete, etc., providing clean surfaces while stripping away old coatings to prepare them for fresh applications. This practice enhances the quality and appearance of these materials while boosting their durability and performance.
Techniques & Tips for Sandblasting;
Here are some techniques and tips for sandblasting;
Consider both the material of the surface being treated and the desired finish when selecting an appropriate abrasive for your project. Super fine silica sand is a choice as it cuts quickly can be recycled and preserves metal integrity – making it ideal, for auto restoration projects.
Safety Protocols;
Ensure you have on the safety equipment, such, as gloves, goggles and respirators and operate in a ventilated area. Sandblasting generates noise and dust particles. It’s vital to wear the right safety gear.
Surface Preparation;
Before starting the blasting process it is important to clean the surface to remove any impurities such as oil, grease or loose rust.
Technique
To achieve desired results it is crucial to maintain a distance and angle with the nozzle. Arrange the equipment according to needs and methods.
This involves adjusting pressure and choosing the abrasive materials. Glide the nozzle smoothly over the surface with overlapping strokes in each pass.
Take your time. No need to rush.
Opt for a material based on desired surface finish. Using an material might lead to undesirable results.
Dispose of waste produced during sandblasting with care to prevent contamination.
Equipment Configuration;
Adjust your sandblasting setup as, per the technique by tuning pressure settings, nozzle distance and choice of abrasive material.
To achieve the results when using fine silica sand it is recommended to employ a 3/32″ carbide nozzle and pressurized blasters set at, around 80 psi.
After carefully inspectection of sandblasting, the surface to ensure that the desired outcomes have been met so follow safety precautions by wearing gear and working in a well ventilated area for your own protection.
Dispose of waste and abrasive materials responsibly to minimize their impact.
Regular inspection and maintenance of sandblasting equipment are essential to ensure their long term functionality.
By following these tips and guidelines you can prioritize safety. Achieve sandblasting results. While expertise and experience are necessary for this process it plays a role, in restoration projects.
Various sandblasting techniques are commonly used based on needs. Dry Sandblasting is one technique where abrasive material is directed onto metal surfaces without water effectively removing scales, rust, corrosion, etc. resulting in an smooth finish.
Airless Sandblasting;
In sandblasting a high pressure system propels the material forward. This method is versatile and ideal for heavy duty tasks like removing coatings, rust and corrosion from metal surfaces.
Bead Blasting;
Bead blasting utilizes small glass beads as abrasives. This method is known for its ability to create finishes, on metal surfaces. It finds application in industries like automotive and aerospace.
The Technique of Soda Blasting ;
In this technique, we employs baking soda or other material such as sodium bicarbonate as a material. This eco friendly method efficiently cleans surfaces and prepares them for treatments.
Wet Abrasive Blasting;
In blasting water is utilized to encase the abrasive material during the process leading to reduced dust and spillage. The method also helps in collecting used blast media and loose particles from the surface offering an alternative, with lower blast media consumption.
Wheel Blasting;
Wheel blasting uses a wheel mechanism to propel materials onto surfaces. It is commonly employed in cleaning commercial structures providing a means of eliminating contaminants and preparing surfaces for further processing.
Micro abrasive Blasting;
The process of abrasive blasting involves using fine abrasive particles to meticulously clean and prep surfaces, with intricate details. It is particularly suited for handling workpieces that require a yet thorough cleaning approach.
There are metal sandblasting techniques to address different surface preparation requirements providing a range of options to achieve specific finishes and cleaning needs.
Summing Up
Metal sandblasting serves as a method for preparing, cleaning or etching metal surfaces across industries. It entails the use of air or a centrifugal wheel to propel materials like sand, steel shot or aluminum oxide at high velocities.
When performing metal sandblasting it is crucial to adhere to safety protocols by wearing protective equipment (PPE) such as respirators, goggles and gloves. Additionally operating in a ventilated environment can help minimize exposure, to dust particles.
Ensuring safety is crucial when sandblasting metals. This includes wearing gear such, as respirators, goggles and gloves and operating in a ventilated space to manage harmful dust. By using the tools, abrasive materials and safety precautions metal sandblasting can efficiently eliminate rust, paint and impurities from surfaces in preparation for painting, restoration or other finishing tasks. This method is vital for metalwork fabrication and repairs.
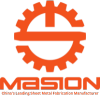
Send Your Inquiry Today



+86-18969433502

sales@sheetmetalmasion.com