Capability
Design for Manufacturability (DFM)
In general, the customers supply us with the basic design plans. They want us to manufacture their products, based on their designs. Nevertheless, some customers who work with contractors and builders do not have design drawings at the early stages. In such cases, they look to us for help in designing their parts. So, these descriptions will be discussed in detail with all the R&D engineers within our team and the manufacturing engineers. Especially those who would deeply investigate the application scenarios of the project and all the production features. We then give specific DFM (Design for Manufacturability) sheet metal to meet all the client requirements. We’re the leading supplier companies in China and provide design manufacturing services.
Many of our clients benefit from involving us in the mechanical design of their entire product. They use our DFM for sheet metal products. Here we assist in improvements on the manufacturability and reliability of the final products. Besides this, our team of experts controls the production costs and increases efficiency.



+86-18969433502

sales@sheetmetalmasion.com

Cost Reduction And Efficiency Improvement Design
With our DFM design support for sheet metal, you can count on our help in redesign. Besides this, we will help improve your current designs as well. This includes improving quality and increasing the production of sheet metal products. It also includes cutting the expenses on production. Also, manufacturing of the sheet metal in the company reduces lead time and provides high-quality product satisfaction.
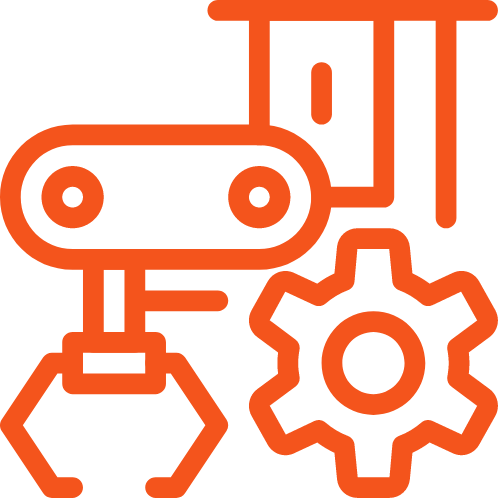
Inspection Error Proofing
The inspection aids that we use include inspection jigs and fixtures, calipers, micrometers, CMM, and go/no-go gauges while checking the dimensions of the designs. This makes the mass production of sheet metal parts possible. In this stage, extensive and huge production is made and deadly mistakes that can lead to poor quality of the final product are discouraged.
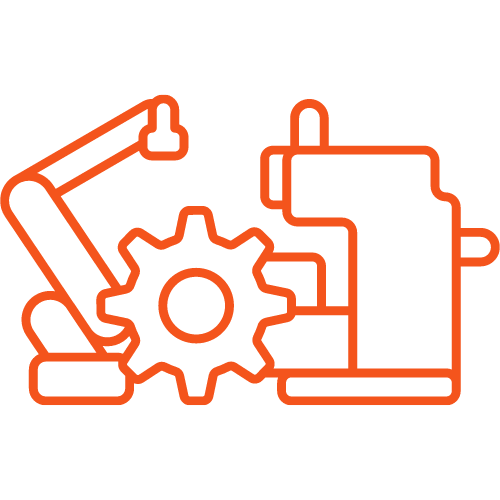
Product Design Localization
Working closely, we address the ability of the local Chinese Design and Supply Chain of materials, components, and other associated parts of sheet metal parts. So, they can meet the production requirements of our clients. This assists in attaining the optimum lead time and the most practical form of prices.
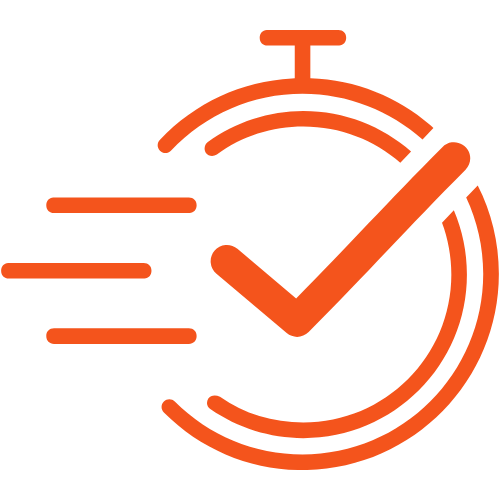
Product Reliability
Our main challenge is product quality. We focus on how to increase it and how to minimize the number of sheet metal part failures. Because this strategy will ultimately lead to customer returns. We always contact our clients to point out a design problem and work on its prevention. Some of the preventive measures that we give from our R&D department, manufacturing departments, and suppliers are in the following areas:
Bend relief is a depression on a particular given design, which aids in the bending process during manufacturing. When this need is not relieved, a metallic flange will get distorted. It will cause the material in use to tear. The rule applied in bend relief is its minimum value, i.e. the bend relief shall be equal to or greater than the inside radius of the bend.
Bend Relief
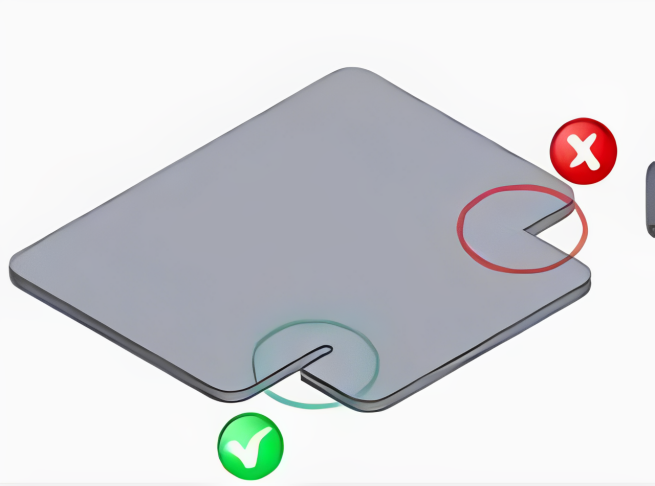
Any metal can get distortions because there is a tolerance-controlled distance between a hole and a bend. Every time designers will be on the bend, the distance between them should be 2 times or more the thickness of the metal. Thus, there will be negligible or no progression of the metal in the process which we call deformation.
Distance between a Hole and a Bend
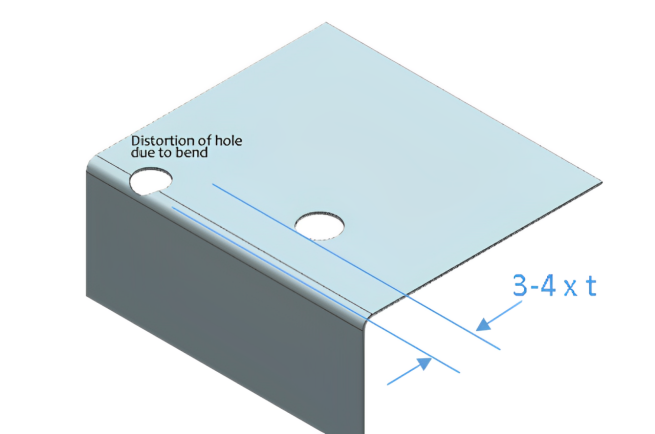
As it concerns installations, these should be well made to avoid any complications for the team. The objectives of DFM guidelines say that everything is in line and there is no wrong positioning. Consequently, anything that has been worked on will run efficiently.
Symmetric Optimization
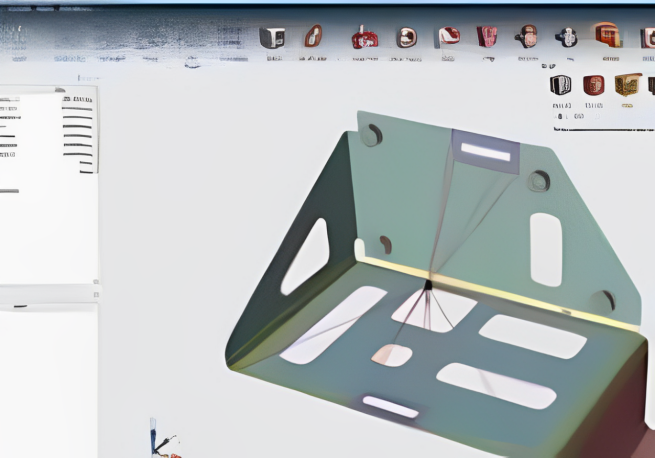
We closely adhere to modular piercing to fix the equipment. That is why we make it a point to improve the installation positions. So, no other problems in the future, arise regarding large-scale production. During the DFM process, we cannot tolerate errors. So, it becomes worse when manufacturing numerous parts simultaneously. While ensuring that all processes flow efficiently, the general productivity from the production process rises.
Modular Piercing
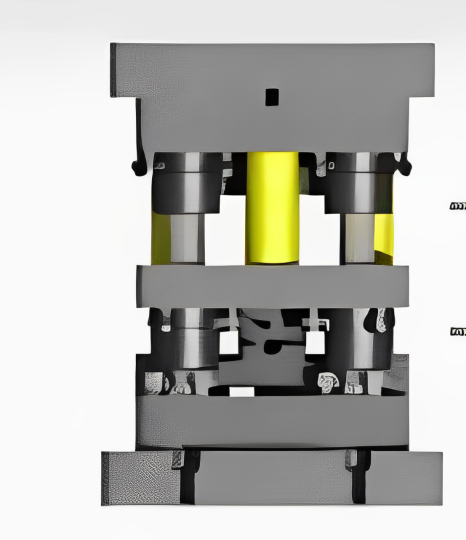
Concerning the mechanical properties of the structure, the weld groove should be created before welding. So, it can provide enough strength and high quality to the piece. You also end up with a relatively better-looking piece of work.
Generate Weld Groove
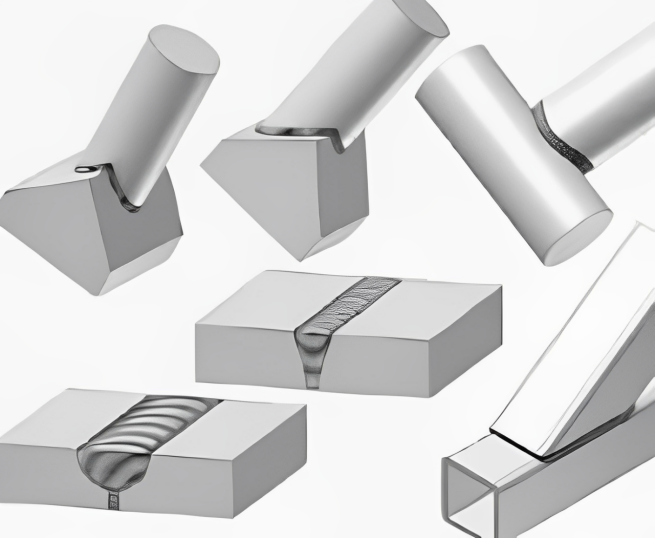
Checkout Our DFM Design Process for sheet metal
The design for manufacturing is often marked as DFM. It is one of the most significant facets of sheet metal design because it outlines if it can produce low-cost, high-efficiency, and high-quality sheet metal parts. Usually, the DFM design realizes the producibility of subsequent production. So, the manufacturing complexities of sheet metal products and the production processes can easily be simplified. With proper and comprehensive DFM design support, it is possible to help your sheet metal manufacturing projects substantially.
Concept Design: If you are unable to offer design drawings and only have a concept in your mind, based on your actual application fields. Still, we will give you a reference concept design. This will assist in defining the simple geometry of the sized and shaped sheet metal parts together with their usage.
DFM Support: When the design plan is set, the manufacturability and assembly possibilities will be considered from the design phase. Production and assembly costs and production efficiency will also help enhance the design plan.
Detailed Design: It includes the use of computer-aided design software like SolidWorks, AutoCAD, Pro/ENGINEER, and UG in the advancement of the design plan by the R&D design team. These are material selection, form design of a part, size design, hole design, bending design, and, assembly design. So, it can increase the accuracy of the design endeavor and the ease with which it can be manufactured.
3D Modeling and Simulation: Through superior 3D modeling and simulation equipment, we can conduct simulation checks on the dimensions detailed on the design drawings. It will measure the feasibility of manufacturing the assembly parts and consequently its efficiency. This makes it possible to determine and address possible assembly problems before they occur.
Rapid Prototyping: It develops within a short period from the design drawings and tests will be carried out on the various aspects and sub-assemblies. So, it can verify the design functionality and the various dimensions of the design drawings.
Design Optimization: While conducting the tests in the context of rapid prototyping, the design plan is further adjusted and improved to increase the mechanical characteristics of the sheet metal assemblies. It will implement actual high-efficiency and low-cost production.
Final Design and Drawing Output: After finalization of all the designs, we shall give the final design drawings for your further verification and adjustment, concerning the sheet metal assembly production; this will help in eliminating indiscriminate difficulties, by strictly adhering to the drawings.

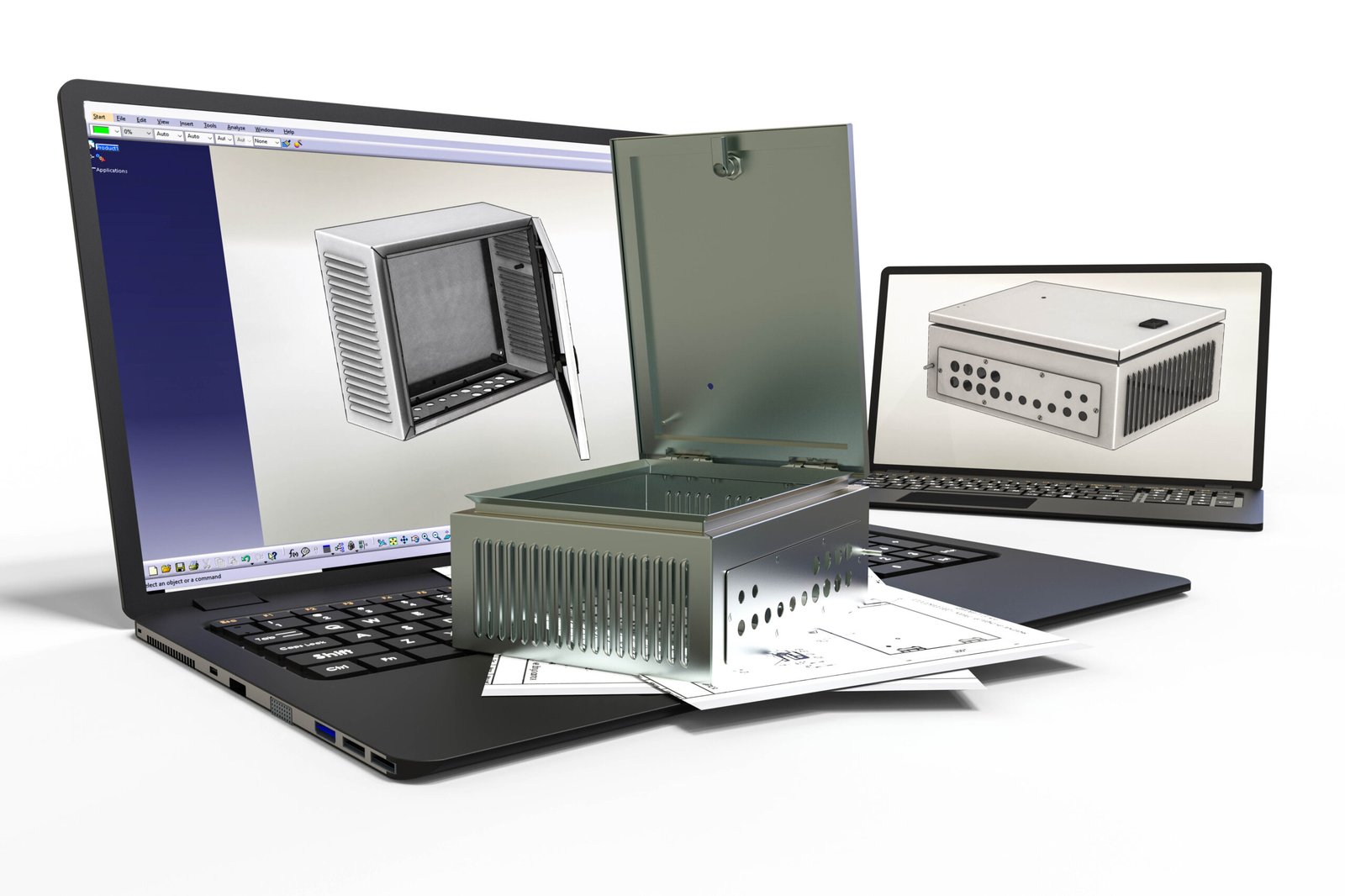

Let’s Explore our DFM Sheet Metal Design Guide
We are here to give design-for-manufacturing (DFM) templates. They’re specially created to help in creating better-quality product parts at a lower cost. Some of the general recommendations for sheet metal designs are distances between the holes, notches, and slots of the parts, distance of holes, notches, and slots from the edges of the part and bends, and bends in the same direction. Besides this, it may include minimum bend radius, minimum radius near the hemmed edges and teardrop hems, less width of flange, and minimum sizes of slots and holes are other guidelines for sheet metal designing.
Some of the general DFM Pro sheet metal design guidelines are quite flexible. They can be adapted easily for adherence to the design rules of a particular company. It is also known to provide the functionality of easily creating new design rules for the existing database.
Category | Tip | Details | Simplified Drawings |
General Tips | Minimize Complexity | Design with simple, uniform geometries to reduce complexity and costs. | ![]() |
Consider Material Properties | Understand material properties for suitable design features and tolerances. | ![]() | |
Cutting Processes | Waterjet Cutting | Consider kerf width and cut quality; account for nozzle health and machine upkeep. | ![]() |
Laser Cutting | Be aware of the heat-affected zone; account for kerf width (typically 0.75-1.0mm). | ![]() | |
Punch Press | Use standard tools for low volume and custom tools for high volume; consider edge quality and deformation. | ![]() | |
Forming Processes | Bend Allowance | Calculate bend allowance to relate 2D blanks to 3D parts; understand material bending response. | ![]() |
Minimum Bend Radius | Design bends with radii relative to material thickness (e.g., 4x thickness for 6061-T6 aluminum). | ![]() | |
Bend Relief | Design relief to prevent cracks and tearing; relief width ≥ half material thickness. | ![]() | |
Feature Design | Holes | Avoid small holes; locate holes 1.5x thickness from edges and 2x thickness apart. | ![]() |
Slots, Notches, Tabs | Slots wider than thickness; positioned 2x thickness from edges and 4x from bends; notches ≥ thickness. | ![]() | |
Stiffeners | Use beads, coining, and embossing; consider material thinning and stress. | ![]() | |
Finishing and Assembly | Coating Considerations | Account for dimensional changes from coatings; plan for uncoated sections. | ![]() |
Assembly Simplicity | Design self-locating parts; use PEM inserts or rivets instead of welding if possible. | ![]() |
Masion - Best sheet metal DFM Services Provider in China
Our Culture
Core Values:
Innovation is one of the organizational values together with integrity, collaboration, customer focus, and excellence. Cognitive values include creativity, integrity, cooperation, professionalism, and striving to produce the best output in any given task for the clients.
Work Environment:
We engage in offering a working environment that is open to all and suitable for innovation and performance. The environment. It’s constantly evolving and changing reflecting the possibility of learning and developing professionally, which benefits our team.
Team Spirit:
Everyone is made to understand that we work as a team and that any success is a success for all of us. Our organizational culture fosters teamwork and communication and focuses on the productivity of people in a group, thus increasing morale among people working in groups.
Community Engagement:
This culture is anchored on effective social responsibility and sustainability. It is involved in community activities as well as employs environmental conservation policies to ensure it is ethical.
Leadership Style:
Regarding leadership, it is more centralized and based on delegation of authority and freedom of information. We promote team delegation, provide transparency in communication, and provide the employees with the decision-making authority to attend to their needs towards nervousness.
Let’s Explore Our Certifications
- ISO 9001 – Quality management systems
- GB/T 19001 – the Chinese equivalent of ISO 9001
- ISO 14001 – Environmental management systems
- GB/T 24001 – the Chinese equivalent of ISO 14001
- IATF 16949 – Automotive quality management systems
- RoHS – Restriction of hazardous substances
- CE Marking – EU conformity for safety, health, and environment
- UL Certification – Safety standards by Underwriters Laboratories
- CCC Certification – China Compulsory Certification for product safety
- TS 16949 – Former automotive quality standard, replaced by IATF 16949
- GB/T 28001 – Chinese occupational health and safety management systems
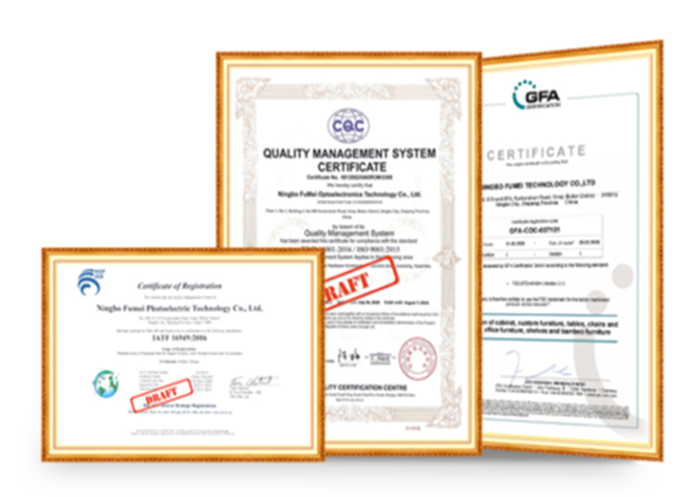
Frequently Asked Questions
DFM (Design for Manufacturability) for sheet metal parts is a design process used to maximize the manufacturing efficiency of sheet metal products, increase their quality, and minimize their cost at the stage of design of the final product by taking into account the factors that will be most likely to influence the manufacturing of the product.
We provide the following DFM services; first-time design help, re-design and improvement, cost reduction, increased efficiency, elimination of inspection errors, modification to localize products, and improvement of related products’ reliability.
DFM involves a collaborative effort from various experts and teams to achieve the best results: DFM involves a collaborative effort from various experts and teams to achieve the best results:
- Design Engineers: Design is responsible for creating the first layout of the product which includes ideas like simplicity, standardization, choice of the material, required tolerance, environment, etc, and assembling.
- Manufacturing Engineers: Advise on the manufacturing procedures, aids as well as appliances within an organization’s manufacturing line to effectively enhance the manufacturing line and reduce remarkable costs.
- Product Managers: Coordinate product requirements and be responsible for the design and manufacturing directions concerning the particular product the company goals and customers’ demands.
- Quality Assurance (QA) and Quality Control (QC) Teams: Determine quality parameters and guarantees of the produced items regarding these parameters, and reveal possible quality problems.
- Procurement and Supply Chain Teams: Acquire necessary supplies, components, and vendors that will provide the best quality at optimum costs.
- Cost Estimators: Estimate manufacturing cost foreseen on designs and manufacturing strategies.
- Tools and Equipment Experts: In process selection and design need to find appropriate tools, molds, and equipment required for manufacturing.
- Cross-Functional Teams: You will have to supervise the DFM process soliciting the cooperation of all the concerned departments.
- Suppliers and Contract Manufacturers: Ensure that you conform with the DFM directives of the company by working with the design and manufacturing subgroups.
- Testing and Inspection Teams: Test and inspect the product to determine standards to be taken in the testing of the product.
- Regulatory and Compliance Experts: Foster that the design and manufacture of its products adhere to requisite quality levels.
- Continuous Improvement Teams: Emphasis on the ongoing activities for the augmentation of production, looking for chances that facilitate making the process smoother and better.
- Processes: Select the right manufacturing process to make your product. CAD designers are important.
- Material Selection: In the case of products, the right material has to be selected from the list according to the product it is to be used in, the cost, and sometimes the process of manufacture too.
- Design for Assembly: Minimise the conventional assembly time used in accommodating the design.
- Design for Manufacturing: One of the most important requirements is the considerations when designing the selected part: Use the design for Manufacturability (DFM) when developing the design of the selected part.
- Testing and Quality Control: Check the results of the contest and control the product quality.
We make a hole with a one-unit distance between two holes. It will ensure that the holes made are well placed, If the given point lies close to the edge of the two sets then it is 5T to 2T from the edge. The same case applies to the positioning of holes and bends where the distance should be able to accommodate the bend area (H) and be close to the bend to produce a strong and stable structure.
Integral to product development is therefore the selection of an appropriate manufacturing. Thus, the key criteria for choosing the most suitable process for product production are price, production materials, volume, desired surface finish, specific production requirements, and punch-to-die clearance.
There is always close communication between engineers and fabricators. So that what is designed is possible to be made and vice versa, to obtain the best results and good quality structures.
Design for Manufacturability (DFM) therefore cuts cost and achieves more effectiveness in the product through simplification of its design to make it easier, faster, and cheaper to manufacture. It cuts down on the usage of raw materials; simplifies the manufacturing process and reduces the incidences of needing to reform a product.
The responsibility of research and development engineers is to come up with new designs of products. These are more efficient to manufacturers than the efficiency of manufacturing engineers who concentrate on the aspect of feasibility and cost of imparting the new designs. Both are involved in optimizing designs to satisfy the specified performance and manufacturing standards expected in the construction of the new structures.
Yes, we help customers who have no initial design drawings by offering design consulting services. It can be necessary to create early designs according to their needs and suggestions with specific reference to manufacturability and function.
For quality and reliability, they undergo various tests, conform to industries’ best practices, and also inspections. All our designs and manufacturing procedures are strictly done in compliance with our laid down standard policies to achieve the best quality.
Product design for manufacturing localization means a change in the design of the product. So, it can fit the regional manufacturing capacity, norms, and customers’ tastes. By following such an approach, products are best suited to fit the local manufacturing environment. But; lowering the expenses that may be affiliated with compliance and streamlining the products to better address the market environment.