Solution
Progressive Stamping Die
Masion is the top Chinese Provider of Research, Design, and Manufacturing Solutions for Precision Progressive Stamping Die.
• Focusing on the design and production of precision-grade progressive molds;
• Having 20 highly qualified and experienced Stamping Die engineers on staff.
• Outfitted with cutting-edge die manufacturing machinery, such as precision grinding machines, electrical discharge machining, machining centers, and slow wire cutting.
• Being well-versed in producing progressive stamping goods in quantities up to 10,000,000.
• Appointed provider of progressive stamping dies to different brands including LiXiang Auto, Tesla, Bull, and Geely Auto.



+86-18969433502

sales@sheetmetalmasion.com
Precision Progressive Stamping Die in China
We thrive in producing a wide range of progressive stamping die OEM products as a leading progressive die custom manufacturing facility in China. We are also known to vertically integrate our production processes, which makes it possible to produce progressive stamping dies quickly.
Progressive Stamping Die Solutions
We provide various solutions for precision stamping dies. We take pride in providing services of experienced masters in stamping dies (both progressive dies and compound dies) and the availability of modern equipment and technology for die production. We can proudly state that we can meet the manufacturing needs of various complex precision stamping parts.
Starting from the very beginning of your precision stamping project design, we offer mold design for DFM (Design for Manufacturability) and practical processing solutions for precision stamped parts. We have a team of professional R&D engineers and mold engineers dedicated to working in the design process, manufacturing progressive dies, and skilled machinists to handle the bulk production of precision stamping parts. Our quality inspectors conduct first-piece, in-process, and final inspections, while our mold masters manage, organize, maintain, and repair the progressive dies. From the beginning till the end, our experienced professionals ensure that the finished product satisfies our clients.
Having our production management vertically integrated, we make use of rapid prototyping technology, to swiftly produce progressive dies and also to save on your investment costs for such dies. We believe in testing for the performance and quality of the stamped parts and take it seriously so you get to save significant time during the precision stamping process, accelerate time to market, quickly seize market opportunities, and concurrently reduce stamping costs, thereby enhancing your competitiveness in the market.
Materials
● Tool Steel
D2 Steel, A2 Steel, O1 Steel)High-Speed Steel, HSS (M2 Steel、M4 Steel)
● Carbide
Tungsten Carbide
Heat-Treated Steel:
(H13 Steel、S7 Steel)
● Wear-Resistant Steel
Stamping Dies
● Compound Dies
● Progressive Dies
● Simple Stamping Dies
● Combination
Machines
● CNC Precision Slow Wire EDM Machine
● CNC Precision Machining Center
● CNC Lathe Electrical Discharge Machine (EDM)
● Large Surface Grinding Machine
● Precision Surface Grinding Machine
● Milling Machine
Surface Finish
● Surface Hardening
● Carburizing and Quenching
● TD Treatment
● Nitriding Treatment
Progressive dies are multifunctional (single-stage or integrated) tooling systems used for stamping purposes. They include an upper die known as punch and a lower die known as die, having various stamping stations designated within the die cavity. Shearing, blanking, bending, punching, trimming, threading, embossing, imprinting, and stripping can all be done simultaneously with the help of these dies. In most cases, the progressive stamping press’s bed holds the lower die (die), while the equipment’s slide holds the upper die (punch). The automatic feeder transfers coils of sheet metal (thickness less than 2.5mm) incrementally into the die cavity by moving the upper die step by step. After that, the upper and lower die work together to perform stamping, shaping the metal following the die cavity’s design. Every time the coil goes into the die cavity, stamping is done. Until the stamping process is finished, the coil keeps going through the progressive die cavity.
What is a progressive stamping die?
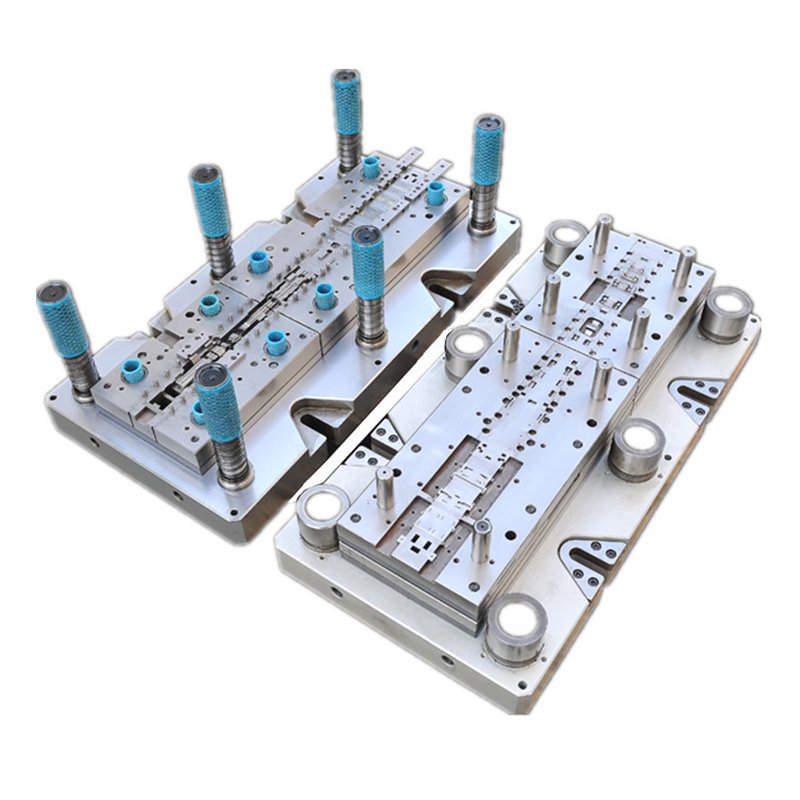
The Pros and Cons of Using Progressive Stamping Dies
The most sophisticated stamping dies currently on the market are progressive dies. Progressive dies produce stamped parts in large quantities. They are widely used for the mass production of stamped components in industries like automotive, electronics, and home appliances. This kind of die can combine all of the stamping part processes into one, which has many benefits but also some drawbacks, which are briefly discussed below:
Advantages:
– Fast Production: By completing various stamping operations like cutting, punching, bending, trimming, threading, embossing, imprinting, and stripping, Progressive Dies accelerate processing speed.
– Material Waste Decreases: Carefully planning and refining the stamping operations in Progressive Dies decreases material waste drastically, which lowers production costs.
– High precision and quality: Goods imprinted using progressive dies can attain ±0.05mm precision, more than the usual ±0.1mm precision, guaranteeing uniformity in every product.
– Lower Labor Cost: Automation of feeding systems and stamping processes eliminates the need for manual labor, lowering labor production costs.
– Higher Safety: Progressive Dies, combined with Progressive Stamping Presses induce safety measures to reduce production hazards and enhance worker safety.
– Long Lifespan of Progressive Dies: We design our Progressive Dies with a lifespan of generally 500,000 stampings. If the product exceeds 500,000 stampings, we will develop new dies to ensure product quality.
Disadvantages:
– High Die Manufacturing Costs: The development, design, and production costs of progressive dies, which can range from tens of thousands to hundreds of thousands, are substantially higher than those of conventional stamping dies. Progressive dies are, therefore, not recommended for small-scale stamping.
– Complex Design and R&D: Since progressive dies are mixed from several separate parts, their development calls for skilled toolmakers and designers.
– High Maintaining Expenses: Progressive dies can be difficult and expensive to repair because of their complexity.
– Low flexibility: Because progressive dies are to fit particular products, they are only able to produce a single kind of product and are difficult to alter.
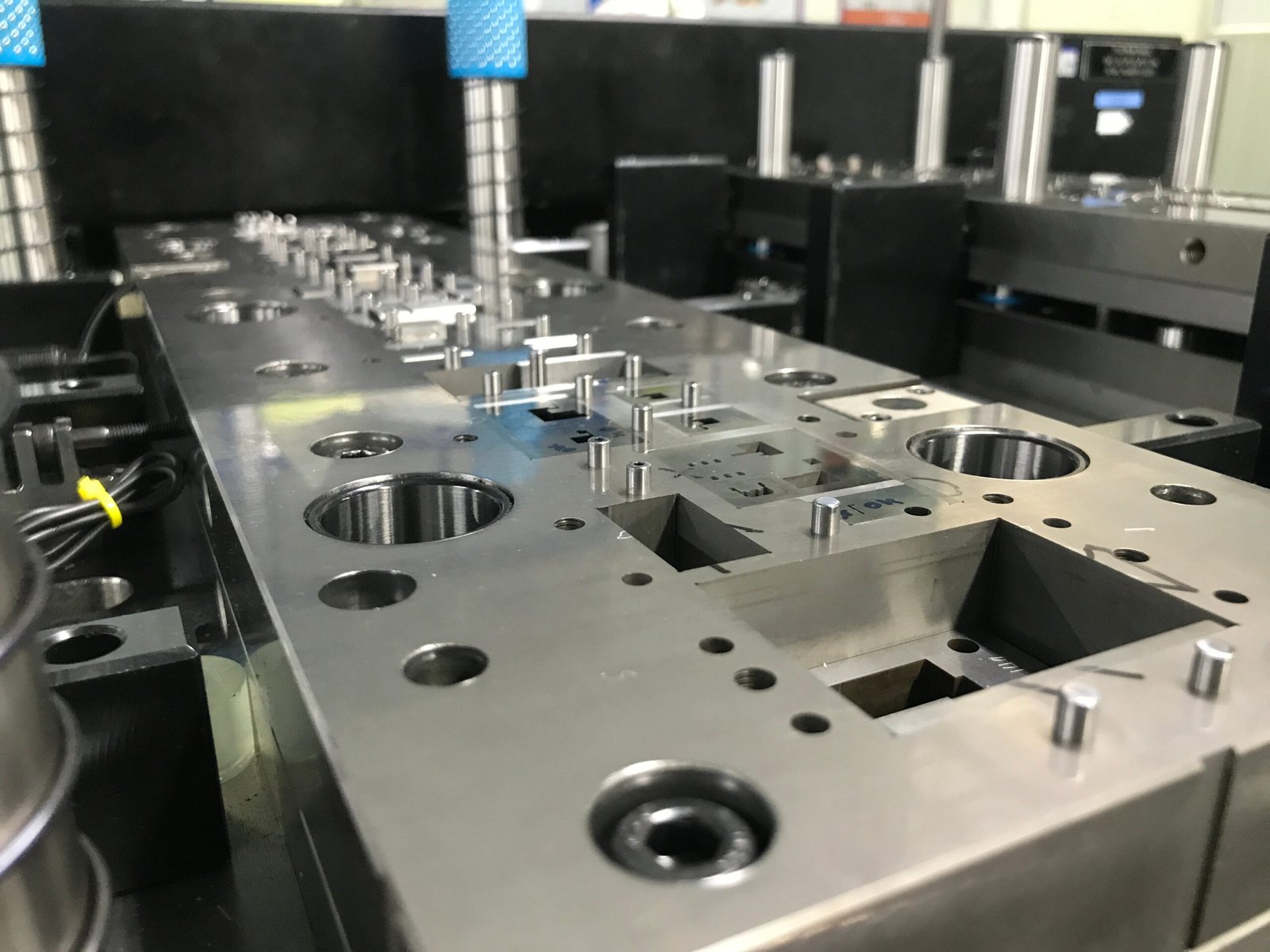


Why Choose us for your Custom Precision Progressive Stamping Die? Here is why:
As a precision stamping progressive die manufacturer in China, we are ISO/TS 16949 certified and have a wide range of automotive clients, including Geely, Lixiang Motors, and Tesla. Since 2007, we have offered precision stamped parts technical support services at different project stages. We are a dependable source for detailed and complex precision-stamped progressive dies or switching stamping part suppliers to care for project quality concerns.
Quality Management System: We possess strong quality management certifications from ISO 9001 and ISO/TS 16949. Ensuring quality is our top priority.
Internal DFM and Tooling Design: We use a robust ERP system to improve lead time control over suppliers, costs, and production. We have six manufacturing facilities devoted to die design and production, with the help of twenty experienced mold engineers.
Support for Large Projects: We have a wealth of design and production experience from our work on prestigious projects and alliances with businesses like Tesla, Top, Xusheng, Lixiang Motors, and Geely.
Variety of Material and Thickness: We have extensive experience choosing materials for progressive dies, including mold steel and high-speed steel.
Comprehensive Processing Capabilities: We not only manufacture precision progressive stamping dies, but we also provide secondary processing such as surface treatment, riveting, welding, and precision stamping.
Modern Stamping Equipment: We can produce progressive dies with remarkable accuracy and high precision thanks to our superior mechanical equipment, which is the most advanced in China. to manage a range of challenging projects.
Increased Precision: The precision of the die can reach ±0.01mm.
Progressive Die Monitoring: To prevent die damage when producing a large quantity of precision stamped parts using progressive dies, we employ die monitoring to identify whether stamped parts may come loose.
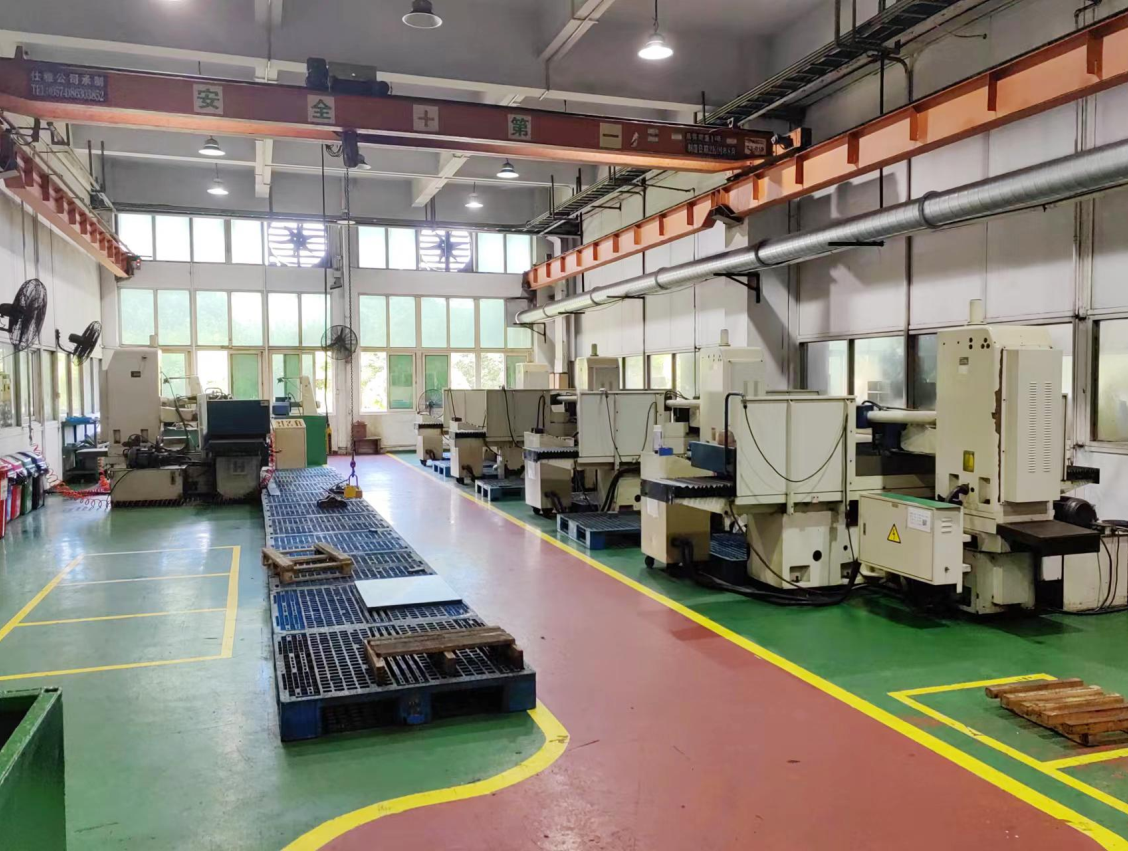
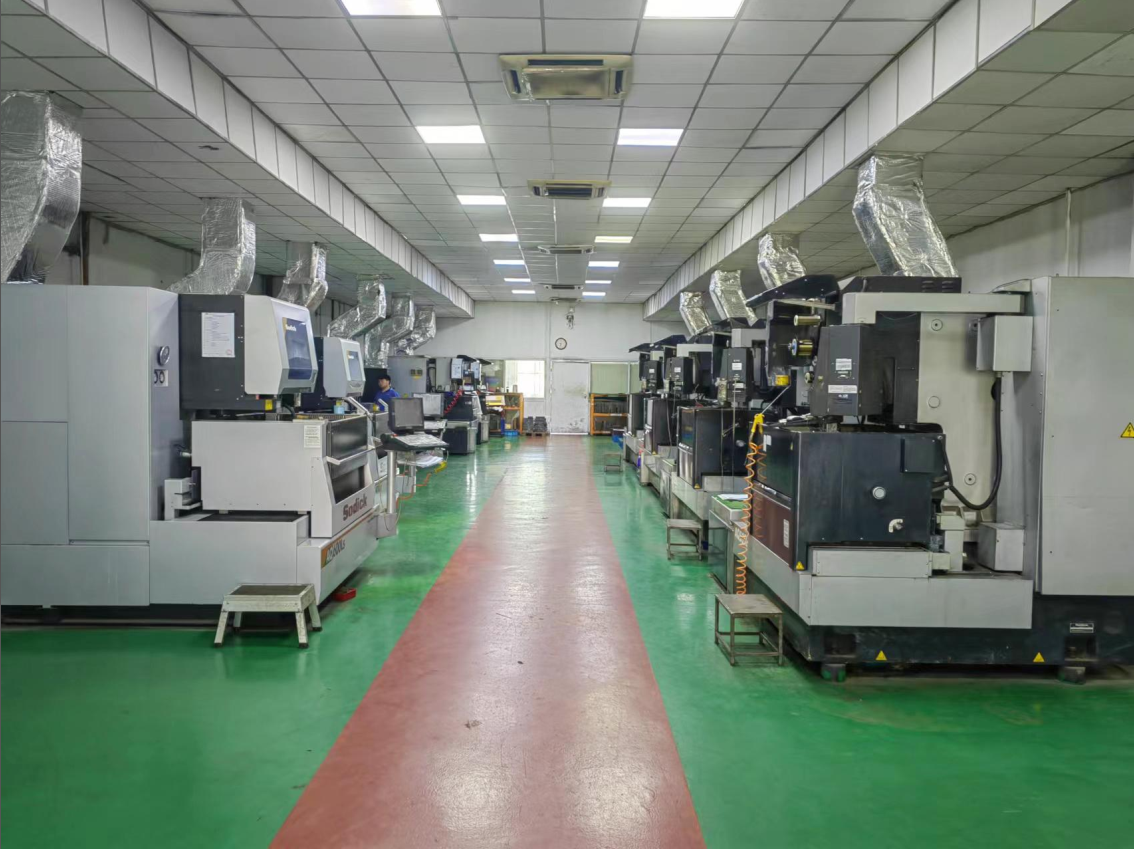

Progressive Stamping Die Design
Our R&D team is highly skilled and has a great deal of experience creating progressive stamping dies. Our R&D engineers are skilled in using a variety of design programs, including AutoCAD, SolidWorks, and UG. Provide us with the stamping part drawings, and we will assist you in creating the necessary progressive stamping dies.
We use the latest and most sophisticated design software for our progressive stamping dies, including
UG (Unigraphics NX): Our engineers can use UG which is known for its comprehensive suite of CAD, CAM, and CAE tools, to create detailed and accurate designs.
SolidWorks: We can visualize, simulate, and refine our die designs for maximum efficiency and reliability with the help of SolidWorks.
AutoCAD: A staple in the industry, AutoCAD provides us with the flexibility and accuracy needed for intricate die design work
Custom Design Solutions
At any point in the design process, we are well-equipped to assist you whether you have a detailed blueprint or a conceptual idea. Sending us your stamping part drawings initiates a collaborative process where our experts will:
Analyze Requirements: To comprehend the dimensional and functional requirements of your stamping parts, we carefully go over your specifications.
Design Optimization: We develop optimized die designs that improve production efficiency and cut down on material waste by using cutting-edge software tools.
Quality Assurance: To guarantee that our designs satisfy your performance requirements and are prepared for smooth integration into your production line, they go through extensive testing and validation.
Why Choose Us?
Our commitment to innovation ensures that we are always at the forefront of technology and industry trends.
Reliability: Our thorough testing and validation processes guarantee that our progressive stamping dies deliver consistent and reliable performance.
Support: We offer continuous support throughout the design and implementation stages, ensuring a smooth and efficient transition from design to production.
Key Benefits of Our Progressive Stamping Die Design:
Precision Engineering: We ensure high precision and strict design parameters for complex stamping parts.
Efficiency: Our efficient workflow streamlines the production processes, reducing cycle time and material waste. This also makes our process cost-efficient for our clients.
Durability: We make sure that our designs are durable by focusing on longevity and robustness to withstand high-volume production.
Cost-Effectiveness: We provide optimized designs that minimize production costs without compromising quality.
Scalability: Solutions designed to scale with your production needs, from small batches to large-scale manufacturing.
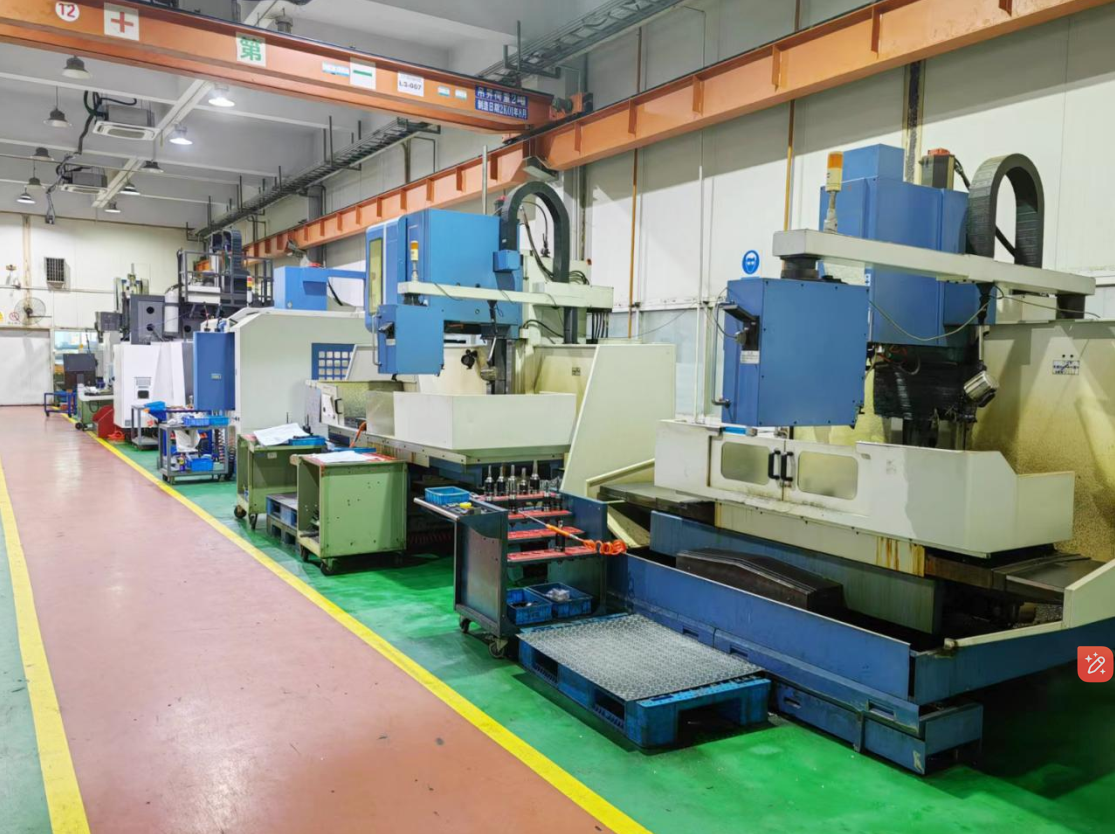
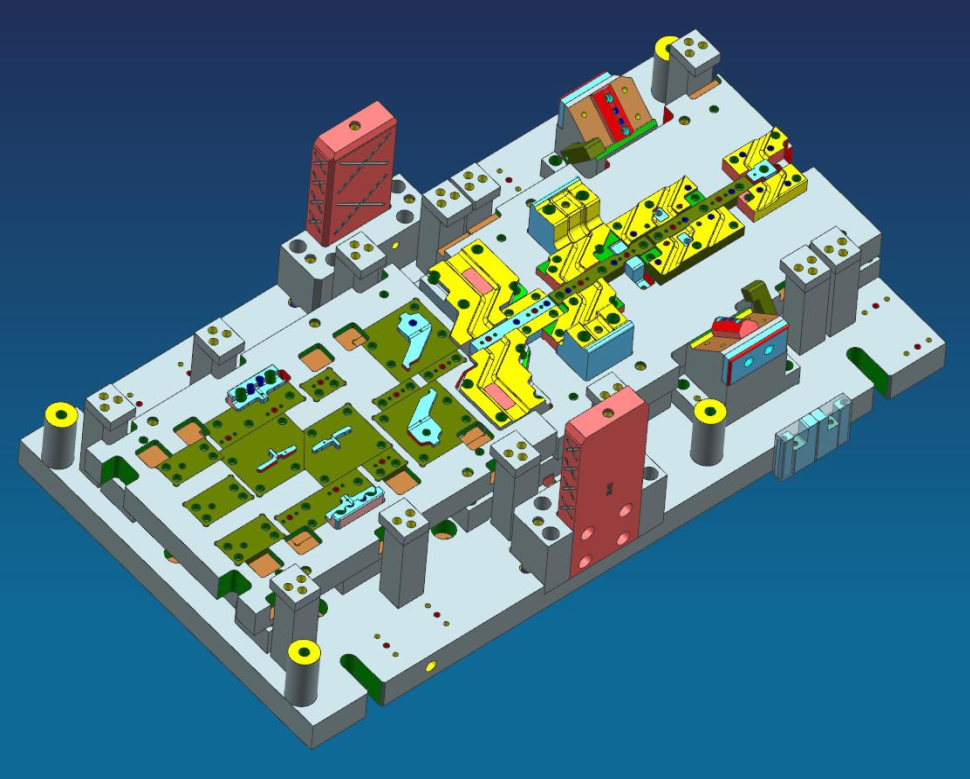
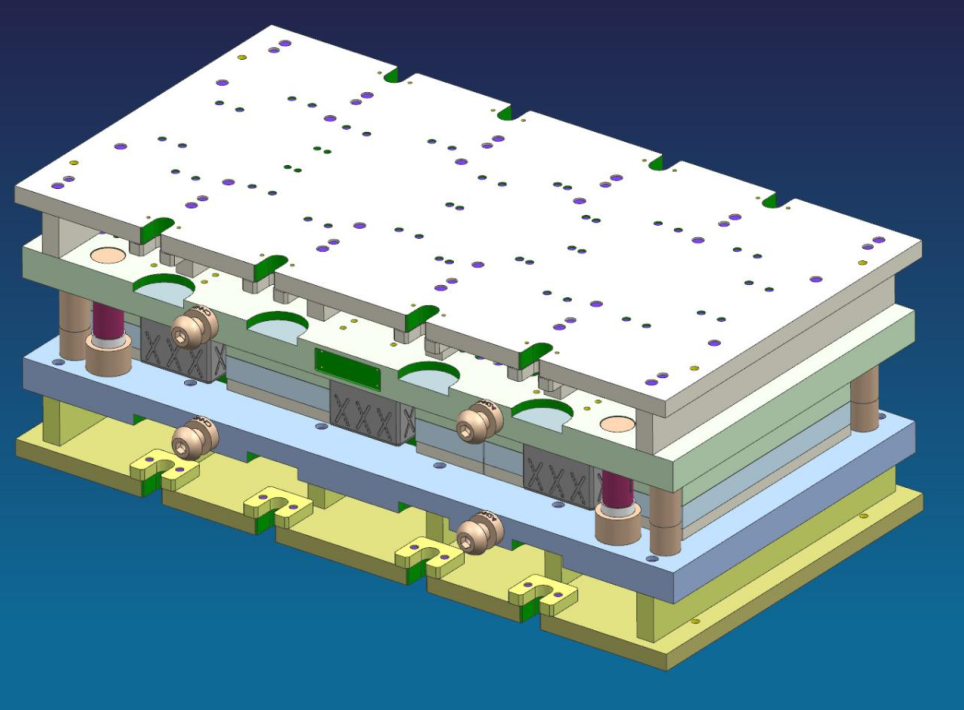
Certificate of Progressive Stamping Die
● ISO9001 Quality Management System
● ISO14001 Environment Management System Certification.
● TS16949 Automotive Industry Quality Management System
● FSC Forest Stewardship Council
● Patent 39 patents of invention
● CE CONFORMITE EUROPEENNE(As you need we could apply)
● RoHS Restriction of Hazardous Substances(As you need we could apply)
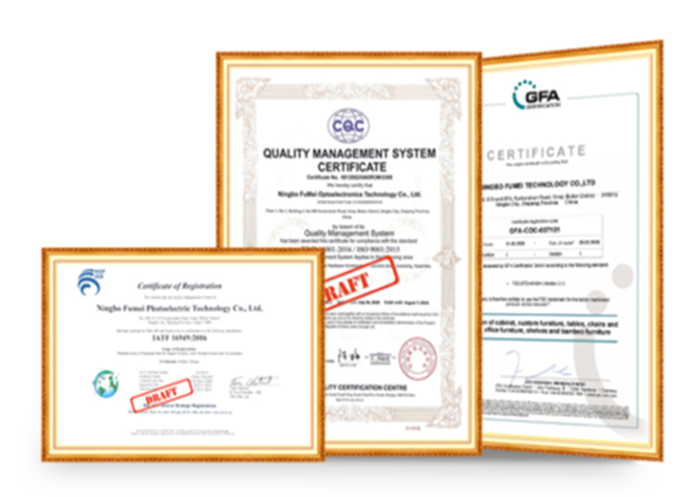
Progressive Stamping Die Gallery
The progressive die industry has become a part of everyone’s daily lives. To consider the example of the automotive sector, automotive parts are manufactured using progressive die stamping. Similarly, in the solar energy industry, brackets are produced using progressive die stamping, and in the electronics industry, plugs and pins are among the many items made by using progressive die stamping.
Progressive Stamping Die Industries
● Computer chassis, power supply housing, electronic equipment housing, etc.
● Plugs, sockets, connector housings, etc.
● Heat sinks, heatsink enclosures, etc.
● PCB mounting brackets, slots, etc.
● LED lamp housings, LED heatsinks, etc.
● Monitor stands, keyboard stands, phone holders, etc.
● Electrolytic capacitor housings, inductor housings, etc.
● Power switches, push buttons switches, etc.
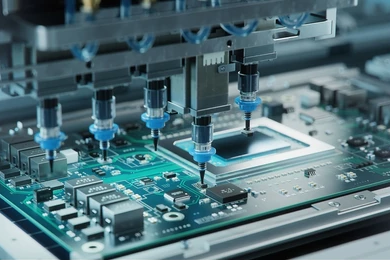
Electronics Industry
● Roof panel, side panel, etc
● Floor panel, suspension bracket, etc
● Dashboard bracket, door panel, seat adjuster, etc
● Hood, cylinder head, engine block, etc.
● Exhaust pipe, muffler, tailpipe, etc.
● Brake disc, brake drum, brake pad, etc.
● Gear, drive shaft, clutch disc, etc.
● Power window switch, power seat adjuster, headlamp reflector, etc.

Auto Industry
- Solar panel bracket, support frame, etc.
- Bracket for supporting and securing solar panels.
- Metal connector for connecting solar panels.
- External protective casing for solar photovoltaic modules.
- Bracket accessories for installing and securing solar photovoltaic modules.
- Housing for protecting photovoltaic inverters.
- Metal connector for connecting photovoltaic cables.
- Housing for photovoltaic temperature sensors, photovoltaic surge protectors, etc.
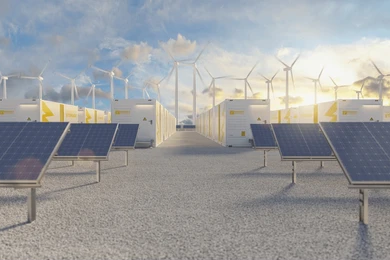
Photovoltaic Industry
● Door and window frames, door latch, door and window hinges, etc.
● Aluminum window frames, aluminum door frames, aluminum hanging accessories, etc.
● Steel structure connectors, steel structure supports, steel structure frames, etc.
● Steel guardrails, metal sheet components, roof rainwater collection system components, etc.
● Stair handrails, railing handrails, corridor handrails, etc.
● Metal safety door panels, metal fireproof door panels, etc.
● Metal roof drainage systems, metal roof vents, metal roof safety guardrails, etc.
● Bridge supports, bridge abutments, bridge girders, etc.
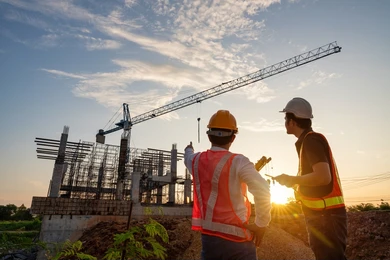
Construction Industry
Other Manufacturing Solutions
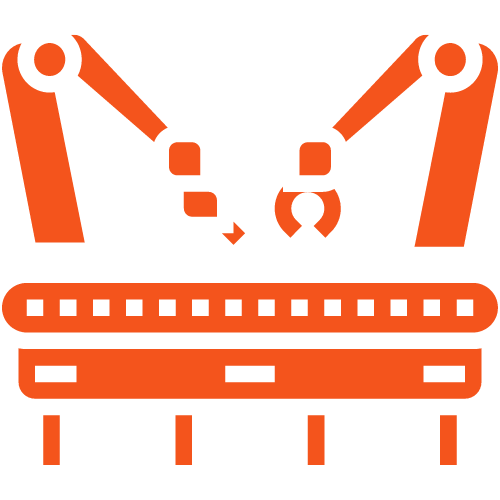
Sheet Metal Fabrication
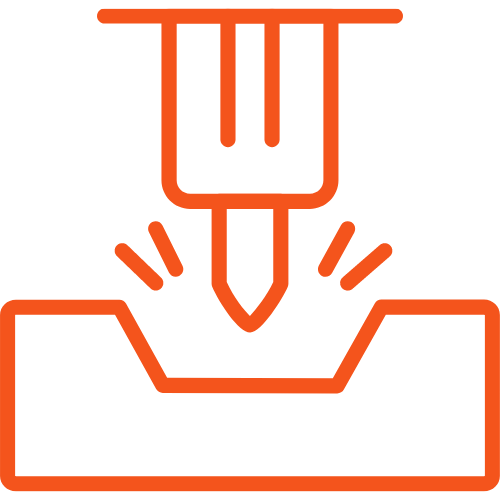
Metal Tube Processing

Laser Cutting
We’re here to provide you with custom solutions for various complex sheet metal manufacturing projects.
Masion gives custom processing services solutions for various shapes. They may include round, square, and special-shaped metal tubes.
Masion provides customized precision laser cutting services solutions. They are used for various materials and complex shapes.
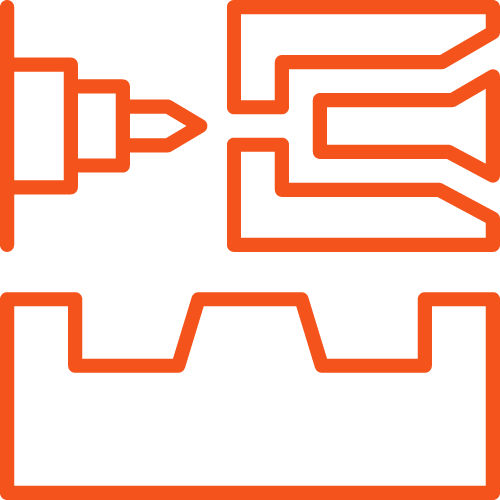
Stamping

Sheet Metal Assembly

Contract Manufacturing
We deal with the production and manufacturing of progressive dies and compound dies. So, we provide solutions for precision stamping parts production services
We provide sheet metal parts assembly services, suitable for large, small, various projects complex sheet metal parts assembly.
We have Vertical Integration Production and Assembly of Sheet Metal Parts Solution.
Resources
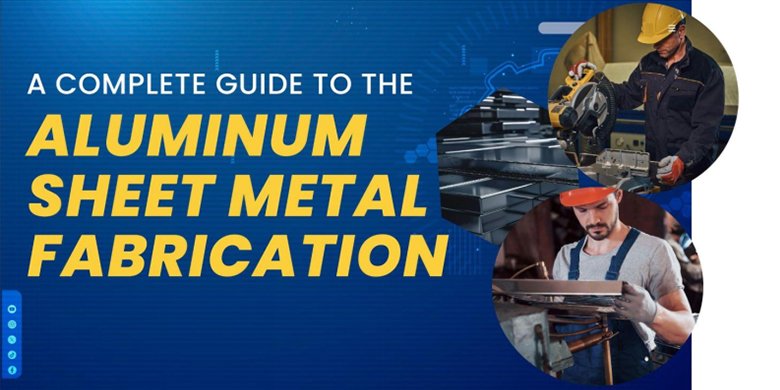
Aluminum sheet metal fabrication converts long sheets into specific shape. So, in this article, we will give you a complete guide to this process and its demands in the manufacturing industry.
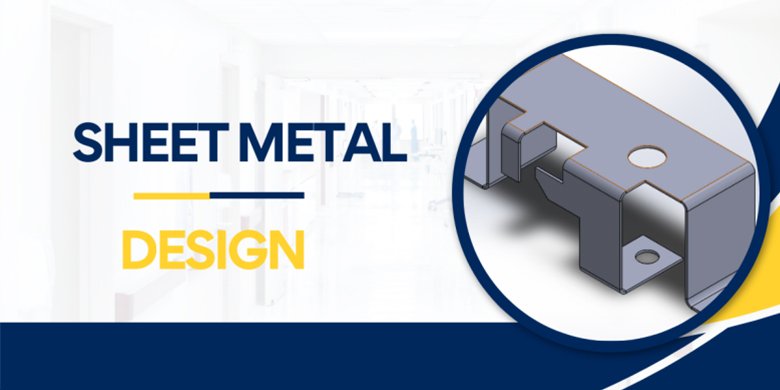
You can learn some tips for sheet metal design from this article. Understand the need, importance, and why the sheet metal design is crucial to play a key role in diverse industries.
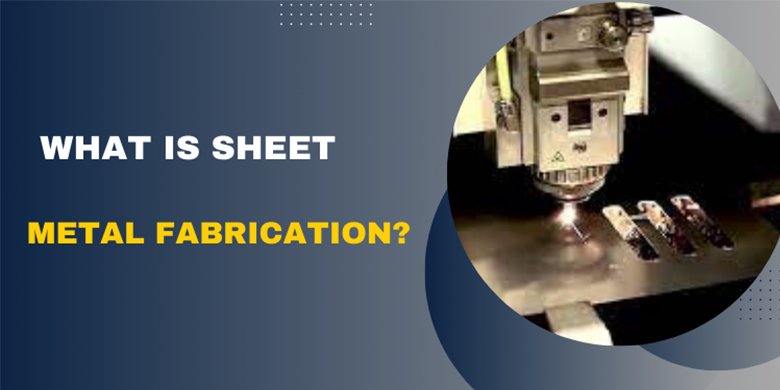
This guide allows you to create good sheet metal parts. We will start with the basics then discuss design best practices. Sounds exciting? Let’s delve in deeper to uncover facts.
Progressive Stamping Die FAQs
Q: What is the lifespan of the progressive dies you design?
A: We create our own dies, manufacture them, and handle the stamping components in-house. Our progressive dies are therefore built to withstand 500,000 stamping cycles. Do not hesitate to get in touch with us if you are looking for a longer lifespan.
Q: Do you provide after-sales technical support for progressive dies?
A: Of course! Our R&D and after-sales teams are trained by experts. We offer after-sales technical support, including maintenance and repairs, in addition to technical guidance during the initial stages, such as installation and debugging. Adhering to the tenet of enduring collaboration, we guarantee the excellence of progressive dies and offer an array of post-purchase technical assistance.
Q: How do you optimize die design to improve production efficiency?
A: Design Simplification: To minimize the complexity of the die structure, we usually base the design of progressive dies on the form and structure of the stamped parts. This lowers the quantity and complexity of die components, which lowers expenses and facilitates installation and maintenance.
Material Optimization: To increase the longevity and durability of the die, we precisely choose the materials used in the die based on the materials of the stamped parts.
Decreased Adjustment Time: In the design stage, we take the time needed for die modifications into account. To improve your production efficiency, we therefore work to minimize the complexity of the dies and shorten the time required for die changes.
Die Maintenance Suggestions: We offer maintenance recommendations based on die components to make sure that the required maintenance—including parts, timing, and sequence—is carried out following die usage.
Q: What materials are used in your progressive dies?
A: Usually, the materials of the stamped parts help us choose the die materials. Wear-resistant steel, carbide, die steel, and high-speed steel are common materials used in progressive dies. In the case of materials like titanium alloys, we might suggest H13 die steel, 8407 die steel, etc.
Q: What is the lead time for manufacturing and delivering progressive dies?
A: The complexity of the stamped parts affects lead time. Our lead time for progressive dies is typically 35–40 days, but it may be less for simpler parts that involve straightforward stamping and bending techniques. The lead time could be 60–70 days for more intricate parts that require several stamping processes. If you send us the stamped parts, we’ll give you a precise lead time.
Q: How do you ensure the quality of progressive dies?
A: Quality Control in the Early Design Stage: To reduce possible problems during manufacturing and use, we carry out DFM evaluations and simulations in the early design stage.
High-quality Die Materials and Inspection: We base our selection of high-quality and appropriate materials for progressive dies on the materials used in stamped parts. We also carry out inspections to guarantee that the specifications are met and that the material has good mechanical and physical qualities.
Quality Control in Die Manufacturing: To guarantee dimensional tolerances, accuracy, surface quality, and wear resistance, we closely monitor the die component manufacturing processes of heat treatment and surface treatment.
Installation and Debugging: During installation and debugging, we make sure that every part of the progressive dies fits precisely and works as intended to guarantee that every stamping operation goes without a hitch.
First Piece Inspection Following Debugging: We check the stamped parts to make sure they adhere to design specifications after debugging the progressive dies to meet specifications. Die adjustments are used to resolve any disparities until the requirements of the final design are satisfied.
Q: Do you provide die tryout and sample testing?
A: Yes, we do! After the progressive dies are manufactured, we test samples and run simulations to make sure the dies match the stamped parts’ design specifications. This enables us to precisely deliver progressive dies that satisfy requirements for both quantity and quality. For your reference, we offer a sample-size inspection report.
Q: What should be considered for die maintenance and care?
A: To extend the life of your progressive dies, die maintenance is essential. The following are some recommendations for maintenance:
- Cleaning after use: To keep the dies from getting damaged, clean the internal surfaces to get rid of any oil or debris after using them.
- Regular lubrication: To minimize friction and guarantee smooth operation, lubricate the dies’ moving parts regularly.
- Frequent inspection: To guarantee correct operation, check all die connections regularly, including guide posts, bushings, sliders, and die cores.
- Replacement of worn parts: To preserve stamping accuracy and quality, replace seriously worn die components, such as die cores and die seats.
- Rust prevention: To stop rusting or corrosion of die surfaces, use rust-proof oil or other rust prevention techniques if the dies are not going to be used for a long time.
- Storage in a dry area: To avoid the progressive dies coming into contact with the ground, store them on shelves or in dry areas if your location is humid.
- Frequent training: To improve operators’ knowledge and proficiency in die maintenance and operation and to minimize incorrect operations that could harm the dies, provide operators with regular training.
Establish a maintenance record system to track die cleaning, lubrication, part replacement, maintenance schedule, and personnel. This will help with die maintenance and repair traceability.
Q: Does your die manufacturing have relevant industry experience and qualifications?
A: To begin with, our factory has obtained ISO9001-2015 quality management certification. We adhere to ISO9001 quality management standards and strictly regulate the die manufacturing process. We are even more certified to ISO16949 quality management standards if the dies are for automotive parts. Both our die manufacturing craftsmen and R&D design team are highly skilled and have many years of combined experience. You can therefore feel secure in giving us the die R&D and manufacturing tasks.