Sheet Metal Fabrication – Everything You Need to Know
Are you dealing with the complicated sheet metal fabrication tasks or projects? The key challenge for various businesses lies in selecting the right process, tools, and techniques. If you don’t pay attention to this then you may end up facing the highe cost, material wastage, and dissapointing final product. Getting in-depth insights on the fabricating sheet metals fundamentals assist you in streamlining your projects and scale up productivity. The aim of this blog is to guide you through the processes, techniques, tools, and much more. Sounds intriguing? Keep reading!
Table of Contents
ToggleWhat is Sheet Metal Fabrication?
It is a process to convert sheet metals into complex structure as well as shapes following cutting, bending as well as assembling. There are a series of methods involve in achieving fabrication of sheet metals. You can accomlish it manually or with automated tools. For fabrication of cheap, qualitative, and reliable components the knowledge of the process is key.
Top Tools and Sheet Metal Fabrication Machines
Each process involve in the fabrication includes the usage of diverse tool types or machines for accurate process accomplishments such as:
- Cutting Tools
- Bending Tools
- Forming Tools
- Welding Tools
- Finishing Tools
- Miscellaneous Tools
Let’s uncover insights on each process tools individually down below:
Cutting Tools
Laser Cutters
In sheet metal fabrication, laser cutters supply high-quality precision and speed for crafting complex shapes. They deploy a focused laser beam to melt or vaporize the material, culminating in smooth, clean edges. This technology is perfect for detailed designs and continuous production, which is why it’s favored by industries such as automotive and aerospace.
Key Features:
- Achieve perfect cuts with limited material waste.
- You can use it for stainless steel as well as aluminum.
- The material’s deformation is reduced by the non-contact process.
- High-speed operations lead to enhanced productivity.
- Capable of automatic cutting, thus increasing its efficiency.
Water Jet Cutters
High-pressure water streams are used in water jet cutters, sometimes combined with abrasive materials, to effectively slice through various thicknesses of metal. This way of cutting is highly adaptable, enabling you to craft detailed shapes with no heat, avoiding distortion of the material. It is perfect for cutting a variety of materials, spanning from metals and glass to composites.
Key Features:
- Cuts without the application of heat, thereby avoiding any thermal damage.
- Capable of precisely cutting sheets of a considerable thickness.
- Environmentally safe, as it does not produce any harmful fumes.
- Suitable for the use of metals, ceramics, and even stone.
- Reduces the requirement for secondary finishing methods due to its smooth edges.
Plasma Cutters
These cutters make use of conductive electric gas to produce high-temperature arc of plasma. You can easily melt the metal sheets at high speed using this method. Perfect for the applications which needs precise as well as rapid cutting. They are specially useful in manufacturing as well as construction.
Key Features:
- Cuts with no difficulty through both thick and thin metals.
- Productivity is greatly increased with high cutting speed.
- Effective in processing conductive metals, such as steel and aluminum.
- Offers a quick and tidy division with small amounts of remaining slag.
Shears
Shears refer to tools for cutting that can either be powered or operated manually. They operate by applying a shear force, which allows them to cut through the resource without producing any heat. Shears are very useful for rapidly cutting material to size, and for trimming away any excess, especially in less professional settings where space is limited.
Key Features:
- Popular for its effectiveness in making precise cuts on thin sheets.
- No energy distortion, maintaining properties of the material.
- Simple and fast to use with only a small amount of setup required.
- Minimal maintenance and operating costs.
- Applicable to materials including aluminum, brass, and other soft metals.
Band Saws
Band saws utilize a continuous strip of metal featuring teeth on one edge, which is used to slice through thick metal plates or delicate forms. They are well-suited for creating curved cuts and slicing through thicker materials that other cutting tools might find challenging. In workshops, band saws are commonly used for the purpose of prototyping and small-batch production.
Key Features:
- Suitable for cutting large sheets and complicated forms.
- Reducing wasted material and making the best use of resources.
- A range of materials are valid, including ferrous and non-ferrous metals.
- Different metals can be accommodated with different speed settings.
- A smaller amount of noise and vibration relative to other cutting tools.
Chop Saws
They make use of a high-speed, abrasive-disc rotating mechanism to slice through the material. These tools are particularly effective for cutting metal bars, tubes, and other profiles to the proper size with precision. Chop saws are popularly utilized in construction and metalworking industries for frequent, precise cuts.
Key Features:
- Gives quick and accurate straight cuts.
- Satisfactory for slicing through metal bars and tubes.
- Designed to be small and convenient for hands-on jobs.
- A high cutting speed promotes efficiency.
- Creates almost no burrs, thereby lessening the need for post-processing activities.
Bending Equipment
Press Brakes
Press brakes are key devices for the bending of sheet metal at a range of angles. These tools make it possible to execute specific bends, thus maintaining the precise specifications of your metal pieces. Manufacturing and metal fabrication widely take advantage of them. Thanks to adjustable settings, you are able to modify the bending operation for various materials.
Key Features:
- Permits fine adjustments in angle.
- Applicable for differing sheet metal thicknesses.
- Reduces expenditure on waste by optimizing the use of material.
- Permits the production of complex shapes without much effort.
CNC Tube Machines
CNC tube bending machines take on the automation of tube and pipe bending. You are able to manufacture elaborate designs and bends with very high precision. These machines increase the productivity levels in large operations. They help to faciliate bending by eliminating manual labor.
Key Features:
- Provides exactitude in bending.
- Decreases the risk of human error by applying automation.
- Able to yield intricate forms.
- Increases the productivity in substantial production affairs.
Forming Tools
Punch Presses
Quite quickly and silently, punch presses either form or drill punch holes into sheet metal. It is possible to make customer parts of multiple designs using these machines. Manufacturing environments extensively utilize them. The pace of operation increases productivity for your projects.
Key Features:
- Offers fast and correct hole fabrication.
- Able to yield multiple forms.
- Lowers material waste generated in the production process.
- Suitable for requirements involving high volumes of production.
Stamping Machines
Machines for stamping are intended for raising designs and making complicated shapes on metal. You have no trouble creating detailed patterns and forms. Being efficient machines, they are ideal for large scale production. Decorating your metal products with unique features is what they are crucial for.
Key Features:
- Permits the creation of complicated and detailed designs.
- Reduces production time greatly.
- Shortens finishing time owing to the reliability of stamping.
- Suitable for production facilities where volume is high.
Welding Equipment
MIG Welders
Metal Inert Gas (MIG) welders are efficient in their fast metal joining process. You can work with multiple materials, all with great ease. The approach is basic, rendering it excellent for both newer welding enthusiasts and veteran welders. For production and repair operations, it is perfect.
Key Features:
- Provides rapid welding services.
- Compatible with a variety of metal kinds.
- Leads to decreased cleanup time owing to the scarce spatter.
- A breeze for beginners to both learn and use.
TIG Welders
TIG welders, known as Tungsten Inert Gas welders, offer you detailed control for optimal welds. Using this method allows you to deal with thinner materials and obtain clean welds. It’s suitable for detailed projects and tough strength requirements. You are able to alter settings for a variety of metals too.
Key Features:
- Supplies superior control for involved assignments.
- Fits best for slim metals and complicated joints.
- Delivers clean and strong weld joints.
- Permits the modification of welding parameters.
Spot Welders
The design of spot welders is focused on electrical resistance welding of sheets overlapping with each other. Quickly and effectively, you can associate numerous metal layers. They are normally utilized for automotive manufacturing and assembly line processes. Increased speed in operating enhances the productivity of production.
Key Features:
- Achieves powerful welds with little distortion.
- Able to act fast and capably for the purpose of mass production.
- Designed for use with multiple metal thicknesses.
- Lowers the necessity for supplementary welding procedures.
Oxy-Acetylene Torches
For both welding and cutting, Oxy-acetylene torches create a flame. You have the ability to simply control heat intensity for numerous materials. This capability makes them favored in an array of uses. For both cutting and welding operations, they are important.
Key Features:
- Enables adjustable heat for different use situations.
- Ideal for both cutting and welding jobs.
- Portable and easy to use.
- Effective for applications involving thick metal.
Finishing Tools
Grinders
The function of grinders is to produce a smooth finish on metal edges. Using these tools helps you create a refined look, improving your final product. For painting or applying coatings, they are critical. Grinders enhance the total quality of your metal fabrication.
Key Features:
- Offers an easy finish around the edges.
- Improves coatings preparation on the surface.
- Versatile in regard to multiple metal types.
- Reducing the requirement for auxiliary finishing processes.
Sandblasters
Sandblasters are tools used for both surface finishing and surface preparation. There is a reliable way to effectively clean and texture metal surfaces. This operation elevates adhesion for paints and coatings. This is a fundamental part of metal fabrication and restoration.
Key Features:
- Efficiently removes contaminants as well as rust.
- Establishes a uniform finish to the texture.
- Ideal for ready surfaces for painting jobs.
- Reduces the time for manual cleaning quite a bit.
Powder Coating Equipment
Equipment designed for powder coating applies shielding coatings to surfaces made of metal. You have the ability to get a resilient finish using several colors and textures. This operation amplifies the lifespan of your products. This option is perfect for use outdoors because of its element resistance.
Key Features:
- Gives a sturdy and long-lived finish.
- Ositale Siwalela Available in many colors and textures.
- Environmentally sound in comparison to paints in liquid form.
- Reduces both overspray and the waste of materials.
Miscellaneous Tools
Metal Brake
Metal brakes help you to bend and fold metal sheets with tremendous accuracy. You are able to generate different shapes and angles for your projects. Custom metal fabrication is impossible without these tools. They enhance the flexibility you have in your design process.
Key Features:
- Guarantees precise bending of sheet metal.
- Supports different material thicknesses.
- Ideal for custom metal work.
- Reduces the amount of manual effort needed in fabrication.
Clamps and Vises
Securing metal during fabrication depends on clamps and vises. You are able to keep components steady for either cutting, welding, or assembling. In your projects, these tools guarantee both accuracy and safety. They are crucial in every shop that focuses on metalwork.
Key Features:
- Presents stability throughout the fabrication process.
- Ensures a correct match of materials.
- Accessible to use and can be changed according to your needs.
- Increases safety by assuring the security of workpieces.
Measuring Tools
Instruments such as calipers, rulers, and squares provide you with accuracy in your projects. Accurate measurement of dimensions for cuts and bends is possible for you. For achieving quality standards in metal fabrication, these tools are essential. These help you maintain your desired specifications over the long haul.
Key Features:
- Secures precise figures for the sake of correctness.
- Required for quality maintenance in fabrication.
- Convenient to use with easy-to-understand markings.
- Compatible with many different applications.
Drills and Taps
Drills and taps form holes and threads in metal structures. You can perform exact drilling for the installation of fasteners and fittings. These instruments are necessary for both assembly and construction processes. They strengthen the efficiency of your metal products.
Key Features:
- Delivers the actual hole sizes needed for fasteners.
- Permits threading in metal for the sake of secure fittings.
- Useful for a wide selection of drilling applications.
- Indispensable for assembly and manufacturing activities.
Deburring Tools
Deburring tools remove not just burrs, but also sharp edges from metal that has been cut. You can realize a safe and easy finish using these tools. They are important for maintaining the quality of your final products. Handling and assembly become safer with the help of deburring.
Key Features:
- Removes sharp edges for the sake of security.
- Improves the look of the surface finish.
- Lowers the danger of injury while handling.
- Simple to operate with several metal types.
Workbenches
Workbenches give you solid work spaces for the assembly and fabrication of parts. You can manage diverse projects efficiently thanks to the available space. These surfaces are developed to cope with both heavy loads and impact. They are an important element of every metalworking shop.
Key Features:
- Gives a persistent and durable work area.
- Offers support for intense materials in the fabrication process.
- Furnishes organization of tools and materials.
- Increases productivity within your environment.
The machines that Sheetmetalmasion utilize for fabrication of sheets are:
Sr. No. | Machine | Definition | Image | Applications | Features |
1 | NCT Turret Punch Press | A machine tool that punches holes or shapes in sheet metal using a turret of interchangeable punches. | Manufacturing components for various industries, including automotive, aerospace, and construction. | High-speed operation, precision, and versatility. | |
2 | Metal Tube Laser Cutting Machine | A machine that uses a laser beam to cut through metal tubes and pipes. | ![]() | Manufacturing components for industries such as automotive, aerospace, and construction. | High precision, clean cuts without burrs, and the ability to cut complex shapes. |
3 | CNC Tube Bending Machine | A machine that bends metal tubes and pipes into specific shapes using computer numerical control (CNC). | ![]() | Manufacturing components for industries such as automotive, furniture, and construction. | High precision, versatility, and the ability to handle complex bends. |
4 | Riveting Machine | A machine that joins two pieces of metal together using rivets. | ![]() | Manufacturing components for industries such as automotive, aerospace, and construction. | High speed, efficiency, and the ability to handle various rivet sizes and materials. |
5 | Welding Machine | A machine that joins two pieces of metal together by melting the edges and fusing them together. | ![]() | Manufacturing components for industries such as automotive, construction, and shipbuilding. | Various welding processes (e.g., MIG, TIG, spot welding) to suit different materials and applications. |
6 | Deburring Machines | Machines that remove sharp edges or burrs from metal components. | ![]() | Manufacturing components for industries such as automotive, aerospace, and medical. | Various methods (e.g., brushing, tumbling, grinding) to remove burrs from different types of metal. |
Sheet Metal Fabrication Techniques
Having knowledge of fabrication techniques is important for getting precision and efficiency in the process of sheet metal production. These solutions provide the ability to design complex pieces and maintain quality as well as cutting down on waste. Making these techniques your own allows you to enhance your manufacturing processes.
Sheet Metal Cutting Techniques
Laser Cutting
Laser sheet metal cutting achieves high precision cutting by means of focused laser beams. The method provides excellent accuracy, allowing you to shape complex designs with little effort. Your benefit is derived from its high accuracy, making it perfect for precise designs.
Water Jet Cutting
Using high pressure, water jet cutting cuts through various types of materials. This method does not generate a heat-affected zone, which keeps your metal whole. This technology is perfectly tailored for thick materials, offering clean edges and a minimal amount of waste.
Shearing
Shearing includes straight-line slicing through blades that resemble scissors. This cost-effective strategy works optimally for thin sheets and delivers fast processing times. Producing well-made flat artifacts is possible at low costs.
Torch Cutting
The cutting method called torch cutting employs a hot flame for slicing metals at risk of oxidation. It serves well for thicker substances and is economical. This approach gives flexibility for various uses, particularly in demanding situations.
Metal Bending Techniques
CNC Bending
CNC bending automates bending and gives the ability to create accurate angles and shapes. This approach facilitates reliable results, allowing it to be effective for large volume production. Using CNC technology enables you to improve accuracy while also keeping labor costs down.
Manual Press Braking
Working a manual press brake has one perform manual operations on machinery that bends materials customarily. This method allows for adaptability, being perfect for small production volumes. Your skill at adjusting bends flexibly can help you meet the individual needs of projects.
Welding Techniques
MIG Welding
To produce swift joins between metals, MIG welding uses a continuous wire feed. Its design is appropriate for dense materials and enables quicker production speeds. A large number of manufacturers take advantage of this method as it is easy to use.
TIG Welding
TIG welding guarantees careful regulate, largely for thin metals. The outcome is excellent welds with a small amount of distortion. You can accomplish detailed welds that add to the beauty and reinforcement of your projects.
Spot Welding
The method of electrical resistance is behind spot welding’s function for sheet metal joining. The rapid and effective characteristic of this technique is perfect for the production process on a large scale. You are able to facilitate your operations, making sure fast assembly occurs without giving up on quality.
Metal Forming Techniques
Punching
Punching accomplishes the creation of holes or defined shapes within sheet metal relying on a die. This technique is both time-efficient and perfect for large quantities of production. Using accurate dies provides a way to accomplish uniform results in a short time. The application of this method saves on time and cuts back on material waste, making it an ideal strategy for broad operational needs.
Stamping
Printing forms creates designs or shapes on the exterior of metal. It provides multiple options for different uses, helping you to tweak products to fit your particular demands. You can apply stamping for design elements or for practical features, which makes it a meaningful technique in the area of metalworking.
Finishing Techniques
Surface Preparation
Prior to completing the task, you have to clean and smoothen the metal surfaces. Improved adhesion and corrosion resistance require superior surface preparation. It provides the confidence that any following finishes bond well and perform satisfactorily, which extends the useful life of your products.
Coating and Painting
Using protective layers increases durability and additionally enhances appearance. You can select from three options, such as powder coating, anodizing, and galvanizing. Every method presents specific benefits, so you should pick the one that matches your project requirements best. These coatings furnish a strong defense from environmental influences.
Paint Spraying
Applying paint or coatings utilizing spray technologies is called paint spraying. This method affords consistent coverage, which makes it swift and efficient, especially concerning extensive surfaces. You have the ability to produce a smooth result that augments the overall charm of your products, making them more attractive to potential buyers.
Silk Screen Printing
Through silk screen printing, you can put logos, text, or designs straight onto metal. This technique is easily adjustable, making it perfect for branding and the identification of products. You can design striking visuals that successfully represent your brand to clients.
Anodizing
Anodizing is a process of electrochemistry that increases corrosion defense and provides color to metals, chiefly aluminum. The result of this technique is both durable and visually appealing. It enhances the shelf life of your products, all the while presenting an attractive style.
Physical Vapor Deposition (PVD) Coating
PVD coating entails the application of metal coatings of very small thickness onto the surface of the sheet metal in a vacuum environment. The process yields hard and wear-resistant coatings that greatly increase durability. You have the ability to improve performance and extend the life of your metal products with PVD coatings.
Electroplating
Using an electric current, electroplating provides a metal coating onto a sheet metal surface. This execution provides resistance to corrosion and helps to better the aesthetics of your products. In addition, it rises thickness, upgrading durability and performance.
Polishing
The act of polishing improves the finish of metal to produce a gleaming, reflective image. This technique increases visual attractiveness and may boost corrosion resistance by lowering surface flaws. Not just nice-looking, a polished surface also helps shield your products from environmental damage.
How the Sheet Metal Prototype Fabrication Process Works
Design Phase
During the design phase, you cultivate the earliest concept for your sheet metal prototype. Creating sketches and CAD models is part of this process. You ought to take into account the purpose of the product, as well as its dimensions, tolerances, and materials. Early definition of these parameters supports the feasibility of your design and makes sure it conforms to your project’s requirements.
Cutting Process
Subsequently, you go ahead with the cutting process. There are different choices you have, such as laser cutting, water jet cutting, and torch cutting. All strategies come with their benefits, but maintaining precision and accuracy is very important. You need to keep a close eye on the design specifications to confirm that the pieces come together as planned.
Bending and Forming
Following your cuts, you will have to bend and shape the sheet metal. Varying bending methods allow you to use either manual press brakes or CNC folding machines for this operation. The forming process changes the form of the metal without removing any material. This is important in order to achieve the wanted final shape, while also preserving the structural integrity.
Welding Techniques
Sheet metal fabrication relies heavily on welding as an important step. Several different welding techniques are available for you to consider, featuring MIG (Metal Inert Gas), TIG (Tungsten Inert Gas), robotic MIG, and spot welding. The individual applications of each technique mean that choosing the correct one for your material and project specifications is essential. Good welding provides solid joints and a prototype that lasts.
Finishing Touches
Ultimately, you will want to complete the last steps. Corrosion resistance and appearance are key reasons for the need of surface treatments. Finishing techniques that are common encompass powder coating, anodizing, and laser marking. The processes enhance not just the appearance of your prototype but also amplify its performance and keep it going for a longer time in its relevant environment.
Assembly Phase
Riveting
Riveting refers to attaching sheet metal parts with rivets. With this technique, you get durability that is commonly utilized in both aerospace and automotive sectors. You can depend on riveting for fantastic, secure joints.
Bolting
Bolts and nuts are what Bolting utilizes for securing sheet metal components. This process is easy to follow, facilitating ready disassembly whenever maintenance or repairs are necessary. You leverage the flexibility of putting the parts back together without causing them harm.
Adhesive Bonding
Industrial adhesives link metal parts using adhesive bonding. The result is a polished surface finish that makes it suitable for thinner metals. This method excels when you prefer a tidy design devoid of visible fasteners.
Brazing and Soldering
The heating of a filler metal connects two pieces of metal while keeping the base material solid. This technique serves to join various metals and intricate, sensitive elements. You can develop solid relationships while preserving the quality of the underlying materials.
Press Fitting
Press fitting is the act of pushing one component into another with pressure to develop a secure fit. This methodology is easy to use and powerful, needing no further fasteners. You can depend on press fitting for connections that are reliable over a range of applications.
Quality Inspection in Sheet Metal Fabrication
Visual Inspection
Visual inspection is looking for defects on the surface, dents, or scratches. Such a step guarantees quality and how it looks overall. You must perform this review on a regular basis to continue to have appealing product aesthetics.
Dimensional Inspection
The process of dimensional inspection is to take the measurements of manufactured parts to verify they follow design specifications. The process requires essential tools such as calipers, micrometers, and gauges. In order to preserve functionality, you have to confirm that your pieces are accurate.
Weld Quality Inspection
The goal of weld quality inspection is to inspect welded joints for strength and integrity. Visual inspection, ultrasonic testing, and X-ray inspection serve to help you evaluate weld quality with great effectiveness. Following high weld standards guarantees safety and reliability.
Material Thickness Testing
The testing of material thickness guarantees that the sheet metal holds the right thickness throughout its fabrication. The use of tools including thickness gauges and calipers helps with this testing. You need to observe thickness to stop vulnerabilities in your products.
Surface Finish Inspection
Surface finish inspection confirms the quality of coatings and finishes including painting, anodizing, and electroplating. You verify the evenness of application and the flaws on the surface. Higher quality finishes improve the appearance and resilience of a product.
Tensile and Hardness Testing
This kind of stress testing evaluates both the strength and hardness of the engineered metal. Instrumentation such as tensile testers and hardness testers is essential to fulfill performance standards. Running these tests is essential for you to make sure your products operate reliably in stressful environments.
The evaluation of flatness and alignment.
It is particularly important for precision components to ensure that parts are flat and aligned due to flatness and alignment testing. Straightedges, levels, and laser alignment tools support you in this procedure. Functional assembled products require correct alignment.
Load Testing
Load testing provides stress to components so they can successfully manage anticipated loads and not result in failures. For structural components in construction, automotive, and aerospace industries, this testing is of great importance. Safety requires you to confirm load-bearing capacity.
Corrosion Testing
Corrosion testing makes sure the metal is processed to withstand corrosion, mainly after the finishing processes. Standard methods such as salt mist tests and humidity tests are popular. You need to emphasize corrosion resistance in order to extend the life of your products.
Final Assembly Inspection
The final assembly inspection makes sure that everything fits together properly and that the assembled item adheres to quality and design standards. You perform your verification through the execution of functionality tests, reviews of component integrity, and the measurement steps. The final step makes certain that your product is in a state of being used.
Major Types of Sheet Metals Used in Sheet Metal Prototype Fabrication
Aluminium
Aluminium has low weight, excellent resistance to corrosion, and is simple to shape. The characteristics of excellent conductivity and strong weight ratio make it a common choice in automotive and electrical applications.
Aluminised Steel
Aluminised steel presents durability along with resistance to high temperatures. You’ll notice it being applied in products exposed to high temperatures like kitchen tools and exhaust systems because it can tolerate heat effectively without wearing down.
Carbon Steel
This metal is known to have both strength and versatility. It serves well for industrial uses, particularly within heat treatment applications to strengthen hardness. You will come across its use in construction, machinery, and pipelines.
Copper
Because of its high conductivity and corrosion resistance, copper functions excellently in electrical situations. It is clear that it finds use for sinks, roofs, and decorative elements because of its strong performance and attractive visual presence.
Galvanised Steel
To stop rust, galvanised steel is steel that receives a coating of zinc for protection. You will commonly observe it utilized in the fields of construction and automotive industries, where the resistance to corrosion is essential.
High-Strength Steel
Superior tensile strength is attributable to high-strength steel. You’ll find it in military applications, particularly in regard to armor plating and the structural components, where strength is essential.
Stainless Steel
It stands out for its excellent ability to resist corrosion and is very durable. In food processing and chemical industries, you commonly see it because of its hygienic characteristics and ability to resist chemical changes.
Titanium
Titanium is renowned for its superior strength and endurance in severe atmospheres. The resource will show up in the aerospace and medical sectors, mainly where reducing weight and achieving biocompatibility is of great importance.
Applications of Sheet Metal Fabrication
Kiosks and Vending Machines
Sheet metal fabrication is the option you can trust for the production of long-lasting kiosks and vending machines. Its flexible nature guarantees you customized solutions designed for different needs. The toughness of sheet metal gives shielding from external influences and attempts to tamper.
Construction and Security
Sheet metal acts as a structural support and improves the security in construction. It is visible in roofing, wall panels, and the frames of buildings. Its resilience ensure protection from harsh weather and its solid frame increase the security of the built environment.
Retail Displays
In retail spaces, sheet metal fabrication gives you both stylish and practical displays. Its adaptability permits the creation of creatively practical designs that appeal to consumers. It’s quite simple to turn it into shelves, racks, and signage.
Science, Medications, and Food Professions
Sheet metal fabrication is important for the functioning of science, medical, and food industries. It is available in medical machinery, laboratory apparatuses, and food processing devices. The sterile characteristics of it make it optimal for using in sterile settings.
Transportation
Sheets metal is important in the transportation industry. In the realm of manufacturing vehicle parts, it supports you from body panels to the engine components. Its compact nature improves fuel efficiency, and its high strength contributes to better safety.
Benefits of Sheet Metal Fabrication
Strength and Durability
Sheet metal fabrication results in the creation of products that can tolerate harsh situations. Incorporating metals such as stainless steel and aluminum provides you with a considerable advantage with respect to high tensile strength. This provides sustainable performance in even the most tough conditions.
Versatility
The use of sheet metal fabrication is applicable to diverse markets, including the automotive and construction industries. The method supports personalization to meet particular design requirements, rendering it ideal for original projects or niche applications.
Cost-Effectiveness
With exact cutting methods that cut down on waste, you save on material costs. As you scale up your production, sheet metal fabrication grows more affordable, due to the benefits of economies of scale.
Precision and Accuracy
CNC machining and laser cutting offer advanced methods where you obtain identical specifications each time. High precision greatly lessens errors, which in turn requires less rework and ensures that product quality is always consistent.
Easy Maintenance
Because of their ability to resist corrosion, heat, and wear, metal surfaces are quite easy to keep up. Whenever repairs are essential, they can occur quickly and economically, helping you lengthen the useful life of your products.
Conclusion
To sum up, sheet metal fabrication is a multifaceted and versatile process where the metal is bent, cut, and shaped in order to fashion components. From laser cutting and always bending, welding, and assembly, each process is essential in the creation of precision and strength. It also helps fabricators to create work of great complexity and interesting designs with the aid of tools such as the CNC machines. Irrespective of its use for the industrial, automotive, or construction sectors, sheet metal fabrication is crucial in manufacturing. Familiarity with those tools and techniques assists in achieving efficiency in any fabrication activities.
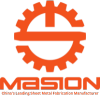