Solution
Masion - Providing Custom Progressive Die Stamping Metal Parts
We are a leading company in providing progressive die stamping services in China. We offer OEM production of various stamping parts. We are capable of dealing with diverse materials. Additionally, we use vertically integrated manufacturing processes in-house. It helps us rapidly produce progressive dies, compound dies, and more for stamping applications.
● Design and manufacturing of progressive die
● ISO16949, ISO9001-2005 certification.
● Manufacturing experience of 10,000,000 pieces
● Bulls, Tesla, Greely Auto, and LiXiang Auto appointed Supplier.



+86-18969433502

sales@sheetmetalmasion.com
Premier Progressive Dies Stamping Solutions
Masion provides a variety of progressive die precision stamping solutions. They are backed by experienced progressive die masters, stamping equipment, and technology. So, they can meet your complex precision stamped part manufacturing needs.
We provide DFM (Design for Manufacturing) services and viable processing solutions for precision stamped parts. Moreover, our professional R&D engineers and mold engineers participate in manufacturing progressive dies. On the other hand, our skilled machinists handle the mass production of precision-stamped parts. Our professional-quality inspectors conduct first-article, in-process, and final inspections. Besides this, our die masters manage the progressive dies. They all guarantee that they will neatly arrange, maintain, and repair the metal parts.
Furthermore, our vertical production management uses rapid prototyping technology. It allows us to produce stamping parts samples quickly. Besides this, it also saves on your progressive die investment costs. At the same time, we test the performance and quality of the stamped parts. It helps save a significant amount of time during your precision stamping process. Moreover, it speeds up the time to market. It quickly captures the market and reduces the cost of stamped parts. So, it ultimately increases your competitive strength in the market.
Materials
● Aluminum
(1060 6061-T6 / T5 6063 5052-O 5083 5754 7075 2A12)
● Stainless Steel
(201 303 304 316 316L 420 430 440)
● Cold-rolled sheet
(SPCC SPCD SPCE SPCF SPCG)
● Copper
(H59 H62 H65 H68 H90 C10100 C11000 C12000 C51100)
Stamping Dies
Progressive Dies
Manufacturing Size
- Aluminum
Thickness:0.6mm – 4mm
Size:1220mm * 2440mm
- Stainless Steel
Thickness:0.5mm -3mm
Size:1220mm * 2440mm
- Copper
0.5mm – 4mm
1200mm * 4000mm
- Cold-rolled sheet
Thickness:0.5mm – 4mm
Size:1500mm * 6000mm
Stamping Presses
Total 75 machines
1 unit of 500 tons,
1 unit of 400 tons,
5 units of 250 tons,
1 unit of 200 tons,
12 units of 160 tons,
10 units of 110 tons,
25 units of 80 tons,
14 units of 60 tons,
3 units of 45 tons,
2 units of hydraulic presses.
Additionally, there are 20 robots for automatic feeding.
Surface Finish
● Powder Coating
● Anodizing
● Electroplating
● Trivalent Zinc Plating
● Hot-Dip Galvanizing
● Passivation
● QPQ (Quench-Polish-Quench)
● Dacromet Coating
● Sandblasting
● Polishing
● Silk Screening
● Phosphating
● Baking Paint
● Heat Treatment
● Electrophoretic Coating (E-Coating)
● Physical Vapor Deposition Coating (PVD Coating)
Progressive die stamping is also called continuous die stamping. It is an advanced and precise metal stamping technology. So, it is commonly used for the mass production of metal-stamped parts. Besides this, the technical challenges of progressive dies are primarily concentrated on the design and production of the die itself. This is because all stamping processes need to be incorporated into the progressive die. Here each stamping process is completed independently within its die cavity, i.e. punching, bending, drawing, and trimming. So, each cavity performs a separate task without interference from other processes. As the feeder machine advances the material, it progressively feeds the coil into the entire die cavity. It helps complete the entire stamping process. This tests the technical and production capabilities of a precision stamping manufacturer. This whole process requires the assistance of experienced die engineers and a team to complete a highly challenging task.
Furthermore, a progressive die functions like an integrated system. According to process sequence requirements, the material (typically less than 2.5mm thick) is sequentially fed into the die cavities. It is usually done by feeder machines. Here, cutting, blanking, bending, punching, trimming, drawing, threading, embossing, coining, and stripping are all carried out in a single pass. They all help complete the entire stamping process at once. Ultimately, the stamped products are manufactured to the required specifications.
Progressive die stamping is a highly efficient production technology. It can deal with the mass production of various complex-shaped stamped parts. Due to its continuous stamping action, the entire production process can be shortened. So, it eventually reduces the production costs.
What is the Progressive Die Stamping?


The Pros and Cons of Using Progressive Die Stamping
Progressive die manufacturing processes are critical tests of a manufacturer’s technical capacity and capability. The initial design and manufacturing costs are high. It takes longer to produce the mold compared to standard molds. Moreover, it benefits from high-efficiency production in the long term. So, it can reduce the overall production cost and cycle of the stamped parts. It also minimizes the risk of quality issues. Thus, progressive dies are suitable for stamping large volumes of complex parts. For small quantities and simpler structures, progressive die stamping is not recommended. Because its focus is more on cost savings. Overall, progressive die stamping provides several production advantages and disadvantages. Here we list some for your reference.
Progressive dies have complex structures. They need high-precision manufacturing. Besides this, they have a lengthy production cycle and lower material usage. So, this process requires more cost.
Furthermore, the progressive die sequentially punches the internal and external shapes of the workpiece. So, each stamping operation introduces positioning errors. So, this makes it difficult to maintain stable and consistent relative positioning.
Disadvantages of Progressive Dies:
Here are some advantages of progressive dies.
1. Faster Production Efficiency
Progressive die stamping is a continuous process of feeding, stamping, bending, and deep drawing. So, it allows the rapid production of stamped parts suitable for mass production.
2. Effective Material Waste Reduction
The whole coil is optimized in design. So, it gives better material usage and reduces waste.
3. High Precision and Consistency
Tolerances are as tight as +/- 0.05mm. Besides this, automated stamping reduces the need for product movement and positioning errors. So, it ultimately increases the quality of the stamped parts.
4. Reduced Cost per Part
The production speed of progressive dies is fast and requires less labor. So, it reduces the production time and cost per part compared to conventional stamping.
5. Improved Safety Operations
Progressive die stamping generally includes safety guards. So, it does not demand to reach inside the mold. The entire stamping operation is automated. So, it reduces the need for manual intervention. The mold includes monitoring equipment that can quickly check its operational status to prevent damage.
6. Wide Range of Material Choices
Progressive die stamping is used to deal with various materials. They may include aluminum, carbon steel, and copper.
7. Flexible Design Options
Progressive dies can be simple or complex. So, you need to design according to the product’s specifications.
8. Long Lifespan of Progressive Dies
Generally, progressive dies are made from durable and wear-resistant materials. These materials can be die steel or tool steel. So, these dies can be used repeatedly. They reduce the need for frequent redevelopment.
9. Increased Production Capacity
They significantly increase the number of units produced per unit time. This ultimately increases the overall production capacity.
Moreover, it has fast production speed and high efficiency.
Advantages of Progressive Dies
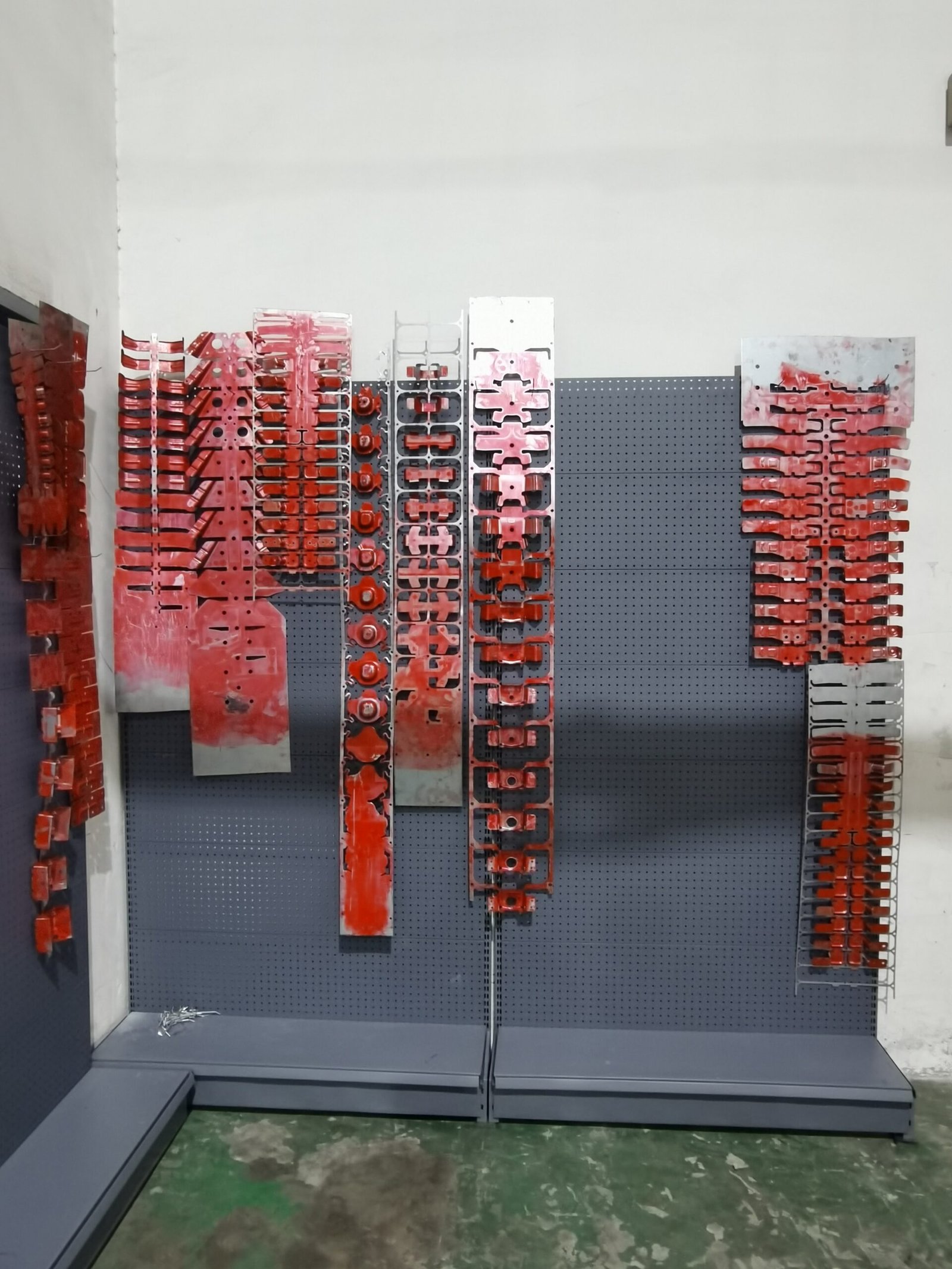

Step-by-Step Process of Progressive Die Stamping
Progressive die metal stamping is a comprehensive process. It helps integrate multiple processes, i.e. cutting, stamping, flanging, bending, deep drawing, three-dimensional forming, and assembly. It requires feeding coil stock step-by-step into the progressive die cavities. Moreover, it uses feeding equipment. Here’s a brief overview of the entire process:
1. Die Design
The progressive die stamping designs may include the following steps;
Draw Analysis: Here we analyze the structure of product drawings. It may include the complexity, dimensions, materials, tolerance requirements, and quantity of stamped parts.
Material Selection: After that, we select the appropriate metal material according to the material requirements of the stamped parts drawings. These generally are aluminum, carbon steel, galvanized sheet, and copper. We typically choose metal coil stock.
Die Material Selection: Then we select the material for the die. It is based on the material of the stamped products, i.e. die steel, tool steel, etc.
We design the die based on product deformation, stamping processes, and material characteristics.
2. Die Manufacturing
This process usually includes;
Machining Die Parts: We make each part of the die according to design drawings using precision equipment. These equipment are usually CNC lathes, precision grinding machines, and slow wire EDM.
Die Component Assembly: Then we assemble each machined die component.
Die Placement and Testing: So, here we assemble the die. We use a crane to install the upper and lower dies (male and female dies) onto the press. Then we conduct trial stamping tests. Here we adjust it continuously to achieve optimal results. Moreover, we guarantee that each stamping process is completed smoothly.
Installing the Coil Stock: Then we load the selected coil stock onto the press. It helps feed the material automatically.
3. Stamping Process
Progressive stamping starts with the machine. Feeders allow the coil to feed into the progressive die cavities. Here, the material continuously passes through the die cavities. It is then complete the entire stamping process for the parts.
4. Part Separation
Here, we eject the finished stamped parts using an ejector. Then we process them into the final required sizes and shapes.
5. Inspection and Post-Processing
This process may include;
Quality Inspection: It’s a Post-processing of the stamped parts. Here we make sure that part meets the tolerance requirements specified in the drawings, Then we inspect the dimensions, tolerances, and appearance. So, it helps us get the accurate part based on drawing needs.
Deburring: Generally, light burrs are produced during the stamping process. Then they are ground off to guarantee the product is smooth and safe to handle.
Surface Treatment: We perform surface treatment operations. They may include plating, painting, oxidation, or applying a dacromet coating on stamped parts. Thus, it increases their corrosion resistance and aesthetic appeal.
6. Secondary Processing or Assembly
Sometimes we need additional processing like threading, drilling, or milling. So, it may include.
Assembly: If the stamped parts need to be assembled onto other products. We can use assembly operations such as riveting, welding, etc., are performed.
Packaging and Shipping: At the end, the stamped products undergo a final inspection. They are packed in wooden crates, cartons, or pallets and shipped.


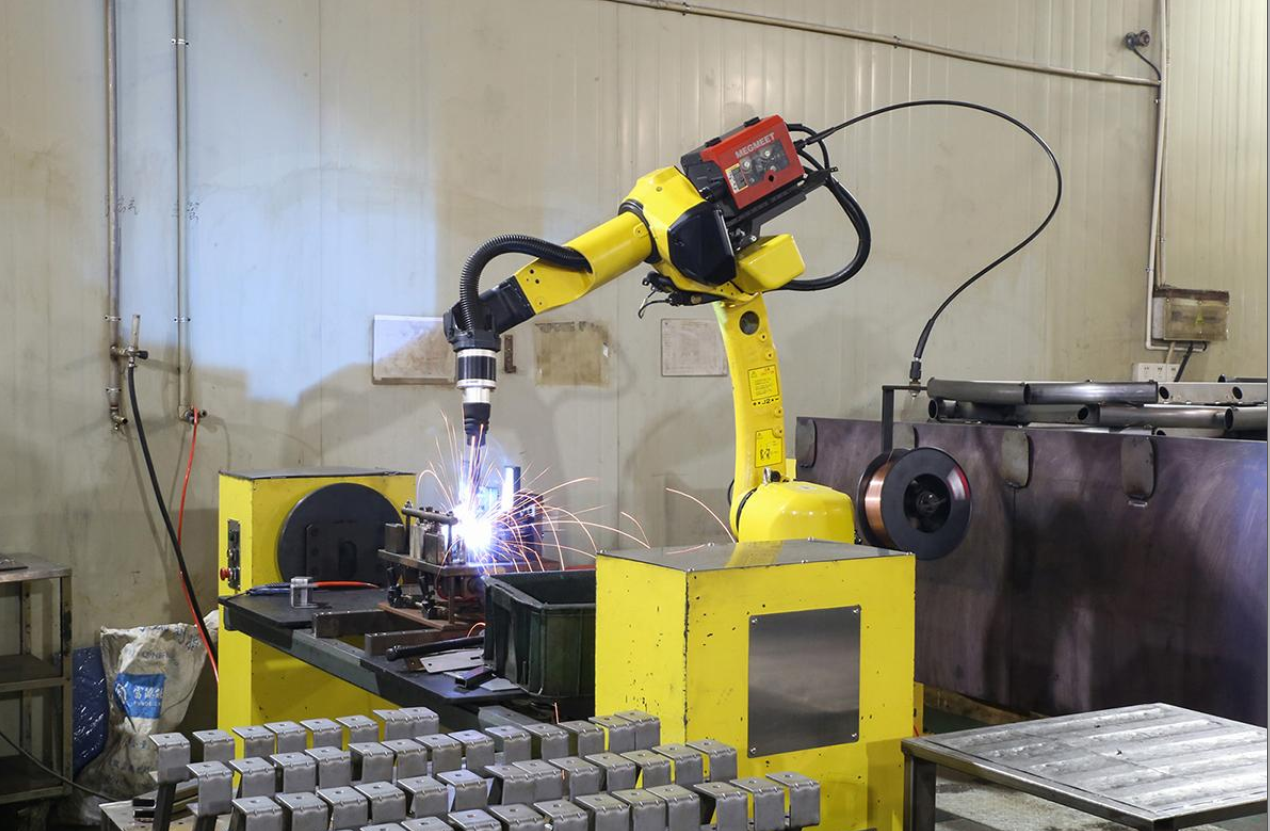
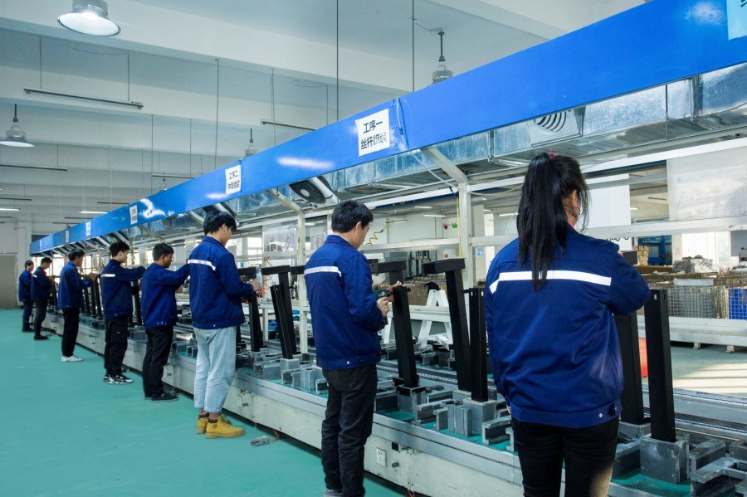
Why Choose Us For Progressive Dies Stamping?
Masion has an extensive experience in progressive die design and manufacturing. We take pride in manufacturing over 10,000,000 progressive die-stamped parts. Besides this, we hold ISO9001-2015 and ISO16949 quality management certifications. Masion provides professional services to major enterprises. These may include CRRC and Geely Automobile. So, if you are looking for a reliable progressive die-stamping supplier. we are an exceptional choice. Here are some reasons to choose us:
1. Quality Management System
We have ISO16949 and ISO9001 quality management certifications. So, we help our customers in getting AS9100 and NIST 800-171 certifications.
2. Internal DFM and Mold Design
We operate six manufacturing plants. They all are dedicated to the design and production of molds. Besides this, we have 20 years of experience as mold engineers. They are responsible for designing professional molds. Moreover, we use a strong ERP system. It increases supplier control, cost control, and production lead time control.
3. Support for Large Projects
We have been serving large projects and collaborating with renowned clients for the last 20 years. Our main customers are Geely, Lifan Motors, Tesla, Topoe, and Xusheng. So, we have extensive design and production experience.
4. Material and Thickness Diversity:
We have extensive experience with various materials. These may include stainless steel, aluminum, titanium, brass, and copper. Our Material stamping thickness ranges from 0.1mm to 2.5mm.
5. Flexible and Adaptive Solutions
We cater to both large clients with bulk orders and smaller clients with smaller orders. Here, our flexibility and adaptability help deal with any project requirements.
6. Vertical Integration
We are using all the processes, i.e. welding, riveting, bending, laser cutting, assembly, and surface treatment. So, it controls costs and quickly provides cost-effective production solutions.
7. Advanced Stamping Equipment
We are equipped with China’s most advanced machinery. So, they can produce high-precision stamped parts with excellent accuracy. So, they are good options for handling various complex projects.
8. Progressive Die Monitoring: We use mold monitoring to detect any potential part ejection issues. It helps us protect the mold from damage.
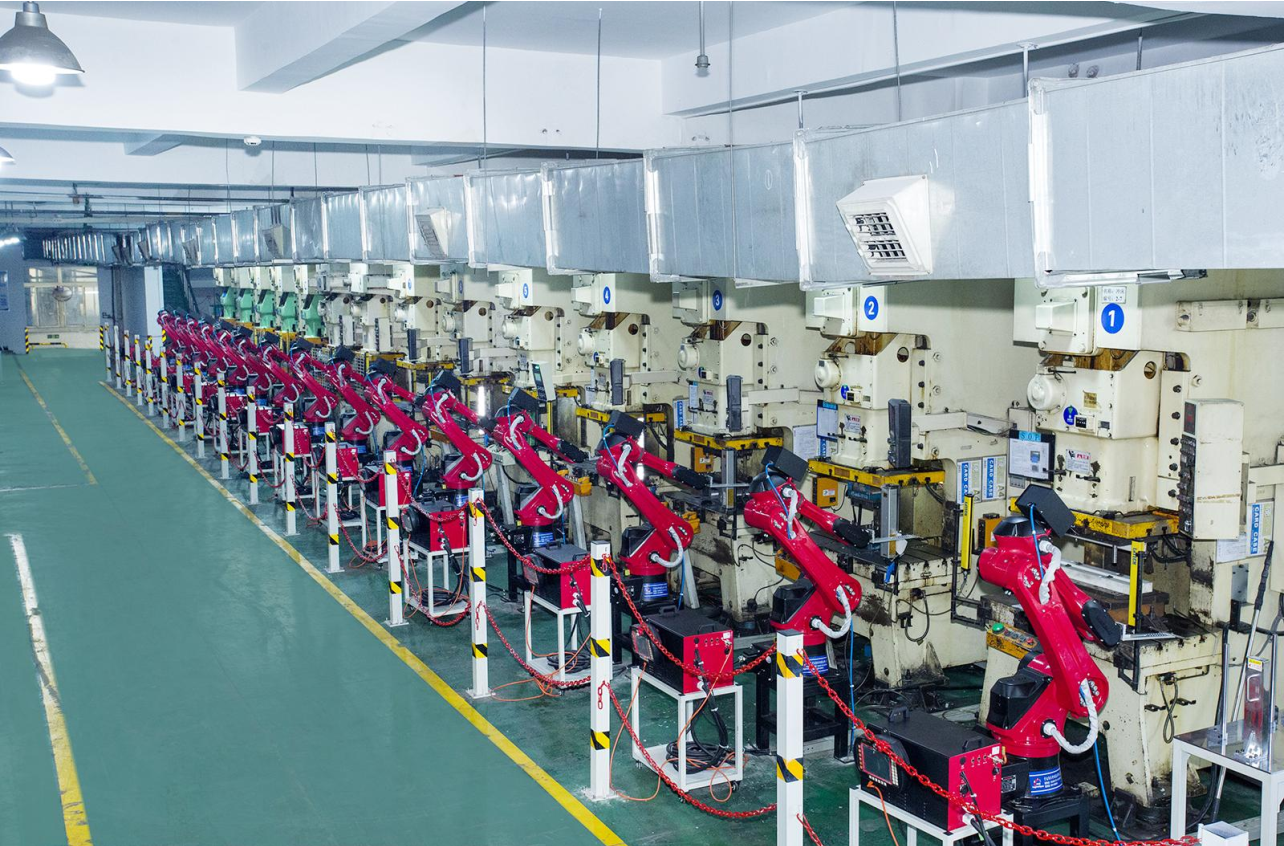
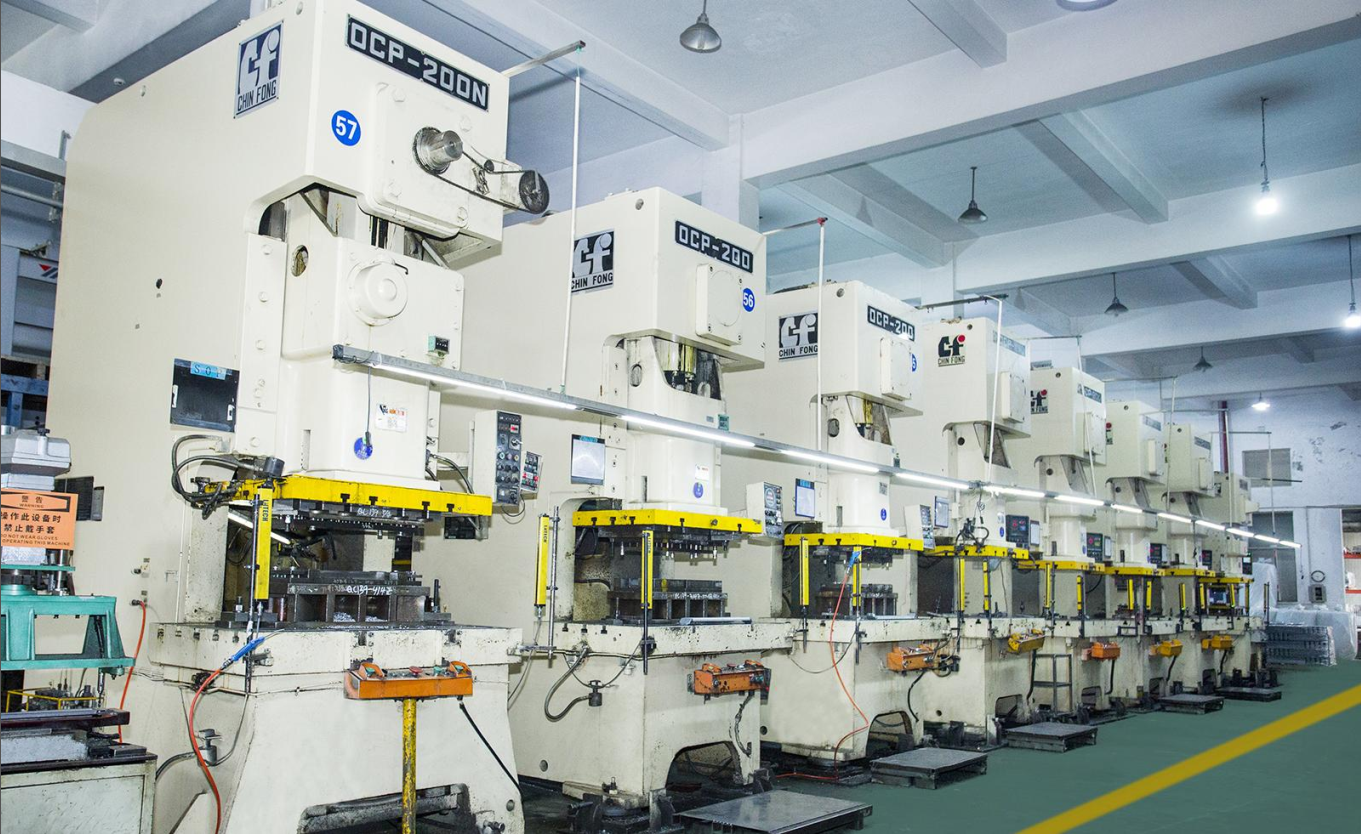
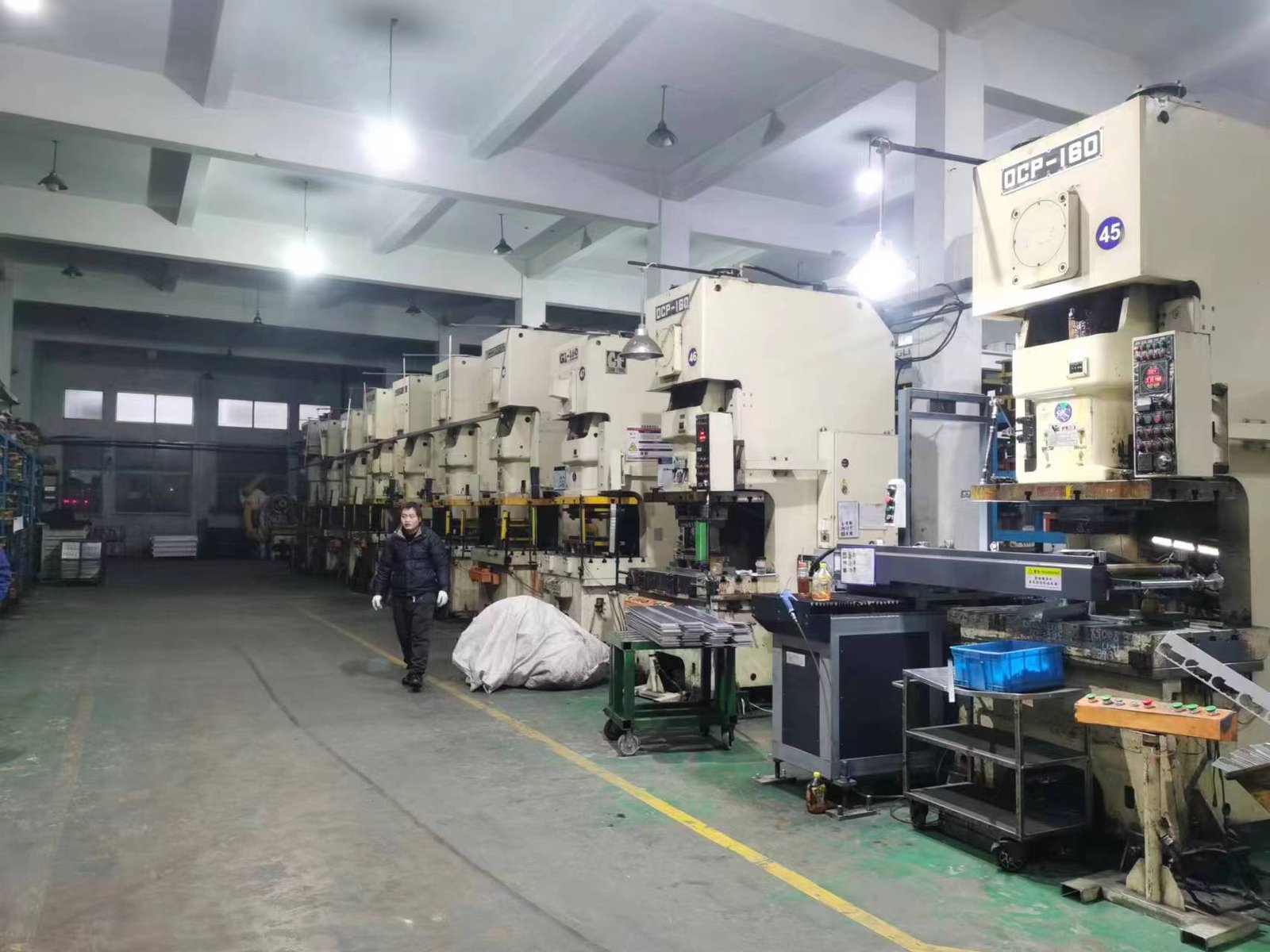
Design And Manufacturing of Progressive Stamping Dies
We always make sure to make Precision Stamping Dies. These may include progressive dies and compound dies. Below is a brief introduction to the Progressive Stamping Dies
Structural Principle: It is generally like a single station with multiple stamping processes. It can complete processes like stamping and blanking within the die cavity. However, it cannot perform multiple processes like bending and curling together, So it may require additional molds. Moreover, Compound dies are commonly used for the stamping of simple-designed parts. They work surprisingly well with medium to small-scale production.
Application: Compound parts may include washers and gaskets. Moreover, they perform a single stamping operation for processes like blanking or bending.
Production Efficiency: A single mold station performs multiple stamping actions. Therefore, it works well for small-scale stamping. Its efficiency is lower compared to progressive dies.
The complexity of the Mold: It’s structure is simpler, with only one station for processes, i.e. blanking or bending. This simplicity lowers costs and less time for design and production.
Compound Dies:
Structural Principle: We have many stations. These complete the whole stamping process inside a die cavity. So, these processes are blanking, stamping, bending, shearing, drawing, curling, threading, etc. Generally, they are used for continuous stamping. So, it is suitable for large-scale production. Moreover, they are compatible with automatic punch press processing.
Application: Progressive dies has a wide scope of applications producing large quantities. These products are identical. So, the continuous process is suitable to opt for them. Besides this, these parts are mainly used in industries like connectors, terminals, and plugs.
Production Efficiency: The design of various stations helps us to get the efficient completion of stamping processes. Moreover, it significantly boosts production efficiency.
The complexity of the Mold: Progressive dies with more stations are more complex. They may need precision equipment for manufacturing. On the other hand, the design and production need higher costs and time.
Progressive Dies
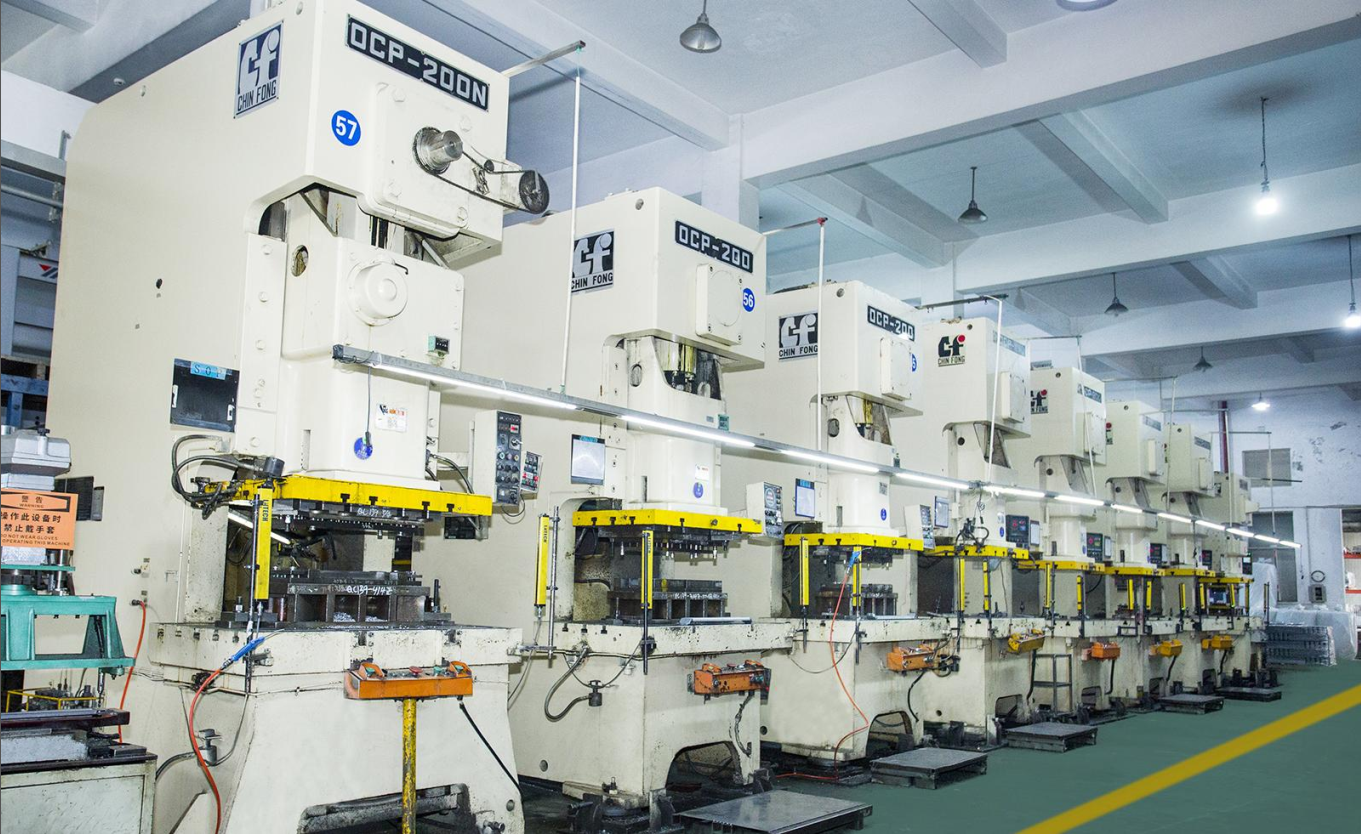
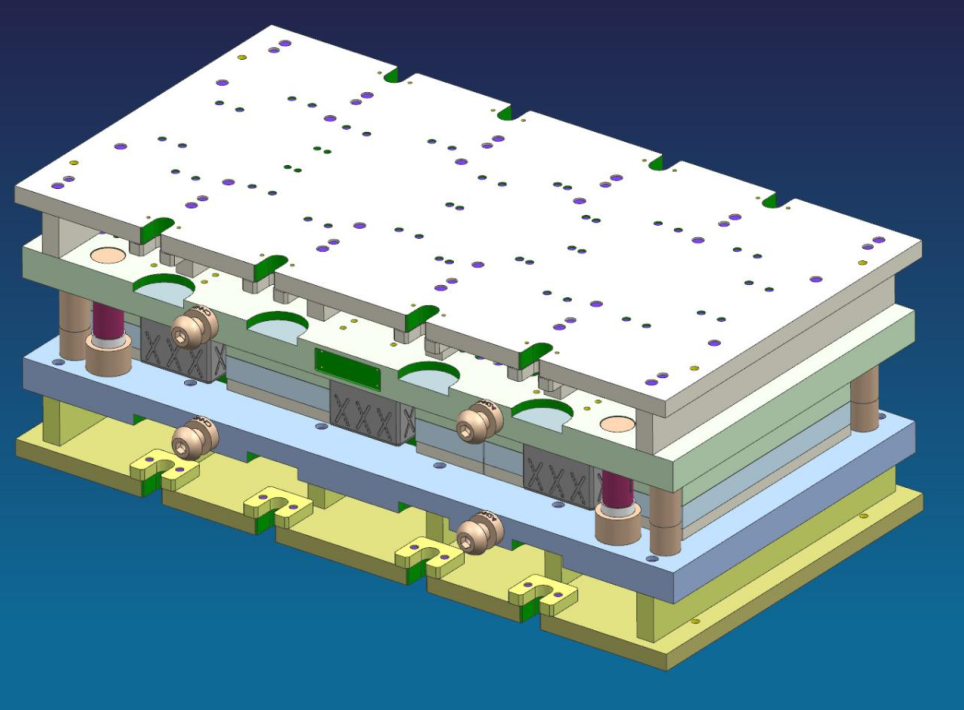
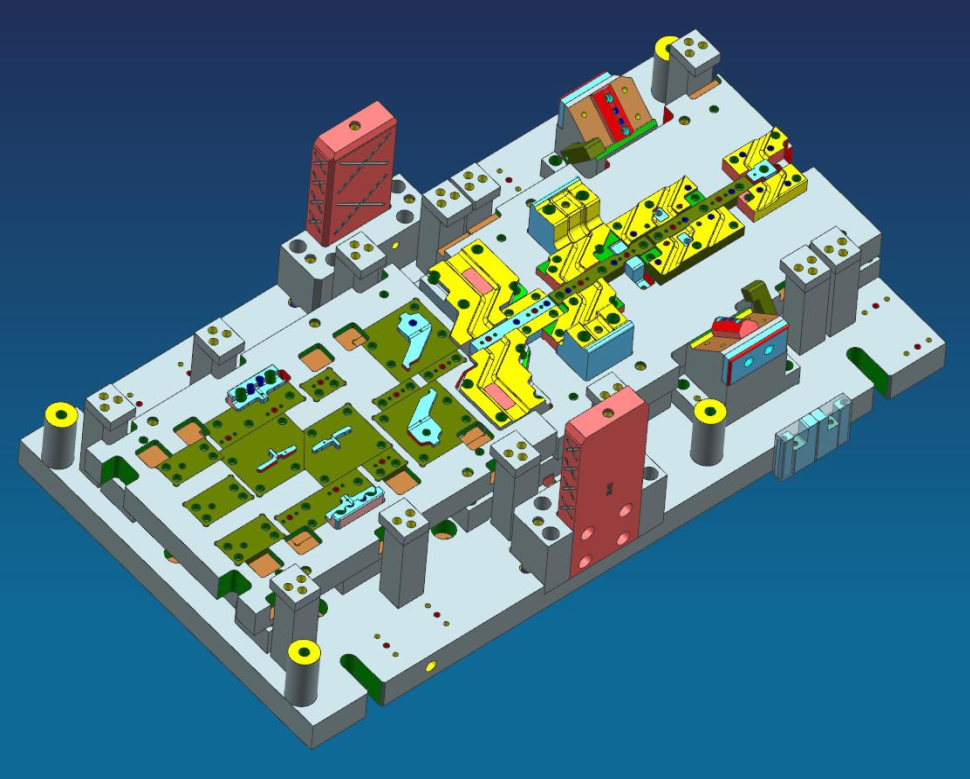
Certificate Of Progressive Dies Stamping Parts
● ISO9001 Quality Management System
● ISO14001 Environment Management System Certification.
● TS16949 Automotive Industry Quality Management System
● FSC Forest Stewardship Council
● Patent 47 patents of invention
● CE CONFORMITE EUROPEENNE (As you need, we could apply)
● RoHS Restriction of Hazardous Substances (As you need, we could apply)
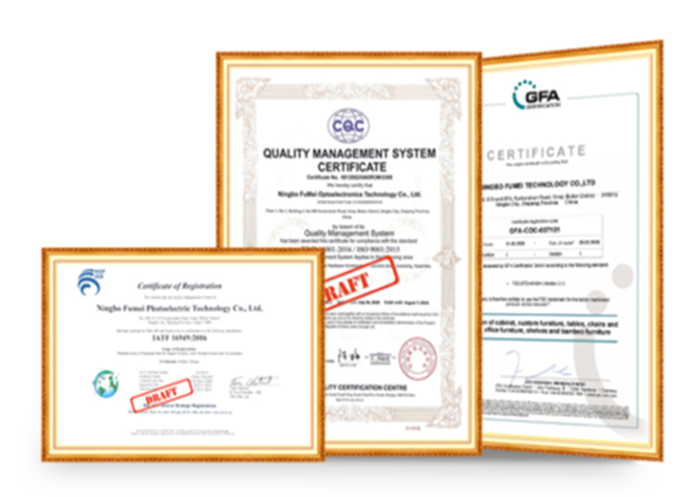
Explore our PROGRESSIVE DIES STAMPING Parts Gallery
Progressive Dies Stamping Industries
We’re experts in precision stamped parts. Our parts find extensive applications in various industries. These well-known industries include the automotive, aviation, defense, maritime industry, and other high-end industries. Additionally, our precision-stamped parts are commonly found in everyday life in industries, i.e. such as telecommunications, robotics, fitness equipment, construction, machinery, consumer goods, and more. So, below are some common applications for precision stamped parts in these industries.
● Power sockets
● USB plugs
● HDMI interfaces
● Metal casings
● Heat sinks
● Precision mounts and frames for mobile phones, tablets, and laptops
● Battery clips
● Metal frames for LCD or LED screens
● Miniature push-button switches, contacts
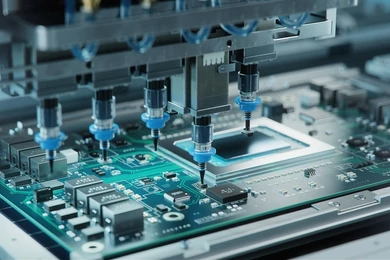
● Outer panels, inner doors, outer panels, roofs, front and rear bumpers
● Chassis frame, chassis support components
● Hood, transmission system cover, engine assembly
● Suspension system support components, suspension arms
● Dashboard, inner door trim panels, seat structures
● Fuel tank casing and bracket
● Exhaust pipes and exhaust system support components
● Metal bracket supporting the vehicle’s battery
● Seat slides, hood inner panels, trunk inner and outer panels

● Solar panel frames
● Mounting system components
● Grounding clips
● End clamps and mid clamps.
● Metal Rails
● Junction boxes
● Cable management accessories
● Connectors and adapters
● Lightning protection components

- Laptop metal casing and heat sinks
- Camera body metal frame and protective cover
- Machinery body metal frame and protective cover
- Watch metal casing and adjustment knobs
- Mixers, coffee machines, ovens metal casings, and internal supports
- Electric shaver and hair dryer metal structural components
- Speakers’ casing and internal metal support structures
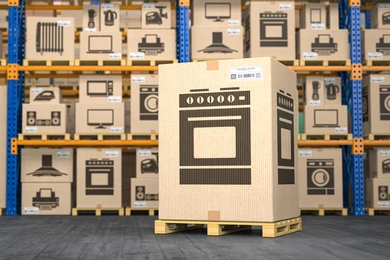
Checkout our Another Manufacturing Solutions
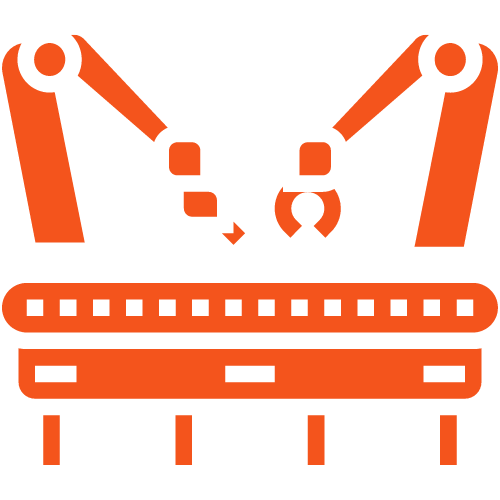
Sheet Metal Fabrication
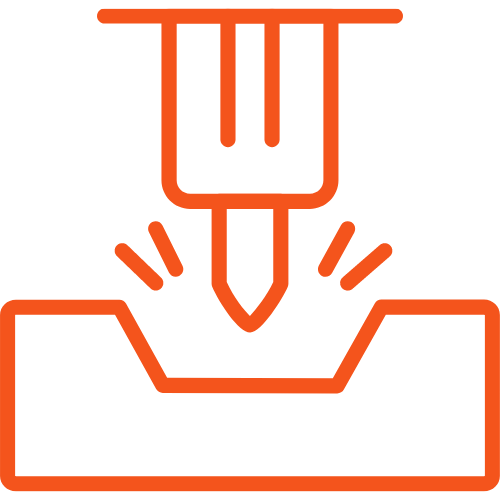
Pipe and Tube Processing

Laser Cutting
We’re here to provide you with custom solutions for various complex sheet metal manufacturing projects.
Masion gives custom processing services solutions for various shapes. They may include round, square, and special-shaped metal tubes.
Masion provides customized precision laser cutting services solutions. They are used for various materials and complex shapes.
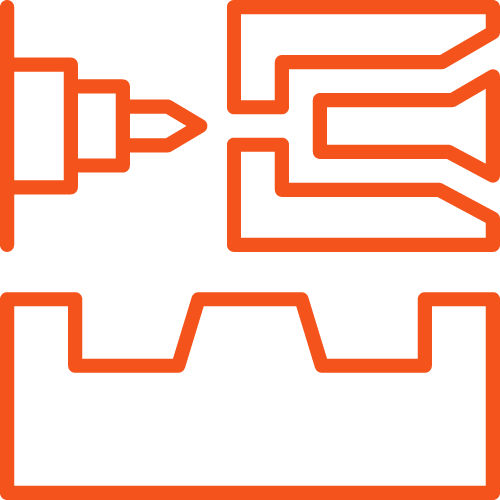
Plastic Injection

Sheet Metal Assembly

Contract Manufacturing
We give facility for the Production and manufacturing of various assembled plastic injection parts. Besides this, they are supported by multiple processing services solutions.
We provide sheet metal parts assembly services, suitable for large, small, various projects complex sheet metal parts assembly.
We have Vertical Integration Production and Assembly of Sheet Metal Parts Solution.
Resources
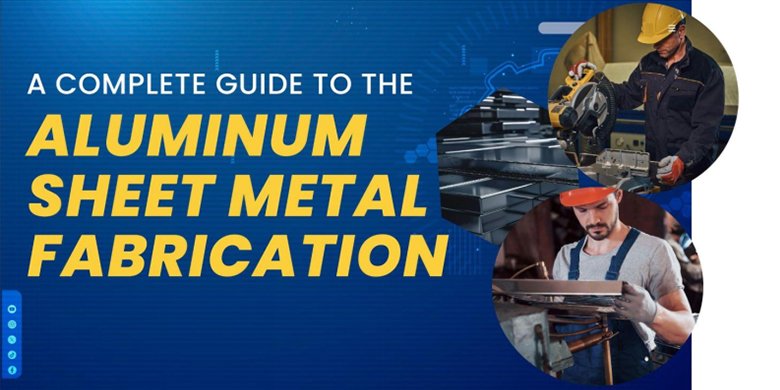
Aluminum sheet metal fabrication converts long sheets into specific shape. So, in this article, we will give you a complete guide to this process and its demands in the manufacturing industry.
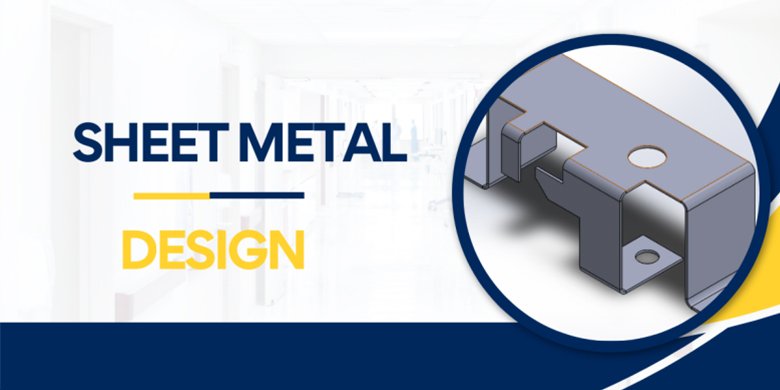
You can learn some tips for sheet metal design from this article. Understand the need, importance, and why the sheet metal design is crucial to play a key role in diverse industries.
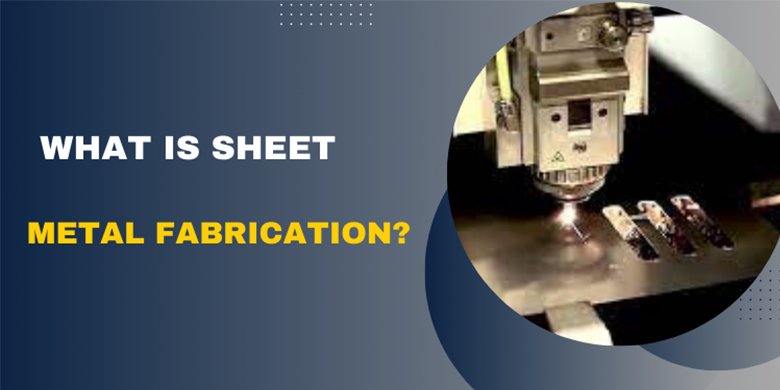
This guide allows you to create good sheet metal parts. We will start with the basics then discuss design best practices. Sounds exciting? Let’s delve in deeper to uncover facts.
Frequently Asked Question
Q: What materials can your progressive die stamping process handle?
Our progressive die stamping can handle a wide range of materials. We currently use materials, i.e. aluminum, cold-rolled steel, hot-rolled steel, brass, copper, bronze, nickel and nickel alloys, titanium alloys, stainless steel, etc. So, if you have other materials in mind, please contact us.
Q: Can you design and manufacture progressive dies?
Absolutely yes, our company has over 20 die designers and makers with many years of experience. We also have various equipment for mold manufacturing, i.e. slow wire EDM, CNC machining centers, precision surface grinders, etc. So, you can confidently entrust your progressive die-stamping projects to us.
Q: What is the lifespan of your progressive dies?
Our die designs usually have a service life of 500,000 times. Besides this, we maintain our dies regularly. So, if the die is damaged due to our improper use. We will bear the cost of re-making the die. You don’t have to worry.
Q: What is the precision of your progressive die stamping?
Our progressive die-stamped parts generally achieve a precision of ±0.05mm (0.002”). Although the complexity of the stamped parts might affect this. We strive to meet the precision requirements of your progressive die-stamped parts.
Q: How do you optimize progressive dies to reduce material waste?
We use the following ways to optimize our progressive dies.
- Mold Optimization: We use design software to calculate the dimensions. They may include material layout and spacing. It helps us reduce waste in the actual processing.
- Material Simulation Analysis: We use material simulation software to simulate the stamping processes. Besides this, we optimize where material waste occurs.
- Choosing the Right Material Size: We select coil materials of appropriate widths based on calculated die sizes. It minimizes the waste during stamping.
- Collinear Stamping Technique: We use collinear stamping for batch linear contour stamping. Here the common edges are stamped only once. So, it significantly reduces the material waste.
- Mold Maintenance and Calibration: We perform regular maintenance and calibration. This measure helps us guarantee the precision of the molds. So, it ultimately reduces the material waste due to damage.
- High-Precision Feed Machines: We guarantee the feed machine’s accuracy. So, it reduces material waste during the feeding process.
Q: Can your progressive die stamping process handle automotive parts?
We are ISO16949 certified. This is a quality management certification for the automotive industry. We have many years of experience producing automotive stamping parts. Therefore, you can confidently entrust us with your automotive parts.
Q: What quality inspection standards do your progressive die stamping products meet?
Our inspection standards strictly follow the ISO16949 quality control standards. They may include dimension inspection, material testing, tensile testing, fatigue testing, hardness testing, salt spray testing, and electronic testing. Besides this, we adhere to the ISO9001 quality inspection standards for non-automotive parts. They may include material testing, dimension inspection, surface inspection, etc.
Q: I have a sample of a stamped part but no drawings. Can you help design the drawings?
Certainly, we have our own design and R&D team with extensive experience. They have all relevant design software capabilities. Moreover, we can assist in designing your progressive die stamping product and send you the drawings for review. If there are no issues with the drawings. We can quickly manufacture a sample (excluding mold manufacturing) and send it to you for confirmation. For more details, please contact us.
Q: What quality certifications do you have?
We are certified under ISO9001-2015, ISO16949, and other relevant standards. If you require additional certifications, please contact us.
Q: Can you provide design and mold manufacturing services separately? I want to produce progressive die-stamped parts myself.
Our progressive dies are generally developed and manufactured in-house for our stamping use. If you are interested in purchasing progressive dies. Masion can refer you to relevant factories. If you need our production services, we can adjust our schedule to see if we can help produce the molds for you. Please contact us for further discussions.