Sheet Metal Laser Cutting | Complete Guide
Table of Contents
ToggleAs the world is progressively moving towards development. Everyone is shifting towards modern and smart solutions to make life easier. So, sheet metal laser cuttings serve for the same reasons. It is like a game changer in the metal fabrication industry. It is used to cut the metal sheets into precise metal parts. Besides this, it can deal with multiple ranges of material. So, in this article, we will talk about the working of sheet metal laser-cutting. Besides this, we will discuss its limitations and wide applications in the diverse market.
Laser Cutting of Metal Sheets and Discuss Its History
Sheet metal laser-cutting is now one of the most popular processes in the fabrication industry. It is known for its precision, speed, and versatility. Besides this, it uses high-powered laser beams. So, it helps them precisely cut through various metals. It requires minimal heat-affected zones.
So, the roots of laser cutting trace back to the mid-20th century. It has now become a significant milestone in manufacturing technology. Today, it is one of the most important processes for dealing with complex shapes. It has a wide scope of applications in multiple industries. They may include automotive, aerospace, marine, electronic, and consumer goods.
Sheet Metal Laser Cutting – Step-by-Step Process
So, let’s discuss in depth how the Sheet Metal Laser-Cutting technique works. Here is the complete process included in its working.
Design Making
Here, first of all, the engineers need to create digital designs. This is usually done by modern tools, i.e. Computer-Aided Design (CAD). In this design, the designers specify the dimensions, shapes, and cutting parts. Besides this, it is important to make an efficient design. It may not lead to material waste and improve the overall efficiency of the sheet metal laser-cutting process.
Material Selection
Every sheet metal has a specific shape, size, thickness, and other properties. The sheet metals may include steel, aluminum, or stainless steel. So, before starting working on sheet metal laser-cutting, make sure that the material is suitable for cutting. Besides this, the material must be thoroughly inspected for defects and other imperfections. Moreover, once the material is decided and it is ready to use. You must place it securely onto the cutting bed of the laser machine. Once it is cut, make sure to perform proper cleaning of the material after cutting.
Sheet Metal Laser Cutting Machine Setup
As we know, sheet metal laser cutting equipment are highly precise and versatile. But besides this, they require proper setup for each job. So, the operator’s input parameters, i.e. laser power, cutting speed, focus depth, and assist gas pressure into the machine’s control interface. These settings vary based on the material type, thickness, and desired cutting quality.
Laser Cutting
One of the major parts is the emission of a high-powered laser beam. It is usually created by a CO2 or fiber laser source. So, the beam is first directed onto the surface of the sheet metal. Here it rapidly heats and melts the material. Besides this, we ensure the cutting path is defined in the design file. Moreover, the laser beam is guided by computer-controlled mirrors or lenses. It will help us get precise and accurate cuts.
Cutting Path Guidance
Laser-cutting machines always follow the cutting path. We can highlight the design in micrometer precision. So, this path may consist of straight lines, curves, or complex shapes. Its types may depend on the part design. Here the advanced CNC systems monitor and adjust the position of the laser beam in real-time. Moreover, it helps maintain accuracy. Besides this also helps in providing consistency throughout the cutting process.
Cooling and Debris Removal
Here the laser produces intense heat. This heat can result in thermal stress and distortion in the material. So, we can eliminate this issue using some laser cutting systems that use cooling methods. These cooling methods can be compressed air or coolant jets. Additionally, some assis gases like oxygen, nitrogen, or air help blow away the molten metal. They also remove the debris from the cutting zone. So, it overall avoids interference with the laser beam. So, consequently gives clean cuts.
Quality Inspection
So, once sheet metal laser cutting is complete, the cut parts undergo a continuous inspection. This inspection verifies dimensional accuracy, edge quality, and overall finish. Moreover, it includes many manual or automated measurement techniques, such as calipers or optical scanners. So, here we note down every deviation from the design specifications. Besides this, we provide adjustments for cutting parameters if necessary.
Post-Processing, if Required
This method completely depends on the scope of applications and requirements of the process. So, here your cut parts may undergo additional finishing operations. These operations can be deburring to remove sharp edges, surface grinding, or polishing for cosmetic purposes. It can also include bending to get specific shapes or angles. We generally perform post-processing steps to fulfill your needs for each part. This may include manual or automated techniques.
Waste Management
So, it is common that if we use Laser cutting process. It produces scrap materials. These scraps can be cut-off pieces, slag, and dust. So, here proper waste management practices are necessary to reduce the environmental impact. Moreover, it saves the workplace integrity. Additionally, we can recycle the scrap materials. On the other hand, the hazardous by-products, i.e. fumes or dust. We can use filtration systems and dispose of them according to regulations.
Laser Metal Sheet Cutting Essential Design Tips
Here are some design tips for sheet metal laser cutting. They require careful consideration to increase the overall efficiency of the process. Additionally, these tips will also reduce waste. They will give us optimal part quality. So, let’s discuss all these here.
1.Avoid Complex Designs: The simple designs are easy to handle. So, they help reduce the cutting time and material waste. So, you must avoid using complex shapes and features in your design parts. Otherwise, it will lead to complexity and ultimately add significant value to the metal part.
2. Use Standard Thicknesses: If we opt for the standard thickness of sheet metals. It will help reduce the overall cost. Besides this, you can consult with material suppliers to get the appropriate material based on your requirements.
3. Do not use Sharp Corners: The sharp internal corners are relatively difficult to cut. So, it may result in stress concentrations. In this case, you can use round or fillet corners. So, It will eventually improve cutting accuracy and part durability.
4. Use Bend Relief: If your design parts have bends. You can add bend reliefs or fillets at the bend radius. They will help you avoid material distortion. Moreover, it will give you accurate folding. Resultantly, the bend relief will help maintain dimensional consistency. So, it will reduce the risk of cracking or tearing.
5. Provide Kerf Offset: We can define Kerf as the width of the laser beam. This helps us remove the material during sheet metal laser cutting process. So, if you adjust a suitable kerf width. It will give you accurate dimensions. This kerf offset has a wide scope of applications in tight tolerance applications.
6. Feature Orientation: Make sure you provide the appropriate orientation to the different features. These features may include holes, slots, or tabs. Their orientation will help us align with the cutting direction whenever possible. Moreover, it will reduce the cutting time. Besides this, the orientation of the appropriate feature also reduces the burrs or distortion on the finished part.
7. Clearances and Tolerances: Always provide adequate clearances between features and edges. This strategy helps prevent interference during cutting. So, whenever you specify the tolerances, always consider the laser’s beam diameter and the material’s thickness. They both will provide you the dimensional accuracy.
8. Include Tabs or Bridges: Sometimes, the complex parts need effective designs. So, for its effectiveness, you can include tabs or bridges to the surrounding material. It will eventually keep the part in place during cutting. Moreover, you can avoid damage by removing these tabs and bridges in post-processing.
9. Optimize Nesting: You can arrange parts efficiently on the sheet. It will eventually increase the material usage and reduce the scrap. In this case, you can use nesting software or consult with your fabricator. They will help optimize part placement. Additionally, they will give the most appropriate orientation for the most economical production.
Suitable Materials for Sheet Metal Laser-Cutting Process
Here are some suitable materials and their alloys for sheet metal laser cutting. We have discussed their tolerance ranges and their possible applications in diverse fields.
Material | Alloys | Tolerance Range | Applications |
Stainless Steel | 304, 316, 430 | ± 0.1mm – ± 0.3mm | Aerospace, automotive, electronics, machinery |
Aluminum | 6061, 5052, 7075 | ± 0.1mm – ± 0.3mm | Aerospace, automotive, signage, consumer goods |
Carbon Steel | A36, 1018, 1045 | ± 0.1mm – ± 0.3mm | Construction, automotive, machinery, appliances |
Galvanized Steel | DX51D, SGCC | ± 0.1mm – ± 0.3mm | Construction, automotive, HVAC, electrical |
Titanium | Grade 2, Grade 5 | ± 0.1mm – ± 0.3mm | Aerospace, medical implants, marine |
Copper | C11000, C12200 | ± 0.1mm – ± 0.3mm | Electronics, plumbing, decorative applications |
Brass | C26000, C36000 | ± 0.1mm – ± 0.3mm | Plumbing fixtures, musical instruments, jewelry |
Nickel Alloy | Inconel 625, 718 | ± 0.1mm – ± 0.3mm | Aerospace, chemical processing, marine |
Mild Steel | ASTM A36 | ± 0.1mm – ± 0.3mm | Construction, automotive, machinery, furniture |
Spring Steel | 1095 | ± 0.1mm – ± 0.3mm | Springs, knives, cutting tools, automotive |
Types of Lasers or Machines for Sheet Metal Laser-Cutting
Here are some commonly used lasers to perform sheet-metal laser cutting operations.
CO2 Lasers
CO2 lasers are comprised of carbon dioxide, nitrogen, and helium gases. Here, the resonator first emits the laser beam. Then this laser beam moves towards a series of mirrors and lenses. Its wavelength is approximately 10.6 micrometers. Besides this, it generally operates in the infrared spectrum. Additionally, this type of laser can be used for a range of materials. They may include, mild steel, stainless steel, aluminum, titanium, plastics, and wood.
These suitable materials must have a thickness of up to 25 millimeters (1 inch) or more. So, CO2 has a wide scope of applications in cutting the fine details. Besides this, it also provides smooth edges and minimal burrs. But if we talk about the cost, CO2 lasers are more expensive than other lasers.
Fiber Lasers
It is mainly comprised of optical fibers. These fibers are doped with rare-earth elements. This may include, ytterbium that produces the laser beam and allows it to move towards the cutting head via fiber optics. Additionally, the fiber lasers have relatively shorter wavelengths, i.e. 1.06 micrometers. So, this laser can deal with materials having 25 millimeters (1 inch) medium-thickness. Moreover, the most commonly used materials are stainless steel, carbon steel, aluminum, brass, and copper.
Furthermore, fiber lasers are efficient. Besides this, they need less maintenance as compared to CO2 lasers. So, they are the best fit for sheet metal laser cutting. But this type of laser gives rough edges on cutting. So, it is not suitable for non-metallic materials.
Crystal Lasers
Crystal lasers or Diode-pumped solid-state lasers usually use a solid crystalline medium. This may include neodymium-doped yttrium orthovanadate (Nd: YVO4) or neodymium-doped yttrium aluminum garnet (Nd: YAG)
So, here semiconductor diodes provide high power to the specific gain medium. As a result, it emits laser light with different wavelengths. The most common wavelength is about 1.064 micrometers. Crystal lasers are suitable for multiple materials, i.e. stainless steel, aluminum, titanium, plastics, and ceramics. Additionally, this type of laser is highly stable and has precise control over pulse duration. Besides this, it can deliver high peak powers. So, they are a suitable option for precision cutting applications.
Common Problems, their Reasons, and Solutions of the Laser-Cutting Process
Here are some common problems that you can face while working with the sheet metal laser cutting technology. Let’s discuss them with their reasonings and possible solutions to overcome these problems
Problem | Cause | Solution |
Continuous Startup | Incorrect laser mode or broken components | Check motherboard parameters, replace components |
High Voltage Ignition | Poor connections or component failures | Check connections, replace faulty components |
Uneven Cleaning | Lens or graphic issues, aging equipment | Clean lens, adjust graphics, replace equipment |
Wave Phenomenon in Outline | Loose components or software issues | Fix loose components, overhaul software |
Laser Sparking | Impurities or component failures | Address impurities, replace faulty components |
Rapid Recycled Water Heating | Excessive laser intensity or poor water flow | Reduce intensity, ensure smooth water flow |
Chiller Alarm | Voltage, water level, or component issues | Ensure proper voltage, check the water system |
Boot Failure | Loose connections or component failures | Check connections, replace faulty components |
Unstable Current | Mainboard or power supply issues | Replace the main board or power supply |
Beam Jitter | Configuration or mechanical issues | Redownload configuration, fix mechanical issues |
Data Processing Failure | Faulty connections or software settings | Check connections, adjust settings, replace parts |
Hook Misalignment | Beam or belt issues | Adjust parallelism, tighten belts |
Misalignment during Cutting | Speed, graphics, or mechanical issues | Adjust speed, correct graphics, fix mechanicals |
Serrated Edging | Speed, resolution, or mechanical issues | Adjust speed, increase resolution, fix mechanics |
Inadequate Cleaning Effect | Focus, lens quality, or laser tube issues | Adjust focus, clean or replace lens, check tube |
Laser Light Failure | Optical path or component issues | Clean or replace components, adjust the path |
Shallow Cutting | Speed, depth, or lens issues | Adjust speed, increase depth, clean or replace |
Intermittent Laser Output | Lens, water circulation, or protection issues | Clean or replace components, check the circulation |
Incorrect Graphic Size | Software settings or resolution issues | Adjust settings, recalculate resolution |
Unusual Machine Reset | Mechanical or software issues | Check and replace faulty parts |
Mid-Cut Failure | Grounding, graphic errors, or component issues | Keep proper grounding, correct graphics, check components |
Pros and Cons of Sheet Metal Laser-Cutting
Although laser cutting has its advantages. But every rose has its throne. So, laser-cutting also offers some disadvantages. So, the following table briefly shows the pros and possible cons of the laser-cutting process.
Advantages | Disadvantages |
1. High precision and accuracy | 1. Higher initial equipment cost |
2. Versatility in cutting materials | 2. Limited thickness capacity |
3. Minimal material wastage | 3. Potential for thermal distortion |
4. Complex designs with ease | 4. Requires skilled operator |
5. High sheet metal laser cutting speed | 5. Environmental concerns (fumes, gases) |
6. Minimal post-processing required | 6. Maintenance requirements |
7. Reduced tooling costs | 7. Reflective material issues (CO2) |
5 Factors to Consider for Choosing Laser-Cutting Machines
Every laser machine has its purpose and limitations as well. So, you must choose a suitable laser-cutting machine that is precise and aligned to your demands. So, you can follow these factors while choosing the right laser-cutting machine.
Material Compatibility
Every material has its properties and thickness. So, make sure that the laser cutting machine is suitable for the sheet metal materials. Different machines have varying capabilities concerning material. So, it is necessary to choose one that can handle your desired materials efficiently.
Cutting Speed and Accuracy
You must take an estimation of the cutting speed and accuracy of the machine. These two factors can directly affect productivity and part quality. So, choose the machines that have relatively high-speed cutting capabilities. Besides this, it must have a precise positioning accuracy. So, it will ultimately improve the production efficiency. Additionally, it will help achieve tight tolerances.
Laser Source
The laser source is also important to consider while choosing the right laser-cutting machine. These sources may include CO2, fiber, or solid-state lasers. So, each source has its pros and cons. They may vary in their speeds, energy efficiency, or material compatibilities. So, always choose a laser source that aligns more with your needs and budget limits as well.
Power and Wattage
Power and wattage, both estimate the cutting capabilities. In particular, they deal with thicker materials. If you have a high-power and high-wattage machine. It will cut the thicker material quickly. Besides this, such machines are more efficient. So, they will give you more precise cuttings. But, they are more costly. So, before choosing, must check if they align with budget limits or not.
Automation and Integration
The advanced laser machines come with automation features. These features may include, robotic loading and unloading, automatic material handling, and integrated software systems. So, when you choose a sheet metal laser cutting machine, must check for these features. Additionally, these features will eventually help provide a smooth production process. Besides this, it will also reduce the labor costs and improve efficiency.
What are the Alternatives for Laser-Cutting Process?
The sheet metal fabrication industry is now revolutionized. It is now integrated with multiple machinery and equipment. So, every project has a margin to select the most suitable process and machinery to carry out the cutting operations. So, here is a detailed list of all the alternatives available for the laser-cutting process. So, let’s discuss each property in the following table.
Cutting Method | Laser Cutting | Waterjet Cutting | Plasma Cutting | Mechanical Cutting | Abrasive Cutting | Chemical Etching | Wire EDM |
Cutting Principle | Uses a focused laser beam | Uses high-pressure waterjet | Uses ionized gas (plasma) | Uses mechanical force | Uses abrasive discs/wheels | Uses chemical etchants | Uses electrical discharges |
Material Versatility | Versatile; cuts various metals, plastics, etc. | Versatile; cuts most materials | Primarily used for metals | Limited to certain materials | Primarily used for metals | Limited to certain metals | Primarily used for metals |
Cutting Speed | High | Moderate | High | Moderate to High | High | Low | Moderate to High |
Accuracy | High | High | Moderate to High | Moderate | Moderate to High | High | High |
Edge Quality | Smooth | Smooth | Moderate | Variable | Variable | Smooth | Smooth |
Heat Affected Zone | Minimal | None | Significant | None | Moderate | None | None |
Thickness Range | Thin to Medium | Thin to Thick | Medium to Thick | Thin to Medium | Thick | Thin to Medium | Thin to Medium |
Automation | Yes | Yes | Yes | No | No | No | Yes |
Initial Cost | Moderate to High | Moderate to High | Moderate to High | Low to Moderate | Low to Moderate | Low to Moderate | High |
Maintenance | Moderate | Moderate | Moderate | Low to Moderate | Moderate to High | Low to Moderate | Moderate |
Factors that Guarantee the Quality of Laser Cutting of Sheet Metal Parts
Multiple factors may contribute to the quality of laser cutting metal sheet. So, let’s discuss these factors below.
- Laser Power: Make sure the laser power must be sufficient. So, it can penetrate the sheet metal material effectively. Here the power level is adjusted depending on the thickness and type of material.
- Material Type and Thickness: Each material has unique properties. These varying properties may include conductivity and reflectivity. These two factors affect the cutting process. So, the thickness of the sheet metal also affects the required power and cutting speed.
- Cutting Speed: It helps determine how quickly the laser beam moves along the material surface. So it is important to have a balance between speed and power. It will help us get the clean cuts without excessive heat buildup. Besides this, if we test the two cutting speeds. It will lead to the optimal setting for each material. Additionally, if the speed is slow, it can risk heat distortion. It also gives incomplete and rough edges
- Focus Position: You must provide a precise focus of the laser beam. It will ultimately help you out in getting clean cuts. A proper focus position also guarantees maximum energy concentration at the cutting point.
- Gas Selection and Pressure: You may use gases, i.e. oxygen, nitrogen, or compressed air. They will be good to blow away molten material from the cut. Moreover, this pressure of the gas gives you the quality of the cut. Besides this, it avoids edge roughness and dross formation.
- Nozzle Diameter: The size of the cutting nozzle may affect the width of the kerf (cut width) and the precision of the cut. So, you can simply select the appropriate nozzle diameter for the specific application is essential.
- Machine Calibration and Maintenance: Always provide maintenance and regular calibration of the sheet metal laser cutting machine. It will guarantee optimal performance and consistent cut quality over time.
- Cutting Path Optimization: It is generally referred to as the sequence and direction in which the laser cuts the parts. It can affect the overall quality. This may include reducing heat-affected zones and avoiding the risk of distortion.
- CAD/CAM Software: You can opt for high-quality CAD/CAM software. It will help in designing precise cutting paths. Moreover, it will optimize the cutting parameters for specific materials and geometries.
7 Effective ways to reduce material waste in sheet metal Laser-Cutting
Here are the effective ways that can help you reduce material waste while dealing with laser-cutting techniques
- Optimize Nesting and Layouts: You can use nesting software. It will arrange parts closely together within the cutting area. So, consequently, it will reduce the unused space. Besides this, it will increase the material usage.
- Standardize Designs and Components: Make sure your design must be of standardized dimensions. It will reduce the number of different shapes needing to be cut. Besides this, it should be aligned with common sheet sizes. So, it can minimize offcut waste.
- Material Efficiency and Selection: Make sure you use an appropriate material thickness and type for the application. So, they can help you reduce excess material usage. For this, you can use sheet sizes that closely match the required dimensions of the parts.
- Optimize Cutting Parameters: Multiple parameters, i.e. cutting speed, laser power, and focus position must be optimized/ So, they can help in optimal cutting and reducing the material waste. You must regularly monitor their performance based on different material type, thickness, and part geometry.
- Recycle and Reuse Offcuts: You can also reduce material waste using recycling. Simply collect and segregate the offcuts. Then you can recuse them where possible. For example in progressive die stamping, they can be melted down and reused again.
- Lean Manufacturing Practices: You can use lean manufacturing principles. It will help you streamline production processes. Additionally, it will reduce waste at every stage of laser cutting.
- Continuous Improvement and Analysis: Check the cutting layouts, material usage, and waste generation. It will help you give a deep analysis to identify the areas of improvement.
Why choose Masion for Sheet Metal Laser-Cutting?
The Masion is equipped with advanced technologies and equipment. So, we always make sure, we carry out each project with precision and good quality. Similarly for sheet metal; laser cutting. We are using multiple units and providing high-quality laser-cutting services. Our services can deal with both simple and complex parts. Additionally, we are not limited to manufacturing. We also provide design facilities for your metal parts. So, if you need to design a part or just need manufacturing or cutting of the metal parts. Connect with us. We will provide you with high-quality services in very little time.
Get Your Quote Now
Conclusion
In conclusion, sheet metal laser cutting is now a popular and most advanced technique to cut sheet metals. It uses a light beam of a certain width and wavelength. So, this light helps to cut the different materials. So, if you deal with laser cutting you must consider the material thickness. Besides this, laser cutting has diverse applications in different industries. So, if you are looking for precise and accurate laser-cutting services. Masion is here to serve you well. We are using advanced technologies to carry out the cutting operations very well. get your quote now.
Frequently Asked Questions
Q1. What Laser Cutting Machines are Suitable for Sheet Metal?
Choosing the best one depends on the cutting speed, accuracy, material compatibility, and budget. But if we talk about the market, the top machines are Trumpf TruLaser, Bystronic ByStar, Amada ENSIS, and Mazak Optiplex series. These all are famous for their quality, performance, and reliability.
Q2. How To Reduce Sheet Metal Wastage During Laser Cutting
It can be reduced using nesting. The optimized nesting eventually increases the material usage. Besides this you can select the appropriate cutting parameters, They will allow the effective use of material.
Q. Where we can find the Sheet Metal Laser Cutting applications?
Sheet metal laser-cutting is now used in several industries. They may include automotive, aerospace, electronics, signage, architectural, and manufacturing.
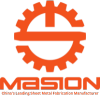
Send Your Inquiry Today



+86-18969433502

sales@sheetmetalmasion.com