Sheet Metal Forming – The Guide You Need
Sheet metal forming is now becoming popular in the preparation of metal components. Like sheet metal fabrication, it works on sheet metals and converts them into specific geometry and shapes. This process has wide applications in different sectors of life. So, let’s discuss forming metal sheet. Moreover, we will get a deep insight into its fundamental process, design considerations, material requirements, and applications in diverse fields.
Table of Contents
ToggleWhat is Sheet Metal Forming?
Forming metal sheet is an old but significant method of manufacturing metal parts. It takes the flat sheets as a feed and then molds them into the desired shape. This method has a wide scope of applications in different metal industries. These may include, electronics, construction, aerospace, and automotive industries. Moreover, sheet metal forming is comprised of several techniques. So, each technique has its abilities and limitations. So, it allows the customers to select the most suitable approach, based on their requirements.
What Materials Can be Used for Forming Sheet Metal
So, the following materials have different properties and have a wide scope of applications in the market.
Material | Characteristics | Common Applications |
Steel | – Good strength-to-weight ratio – Ductile and formable – Various grades available (e.g., mild steel, stainless) | – Automotive body panels – Structural components – Appliances (e.g., washing machines) |
Aluminum sheet metal forming | – Lightweight – High strength-to-weight ratio – Excellent corrosion resistance | – Aircraft components – Beverage cans – Heat sinks |
Stainless Steet | – Corrosion resistant – High strength – Hygienic properties | – Kitchen appliances (e.g., sinks, cookware) – Medical equipment (e.g., surgical instruments) |
Copper | – Excellent electrical and thermal conductivity – Corrosion resistant – Malleable | – Electrical wiring – Roofing and flashing – Heat exchangers |
Brass | – Attractive appearance – Corrosion resistant – Good machinability | – Musical instruments (e.g., trumpets, trombones) – Plumbing fixtures (e.g., faucets) – Decorative Hardware |
Galvanized Steel | – Corrosion resistant due to zinc coating – Good strength | – Outdoor structures (e.g., fences, guardrails) – Roofing and siding material – Automotive parts |
Galvanized Steel B | – Similar to galvanized steel, with specific strengths | – Automotive manufacturing – Construction projects with specific requirements |
Carbon Steel Sheet | – Strong and durable – Versatile and easily machinable | – Construction (e.g., beams, pipes) – Automotive frames and structural components – Machinery parts |
Titanium Sheet | – High strength-to-weight ratio | – Aerospace components (e.g., aircraft frames, engine parts) |
Processes and Design Tips for Forming Metal Sheet
Let’s discuss each step of sheet metal forming processes in sequence;
Material Selection
Although sheet metal form helps in converting different materials into desired shapes. However, before starting work, it is necessary to select the material type. So, this choice of material may vary due to several factors. These factors may include applications of metal parts and mechanical properties, i.e. strength, ductility, and hardness. Moreover, environmental conditions and cost also affect the selection of materials. So, the commonly used materials are aluminum sheet metal forming, copper, brass, and stainless steel.
Blanking
Here, a large sheet of metal cuts down into the initial shape of the part. You can use several methods for cutting. These methods may include shearing, punching, or laser cutting.
Curling
Curling is used for forming. So, it rolls and curves the sheet metal edges. It is often used to make cylindrical or round-shaped parts. These shapes may include, cans, pipes, tubes, and drums. This process uses different machines and sheet metal forming tools. So, its sheet metal forming machine type depends on the geometry of your metal part. Here are some design tips for the curling process.
- The material must be thick from the edges. So, it can avoid cracking and tearing during manufacturing.
- Make sure to use gradual curves and optimal radii. These will prevent metal from sharp bends. These bends can deform the material and tooling wear.
- Apply lubricants and proper coating on the material. It will reduce friction and ultimately increase the curling quality.
Laser Cutting
This is quite a precise process to cut the metal sheets. It uses a high-powered laser beam and gives highly accurate cutting. Moreover, it is highly suitable for cutting complex designs and shapes. Laser cutting is suitable for many materials. These may include, steel, aluminum sheet metal forming, stainless steel, and titanium. This process has wide-scope applications in prototyping and small-scale production.
Here are some design tips for this process;
- Your CAD designs must be clear and accurate. They must show appropriate dimensions and tolerances.
- Try to reduce the number of precise points. It will help you prevent tools for forming sheet metal from wearing and speed up the process.
- Don’t use complex internal features and sharp corners. They may lead to incomplete cuts.
Bending
Here the metal deforms along with a straight axis. So, it is used to create angles, curves, and other shapes. Moreover, it uses press brakes. We clamp the sheet between a punch and a die at a desired angle. Then the punch applies a force on it. So, it is important to choose a suitable material. Additionally, use proper forming tool sheet metal. So, you can avoid defects, i.e. cracking or wrinkling.
Here are certain design tips for bending;
- Always make sure the appropriate bend radii. It prevents material cracking and tearing. You can adjust radii equal to or greater than material thickness.
- Your designs must have symmetry. So, it can equally distribute force and reduce distortion.
Avoid bending on the hypotenuse
1.It can be of different shapes, So make sure to design them with accurate dimensions.
Give Specific Arcs
U-Shape Bending
2.You can use pre-bending or relief cut operations. They will give tight radii and complex shapes to bending.
Ironing
It is used to reduce the wall-thickness of cylindrical cup-shaped parts. It helps in maintaining the height of the part during manufacturing. Ironing is commonly used to increase the length of a part with a specific thickness. It has wide applications in the manufacturing of cans, containers, and other cylindrical tubular components.
Here are certain design tips to get precise results during this process.
- Your designs must have a uniform thickness distribution. So, it can give proper material flow throughout the process.
- Make sure to set the appropriate reduction ratio and wall thickness. So, you can get the required length of the part.
- You can use lubricant and optimal coating to avoid friction and wear and tear.
Hydroforming
It uses high-pressure fluid and gives tube-like shapes to the metal sheet. It has several benefits. These may include uniform material flow and reduced spring-back. Moreover. It can form large complex parts. This is the reason, it has a wide scope of applications in multiple industries, i.e. automotive, aerospace, and appliance industries.
Here are certain design tips to maximize the efficiency of this process.
- Make sure your design parts with gradual transitions. They will help reduce the material thinning. Moreover, it can eliminate the risks like wrinkling or tears.
- You must specify the right amount of pressure and forming sequence. It will give the desired shape and thickness distribution.
- You can opt the internal or external support to control the material flow. This will help you avoid distortion.
Deep Drawing
It is a technique used to stretch the metal sheet over a die. It helps form a complex and deeper metal part. For this, your material must be highly ductile. It must have elongation properties as well. So, it can prevent wrinkling and tearing. Deep drawings are widely used in the manufacturing of sinks, cookware, and automobile parts.
So, here are some design tips to increase the efficiency of the shearing process.
- Your designs must have uniform thickness. It will give a consistent material flow and reduce the tearing risks.
- Make sure to give appropriate draft angles and fillets. They will avoid sticking the part in the die.
Shearing
It uses different machines to separate the metal sheet along a straight line. The machines may include simple bench-mounted tools and large hydraulic or mechanical presses. So, you can select the sheet metal forming machine based on the material type and geometry of the metal part. This process usually uses sheer force to do this. It helps cut the large metal sheets into small blanks. Moreover, it also effectively trims the edges of parts.
Here are certain design tips to increase the efficiency of the shearing process;
- Must use an optimized layout for parts on the sheet. It will reduce the scarp and effectively use the material.
- The edges must be straight with simple geometry. So, it can avoid tooling wear.
- Mark the proper edge quality and tolerance requirements.
Punching
It helps make different features, i.e. holes, notches, and other shapes on metal sheets. So, it has a wide scope of applications in perforation and blanking. It is commonly used to make geometric shapes of metal sheets. Several kinds of machines can be used here. They may include mechanical presses or cnc sheet metal forming.
Here are some design tips to optimize this process.
- Design and mark holes, shapes, and locations accurately. So, you can get proper fitment and alignment of punched features.
- Make sure to rescue the distance between holes. It will reduce the tooling cost.
- You can consider pilot holes or starter punches. They guide the cutting tool and increase the quality of the thick material.
Embossing
During this process, the punch exerts force from one side. It allows the material to flow in an opposite direction. This allows us to make patterns on the sheet metals. Here are some design tips for it.
Precision Sheet Metal Forming – Suitable Ranges of Thickness of Metal
Here are some suitable ranges you can opt to design the different components of forming sheet metal;
Sheet Metal Forming Process | Suitable Thickness Range (inches) | Suitable Thickness Range (millimeters) |
Blanking | 0.005 – 0.25 | 0.13 – 6.35 |
Curling | 0.010 – 0.125 | 0.25 – 3.18 |
Laser Cutting | 0.005 – 0.75 | 0.13 – 19.05 |
Bending | 0.010 – 0.25 | 0.25 – 6.35 |
Ironing | 0.010 – 0.25 | 0.25 – 6.35 |
Hydroforming | 0.010 – 0.25 | 0.25 – 6.35 |
Deep Drawing | 0.010 – 0.25 | 0.25 – 6.35 |
Shearing. | 0.005 – 0.75 | 0.13 – 19.05 |
Punching | 0.005 – 0.75 | 0.13 – 19.05 |
What are the Applications of Sheet Metal Forming?
It has various applications in different industries, So, let’s discuss them all here.
- Automotive Industry: It helps manufacture Body panels, chassis components, and exhaust systems.
- Aerospace Industry: iT helps make Fuselage, wings, and engine components.
- Construction and Architecture: It has wide applications in making Roofing, cladding, and structural elements.
- Appliances and Consumer Goods: It also serves for the manufacturing of Kitchen appliances, household items, and electronics enclosures.
- Manufacturing Equipment: Metal forming is also used for Machinery components, tooling, and fixture manufacturing.
- Medical Industry: It has wide applications in Medical equipment and healthcare facilities.
- Energy Sector: It helps make power generation and renewable energy components.
Types of Forming Metal Sheet
Here are certain types that have different applications for different industries;
Straightening: It is used to remove the deformations in metal parts. Moreover, it gives a flat shape to sheet metal. It usually gets through roller leveling. So, the sheet is allowed to pass through rollers or hydraulic press and get flattened.
- Edge Flanging: Here, the edge of sheet metal parts is bent into flanges. So, you can use several techniques to achieve them. These may include bending, roll forming, or stamping.
- Flaring: It may include expanding or widening the end of a cylindrical or tubular component. So, this can be achieved through processes like tube flaring. Here the end of the tube is expanded to create a larger opening.
- Edge Rolling: Edge rolling in sheet metal forming involves rolling the edge of a sheet metal component to create a rounded or beveled edge. So, this can be achieved through edge-rolling sheet metal forming machine. These machines apply pressure to the edge of the sheet to create the desired profile.
- Hemming: It folds the edges back onto itself. Moreover, it makes smooth and round edges. So, this method is now widely used to get reinforcement and safety. So, we can perform it using bending or folding operations.
- Seam Locking (Seaming): It helps join two sheet metal pieces together. It folds and then interlocks its edges. As a result, a strong joint will be formed. The technique used for this operation may include clinching. Here the metal deforms and makes a mechanical interlock between two sheets. It is usually carried out using welding operations.
- Curving: This process is generally used in bending sheet metals. It is usually used in press baking, roll forming, and incremental forming in its operation. These help get the curvatures and properties of the material.
Methods Used to Correct Deformations in Different Materials
When we apply the sheet metal forming process for manufacturing. We often face deformations in our metal parts. It results in compromising the quality and functionality of the metal parts. Here are some techniques to address the deformation in different materials.
Methods for Correcting Deformations in Steel Plate Parts
Deformation Type | Correction Method | Simplified Drawings |
Irregular Deformation | Hammering Method | ![]() |
Local Heating Method | ![]() | |
Wavy Deformations | Flame Correction | ![]() |
Tight Areas | Roller Method | ![]() |
Techniques for Correcting Deformations in Angle Steel
Deformation Type | Correction Method | Simplified Drawings |
Distortion | Twisting Method | ![]() |
Non-Perpendicularity | Hammering Method | ![]() |
Bending | Flame Correction | ![]() |
Correction Methods for Deformations in Welded Parts
Deformation Type | Correction Method | Simplified Drawings |
Angle Correction | Using a Thick Chisel | ![]() |
Rectangular Frame Correction | Hammering Method | ![]() |
Adjusting Size Discrepancies | ![]() | |
Correcting Angle Errors | ![]() |
What are Common Techniques Used in Bending?
Here is the description of some bending techniques, that are widely used in the industries. So, let’s discuss them in detail;
- Bending Methods for Angular Workpieces
Here are some bending techniques for angular shape workpieces.
1. Free Bending
First, draw a bending line on the finished sheet. Now align the bending line with the corner line of the mold. After that, press the sheet with your left hand. Then tap the two ends of the sheet with a wooden hammer with your right hand. Now allow it to bend at a certain angle for easy positioning and shape. Moreover, use a wooden hammer and gently tap along a curved surface of the plate. So, it will stick it to the cattle tool.
2. Clamp Bending
Here first, draw bending lines on the sheet blank. Now align the bending line with the corner of the mold and clamp it on the vise. After that, use a wooden mallet. It will help by gently tapping the base of the curved corner. So, if the width of the curved edge is large. Place a wooden block on the curved edge before beating to prevent warping. After that, use a wooden hammer to hit the sheet evenly to make it close to the mold.
3. Shaped Parts Bending
You first need to draw two bending lines on the blank. Now align a bending line with the bending corner of the mold. Then clamp it firmly with a bench vise. Allow tapping the bending root with a wooden hammer to shape it. Now, turn the bent piece around. Again align the other bending line with the bending corner of the mold, and clamp it. Then tap the bend with a wooden hammer to shape it. If the curved surface warps. you can put them-shaped pieces on the iron gauge.
Bending of Shaped Workpieces
It generally uses a Shaped Workpiece Bending technique. So, you should draw four bending lines on the sheet blank. Now align the bending line with the bending angle of the mold and clamp it. Then hit the bend with a hammer to bend it. After that, use a vise and mold to form the corner at the bending line. Now allow the mold to bend the angle corresponding to the bending line. So, it can get a final shape. During operation, the sheet blank should be clamped firmly with the mold.
Bending of Cylindrical Workpieces
Here you need to draw several bending lines on the blank. These lines work as a reference line for hammering when rounding. So, use molds or round steel to bend both ends of the sheet blank. It may require the bending radius to be slightly less than or equal to the required bending radius. So, place the sheet blank with both ends bent on the channel steel or the rail. Now use a hammer to hammer evenly along the bending line. You must place the cylinder on the rail or gauge iron for rounding.
Bending of Conical Surface
Firstly, you must divide the arcs at both ends of the sheet into equal parts. Now draw the bending line. After that, fix the two round sheets of steel on the platform parallel or slightly tapered. Now place the marked sheet blank on the round steel. Here use the hammer to hammer evenly along the bending line of the sheet. When hammering, hammer the two ends of the sheet first, and then hammer the middle.
Comparison of Forming Sheet Metal with Other Alternatives in the Market
As there are multiple alternatives available for sheet metal forming. So, let’s discuss them briefly here.
Aspect | Forming Sheet Metal | Injection Molding | 3D Printing | CNC Machining |
Material Variety | Wide range of materials including metals like steel, aluminum, and copper, as well as alloys and composites. | Limited to plastics (thermoplastic or thermosetting) or metal powders. | Limited to specific types of plastics, metals, ceramics, and composites. | Works with metals, plastics, and composites. |
Strength and Durability | Offers high strength and durability, suitable for structural applications. | Strength depends on the material but may be lower than metal parts. | Varies based on material and method, and may be less durable than traditional manufacturing. | It can achieve high strength, especially with metals. |
Complexity of Shapes | Capable of producing complex shapes with high precision. | Limited in complexity, especially with deep recesses or undercuts. | Can produce highly complex shapes, including internal features. | Capable of complex shapes, but may have limitations on internal features. |
Production Speed | Fast production rates, especially for high-volume production. | Production speed can be high for large runs but lengthy setup times. | Production speed varies and is generally slower than traditional methods. | Speed depends on part complexity, but can be relatively fast for simple geometries. |
Tooling Costs | Initial tooling costs can be high but cost-effective for large runs. | Tooling costs can be significant, especially for complex molds. | Tooling costs may be lower than traditional methods, but equipment costs can be high. | Tooling costs can be significant, especially for complex parts. |
Surface Finish | Can achieve a variety of finishes including smooth, textured, or patterned. | Surface finish may be affected by mold texture and ejection method. | Surface finish may be affected by layering but can be post-processed. | Highly customizable surface finishes including smooth or textured options. |
Every process has its features. So, it depends on what suits you more to meet the requirements.
Precision Sheet Metal Forming – Benefits
Sheet metal forming has many applications. So, let’s discuss how beneficial it is to use in the manufacturing of different metal parts.
- Versatile: It shows versatility. So, it has wide applications in the manufacturing of different metal parts. It can deal with both simple and complex designs. Moreover, it helps with bending, stretching, and molding the metal sheets using different processes.
- High Strength-to-Weight Ratio: Its metal parts have a high strength-to-weight ratio. So, it has many applications where strength and durability are important. These applications may include, the automotive, aerospace, and construction industries.
- Cost-Effective Solution: If we talk about mass production. Metal forming is quite less expensive. It can appropriately use the material at fast production rates. So, it offers relatively low tooling costs. Moreover, it allows for recycling the material.
- Excellent Surface Finish: It is a good option for smooth, textured, or patterned surfaces. So, when it comes to the appearance of metal parts. Sheet forming is quite a reliable solution.
- Design Flexibility: It can deal with simple and complex designs. So, engineers have an option to make drawings appropriate without concerning the intricacy of metal parts.
Drawbacks of Sheet forming
So, here are some disadvantages of metal forming
- Sheet forming has some limitations while dealing with thin gauge materials.
- In bulk production and complex designs, it sets initially high tooling costs.
- This process may experience springback. This means the material returns to its real shape after formation. So, it can lead to dimensional inaccuracy.
- Although it can use different metals, i.e. aluminum, brass, and copper. However, it doesn’t work well with composite materials.
- Particularly in the deep drawing process. It may need an accurate and precise design. Otherwise, the part can undergo deformation.
Conclusion
In conclusion, sheet metal forming is working as a foundation for advanced manufacturing. It allows multiple processes to make high-quality components. So, it has multiple applications in different industries. Moreover, it supports the process like blanking, curling, laser cutting, and bending. This makes this process more efficient and allows engineers to shape the flat metal sheet in different shapes. Moreover, it uses materials like steel, aluminum, and copper into complex and strong parts. Although it has some limitations. But still, it is quite a flexible and durable technique for manufacturing.
Frequently Asked Questions
Q1. Can you use galvanized steel in forming metal sheet?
Yes, the galvanized steel is good for metal forming. It has remarkable corrosion resistance due to zinc coating. So, it is quite a durable and long-lasting material in the different industries.
Q2. Is forming sheet metal useful to use?
It is useful because it offers different fabrication options. So, it is used to create durable and complex shapes. Moreover, it is a cost-effective and high strength-to-weight ratio.
Q3. Can you use Tool steel in sheet metal forming?
Yes, we can. It is a suitable option. because of its excellent mechanical properties, i.e. hardness, toughness, and wear resistance. It is also used in different industries as well.
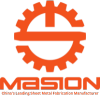
Send Your Inquiry Today



+86-18969433502

sales@sheetmetalmasion.com