Sheet Metal Fabrication and Quality Control at Sheet Metal Masion
At Sheet Metal Masion, we understand the significance of sheet metal fabrication quality control in the production of sheet metal parts. Our company’s goal of achieving consistency in our components does not only eliminate defects but also help to minimize costs while keeping safety and reliability in sheet metal standards high. The following comprehensive guide outlines how we maintain quality control QC principles and practices based on best practices along with industry tips.
Table of Contents
ToggleUnderstanding Quality in Sheet Metal Manufacturing
Product quality in manufacturing can be defined as the extent to which a product conforms to its requirements. As stated in the third section of ISO 9000:2015. the extent to which a set of inherent attributes of an object meets the requirements’. For us at Sheet Metal Masion, it means that every fabricated part meets the design specifications and performs as expected.
In functional sense quality means the quality of materials used right from the raw material stage to the final inspection of the product. It entails a systematic method of handling each phase of the process, to ensure compliance with the set level of quality. The strict adherence to quality measures ensures that sheet metal masion offers not only functional parts, but also durable and reliable ones.
Metal Quality Control Importance
In relation to the sheet metal manufacturing process, quality control seeks to eliminate or reduce defects and guarantee that parts are fabricated to design requirements. By maintaining a good QC system, we are able to ensure that manufacturing time is on schedule and cost efficient while preventing products with safety complications, recall, and additional expenses due to failure.
Benefits of Competitive Sheet Metal Quality at Sheet Metal Masion:
- Consistency: This ensures that there are no variations in the different parts produced because they all have to be up to sheet metal standard. Quality that is maintained also helps in supporting the reputation that we have with our customers. This consistency is maintained through documented procedures, qualified personnel, and accurate equipment, to ensure the quality of products.
- Cost Savings: Thus, waste and rework are minimized, giving us the benefits of time and material savings. Efficient quality control is one of our strengths, as it allows us to identify defects and address them before on, which leads to reduced production costs. Thus, adopting this kind of approach to defect prevention is not only cost-effective but also allows us to sustain a competitive advantage over our rivals in terms of price and product quality.
- Customer Satisfaction: Lower rate of returned products or complains also result to happy consumers hence giving repeated business and referrals to other customers. Being aware of the fact that our reputation is based on the satisfaction of our customers we are committed to the stringent quality control. This helps to establish long term relations with customers based on trust and reliability by serving their needs through delivering products that are of high quality and exceed expectations.
- Compliance: Respecting legal and compliance requirements, we do not violate legal rules and standards, making the final product safe and efficient. Adherence to a standard for instance ISO 9001 does more than make us a compliant organization but also enables a continuous improvement program. It also helps in making sure that our quality management system is relevant within a dynamic and competitive industry.
Establishing Quality Requirements at Masion Sheet Metal Manufacturing Industry
To obtain high quality of sheet metal parts the first step is to specify requirements, describe needed design and focus of attention on the most relevant characteristics.
Here at sheet metal masion we follow these sheet metal quality control list:
Sr. No. | Plate Size | Allow Tolerance |
1 | W/H(width or height)≤1000mm | ±0.5mm |
2 | 1000mm<W/H≤3000mm | ±1.0mm |
3 | W/H>3000mm | ±1.5mm |
4 | Diagonal≤1000mm | ±0.5mm |
5 | 1000mm<Diagonal≤3000mm | ±1.0mm |
6 | Diagonal>3000mm | ±1.5mm |
7 | R dimension | Thickness of the panelδ×1.5(According to design drawings or technical note) |
8 | Plate direction | According to the drawings |
9 | Angle | ±0.50 |
10 | hem dimension | ±0.2mm |
11 | Location of angle protector | ±0.5mm |
12 | Height of angle protector | ±1.0mm |
13 | hole/gap dimension | ±0.2mm |
14 | hole/gap dimension≤200mm | ±0.5mm |
15 | hole/gap dimension>200mm | ±1.0mm |
16 | location of stiffeners | ±2.0mm |
17 | quantity of stiffeners | According to design drawings or technical note |
18 | accessories location≤1000mm | ±0.5mm |
19 | accessories location>1000mm | ±1.0mm |
20 | Plate flatness (After setting Stiffeners) | <1 |
Detailed Design Specifications for Sheet Metal Fabrication Quality Control
We provide our manufacturing team with comprehensive engineering drawings that include all necessary characteristics of the part, such as:
- Straightness
- Flatness
- Circularity
- Concentricity
- Cylindricity
- Perpendicularity
- Parallelism
- Profile
- Runout
Standard dimensions and tolerances addressing each characteristic are placed to encourage accuracy. For instance, if a part requires a hole or pin having a perpendicular relationship with a theoretical axis, such specifics are explicitly described in the drawing. Even in simple shapes and forms, we establish all the critical specifications of the part, functional and ornamental. Such an approach minimizes ambiguity and possible mistakes when making the product to achieve the expected quality.
Prioritizing Requirements
It is also important to note that not all characteristics are of equal importance. It is we who decide which characteristics are most crucial to the functioning and shape of the part at hand, high quality and affordable. Since tighter tolerances are more difficult and costly to accomplish, they are used selectively to prevent the generation of over-engineered components. It is when the main characteristics are considered that we direct our efforts toward reaching the maximum level of accuracy at the points where it is crucial. This strategic approach enables us satisfy the market demands for well-made and affordable auto parts.
Selecting Raw Materials and Suppliers
The selection of raw materials is of paramount importance. Our requirements for the materials for our parts are defined and we set a list of approved suppliers to avoid using substandard material.
Raw Material Characteristics
- Straightness for Proper Machine Feeding: To make certain that raw materials have the necessary straightness to feed the machines properly and with high accuracy. Straight materials mitigate the incidences of jamming and other interruptions in the production line, thus leading to efficient and quality production.
- Specific Chemistry for Non-Reactivity in the Final Assembly: Defining and sourcing raw materials that will not cause a chemical interaction while assembling them to prevent compromising the product’s quality and safety. Such attention to the kind of materials to be used helps in ascertaining that the final products are effective in their use without the occurrence of chemical reactions that may pose risks to the users or the efficiency of the product as intended.
Supplier Evaluation
We carry out supplier evaluation and develop an authorized suppliers’ list to guarantee that suppliers deliver materials of the right size, grade, and quantity. Incoming raw materials are physically checked to ensure they have met the required specifications. In evaluating the supplier, areas such as quality of goods and services provided, ability of the supplier to deliver on time and their capacity to embrace change are considered. This way we can guarantee the supply of raw materials from reputable suppliers always in the right quality.
Documenting Quality Control Processes
Writing out our QC procedures and goals also helps maintain future consistency and gives an explicit plan for attaining quality.
Equipment and Tools:
Outlining the capacity, tolerance capabilities, and features of the equipment, identifying the precise tools and machines necessary to execute each step. By writing down the equipment and tools, there is a proper understanding of all the features related to manufacturing accuracy.
Staff Skills:
Explaining what qualifications staff have received, and what training they must undergo during their employment. Thus we are able to define the skills and the training required so that the team is able to maintain quality standards. Ongoing training activities enable our staff to learn modern industry practices and advancements thus improving our ability to produce quality products.
Work Instructions:
Giving detailed guides on how to use the equipment to avoid making mistakes and hence right usage of the machineries. Standard operating procedures also minimize variations in the production process and guarantee that all employees can manage the equipment as intended.
Process Controls:
Explaining how to check and adjust the process by implementing methods and tools to maintain process variables at specific levels. These are effective controls for the process and allow us to quickly identify any loss of control and bring the process back to normal, so that products are manufactured to quality.
Quality Measures:
Identifying the performance indicators and quality benchmarks, employing quantifiable parameters as to determine whether and to what extent standards are being complied with. This helps to objectively assess the quality of products and processes, which will lead to the constant improvement of quality standards.
Inspection Points:
Determining where and how the inspections will be conducted in order to identify and prevent flaws from going unaddressed. The regular points of inspection on the production line enable the organization to inspect and rectify any problems before they reach the final product, thus maintaining quality and minimizing defects.
Inspection Process
Initial Inspection: Ensuring quality of raw materials before engaging in the process of production. This initial inspection minimizes the possibility of substandard material getting into the manufacturing process, which may lead to substandard products.
In-Process Inspections: Supervising the parts in the process of manufacturing to prevent the identification of defects. Implementation of in-process checks enables us to detect defects during the production process to prevent them from contaminating the whole production run.
Final Inspection: Carrying out a final inspection before packing and dispatching. The final inspection of the parts is very important to ensure that they are ready for delivery and will function as required in the particular application. The final inspection allows us to guarantee that our customers will get products that meet all of the necessary design requirements and industry quality standards.
Achieving Accurate Measurements
Precision is crucial when it comes to the quality aspect of production. Calibrated and standardized tools are used to minimize variation in measurements.
Calibration and Standardization
All measuring devices are also standardized with state or national standards like NIST and are checked and rechecked periodically for accuracy. As per the calibration standards, our measurements are accurate and reliable to support our company’s quality policy.
Tolerances
We know the allowable deviation for our measuring instruments so that devices measure within a certain range of truth. Thus, it is possible to achieve precise control over the tight tolerances needed for parts to function effectively in their respective applications.
Conducting Gage R&R Studies
Gage R&R studies focus on assessing variability attributable to the measurement instrument and the operator so that variation sources can be diagnosed.
Performing a Gage R&R Study
- Select Parts: Selecting a sample of parts that should be typical of the population and exhibit the variation expected in the field. These selections keep the study indicative of normal conditions and the worst case scenario in our manufacturing line.
- Assign Operators: To ensure validity, having several operators measure the selected parts independently to compare results. It also assists in determining whether different operators are accurate in their usage of the same gage, thus pointing out variation that may affect the measurements.
- Analyze Data: Checking measurement results for difference or change, identifying the cause of variation. From these comparisons, it is possible to determine whether what is causing the differences is the gage, the operators or both so that appropriate action can be taken.
- Take Corrective Actions: Modifying the measurement process in accordance with analysis, executing modifications to reduce variation. This might require adjusting the gage, or reorienting the operators to guarantee that they produce accurate measurements.
Ensuring Quality Through Inspections
Periodic monitoring of the parts throughout the manufacturing process guarantees their quality.
- Receiving Inspection: Conducting checks on raw materials against specifications as soon as they are received. This step assists us in confirming that all the materials are of high quality before adopting for usage in the production process to avoid manufacturing of substandard products.
- In-Process Inspection: Observing the parts at different levels of manufacturing in order to identify flaws at the earliest point possible. Regular on-site monitoring allows to handle production related problems immediately, before they spread and affect the quality of the final product.
- Final Inspection: Performing a thorough inspection of all finished parts before dispatching them to the client. This final check ensures our customers get products that meet design requirements and quality standards, which shows our dedication to quality and reliability.
Handling Nonconforming Parts
- Segregation: Ejecting defective products from the production line so that they do not intermingle with quality products. This segregation assists in minimizing the likelihood of such substandard parts being used or distributed, thus preserving the quality and reputation of our products.
- Traceability: Proper documentation of nonconforming parts to enable identification of the root cause of the issue. Thus, we are aware of nonconforming parts and can address the causes of defects and take appropriate measures to avoid repeating mistakes and improve the manufacturing process.
- Corrective Actions: Continuous monitoring and evaluating the effectiveness of corrective actions that are taken to correct deficiencies that result to defects. In practice, we proactively perform correction actions thus preventing defects and ensuring compliance to the highest quality standards.
Final Packaging and Delivery
It is important to note that quality control does not end with manufacturing. Packaging plays an important role so that no part is damaged in transit and everything is in perfect condition.
Packaging Guidelines
- Protection: Ensuring that the parts are protected from physical damage during transportation by wrapping or boxing them in high quality material. These are such as identifying proper packaging materials and methods to protect our products from shock, moisture, or any other harm in transit.
- Labeling: It is also important to properly package and label each container or box to avoid confusion and ensure proper management. Proper and concise labelling helps us ensure that our products are handled properly while in transit and delivered to the right place.
- Documentation: Submitting all relevant documents with the consignment, for instance, inspection reports and quality certifications. Extensive documentation aids the customer in ensuring that the products meet their requirements for quality and specifications, thus underlining the reliability of the work.
Continuous Improvement
Quality management is therefore a continuous process. In maintaining adequate quality control, we continually assess our strategies and enhance the procedures where necessary to meet new tasks.
Key Practices for Continuous Improvement
There are several key practices to follow to ensure that the process improves based on the identified best practices:
- Regular Audits: Organizing internal and external audits to determine shortcomings in the system. A review is an independent, external assessment of the quality management system to reveal weaknesses and recommendations for improvement of our system.
- Feedback Loop: Solution and improvement including feedback from customers and employees. Listening to the communication from our various stakeholders enables us to pinpoint any gaps that needs attention in our efforts towards the quality controls.
- Training: Ongoing training of the staff regarding the methods and techniques that are current on quality management. This is critical in ensuring that we remain up to date with the latest trends and practices in the market and offer our clients the best solutions.
- Technology: Doubling on fixed assets and technologies to enhance quality and productivity. Here it is important to focus on the modern approaches in manufacturing and by doing so, make it possible to optimize processes, improve product quality, and therefore gain a competitive advantage.
Conclusion
In sheet metal fabrication quality control at Sheet Metal Masion, we aim at providing components which are dependable and free from defects. This structured approach to the QC responsibilities such as defining requirements, functional, and final inspections ensures standards fulfillment, lowering of costs and customers satisfaction. You will work with certified sheet metal industry expert as per ISO standards and quality control to help build the success of your business. In this regard, we constantly enhance our efficiency to sustain a high quality and build credibility as a reliable manufacturer. We were able to eliminate some of our raw material suppliers as being below par for our company while giving customers satisfaction that has contributed to our growth in the sheet metal industry.
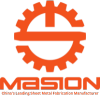