Powder Coating Metal Protection: An Overview of the Procedure
Table of Contents
ToggleOverview of Powder Coating
The dry finishing technique is known as powder coating. It is applied to items to provide a superior, long-lasting finish that improves their appearance and lengthens their lifespan.
This process guarantees a remarkably durable coating that is highly resistant to fading, chipping, and scratching.
Powder Coating’s Advantages Over Liquid Paints
Powder coating is superior to liquid paint in numerous vital ways. Environmental benefits are among the main advantages. Volatile organic compounds (VOCs) are released into the environment in trace amounts by powder coatings containing no solvents.
Liquid paint including flammable organic compounds such as (VOCs) that may harm the environment. Powder coating is a more ecologically reliable choice and powder coating overspray may be collected and recycled to decrease waste.
Powder-coated surfaces outlast liquid paints in terms of resistance to chipping, scratches, fading, and wear. They are excellent for things subjected to inclement weather and it is helpful in eliminating the sagging.
Liquid paints deliver a stronger and more consistent surface. The application procedure is more effective. We require one coat to provide the required finish. It lowers labor costs and speeds up production.
The Method of Powder Coating
The three primary operations are preparation, application, and curing.
Preparation:
This step entails washing the metal substrate to remove contaminants such as oils and grime. Several ways to perform this function are available, including chemical cleaning, sandblasting, and abrasive blasting. Pretreatment is necessary to ensure that the coating sticks to the substrate correctly.
Application:
We can apply the powder using an electrostatic spray cannon. The powder particles receive a positive electric charge, and they are drawn to the grounded metal item, guaranteeing a precise coating.
Curing:
The coated portion is put in a curing oven, and the powder melts and flows in response to the heat, forming a smooth film. The molecular chains are cross-linked during the curing process, which produces a strong and long-lasting finish. Depending on the powder used, curing periods and temperatures might change, but they normally last 10 to 20 minutes.
Powder Coating Types Usd for Metal Protection
Thermoset Powder Coatings:
Chemical coatings are highly long-lasting and resistant to heat. They are based on resins that chemically cross-link while curing. Polyester and epoxy are examples of standard thermoset resins. Polyester coatings provide exceptional UV and weather safety. They make them perfect for outdoor applications.
Thermoplastic Powder Coatings:
In contrast to thermosets, thermoplastic powders do not change chemically as they heal. They dissolve and flow to create the coating, and they may be remelted and reused. These coatings’ powerful resistance to impact and capacity to create thick coats make them widely utilised. PVC, nylon, and polyethene are specimens of common thermoplastics.
Hybrid Powder Coatings:
These coatings incorporate several resins to attain precise performance attributes. Epoxy-polyester hybrids combine the weather solidity of polyester with the sticking and corrosion opposition of epoxy.
Quality-Related Issues
High-quality powder coating is dependent on several aspects:
Surface Preparation:
The substrate must be cleaned and treated correctly to ensure exceptional adhesion. It avoids flaking or peeling. Some techniques include sandblasting, degreasing, and applying conversion coatings like chromates.
Application Control:
As we know, application parameters such as voltage and gun distance are constant and provide uniform coating thickness.
Curing methodology
Curing time and temperature for this process must be followed. It will be helpful to achieve the whole polymerization. Improper brittleness is an example of a shortcoming and it is due to overcuring.
Environmental Conditions
If we manage the temperature and humidity in the coating area while performing powder coating metal process, we may prevent problems like condensation and powder contamination.
Inspection and Testing:
The last step is the inspection and testing of quality-related issues. They are necessary to ensure the coating meets the necessary requirements while routine inspections and testing, such as thickness measurements and visual inspections, are conducted.
Tests for salt spray corrosion resistance, and UV exposure wearability are possible extras for specific applications.
Utilization of Metal Powder Coating
When it comes to finishing metal parts, metal powder coating is a flexible and effective procedure with several advantages over conventional painting techniques. The following are the main uses and advantages of metal powder coating:
Heavy Equipment
Because powder coating is long-lasting and resistant to deterioration, it is widely employed in heavy equipment, including agricultural and construction machinery.
Automobile and Consumer Appliances
Powder coating is used for automobile parts, such as radiators, truck beds, and ornamental accents. Powder-coated panels are a common feature of air conditioners, washing machines, and cooking ranges, among other household appliances, for improved lifespan and a stunning appearance.
Agriculture and Architecture
Guide rails, door knobs, fittings, and gutters are all coated with powder during construction, while tractors, trailers, and storage systems are among the agricultural tools and equipment that employ powder coating.
Electrical
Transformers, electric junction boxes, and small, commonplace items like computers and light fixtures are among the electrical projects that employ powder coating. Powder is also used to coat the boilers, radiators, and furnaces of HVAC systems.
Safety and Public Works:
Public works projects such as pipelines, fire hydrants, buses, and other public works projects require powder coating. Because powder coating is long-lasting and resistant to corrosion, it is utilized in safety equipment, including fire extinguishers and medical devices.
Lawn and Garden
Snow shovels, BBQ grills, and other outdoor equipment are powder-coated.
Powder coating is a popular alternative for a variety of metal fabrication applications because of its many advantages, which include efficiency, minimal maintenance, environmental friendliness, durability, and customization choices.
How much time does Powder Coating Last? How Long does the Powder Coating Finish take to Complete?
Powder coating is renowned for its extraordinary endurance and toughness, and the quality of the application, the surroundings, and upkeep are some of the variables that might affect how long the powder coating finish lasts. It is anticipated to persist for a considerable time—often more than 10 years.
A powder-coating finish has a 15–20 year lifespan if properly applied and utilized in an appropriate setting and powder-coated metal surfaces outlive painted metal surfaces, remaining unscathed and rust-free for up to 20 years.
It has a well-established track record of durability and is frequently selected for its capacity to offer a low-maintenance, long-lasting surface.
What is the Price of Metal Powder Coating?
The costs of metal powder coating can vary based on factors such as the size and type of the object being coated.
Prices for household items such as fences, gates, railings, and appliances usually fall between $50 and $500. The final cost is influenced by factors like prep work and size. Certain items, such as bicycle frames, ATV frames, and motorcycle exhausts, may have different prices. Typically ranging from $70 to $250 per item, and when it comes to vehicles, the cost of powder coating services for various components such as rims and wheels can range from $50 to $700 per item. Industrial applications can vary in cost, ranging from $4 to $45 per square foot. The final price will depend on the project’s complexity and size.
How can you Find Trustworthy Suppliers of Metal Powder Coating?
The first place to look for reliable metal powder coating suppliers is online, where sites like Global Sources, Alibaba, and ThomasNet provide comprehensive supplier profiles and evaluations. A verified membership is another service offered by industry bodies can be prove helpful in this regard. You may see vendors’ products and meet them face-to-face by going to trade exabitions and meetings.
Make careful to use of resources to verify each company’s past, reputation, certifications (such as ISO 9001), and financial soundness.
In order to measure the coatings’ durability, quality, and finish, request product samples from possible vendors after discovering eligible manufacturer. Make certain they supply certifications and test results for their goods.
To get references from previous clients and to learn about their dependability and level of customer service, browse internet reviews. Examine whether they can reliably fulfill your quality standards and delivery dates.
A dependable provider should have good customer service and communication. You may locate credible vendors for your metal powder coating requirements by following these guidelines.
Ask for examples of their work or visit them to check the caliber and workflow. Examining a portfolio of finished work will help you gauge their skill level and workmanship. Get quotations from many vendors and contrast the costs and lead times. Ensure the price covers all required actions, such as application, curing, and surface preparation.
Assess their promptness and quality of client care. Throughout the project, a dependable provider needs to be ready to offer assistance and transparent communication.
How do you Safeguard your Health when Working with Metal Powder Coating? Which Safety Attire is Appropriate for you to Wear?
You must follow safety precautions to safeguard yourself while working with metal powder coating. So, we must follow all these crucial safety precautions:
For respiratory protection, you can use a respirator or dust mask certified by NIOSH. It will be helpful to prevent breathing in tiny powder particles and it can lead to respiratory problems.
Wear safety goggles for eye protection or a face shield to defend your eyes from powder particles and any splashes.
Skin Protection is also necessary, so wear protective clothes like gloves, long-sleeve shirts, and jeans to avoid touching powder-coating materials on your skin.
Proper ventilation can make sure the work area has enough ventilation to lessen the concentration of airborne particles. Operating in specially designated spray booths can help maintain air quality.
If the coating procedure involves noisy machinery, wear earmuffs or earplugs to protect your hearing.
You can wear safety shoes with steel toes and non-slip bottoms to protect your feet from heavy items and provide adequate grip in potentially slippery locations.
It is good if you obtain the necessary instructions on how to handle powder coating equipment safely. Learn about the Material Safety Data Sheets (MSDS) and other safety considerations for the chemicals and powders you use.
You just need to adhere these safety precautions, and using the proper personal protective equipment can greatly lower the hazards involved in working on metal powder coating projects.
Which Color Variations are Possible for Metal Powder Coating?
A vast array of color combinations and finishes are available with metal powder coating to satisfy a variety of practical and aesthetic requirements. Primary and secondary hues like red, blue, yellow, and green as well as neutrals like gray, beige, and brown are examples of standard colors. Silver, gold, bronze, and copper metallic coatings are also well-liked.
A variety of special effects are available, such as textured coatings that provide wrinkled, hammered, or rough surfaces, as well as matte, gloss, satin, and semi-gloss finishes. Vibrant, shimmering, or glossy effects can be added using unusual choices including candy colors, metallic flakes, iridescent finishes, and clear coatings. Using color standards like RAL or Pantone, custom color matching services allow the development of precise colors or combinations.
Combinations include gradient mixes, speckled patterns, two-tone contrasts, camouflage, and multicolored swirls for a marbled effect are popular. Additionally, specialty coatings are offered, including heat-resistant coatings for high-temperature applications, anti-graffiti coatings that facilitate simpler cleaning, and anti-microbial coatings that stop bacterial development. Aesthetic preferences and the intended use and surroundings should be taken into account when choosing a color combination. Speak with providers to determine which solutions are best for your particular needs.
Material Used in Powder Coating Metal
Aluminum (Al 5052, Al 6061, Al 7075)
Aluminum alloys are highly strong and low in weight and are widely used in many sectors. The composition and mechanical characteristics of these alloys vary such as 5052 is renowned for its superior resistance to corrosion. 6061 for its adaptability and strong mechanical characteristics, while 7075 is known for its exceptional strength. Aluminum alloys are perfect for automotive, aerospace, and architectural applications. Powder coating improves its inherent corrosion resistance and offers a range of beautiful finishes. The powder coating procedure prolongs the life of aluminum items while preserving their aesthetics by shielding metal surfaces from environmental elements, including moisture and UV rays.
Steel
It is known for its strength and adaptability and it comes in several types: carbon steel, stainless steel, and mild steel. While mild steel is easily formed and weldable, stainless steel provides corrosion resistance. Carbon steel is robust and long-lasting. Steel may be powder coated in various colors and textures to create an extra defense against rust and corrosion. Because of this, powder-coated steel may be used in various industries, such as equipment, automobiles, and construction. The coating contributes to longevity and it also improves the visual appeal of steel objects.
Iron
Iron is widely utilized for both structural and ornamental purposes and it is include wrought iron and cast iron. Wrought iron is valued for its ductility and malleability. But cast iron is recognized for its superior casting qualities and strength. Iron coated with powder offers a strong surface that resists rust and weather damage, making it perfect for outdoor furniture, gates, and fences. By providing a range of colors and finishes, the coating further improves the iron items’ ornamental qualities while guaranteeing their long-term protection and aesthetic integrity.
Zinc
Steel is galvanized with zinc to stop corrosion. It provides exposed steel surfaces with cathodic protection and acts as a defense barrier. Zinc coatings products become more aesthetically pleasing and durable when we apply powder-coated as adding a powder coating layer to galvanized steel. It makes the things even more resilient to adverse weather and also makes them ideal for outdoor uses like light poles, and structural elements. This two-layer defense guarantees a longer lifespan and lower upkeep expenses.
Copper
Because of its superior electrical conductivity, resistance to corrosion, and aesthetic features, copper is highly prized. It is utilized in plumbing, electrical wiring, and ornamental features. Copper powder-coated has a strong finish that increases its resistance to wear and tarnishing. This is very helpful in ornamental and architectural applications where keeping the look is essential. Furthermore, copper that has been powder-coated might be utilized in settings where it can be subjected to adverse weather, guaranteeing that it will hold its usefulness and visual appeal over time.
Brass
Brass is a copper and zinc alloy prized for its ability to withstand corrosion, machineability, and aesthetic appeal. It is extensively utilized in products like ornamental hardware, musical instruments, and plumbing fittings. Brass’s inherent resistance to corrosion and wear is strengthened by powder coating, which also gives the metal a durable and eye-catching surface. Brass components may be used for utilitarian and ornamental reasons because of the coating, which also allows for various colors and textures. Because of this, powder-coated brass is perfect for usage in damp or worn conditions.
Bronze
A copper and tin alloy, bronze is prized for its robustness, toughness, and aesthetic appeal. Due to its low friction qualities, it is utilized in bearings, medals, and sculptures. Bronze that has been powder-coated gains an extra layer of protection that helps maintain both its aesthetic and structural integrity. This coating is very helpful for outdoor sculptures and architectural features—where exposure to the weather can lead to oxidation and tarnishing. Manufacturers may make sure that these bronze objects have their aesthetic appeal and functionality for a long time by powder painting them.
Titanium
Titanium is a highly desirable material for industrial, aeronautical, and medical applications due to its remarkable strength-to-weight ratio, resistance to corrosion, and biocompatibility. Powder coating, which also improves titanium’s look with different finishes, further protects it from environmental elements. This is especially significant in applications—like high-end consumer goods and architectural components—where durability and aesthetics are equally vital. The coating prolongs the life and preserves the functionality of titanium items by preventing surface wear and scratches.
Steel that is Galvanized
Galvanized steel, which is zinc-coated to resist corrosion, has several uses when rust resistance is essential. Over galvanized steel, powder coating creates a smooth, appealing appearance and an additional layer of protection. The steel components are extremely resistant to corrosion and wear because of the mix of powder and zinc coating, which makes them perfect for outdoor constructions, automotive parts, and building materials. Galvanized steel is a flexible and dependable solution because of the additional durability and aesthetic possibilities provided by powder coating.
Alloys Made of Stainless Steel
Known for their strength and resistance to corrosion, stainless steel alloys are extensively used in everything from kitchen appliances to medical equipment and building materials. Adding a powder coating to stainless steel improves its resistance to wear and increases its longevity. Additionally, a range of finishes may be achieved with this coating, allowing stainless steel goods to be tailored to meet certain aesthetic needs. Stainless steel with a powder coating works especially well in abrasive conditions where performance and appearance are crucial.
Magnesium
Magnesium is a lightweight metal with a high strength-to-weight ratio frequently used in the electronics, automotive, and aerospace sectors. A powder coating shields magnesium against corrosion and surface damage and improves the material’s longevity. This is critical for applications where durability must not be sacrificed to save weight. Because of the protective layer that powder coating offers, magnesium components are appropriate for high-performance applications because they can tolerate exposure to hostile conditions and mechanical wear.
Through comprehension of the distinct advantages associated with each material, producers may enhance the lifetime and performance of their goods.
Final Thoughts
Compared to typical liquid paints, powder coating is a more flexible and long-lasting finishing method that provides several benefits, such as improved durability, a superior finish, and environmental advantages. The procedure calls for careful planning, accurate application, and appropriate curing to guarantee the best outcomes. The powder coating process finds widespread application in several sectors, such as automotive, appliances, outdoor furniture, and architecture, due to the diverse variety of powder coating types accessible, each possessing distinct features and the extensive range of materials that may be powder coated. Through comprehension of the advantages, procedures, and components needed, producers may produce durable, high-quality finishes that satisfy the requirements of their markets.
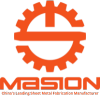
Send Your Inquiry Today



+86-18969433502

sales@sheetmetalmasion.com