How to Cut Stainless Steel Sheet Metal at Home – The Ultimate Guide
Cutting stainless steel sheet metal can be challenging. While advantageous, its strength and durability make it hard to work with with standard tools. Without the right techniques, you could get rough edges, waste materials, or break your tools. It can cause costly mistakes, or compromised projects. But there’s good news! By adopting the proper methods and taking the proper safety measures, you will be able to cut stainless steel efficiently and obtain clean, accurate results. Here, you’re going to learn the tools, techniques and precautions necessary for handling this tough material as a pro. Goodbye, frustration, hello professional cuts!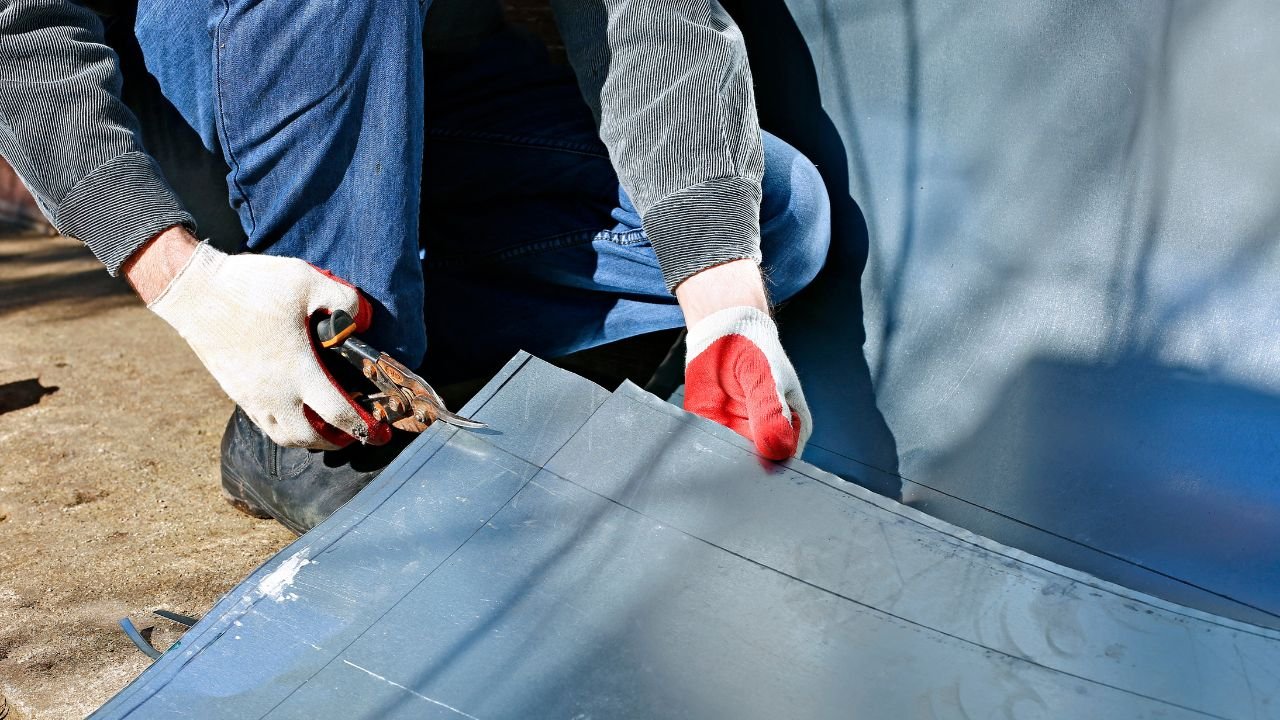
Table of Contents
ToggleExploring Science Behind Stainless Steel Metal
Key Properties
Retaining superior corrosion resistivity, stainless steel is ideal for usage in chemicals or moisture rich environemnts. Its strength is durable even under heavy loads and the heat tolerance makes it suitable for high temperature applications. There are different grades, for example, 304 and 316 for different purposes. For example, the 304 variety is used for general use or 316 which offers better corrosion resistance suitable for marine environments. If you know what grade you need, then you can pick what material is best for your project.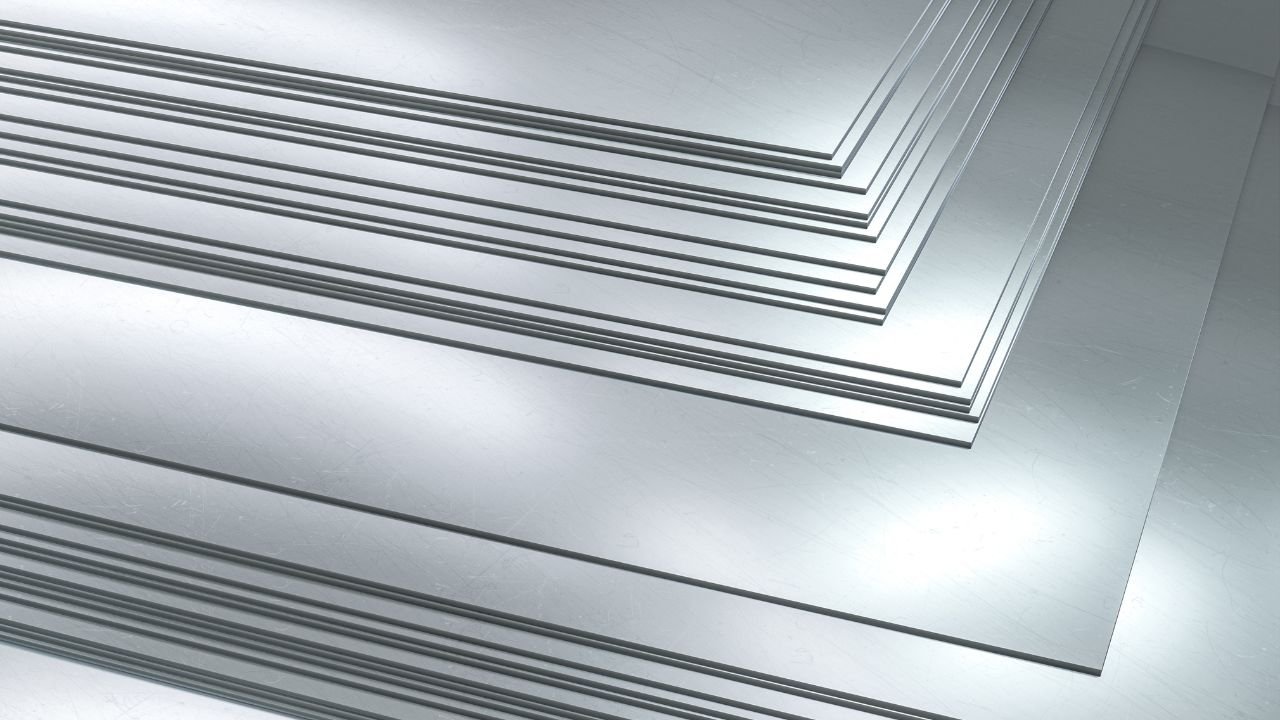
Challenges In Cutting
Working with softer metals is easier than cutting stainless steel. It is fairly hard, so it requires special tools to use without damaging or wearing it. Cutting creates heat and can warp the sheet and affect precision. This is crucial for the process and the many different cooling techniques used. Stainless steel’s reflective properties too will need to be factored in, especially when working with laser cutters. Solving these issues ensures smoother results and material quality.Selecting the Right Method
Sheet thickness and project needs dictate which cutting method is best. For thin sheets, laser or waterjet cutting is precision. Plasma cutting might prove more efficient for thicker pieces. When thinking of machining stainless steel, always consider: the cost of the tool, the precision of the operation, and the type of stainless steel. Time saved by tailoring your approach and results that are optimal.Tools You can Use to Cut
Tin Snip: Perfecct when it comes to cutting thin sheets. They are very lightweight, easy to handle and as well cost effective. Use for straight or slightly curved cuts. Though they hold up to thicker sheets, these tend to be more of a challenge to work with.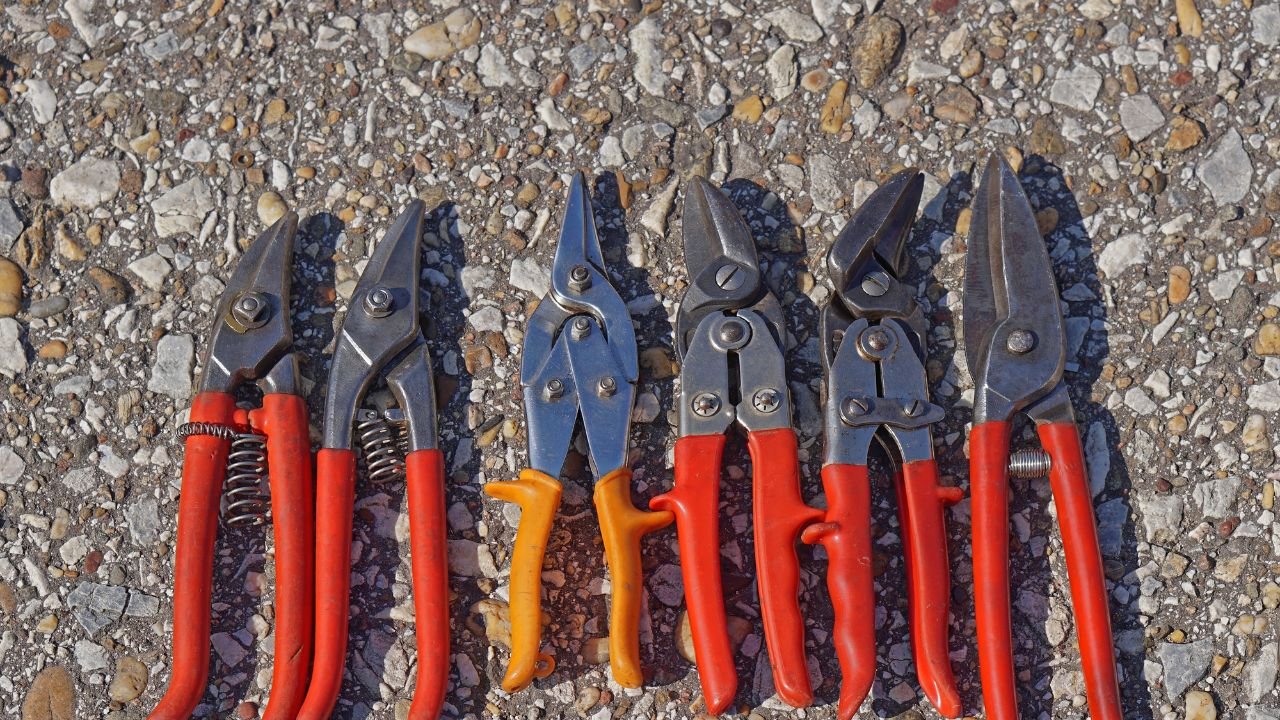
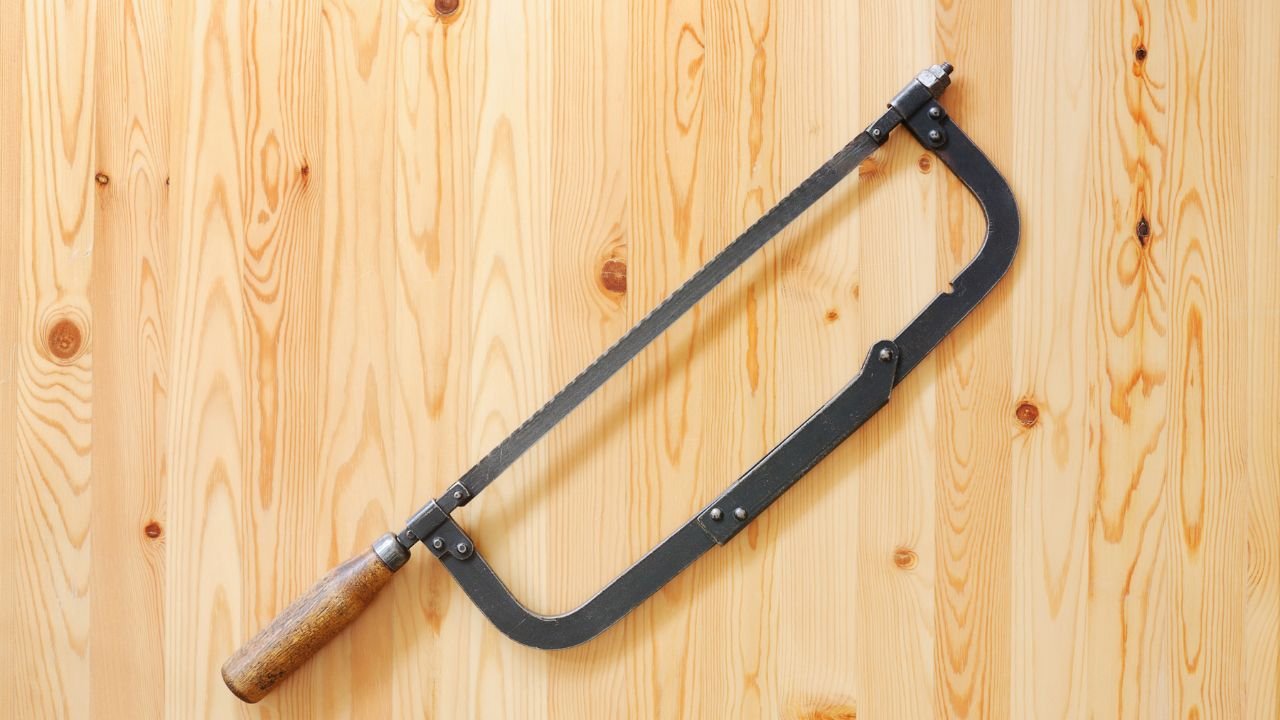
Power Tools
Angle Grinder: It is a versatile, powerful tool. Use with stainless steel cutting disc for fast and accurate cutting. Cutting thicker materials and trimming edges is perfect for angle grinders. Before carving, ensure to wear safety gear to protect against sparks and/or debris.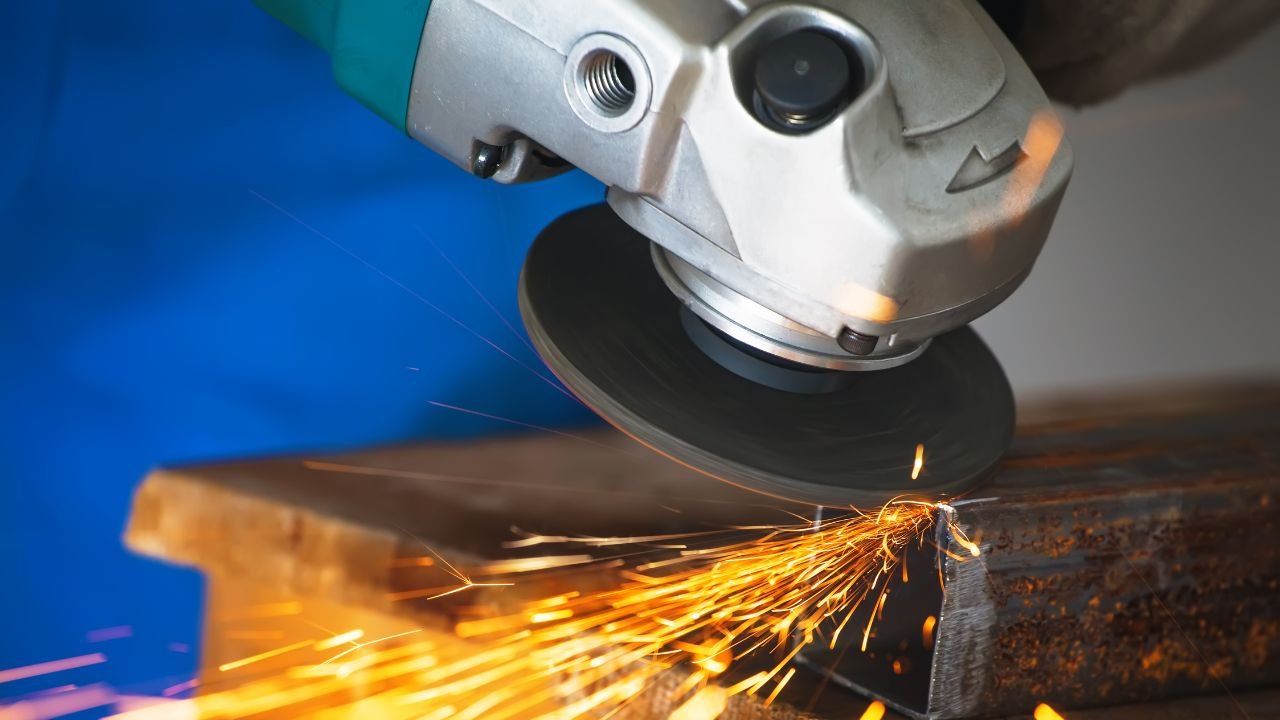
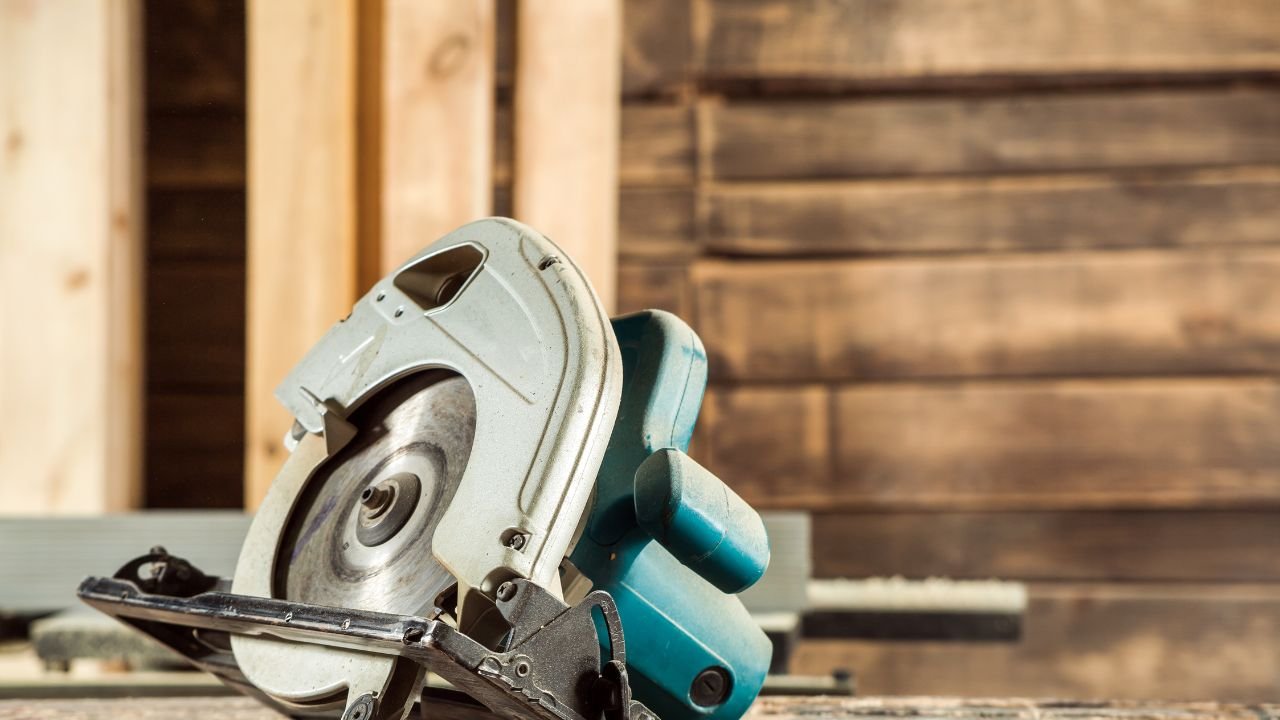
Specialty Tools
Plasma Cutter: For thick sheets, this tool has high precision. It’s a very fast and efficient method but relies on power source and experience.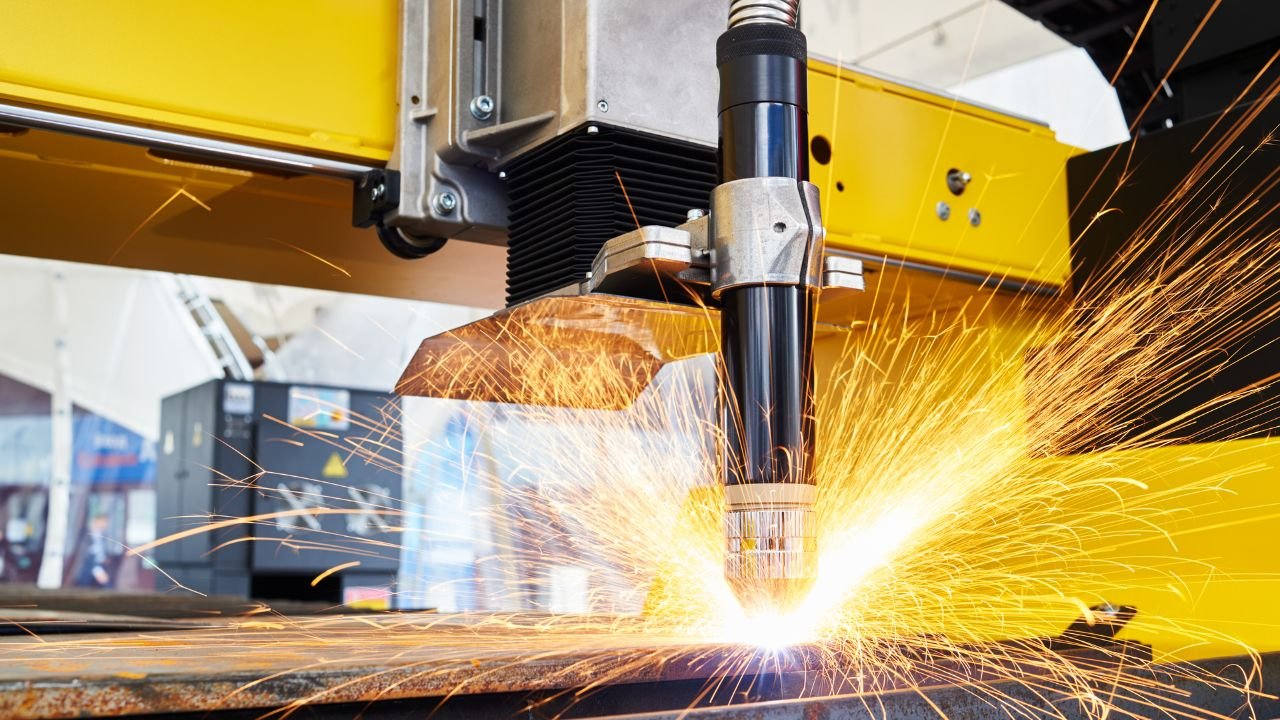
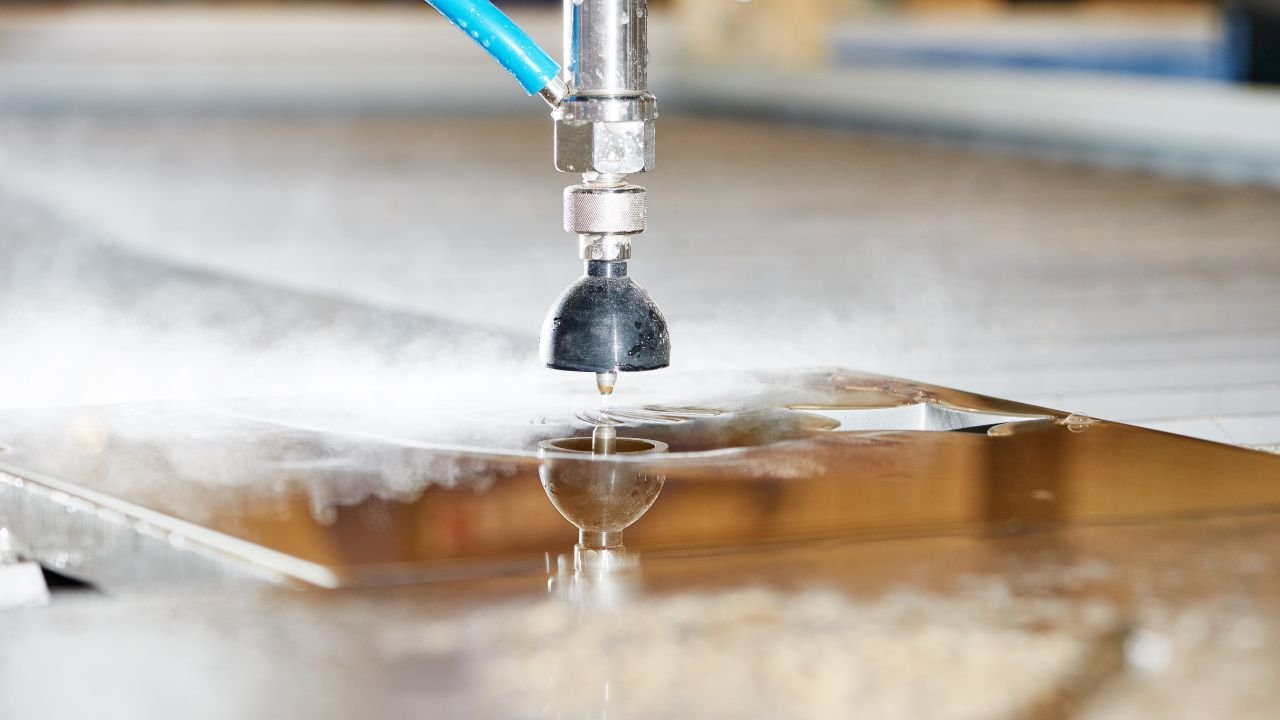
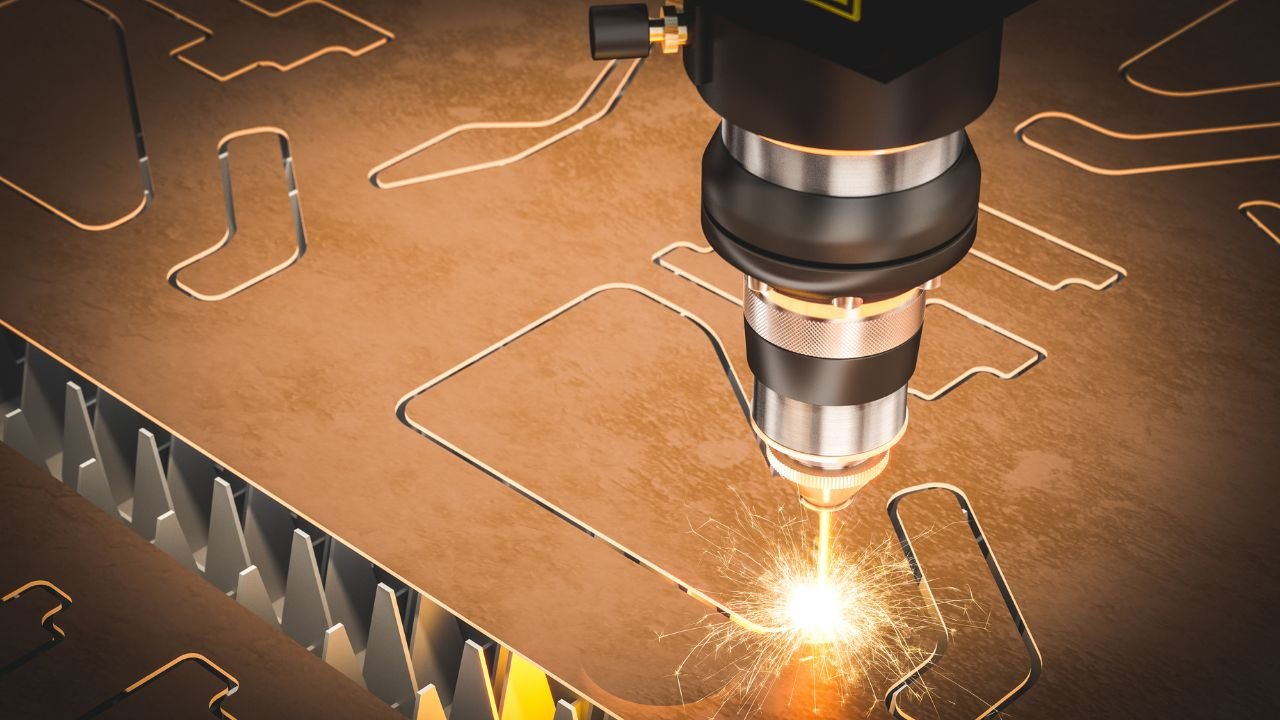
Preparatory Measure Before Starting
Mark and Measure
Measure stainless steel sheet size by utilizing a tape measure. Use marker or tape to mark the lines of cutting. Measure twice and cut once to avoid costly fabrication errors. By taking this simple step of precision, we are also minimizing waste.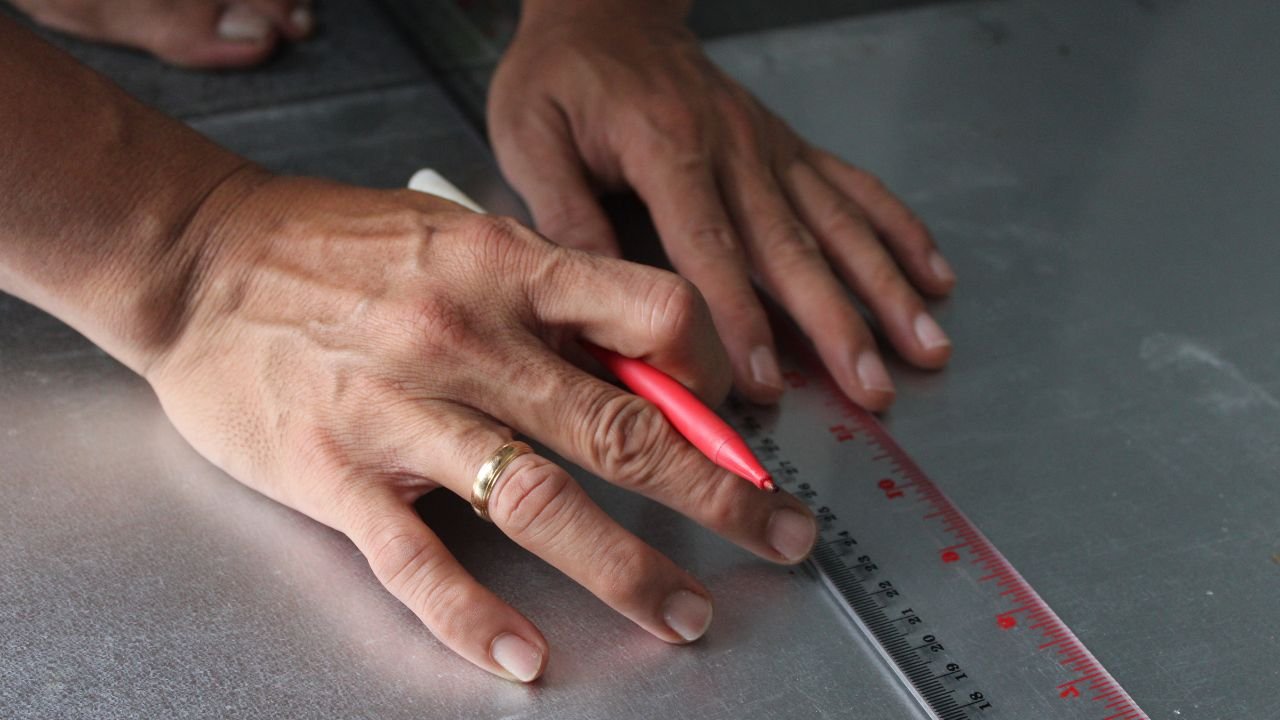
Secure the Sheet.
Ensure the stainless steel stabilizes to safety and accuracy. Holding the sheet securely to a workbench or cutting surface with clamps. An additional stability can be provided by a non-slip mat. Movement during cutting increases the risks of accidents and can sometimes lead to less than ideal edges. For the best results, always work on a firm and level surface.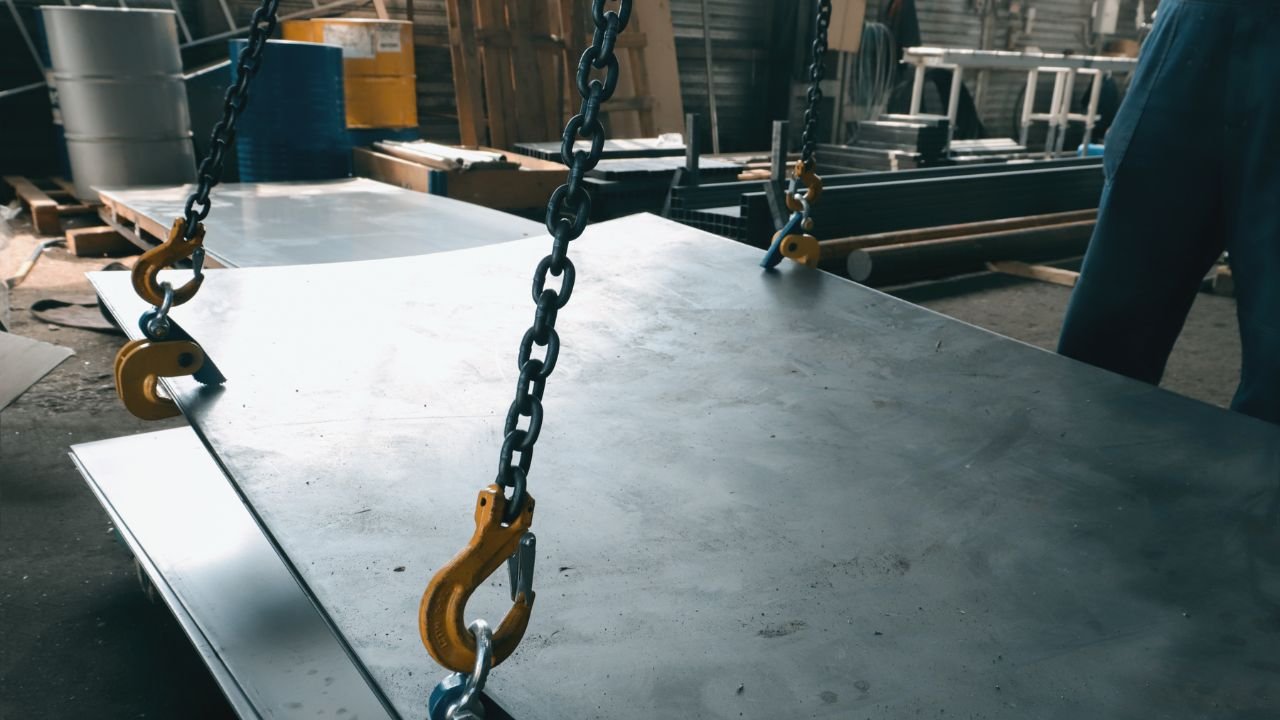
Choosing the Correct Tool
Use tools and cutters that are suitable for the thickness and type of stainless steel you are cutting. If you are working with thin sheets, aviation snips or hand shears might be enough. Angle grinder or plasma cutter power tools are required to cut through thicker sheets. Use of stainless steel matches the blade material for efficient performance. Blades coated with carbide or diamond work best.Pre-Cut Inspection or Maintenance
Pick your tools and inspect them first. Look for sharpness and check for damage to blades. Prevent debris from affecting performance by cleaning the cutting tools. Properly maintained equipment provides cleaner cuts, keeps your tools working longer.Methods or Processes to Cut
Here’s how to cut based on the thickness of the sheet:Cutting Thin Sheets
For thin sheets, use tin snips or hacksaws. For straight cuts, tin snips are perfect whereas hacksaws are for more tight angles. Put your sheet within clamps before begin to cut. Control work slowly and steadily. Make smooth, even strokes to avoid jagged edges.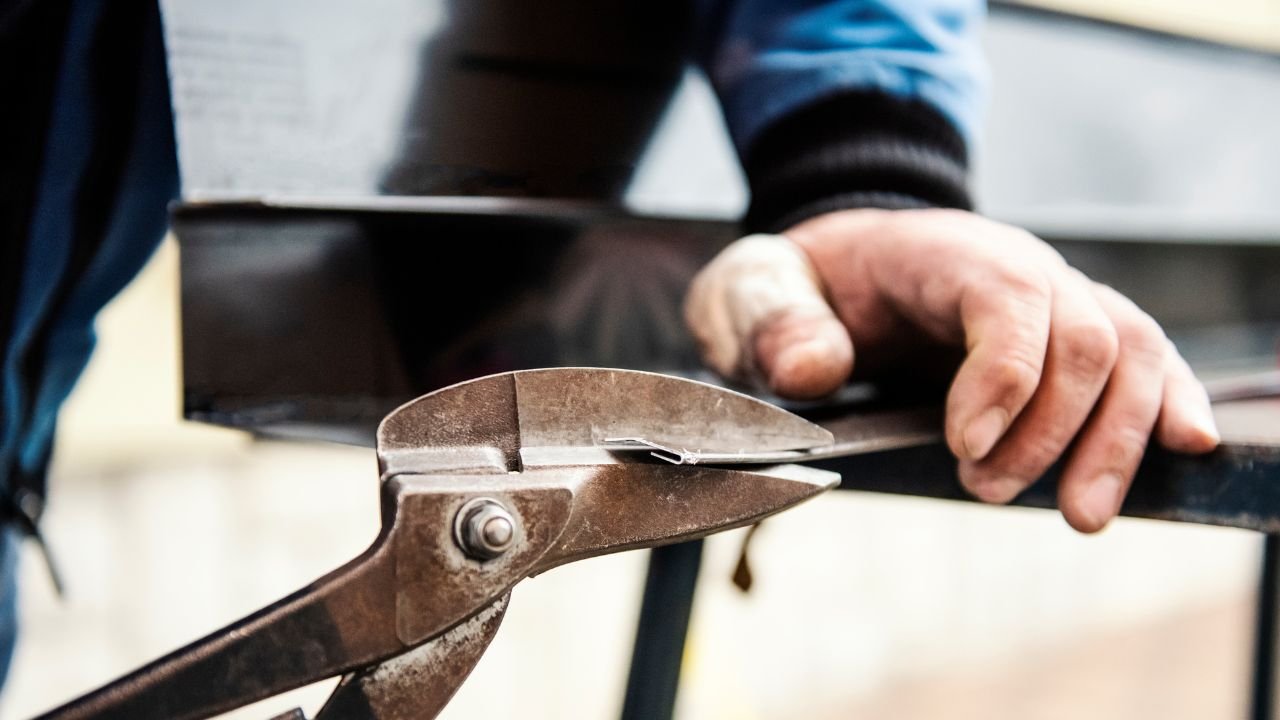
Cutting Medium Sheets
Quick, straight cuts are possible with angle grinders; jigsaws allow curve cutting. Avoid overheating by using cutting blades designed for stainless steel and taking regular breaks. Mark your cut lines precisely and follow them exactly.Cutting Thick Sheets
For thick sheets, consider plasma cutters or water jet cutters. High heat is used in plasma cutters to slice quickly through metal. Water jet cutters, however, use pressurized water pumped through the cut with abrasives, keeping the cut pieces cool, while they precisely slice through flesh. Always wear protective gear to guard sparks or debris.Advanced cutting
Detailed patterns are best cut with laser cutters. These tools are unsurpassed in accuracy for complex designs. Find a speed and power setting for clean cut without scorch. Try your settings with scrap material before tackling your project.Handling Post Cutting Edges
File and deburr edges to smooth finish after cutting. Remove sharpness with metal files or deburring tools. It is important to wear gloves at all times when working with edges. Wipe down the sheet for safety in case any of the remaining metal shards are stuck to the sheet.Safety Measures for Cutting Sheets
To ensure a secure and safe process, follow these precautions.Wear PPE
The safer thing to do is to wear safety glasses when working in areas of flying debris. Wear durable gloves to protect hands from sharp edges. Make sure to include ear protection to protect yourself from loud tool noises. To help reduce the risk of becoming injured by a spark or heat, wear flame resistant clothing that is snug fitting.Maintain Safety
Clean your workspace of mess and clutter. Avoid accidents by removing unnecessary tools or materials. Prevent inhalation of harmful fumes. Sit in a well lit area so you can clearly see your tasks.Follow Tool Guidelines
Examine cutting tools to identify wear and damage. Broken or dull tools add to the danger of accidents. Only take tools from the store when needed, storing tools securely when not in use. Find the right tool for the cut you want to make.Manage Sparks
During cutting, use cooling agents or water to control heat buildup. Keep flammable material away from your workspace.Avoid These Mistakes While Cutting
You can save yourself some time, material, and effort by avoiding these common mistakes.Using the Wrong Blade
Sometimes having the wrong tool or a dull blade can ruin your cut. Unsuitable dull blades struggle to cut through stainless steel, resulting in uneven edges. Use stainless steel blades or specialized shears only. Start from sharpness check. With the right blade, slices are cleaner and smoother.Incorrect Measuring or marking
Wasted material and frustration are caused by inaccurate measurements. Double check your measurements and marking. High visibility markers, along with precise measuring tools like calipers and tape can be used. It allows your cuts to line up perfectly with your design.Ignoring Safety
That puts you at risk of skipping safety measures. Wear personal protective equipment for complete protection at all times. Maintain your tools well and in a good condition. Accidents may occur due to poor tool handling or failure to follow safety checks.Rushing the Process
Sometimes, the hurrying leads to uneven cuts and damages to the material. Plan all cuts and take a methodical approach. Let the tool work at the speed it was designed for and do not force it. This helps minimize mistakes and improve results.Applying Too Much Pressure
This can cause excessive pressure that can warp the material and possibly damage your tools. It takes a steady hand and patience to work with stainless steel. Relax. Let the sharpness and speed of the tool do the work. Consistent, moderate pressure ensures clean cuts without strain.Prior to Cut Processes
Cleaning or Finishing
When cutting Stainless Steel, concentrate on cleaning and finishing for a professional result. Sharpen edges and remove burrs so that they are safe and also have a polished look. Smooth rough edges with sandpaper or use a deburring tool. It will remove any residue, oils or dust from the surface which could affect the further processing or appearance of the product.Inspection
Check the cut sheets over very carefully to make sure they’re absolutely precise. Compare against design dimensions and quality check edge for consistency. Cope with any inaccuracies and make any necessary adjustments to correct them. Solution: This guarantees a perfect fit, especially for complicated projects.Tips for Storage and Handling
Stainless steel sheets are stored in proper way so that they may preserve their integrity. Putting protective layers between sheets prevents scratches. Do not store in humid environments to prevent corrosion. Remind them to stack evenly to avoid warping or damage in the event of hollow.Tips to Optimize Efficiency
Selecting the Best Condition
You can improve visibility by setting up a well lit workspace. Keep tools close and away from distractions to stay focused. It speeds up workflow and decreases error when the environment is clean and efficient.Maintenance
Keep up your cutting tools to perform better. Make sure to sharpen blades regularly for precise cuts. Clean your tools after each use to remove debris. Prevent wear and help moving parts operate smoothly by lubricating them.Cooling Techniques
Both heat and cutting tools can damage stainless steel. Use cutting fluids or sprays to reduce friction and prevent overheating. Blade wear and material finish also improve when cooling techniques are utilized.Plan the Cut Sequence
Avoid making mistakes by planning your cuts logically. Begin to form the larger sections before increasing in complexity to reach smaller details. This approach cuts down on material stress and produces cleaner cuts.Reusing Scrap
Reuse the leftover parts in order to reduce waste. Save scraps for future use or incorporate them into the smaller projects. This provides a sustainable approach, benefiting your budget and the environment.Conclusion
Stainless steel must be cut with the correct tools, using the right techniques and taking the time to prepare it right. You have learnt how to choose tools, manage heat and precision. These tips will help you get clean, professional cuts without damaging the material. Success begins with preparation. Always measure accurately, secure your sheet and wear safety gear. Practice a proper maintenance to extend the tool life and increase the results. Even challenging cuts can be handled with patience and best practices. It’s now your turn to apply these insights. Learn tools, try methods and start cutting yourself!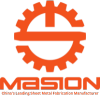