23 Types of Sheet Metal Assembly Rivets. An Ultimate Guide
Sheet metal assembly relies on rivets that provide reliable, permanent fastening across a wide range of industries. Correctly choosing the right type of rivet guarantees structural integrity, maximum performance and long pterm durability for your assemblies. Each type of rivet has a specific function from high strength aerospace fasteners to lightweight options for electronics. This guide will explain the 23 types of rivets, their components, advantages, and uses to ensure your next project is correctly and confidently decided.
Table of Contents
ToggleUnderstanding Rivets
A rivet is a form of permanent mechanical fastening that is used to fasten two or more materials together. They are often used in sheet metal assembly and have predrilled holes that a metal pin is inserted into and then deformed to hold it. This makes a powerful and enduring connection- particularly handy when welding is not the best solution. The sources that provide a variety of rivets include reliable sources such as Zoro fasteners, which are used in industrial, commercial and field use.
Components of Sheet Metal Assembly Rivets
- Rivet Body: The main part of the rivet which usually comprises of aluminum, steel, or copper materials.
- Rivet Head: Rivet head is the top region of the rivet serves as its foundation during installation to offer structural stability.
- Mandrel: It refers to a shaft that creates the rivet piece and supports the rivet body.
23 Types of Rivets for Joining Sheet Metal
Aircraft Rivets
Aircraft rivets play a very important role in the fastening of parts in aircraft. They are aerospace specific. These rivets are applicable in aircraft sheet metal assembly. They are located in fuselages, in wings, in other critical locations. They can handle extreme conditions and vibrations. They are highly durable hence suitable in highly stressful applications. They are also not easily affected by extreme temperatures. Aircraft rivets however cost more than the usual rivets, and they need special tools to handle them, such as an aircraft rivet removal tool, therefore they are not well suited to general use.
Blind Rivets
Blind rivets are the solution when only one side of the material can be reached. They are frequently used in Sheet Metal Assembly applications with one side accessible. These are industries such as automotive and electronics manufacturing. Blind rivets are simple to apply. You do not have to go to the backside of the material. They are very convenient in a cramped assembly. They are however not so strong as solid rivets. The head of the rivet does not necessarily sit flush. This may be a matter of aesthetic reasons.
Eyelet Rivets
Eyelet rivets can be designed with a tubular body and flared head, suiting them for making holes through which wires or cables can pass. With such strength and durability, these rivets are an excellent choice for securing wires and cables. But other types of rivets can be easier to install than theirs. These are mainly used in the electronics, textile and fashion industries, where routing cables or securing components is a must.
Swaged Pin
Swaged pins are strong. Once in place, they are permanent. The pin is deformed through swaging to produce a strong grip. This gives a locking grip in Sheet Metal Assembly applications. It is perfect in heavy-duty applications like machines and building parts. Installation, however, requires special tools. The pin is hard to extract after setting. Construction and heavy machinery often need permanent assembly. This is the reason why swaged pins are used.
Taper-Lok Fastener
Tapered design of Taper-Lok fasteners helps to lock materials tightly together. They are frequently used in precision applications that need high strength fastening. Taper-Lok Fasteners have an outstanding hold, but you have to use special tools to install them. Aerospace and military applications are where they are usually found, where maximum strength and precision are paramount.
Thin Wall Blind Bolt
Thin-wall blind bolts provide a fastening solution for thin materials without opening both sides. Under the Military, the standard bolts are easy to install, even in confined spaces, but limited strength and not appropriate for thicker materials. Such components are often used in automotive and aerospace industries.
Double Cap Rivet
The stainless steel double cap rivets are used similar to the regular cap rivets and have a cap on the front side and backside of the material. They are particularly used in joining thicker materials and they are also durable. They are however cumbersome and most times require other tools to install. They are often selected in such industries as heavy machinery and construction where fastening is important due to their increased holding strength.
Drive Rivets
Installation of drive rivets is simple and fast. A driving tool is used to expand the rivet to keep two materials together. They are good to use in most applications as they are very easy to use. Being a form of automotive rivets, they are commonly applied to vehicle and appliance production. These industries are not after maximum strength in assembly but speed. Nonetheless, drive rivets are not as tough, as any other types of rivets and have a limited holding capacity.
Expansion Rivets
Expansion rivets are versatile fasteners which expand once installed on the material to provide a secure grip. Materials of different thicknesses are suitable and are often used in fragile or hollow materials. Expansion rivets are easy to use but do not hold as well as solid rivets, and can damage softer materials. They are usually used in electrical enclosures and automotive interiors where versatility is important.
Flush Rivets
Flush rivets are designed to allow for a smooth finish with the surface of the material. Because of this, they are ideal for applications where aerodynamics and aesthetics are crucial. Flush rivets can be installed with high precision, but may not be as strong as other rivet types. In industries like aerospace, automotive and military, where a low profile surface is crucial for performance, flush rivets are widely used.
Friction Lock Rivets
Friction lock rivet has a special locking mechanism so that they remain in place when subjected to vibration or pressure. They are highly resistant to movement, so are suitable for critical applications. However, the cost is slightly higher than that of standard rivets, and they require specialized installation tools. In automotive, aerospace and industrial applications where vibration resistance is needed, friction lock rivets are commonly used.
Full Tubular Rivets
There are full tubular rivets with a hollow body and a solid head, delivering secure fastening and still retaining the overall structure’s lightweight. These rivets are employed when weight is a factor, in light automotive components, appliances, and electrical enclosures. Although 1/8” solid rivets can give a good strength, they are not as strong as the larger solid rivets and can be deformed by high stress. In certain applications, full tubular rivets have superior strength-to-weight.
Headless Rivets
The name of headless rivets is exactly what it suggests: i.e., without a head and offering a smooth and discreet way to fasten. Ideal for applications where appearance or a clear finish is paramount, these rivets are perfect. Instead they need special installation tools and are less strong than their headed counterparts. In the electronics and automotive industries, securing components without visible heads is common and headless rivets are used.
Hi-Lok Rivets
Hi-Lok rivets are high strength threaded fasteners with excellent holding power. Specifically, they are designed for applications that require higher clamping forces. Hi-Lok rivets offer more holding strength than standard rivets but are more expensive and require specialized installation tools. In aerospace and high performance automotive areas these rivets are widely used.
Large Flange Rivets
The large flange rivet has a wider head to more evenly distribute pressure on the material. It helps prevent material deformation and adds in strength. The larger head will also have an impact on the aesthetics of the material and may not be the best for all applications. Typically used for heavy machinery and structural components are large flange rivets where strength and stability are critical.
Nameplate Rivets
Nameplate rivets are made to be used to attach identification plates, labels, or nameplates to equipment or products. They can be installed easily and do not have a temporary connection. They are used in assembly of sheet metal parts mostly in cases where clear labeling is needed. They are however not applicable in areas of high stress and are primarily applied in the non structural environment. Nameplate rivets are common in the labeling of products or parts in the electronics and manufacturing industries.
Press Rivets
A secure hold is created by pressing rivets using the pressure to expand the rivet inside the hole. They are easy to install, don’t require special tools and are rivets. However, they aren’t as strong as other rivet types and are difficult to remove without damaging the material. Non structural fastening is achieved using press rivets in industries such as automotive and furniture manufacturing.
Self-Piercing Rivets
Self-piercing rivets are capable of creating a hole during the fastening of two materials. The ability to install without having to pre-drill makes them perfect for the quick installation. They can, however, deform thinner materials and may not be suitable for all material types. Most often used in automotive and electronics manufacturing, these rivets.
Semi-Tubular Rivets
Similar to full tubular rivets, semi tubular rivets are hollow body and have a solid head that makes them easier to install. Lightweight and easy to use, these rivets are not as strong as solid rivets, but are less complicated for use. In light duty applications such as electronics and appliance manufacturing, semi tubular rivets are often used.
Shoulder Rivets
Shoulder rivets also have a collar or shoulder for a precise and secure joint. Standard rivets offer worse alignment control than what these provide. However, installation of these devices requires specialized tools and can be expensive. In applications such as the automotive and aerospace industries, shoulder rivets are used, where precise alignment is necessary.
Solid Rivets
These are solid rivets which are formed with a solid shaft and head. These rivets have excellent strength and are long lasting. But, they need access to both sides of the material and installation can be more labor intensive. Aerospace, construction and heavy machinery industries widely use solid rivets for strength and reliability.
Split Rivets
Split rivets consist of a split shaft that permits them to expand to attach two materials together. They are easy to install and a low cost fastening option. They provide less holding power than solid rivets and are not recommended for high stress applications. Split rivets are widely used in light duty applications, including in the clothing and fashion accessory field.
Barrel Bolts (Sex Bolts)
Sex bolts (or barrel bolts) are a type of fastener, usually a bolt with a mating barrel to create a secure fastener. When put together, they have a good grip thus useful in attaching thicker materials in manufacturing automobiles and heavy machineries. They are stronger than rivets and therefore costly, although the cost is worth it. Other variants such as the window barrel bolt find common use in architectural and fixing applications where strength and cleanliness of appearance are important.
Installation Techniques for Sheet Metal Assembly Rivets
Manual Installation
Nevertheless, manual installation is an option in case you have a small-scale project or require a simple solution. This is commonly applied in the sheet metal assembly process, where hand tools such a rivet guns are used. Low volume production or field work where speed is not an important aspect usually involves manual methods. They are simple to use, and provide controlled pressure on the rivet, which is ideal in precision work.
Pneumatic Installation
In medium and high volume installations pneumatic tools provide a faster and more efficient performance. These tools work by using air pressure to set the rivet, thus dramatically faster than is possible with the use of manual methods. Pneumatic tools can help you save time and effort if you need to do several rivet installations in a short amount of time. In the automotive manufacturing industry, they are commonly used.
Hydraulic Installation
High strength rivets require hydraulic systems; in the case of large scale projects. These systems apply heavy-duty secure fastenings by way of utilizing hydraulic pressure to apply significant force. Hydraulic installation is common in aerospace or auto industries due to the fact that precision and strength are crucial.
Conclusion
Learning the various rivets of the sheet metal assembly assists you to construct stronger and more dependable projects. Every rivet type has a particular purpose depending on the material and project demands in industrial sheet metal assembly. It is critical to select the right rivet to establish effective and permanent connections in various industries such as in automotive, aerospace, electronics, and construction. Examining the compatibility of materials and strength of joints does not only guarantee improved rivet choice but also makes the assembly process more effective.
FAQs
What Materials Can You Use to Make Rivets?
Sr. No. | Material | Properties | Common Applications |
1 | Aluminum | Lightweight, corrosion-resistant | Applications where weight is a concern |
2 | Steel | Strong, durable | Heavy-duty applications |
3 | Copper | Excellent corrosion resistance | Marine or electrical applications |
4 | Stainless Steel | Combines strength and corrosion resistance | Industries where both strength and corrosion resistance are essential |
5 | Brass | Balance of strength, corrosion resistance, and aesthetic appeal | Decorative applications |
6 | Titanium | Lightweight yet incredibly strong, high-strength, corrosion-resistant | Aerospace and high-performance environments |
Where you can employ Rivets?
Rivets are used in many industries for joining materials securely. Here’s how they’re applied in different sectors:
- Automotive Industry
- Aerospace Industry
- Electronics Industry
- Construction Industry
- Marine Industry
What are the advantages of Sheet Metal Assembly Rivets?
Benefits to join sheet metal with rivets include:
- Durability: Rivets offer a permanent, secure, fastening that can handle high stress and heavy duty applications.
- Corrosion Resistance: In severe applications, corrosion resistant alloys such as aluminum solid rivets, stainless steel, and copper are typical.
- Cost-Effective: For many applications, riveting is more affordable than welding or other fastening methods.
- No Need for Access to Both Sides: This is because blind rivets can be installed even when only one side of the material is available.
- Ease of Installation: Pneumatic or hydraulic tools make riveting fast and easy, both in time and labor.
What to Consider While Selecting Rivets?
Choosing the right rivet involves several key factors:
- Material Compatibility
- Joint Strength Requirements
- Environmental Conditions
- Industry Standards
- Installation Method and Tooling
- Aesthetic and Design Considerations
How to Remove Rivets?
Removing the rivets can be tricky but thankfully is possible if you have the right tools:
- Drilling out the center of most rivets will break the rivet and allow for the removal of the body.
- Prying the rivet apart with pliers is possible for headless rivets or softer materials.
- In some cases you would need to grind or use a cutting tool to cut through the rivet material. When doing this, be careful not to damage other surrounding materials.
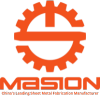