Sheet Metal Stamping – Comprehensive Guide
Sheet metal stamping refers to a change of flat metal sheets into different shapes and geometry. It has wide applications in the component manufacturing of the automotive, aerospace and even household appliances. Moreover, it has also found some applications in electronics manufacturing. So, sheet metal is one of the most important processes in making a wide range of metal parts. It is quite an accurate and cost-effective solution.
Table of Contents
ToggleSheet Metal Stamping
This article will discuss all these techniques in detail. Moreover, we will get a deep knowledge of different classifications, step-by-step processes, applications, and challenges of stamping sheet metal.
What Does Sheet Metal Stamping Mean?
The stamping process is also known as pressing. It includes placing flat sheet metals in a press and converting them into a coil or a blank. Here, a tool or die surface attain a specific shape. So, several techniques featured in this stamping process.
What is the Sheet Metal Stamping Process?
Here we will discuss how to stamp sheet metal. So, let’s discuss the process included in stamped sheet metal.
Designing
So, the first step of the stamping process is designing. We can use advance technologies, such as CAD/CAM engineering technology. So, these designs must be very accurate. They manage each punch and bend. So, it can maintain the optimum geometry of the metal part. Moreover, they must be clear for optimal part quality. Besides this, a one-tool 3D model has hundreds of parts. In this case, the design process is intricate and time-consuming.
Sheet Metal Stamping Design using CAD
Effective Designing Tips to Improve Quality of Stamping Process
Design Concept | Effective Tips for Designing | Simplified Diagram |
Blanking | So, cut the rough shape of the part, reduce, and avoid burrs to cut costs and lead times. | ![]() |
Piercing | Here, the holes and slots fully enclosed within the edges of a part. Also, consider hole diameter and geometry for proper manufacturing and functionality. | ![]() |
Bending | Design the bends with enough material and space. Moreover, consider forming near holes to avoid deformation. | ![]() |
Notches and Tabs | It includes the design with widths ~1.5x the thickness. It will avoid breakage during punching. | ![]() |
Corners | Here, its corners radius is half of the material thickness. It will avoid sharp edges. | ![]() |
Burr Reduction | Avoid sharp corners and complex cutouts. It will help in reducing burrs. Go with the burr direction during stamping. | ![]() |
Coining | Flatten or break the burrs during the stamping process to avoid costly secondary processes. | ![]() |
Plasticity & Grain Direction | Choose plasticity and grain direction for easier forming, especially for high-strength materials. | ![]() |
Bend Height | Give a sufficient bend height for effective forming, typically at least 2.5x the material thickness plus the radius of the bend. | ![]() |
Bend Relief | Design with offsets or relief notches to prevent tearing along edges during bending. | ![]() |
Bend Distortion/Bulge | Choose bending distortion or bulge by relieving parts before bending or consider the bend relief notches. | ![]() |
Countersinks | Always go with countersinking operations and potential bulges around holes to ensure proper fastening. | ![]() |
Carrying Web and Mismatch Cut | Design for mismatch cuts during progressive die stamping to avoid part damage. | ![]() |
So, after the tool design completion, the second process is manufacturing. This manufacturing is carried out using different stamped sheet metal machines and other manufacturing services. So here are the details of the process involved in stamping.
Blanking
Once you complete the design part, blanking is the first in the sheet metal stamping process. Here is the rough outline of the metal part cut from the sheet. We use a blanking die to cut the part in the required shape. So, when you are cutting the outline, make sure to reduce the burrs. Because they can have a bad impact on the final part. It can also need additional processing. Hence, the stamping die must be clear. Besides this, always use sharp tooling to get clean edges.
Blanking Process
Punching
Punching includes making holes, slots, and other features in metal sheets. We use a punch, and a die set to carry out this process. So, the punch applies force on the metal sheet and inserts it into the die cavity. Then it comes out in the desired shape. So, the hole diameter, tolerance, spacing and geometry must be in control. It will give a proper fit and effective functionality of the final part. Additionally, if we deal with complex structures and shapes. We may require specialized punches and sheet metal stamping dies.
Punching of Metal Sheet
Drawing
Drawing gives deep, cup-like shapes and hollow components. Here, we clamp the metal sheet from its edges. Then this sheet is pulled into a die cavity to get the required shape. Additionally, the drawing includes material deformation. In this case, apply adequate lubrication and choose the right material. It will help your metal to prevent wrinkling, wear-and-tear, and surface defects. Moreover, it will give you consistent forming as well.
Deep Drawing Process
Piercing
It works the same as a punching process. But it also removes the material from the perimeter without disturbing the features of the desired shape. Moreover, this process is suitable for creating holes and slots near the edge of a metal part. It prevents bulging and distortion along the part edges. So, always use a clear die and sharp tools during this process. They will lead you to the clean edge and accurate hole dimensions.
Embossing
Embossing is used to make raised or sunken features on the surface of metal parts. So, it is considered as a decorative or a functional process. It is usually achieved by pressing the sheet between the male and female die set. This allows it to get the desired pattern on the surface of the metal. So, embossing needs careful control of pressure and die geometry. It will help achieve the desired depth and clarity of the features. Moreover, material stretch and thinning should be reduced. So, you can prevent tearing and distortion.
Coining
Coining is used to produce smooth and flat surfaces. We use it for the precision forming processes of the metal sheet. So, the sheet is compressed between two dies with the optimal pressure. It results in precise dimensional accuracy and surface finish. So, coining can significantly improve part quality. It also reduces surface roughness. Moreover, it improves dimensional accuracy. So, give high pressure and precise tooling and get consistent results.
Bending
Bending is a process that helps you create bends and folds in a metal sheet. So, it is achieved if you clamp the sheet between the punch and die. Then apply a force to deform the material. This process requires careful consideration of the material, thickness, bend radius and tool geometry. This will help you prevent wrinkling, cracking and excessive wear and tear. Moreover, apply lubrication and use proper tools. So, you can achieve uniform bending and dimensional accuracy.
Flanging
It is a bending of edges of the metal sheet at an angle to create flanges of lips. So, this process is commonly used in strengthened edges. It provides stiffness. Moreover, it facilitates the assemblies. So, flanging needs precise control of bent angles. It needs optimal material thickness and die clearance. So, it can get consistent flange dimensions and geometry. Make sure to apply proper support and clamping of the sheet. So, you can prevent distortion or wrinkling during flanging.
What Material You Use for Cheap Sheet Metal Stamping Components
Here are some commonly used materials you can use for the stamping process.
Metal | Suitability | Details |
Stainless Steel | Moderate to High | Requires higher press force compared to softer metals. |
Low-Carbon Steel | High | Ductile and strong, ideal for stamping various shapes. |
High-Carbon Steel | Moderate to High | Can be stamped but may require higher press force due to increased hardness. |
Aluminum | High | Here, aluminum sheet metal stamping has a low density and high malleability. This makes it highly suitable for stamping. |
Titanium | Moderate | Requires specialized equipment and tooling but can be stamped with care. |
Brass | High | Malleable and formable, ideal for intricate stamping designs. |
Bronze | Moderate to High | May require higher press force and specialized tooling. |
Copper | Moderate to High | Can be stamped but may require higher press force and specialized tooling. |
Inconel | Moderate to High | Requires higher press force and specialized tooling due to its hardness. |
Nickel Alloys | Moderate to High | Suitable for stamping but may require higher press force and tooling. |
Types of Sheet Metal Stampings
Based on different techniques, it can be classified into the following types.
Progressive Stamping
It contains multiple features and has several stations. Each station has its duty. So,
progressive stamping is a highly automated metal working process. It is used to produce bulk of complex parts. This process includes feeding a metal strip through a series of stations. The station could be cutting, bending, shaping curling, etc. So, this strip starts to move through the press. Then move to the next station. Each station sequentially performs some tasks. So, when the final part comes, it is the combination of multiple operations. So, it is efficient for high-volume productions. Moreover, it reduces the need for manual handling between operations.
Fourslide Stamping
This process is used to produce complex but small to medium-sized parts. These parts can have complex shapes. So, this process includes the use of a four-slide machine. This machine has four slides or tooling mechanisms to perform multiple operations. So, these four slide machines can bend, punch and form metal into different shapes. This combination of multitasking makes it a versatile process. It gives different components like clips, brackets and electrical contacts. Moreover, the main advantage of this process is that it produces parts with complex bends and angles. So, it can achieve tight tolerance and reduce the need for secondary operations.
Deep Drawing
Deep drawing helps you produce cylindrical or box-shaped components. These components can have greater depth than their diameter. So, during this process, you place a flat metal sheet or a blank in a die cavity and use a punch to draw the blank in the die. Then you apply force on it to take the shape of the cavity. You can perform this process in multiple stages. Each stage increment deepens the drawn part until you get the required shape. Deep drowning is used in parts production, like cans, containers, automotive body panels, kitchen sinks, etc, it serves metals with high strength and tight dimensional torrents. Moreover, this process is quite beneficial because of material savings, reduced weight and the ability to create smooth and complex geometries.
Transfer Die Stamping
It works like progressive stamping, as a metal strip is usually transferred from one station to another. But it uses mechanical or pneumatic transfer systems. Moreover, It can progressively produce more complex parts, and maintain high efficiency and precision stamped sheet metal is more suitable for parts with complex shapes and features, that we cannot achieve with a single stock.
Fine blanking
It is also known as fine-edge blanking. It is a precise metal stemming process which is used to produce high-quality parts, clean edges, and tight tolerance. Moreover, it uses special tools that apply three separate forces to the metal blank, i.e. cutting plank holding and counter pressure. So, this results in a smooth touch finish. It reduces the need for secondary operations Like deburring or machining.
Shortened Stamping
If we talk about shortened stamping, it refers to the production of small batches. of stamp parts. Generally, it can produce a few hundred to thousands of pieces. Moreover, it is often used for prototyping product testing and fulfilling orders with low demand. Then frequent design changes. Sure. runs stamping may include. different techniques. but they are optimized for flexibility, quickness, and setup. They are quite cost-effective for smaller production volumes. So, the tooling and stamping sheet metal equipment must be designed to accommodate frequent changeovers. They must adapt themselves to the adjustments to meet varying production needs.
What are the Classifications of Metal Stamping Based on Processes
It is classified into two processes, i.e. forming and Material Separation. So, let’s discuss these in detail with their simplified drawings.
Category | Process | Process Description | Simplified Drawings |
Material Separation | Punching | Use a mold to punch out the sheet along the closed line, resulting in workpieces and scraps. | ![]() |
Blanking | Use a mold to punch out the plate along the closed line, resulting in workpieces and scrap. | ![]() | |
Shearing | Cut off excess material from the edge of semi-finished products. | ![]() | |
Forming | Bending | Use molds to bend materials into shapes. | ![]() |
Curling | Round the ends of the sheet. | ![]() | |
Twisting | Twist one part of the flat blank at an angle relative to another part. | ||
Drawing | Press sheet material into a hollow workpiece while maintaining wall thickness. | ![]() | |
Stretching | Change the size of the hollow part to achieve required dimensions. | ||
Flanging | Turn the holed edge of a sheet or workpiece into an upright edge. | ![]() | |
Hemming | Flange the outer edge of the workpiece. | ![]() |
What are the Tolerances for Stamped Sheet Metal
Tolerance helps in the precision of the stamping process? It is the allowable variance in dimensions and shapes. So, several factors influence the precision of stamping. It could be thickness, the complexity of dies and diameter, etc. So, let’s discuss the different tolerance values of stamped Metal Sheets.
Dimension | Tolerance Range | Details |
Linear Dimensions | ±0.05 mm to ±0.25 mm (±0.002 in to ±0.010 in) | Depending on part size, complexity, and material. |
Hole Diameter | ±0.05 mm to ±0.15 mm (±0.002 in to ±0.006 in) | Diameter may vary based on hole size and depth. |
Thickness | ±0.05 mm to ±0.10 mm (±0.002 in to ±0.004 in) | Material thickness consistency is crucial. |
Angle | ±1° to ±3° | Can vary based on bending or forming operations. |
Form Features (e.g., bends) | ±0.25 mm to ±0.50 mm (±0.010 in to ±0.020 in) | Depends on the complexity and geometry of the form. |
Hole-to-Hole Distance | ±0.25 mm to ±0.50 mm (±0.010 in to ±0.020 in) | Critical for assemblies and fit with other parts. |
Edge-to-Hole Distance | ±0.25 mm to ±0.50 mm (±0.010 in to ±0.020 in) | Ensures proper clearance and alignment. |
Edge-to-Edge Distance | ±0.25 mm to ±0.50 mm (±0.010 in to ±0.020 in) | Critical for maintaining part geometry and fit. |
Tolerance Values for the Stamping Process
How to Select a Machine for Stamping Sheet Metal Parts
When it comes to machine selection for the stamping process, you must consider the following aspects first.
- Efficient and Reliable Machine: Always select an efficient and reliable machine. Several brands have good reputations, so you must choose their machines. Moreover, you can check their consistent performance and choose the one that requires less maintenance.
- Effective Tooling System: The selection of a tooling system is also important. Because high-quality tooling gives optimal results. It is specifically designed to make different parts, with different materials. Thus, it improves the quality and efficiency of your production.
Common Custom Sheet Metal Stamping Type Problems, their Reasons and Solution
Types | Problems | Reasons | Solutions |
Blanking | Bug Segment | Chips cutting, improper feeding, small gap, no/st volatile stamping oil, precision/wear issues, long knife-edge punch, worn guidepost/sleeve, close punch causing material to pull. | Monitor feed port limit, adjust gap for accuracy, regulate oil; replace/grind, redesign drawing, replace/reassemble model, and ensure proper punching length, respectively. |
Rough Edges | Punch edge worn or chipped, Gap too large, Unreasonable gap, Upper and lower positions misaligned | Grind, control part accuracy, or modify design clearances, Check knife edge frame, adjust gap, replace mold guide bushing, or reassemble mold. | |
Jumping Crumbs | Large gap, Excessive stamping oil, Simple punching shape with a sharp blade, Improper feeding, no demagnetization after grinding. | Control accuracy/design for large gaps, manage oil for stamping, adjust blade/grinding, enhance surface, Address feeding, Grind/demagnetize carefully. | |
Chip Blocking | Large blanking hole, Worn punch edge with burrs, Fast dripping/sticky oil, rough knife edge, Softer copper, Small blanking area. | Reduce blanking hole, Grind punch edge, Control oil volume, Polish punch, modify punching clearance, and use a vacuum for ventilation slots. | |
Extrusion | PITCH variation, fan-shaped material/burrs, small positioning hole, rough stripping, feeder-mould distance, chips jumping, guide plate | Repair feeder, control quality, grind punch, check parts/springs, adjust distance, scraping, modify guide. | |
Cutting Size | Worn blade punch, improper clearance, misaligned dies, feeder/mold mis adjustment, worn stripping inlet, excessive pressure. | Grind punch, modify the design, adjust position, readjust feeder/mold, grind/replace inlet, adjust pressure. | |
900 molding | 900 is too big, too small | Worn parts, incorrect size, faulty molding gap. | Check part height, assess molding surface wear, and ensure upper/lower mold R angles match. |
Cracks at bends | Abnormal materials, rough parts, small gaps. | Abnormal materials, rough parts, small gaps. | |
mold mark, an imprint | Parts higher than the datum plane, scraps stuck. | Add adjustment station. | |
Dimensional instability | Large mold closing gap, loose parts. | Adjust molding gap and add pre-folded V lines. | |
R angle molding | Bellow size NG | NG or damaged part size, large mold closing gap. | Replace worn R-angle-forming parts and add or remove gaskets. |
Crack | Abnormal materials, rough parts, small gaps. | Polish molded parts R angle, check to form a gap and material punching oil. | |
General angle forming | AngleNG | Damaged part or NG size, large mold closing gap. | Check for worn angle molding parts, replace spare parts, add or subtract gaskets, and ensure the part angle matches the drawing. |
The angle size is unstable | NG bending point position. | Check positioning wear and inspect material and mold interference on individual terminals. | |
High and low PIN | The low height of molded parts, worn parts, and loose/broken adjustment springs. | Check the punch adjustment ratio, ensure the adjustment rod is firmly fixed, and inspect springs force. | |
U molding | V type size NG | NG or damaged part size. | Check for worn upper and lower mold parts, replace them with new ones, or add/remove gaskets. |
V-shaped height difference | Worn or loose molded adjustment rod, soft or broken spring skin. | Check for a simultaneous shift of upper and lower mold inserts in a U-height direction. | |
V-shaped size is unstable | NG feeder size (feed length). | Also, check the feeder PITCH. | |
V-shaped oblique opening | NG molding gap. | Check positioning wear and spare parts wear. | |
V-shaped symmetrical NG | Molding gap NG | Check for excessively large adjustment ratios, broken springs, and worn adjustment rods. | |
Bump forming | Bump size NG | Worn, broken, or insufficiently spaced parts. | Check for worn bump molding insert and consider replacing or adding/removing gaskets. |
Bump cracked | Part molding size too high, NG gap, abnormal material. | If bump breaks, replace with new one. | |
Puncture forming | Tin pin height dimension NG | Worn or broken parts. | Add or subtract gaskets from molded insert and replace with new parts if worn. |
Tin needle bending cracks | NG part size, rough surface, loose positioning pin, worn parts. | Polish and bend the R-angle and pierce the preformed punch to trim the R-angle. | |
Tin pin size is unstable | Soft or broken spring skin, NG gap, abnormal material. | Check puncture gap, regularly replace float spring and top material, and grind puncture punch blade if worn. | |
Tin pin alignment NG | Soft or broken spring skin, NG gap, abnormal material. | Replace with new parts. | |
Tin pin high and low PIN | Soft or broken spring skin, NG gap, abnormal material. | Check if the bending angle of the tin needle into the molding is too large and adjust to a smaller angle. | |
Exterior | metallic line | Worn punch and blade, improper blanking gap, loose inserts, misplaced and scratched parts, no punching oil, rough parts, unreasonable molding gap, flawed cutting design, large burrs in incoming material. | Grind or replace punch and blade, adjust blanking gap, replace loose inserts, grind misplaced parts, add punching oil, polish parts, enlarge molding gap, redesign cutting stations, and control incoming material edges strictly. |
distortion | Punch and blade wear, uneven knife edge or molded parts, large tape burrs, unreasonable design layout, worn round hole punch, faulty positioning pin tape, excessive stress in incoming material without trimmed edges, lack of punching oil. | Grind punch and knife edge, reinstall blade or molded part, grind edge trimming punch and knife edge, change layout station, grind round hole punch, and knife edge, replace positioning pin or adjust feeder and PITCH, increase trimming or replace incoming materials, add punching oil. | |
Dust | Punch collapse, inaccurate positioning, over-cutting, worn round hole punch, scratched knife edge, roughly molded parts, lack of punching oil, large burrs. | Grind or replace blanking punch, check feeder type and PITCH, change blanking station, ground punch and knife edge, polish knife edge, polish molded parts and enlarge the gap, fill the tank with punching oil, offset knife edge clearance and grind blanking punch. | |
sector | Round hole punch wear, inaccurate positioning, unstable molding, uneven knife edge or high molded part, lack of punching oil, belt crushing, large burrs on tape, mold design without trimming. | Grind punch and knife edge, check feeder PITCH and positioning pin, inspect press materials, and formed parts, reinstall blade or formed part, add punching oil, investigate the cause of belt crushing, grind the cutting edge of the cutting punch, add a trimming station or positioning. |
Analysis of Common Defects and Causes of Stamping Parts
There are certain defects and their causes associated with stamping parts. So, let’s discuss them here.
- Burr: This defect is because of the clearance issues, blunt blades, improper stamping status, and improper mold structure. It can be improved by manufacturing. Make sure that your blades are sharp: Moreover, you have maintained the stamping status.
- Wrapped Parts: This is because of large stamping gaps, reverse taper and die holes or structural shape of the parts. It can be cured by adjusting the stamping gaps, improving die-hole designs, or increasing the material handling.
- Poor dimensional accuracy: This is because of the tolerance issues in the mold cutting edge spring bags, poor board shapes and improper adjustment in multi-process parts. So, it can be fixed by the control spring back and maintaining the proper shape, accurate mold manufacturing, proper board shape and adjusting processes accurately.
Analysis of Common Defects and Causes of Bent Parts:
Here are the certain defects and causes of bent parts.
- Shape and Size Mismatch: It occurs due to proper positioning and material plasticity. So, you can reduce it by using a spring bag. Moreover, you can improve back positioning and use a suitable material property.
- Bending Cracks: These are due to material issues and improper bending angles. You can cure it by using suitable materials. So, maintain proper radius and the good blank quality.
- Surface scratches: It is due to material and mould issues, insufficient hardness, or poor finish. So, you can fix it by improving material and mold quality. Moreover, you can also increase heat treatment and good finish as well.
- Deflection and Distortion: Various factors like airflow, pressure and stress distribution contribute to this issue. So, you can solve it by proper blank, using appropriate equipment and maintaining sufficient material stiffness.
Analysis of Common Defects and Causes of Large Curved Surface Drawn Parts
Here are the common defects and causes of large curve surface drawn parts.
- Deformation Properties: This is due to forces associated with the die and blank holder. So, you can fix this issue by applying different forces.
- Common defects: There are defects, like tensile stress issues, material thickness and lubrication. You can check the material and process issues and improve the lubrication quality.
Applications of Stamping Sheet Metal
stamped sheet metal has found a range of applications in different industries. These industries mainly include automotive, aerospace, electronics, household appliances and more. In the automotive manufacturing process, it helps to make the components like body panels, and bracket structure cards. Moreover, in aerospace, it is used to create complex parts like airframes, and engine mounts. So, it is very strict towards quality and performance standards. Moreover, in electronics, it is used to make the components such as connectors, heat sinks and complex parts. So, it is serving different industries because it is a very cost-effective and efficient manufacturing solution.
Advantages of the Stamping Process
So, here are some advantages of metal stamping.
- Cost Effective: When it comes to high-volume productions, it is highly cost-effective. It provides a rapid production rate with less labour cost per part. Moreover, it can use coil or strip metal stock. It minimizes material waste and improves cost efficiency.
- High Precision: The metal stamping process can help us achieve high tolerance with a high level of precision. Moreover, it gives consistent quality across large production runs. This precision is very important for industries like automotive, aerospace, electronics and where tight dimensional control is necessary.
- Versatility: It can adjust a wide range of materials. These materials can be stamped steel, aluminium, copper, and various alloys. Moreover, it can also produce complex shapes and features. So, it is a very suitable solution for the diverse range of applications across industries.
- High speed and efficiency: It is highly automated. So, it allows fast production rates and high throughputs. Moreover, it can perform multiple operations in a single stock. It increases the efficiency of this process.
- Scalability: It is easily scalable. So, it is suitable for both small and large production runs. Moreover, here tooling cost can be amortized over large quantities. This reduces per-part cost and gives high-volume orders.
- Design flexibilities: It offers significant design flexibilities because it can create complex parts with multiple features in a single operation. Moreover, it also allows engineers to maximize part designs for functionality, performance, and cost-effectiveness.
- Reduce secondary operations: This process requires minimal or no security operations like deburring or machining. So, this is a very precise and clean process. It also reduces production time and cost which is associated with additional processing steps.
Limitations of Metal Sheet Stamping
As every rose has thrones. Similarly, where stamped metal sheets provides us with different advantages. It has some limitations as well.
- Making specific tools is expensive for complex shapes or small production runs.
- Some designs are hard to make with stamping because of their shift in complexity.
- A few materials might crack or break during the process. So, it can lead to waste and extra work.
- Getting the right size is also a bit tricky in stamping. Even if it makes things very precise. But sometimes small errors in size can occur during tooling.
- Poor surface finishing also increases the operation requirements. So, it ultimately increases the production cost.
Alternatives for Sheet Metal Stamping Process
There are several alternatives to stamping sheet metal, such as;
Alternative Process | Process Description | Applications |
Machining | It includes cutting away material from a solid block and making a desired shape. | Prototyping, custom parts manufacturing, high-precision components |
Casting | Here molten metal is poured into a mold to form the part. Then it solidifies and takes the shape of the mold. | Automotive parts, aerospace components, jewellery making |
Forging | It needs heat and pressure to shape the metal into the desired form. | Automotive components, hand tools, industrial machinery |
3D Printing | It makes parts layer by layer from a digital design. | Prototyping, custom parts manufacturing, medical implants |
Laser Cutting | Here it uses a focused laser beam to cut through sheet metal. | Metal signage, architectural components, electronic enclosures |
Electrochemical Machining | Here, it uses electrolysis and selectively removes material from a conductive workpiece. | Aerospace components, medical devices, electronics |
Hydroforming | It applies fluid pressure to deform metal sheets into the desired shape. | Automotive body panels, kitchen appliances, bicycle frames |
Why Choose Us for Stamping?
If you need customers stamped sheet metal projects, choose Masion. Because we are offering extensive services based on your requirements. We have experienced staff with advanced technologies and customized solutions. We can provide quality assurance and 100% commitment. With years of expertise and top-notch equipment, we are getting exceptional results based on customer requirements. So, if you need custom sheet metal stamping, don’t go anywhere. Just trust us to provide precision, efficiency, and reliability. We will guarantee your satisfaction and build a lost partnership based on trust and quality.
Conclusion
In conclusion, sheet metal stamping is a cost-effective solution for bulk production runs. It minimizes the operational cost. It has wide applications in large and even small industries, such as electronic industries, aerospace, automotive and marine. Thus, it offers a range of benefits. Despite its limitations, it is significantly important for batch production of metal parts.
Frequently Asked Questions
Q1. How thick can metal sheets be for metal stamping?
It generally ranges between 0.001 – 0.625 inches. While few can even use around 3 inches.
Q2. How to define hamming in sheet metals?
It can be defined as folding the edges over itself or bending over itself at 180 degrees. It is done with tools like press brakes. So, the metal can bend neatly.
Q3. Which material is preferable for sheet metal stampings?
Copper is preferred because it is highly conductive and has good corrosion resistance. Moreover, it is excessive, cheap, and ductile. So, it can bend into complex shapes.
Q4. how to specify sanding sheet metal before stamping?
You can specify it by using fine-grit sandpaper. It will remove imperfections and. make a smooth finish before stamping.
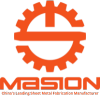
Send Your Inquiry Today



+86-18969433502

sales@sheetmetalmasion.com