Factory and Machinery - China Manufacturer - Sheet Metal Fabrication Factory
Masion is one of the best sheet metal fabrication factory with 6 sheet metal production and processing plants in Ningbo. Our manufacturing site area is comprised of 30,000 sq mt. and over 400 employees are working in it. Besides this, our facility is equipped with advanced equipment to cater to your all manufacturing needs.
Masion has a vertically integrated in-house production. It helps us participate in the design, manufacturing, surface treatment, and assembly. Besides this, this in-house production facility helps us in testing sheet metal parts. We can get higher production efficiency at lower costs. Our experts are specialized in achieving faster delivery times with high precision.



+86-18969433502

sales@sheetmetalmasion.com
Masion - Your Premier Solution For All Sheet Metal Manufacturing Needs
Masion is supported by advanced sheet metal manufacturing machinery, a skilled R&D and production group. We’re experts with an excellent ERP production supply chain management system. So, it is possible to go through high precision, complicated sheet metal parts production with quick turnaround time, and a competitive edge.
Our sheet metal manufacturing services are developed with the help of experience and the trust of our valuable customers. Additionally, we are providing value to the clients and addressing their issues. Also, Masion has high-quality equipment and we have a geek awareness of trends, products, and updates of new technologies. So, let’s discover how we can deliver value, and multiple services to our customers, Besides this, we will allow you to become a market leader as soon as possible.
Our Machines
Masion’s span is 30,000 sq. mt. along with the 6 production buildings. They all are equipped with advanced, efficient, and high-precision, automated machines. So, we’re experts in providing highly advanced sheet metal manufacturing processes to cater to your all needs.
Explore Our Machines

- Standard Sheet Metal Manufacturing: We guarantee high-quality production and always give full attention to every detail.
- DFM Support: Our experts help you with design and production.
- Custom Manufacturing: Masion believes in providing high-quality manufacturing depending on your designs.
- Unmatched Production: We guarantee meeting all the high standards in making your sheet metal parts.
- Fewer Lead Times: We deliver to you on time. So, we provide fast market entry to reduce your cost.
- Strict Quality Control: Our experts provide you with strict high-quality inspection to guarantee high-quality.
- Cost Optimization: We have all in-house production units to Streamline the processes and manage costs.
- Production Tracking: We assure you with high visibility along with in-time delivery.
These features help us in providing efficient, cost-effective, and high-quality sheet metal manufacturing solutions to meet your all demands
What we are experts in?

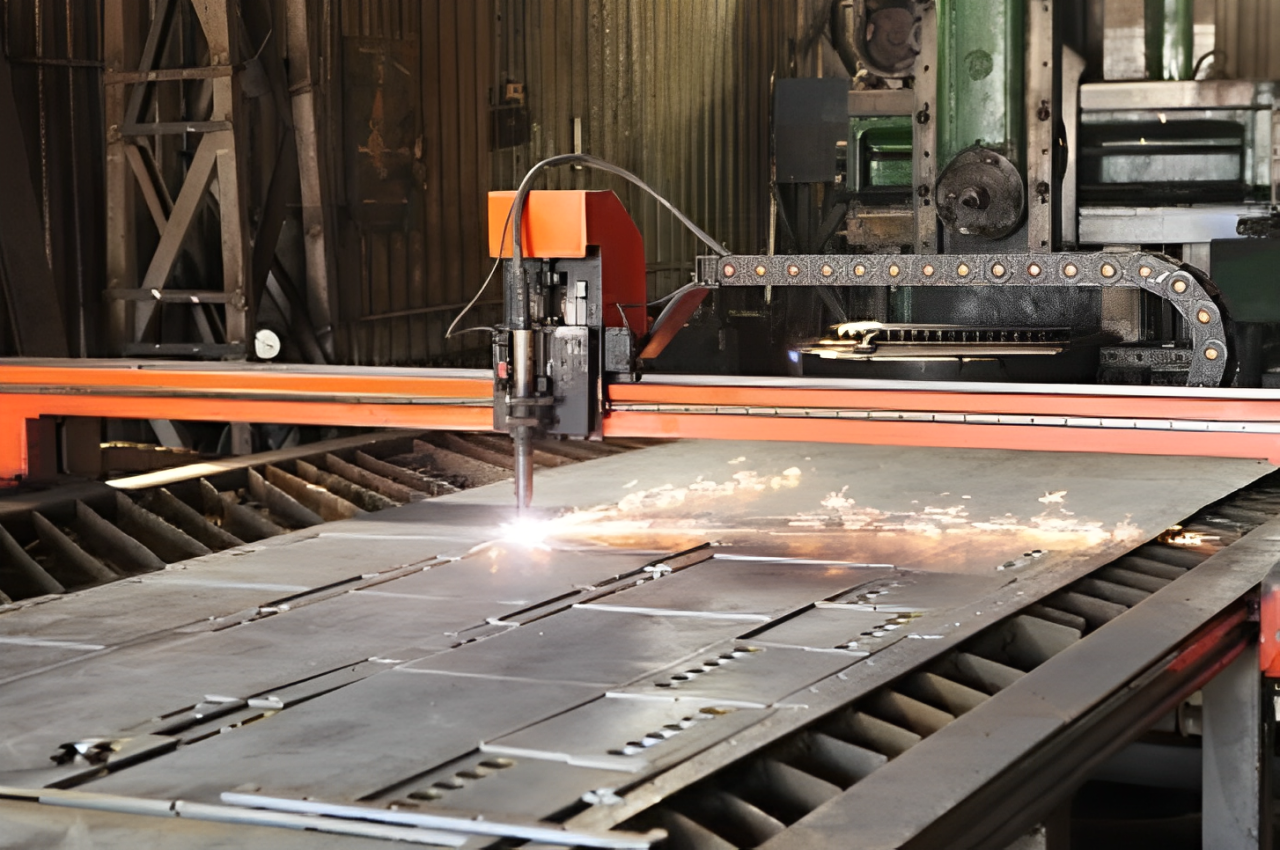
Range Of Options For Machines For Sheet Metal Manufacturing

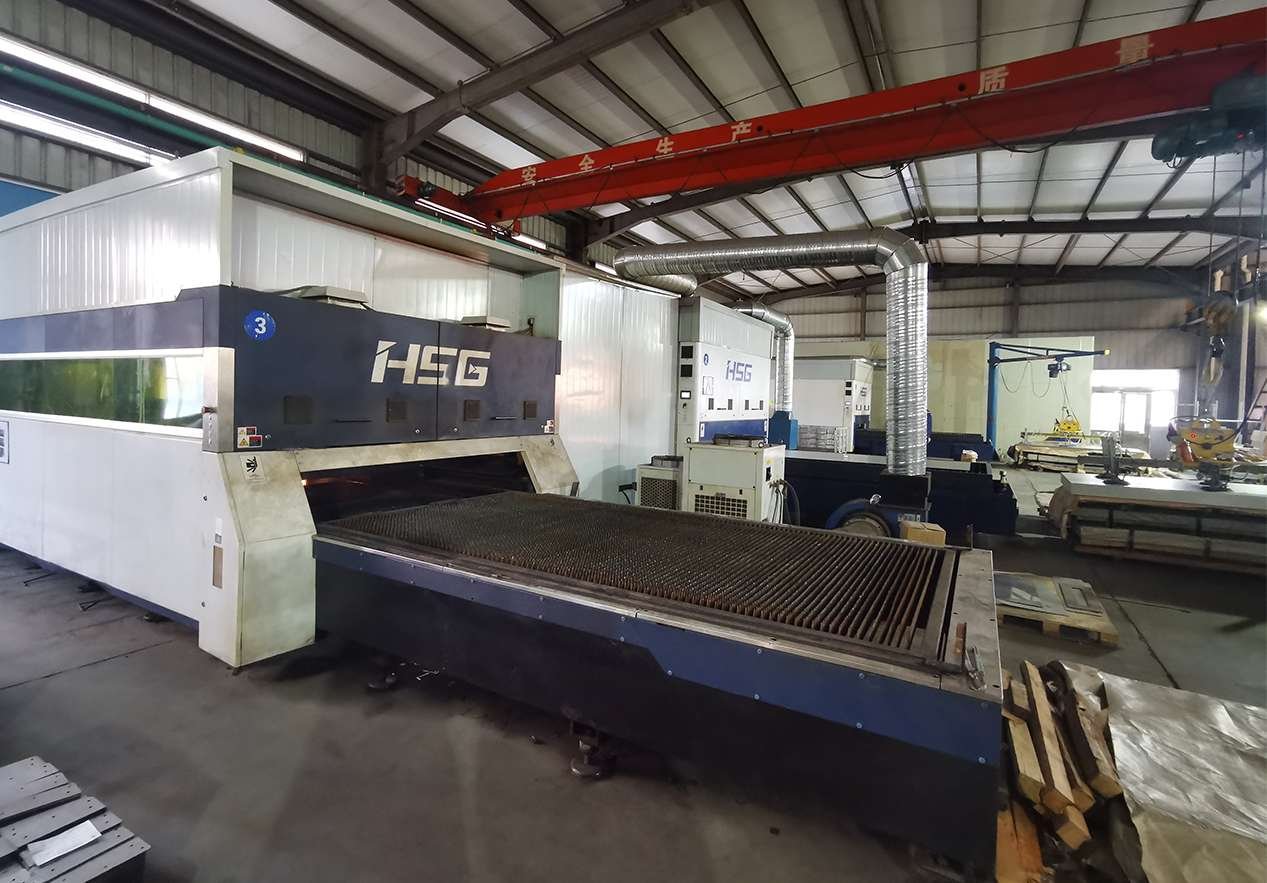
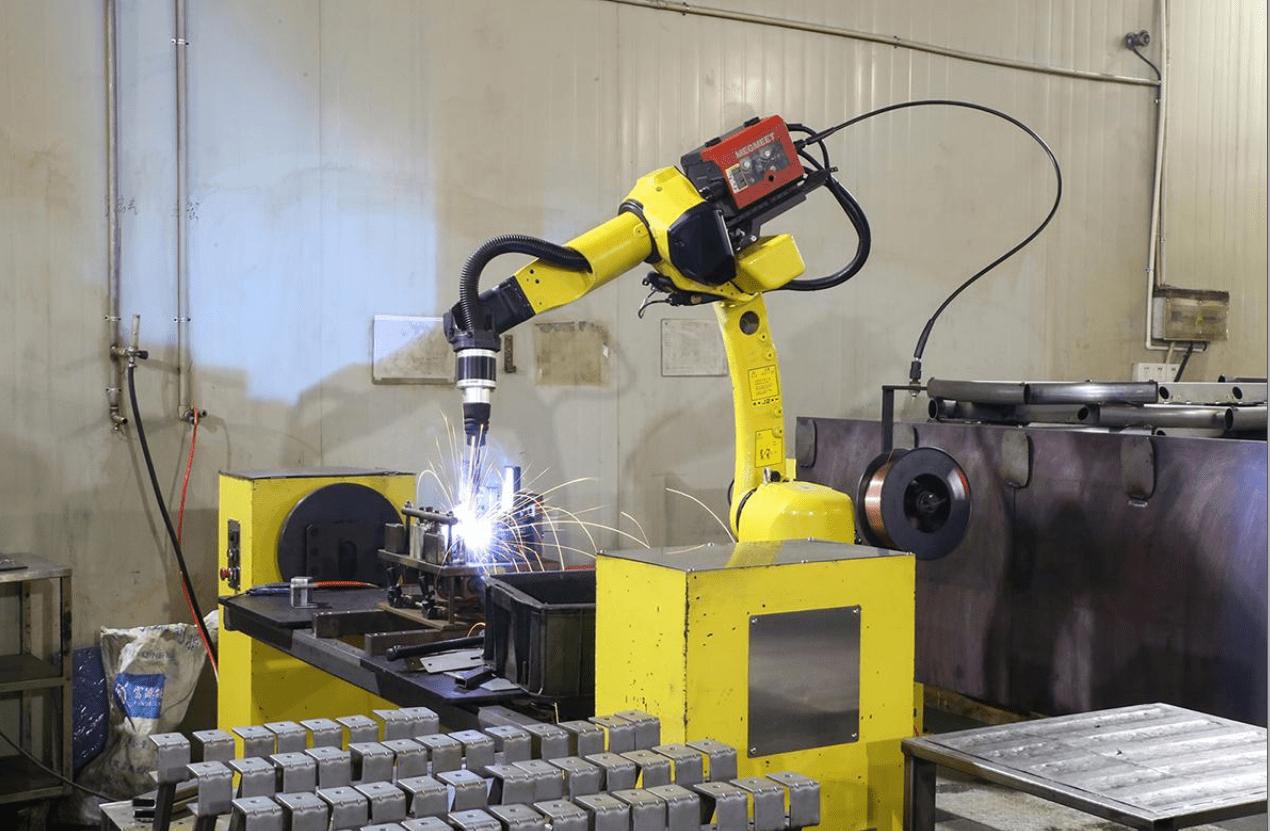
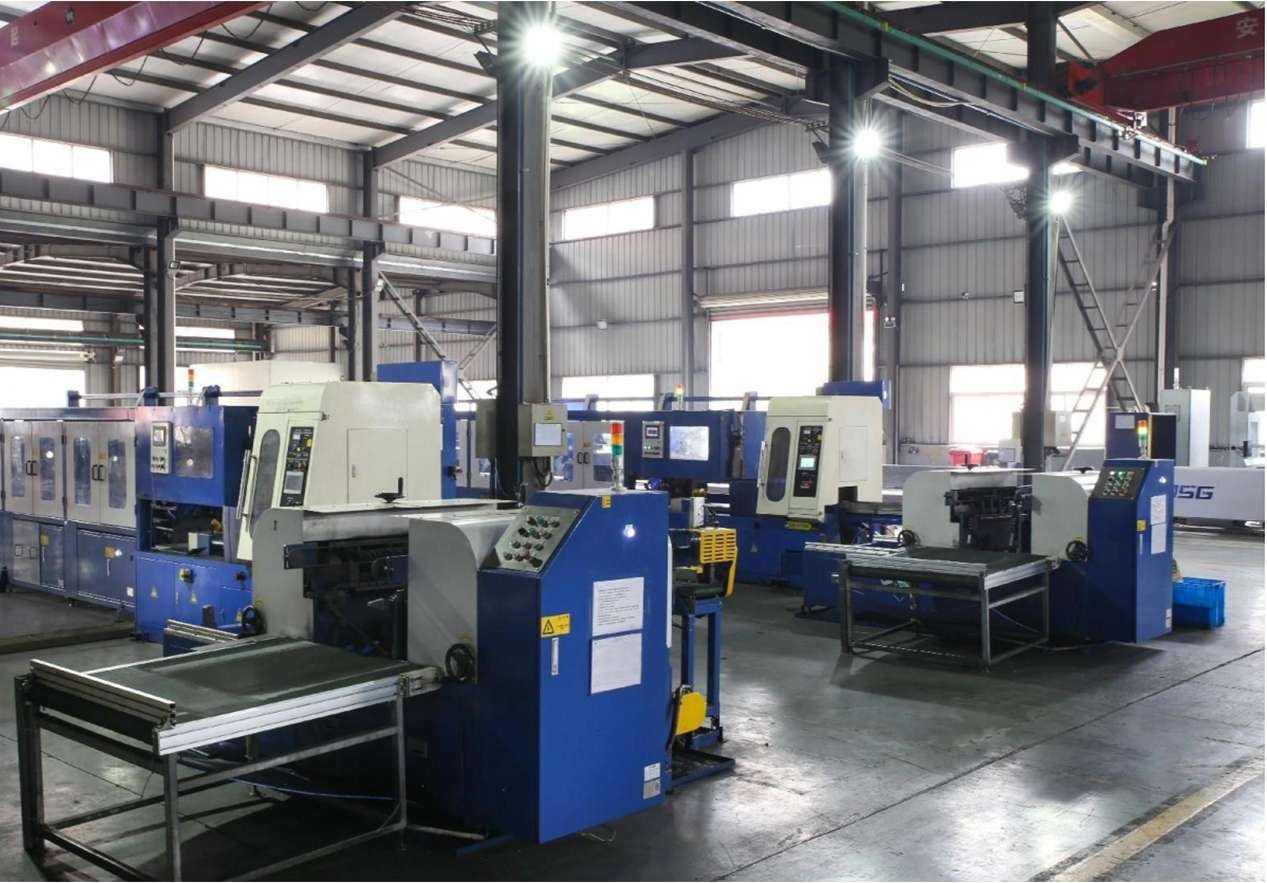
Machines for Stamping Press
- 500T Press: 1 unit
- 400T Press: 5 units
- 250T Press: 1 unit
- 200T Press: 12 units
- 160T Press: 10 units
- 110T Press: 25 units
- 80T Press: 14 units
- 60T Press: 3 units
- 45T Press: 2 units
- Hydraulic Presses: 2 units
- Robot Automatic Feeders: 20 units
Machines for Sheet Metal Fabrication
- HSG 3000W Laser Cutting Machine
- HSG 6000W Laser Cutting Machine
- Yawei CNC Sheet Bending 110T 3+1 axis
- Yawei CNC Sheet Bending 63T 3-axis
- CNC Sheet Metal Drilling & Threading
- Chamfering Machine
Machines used for Welding
- YASKAWA / FANUC / PANASONIC Welding Robots
- Laser Welding 3000W
- AC/DC Inverter Welding Machines
- TIG Welding Machines
- Gas Shielded Welding Machines
Machines for Metal Tube Manufacturing
- 3 sets HS-TS65 Laser Tube Cutting Machines 3000W
- 4 sets of Fully Automatic Tube Cutting Machines
- 2 sets Angle Tube Cutting Machines
- Deburring Machines
- Pipe Bending Machines
- Punch Presses
- Diameter Reduction Equipment
- CNC Pipe Bending M
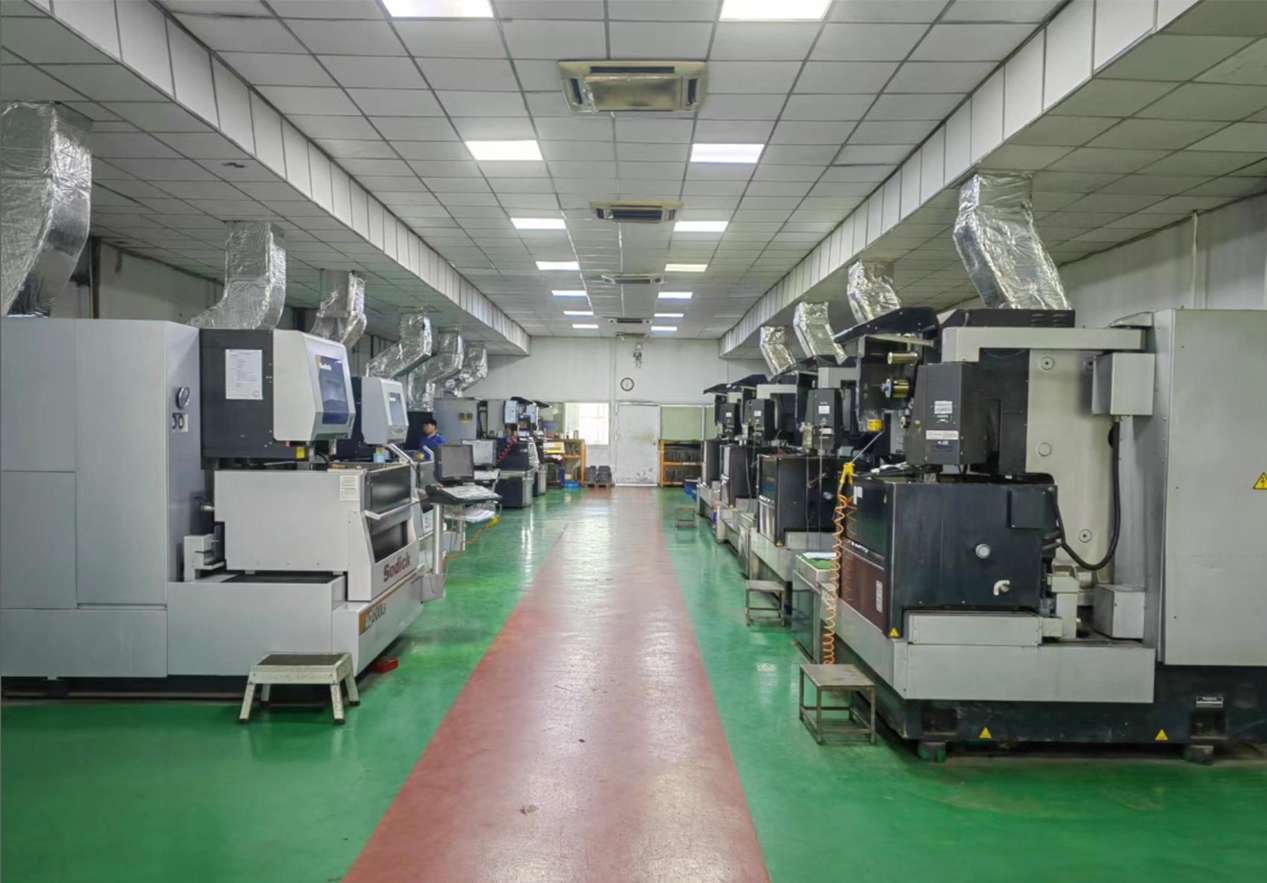

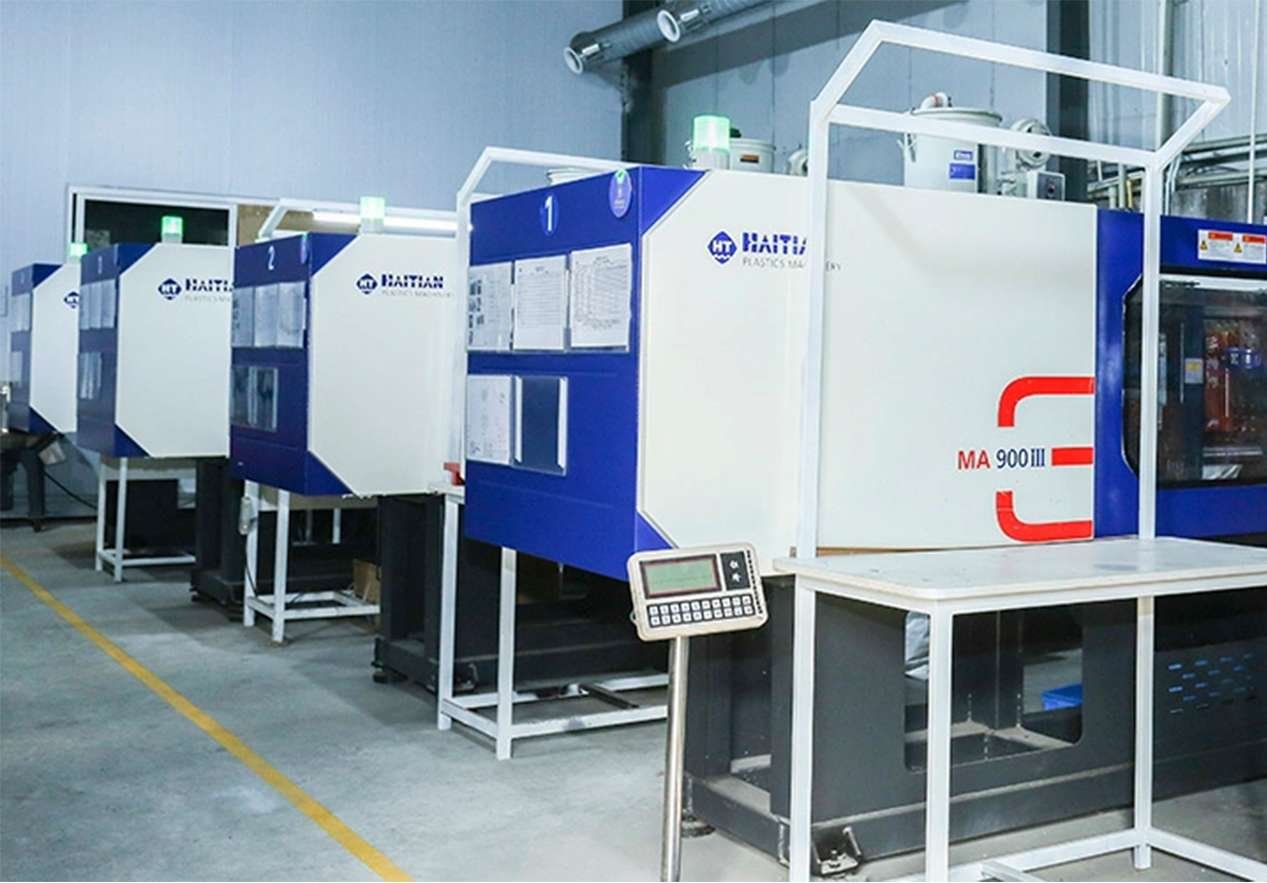
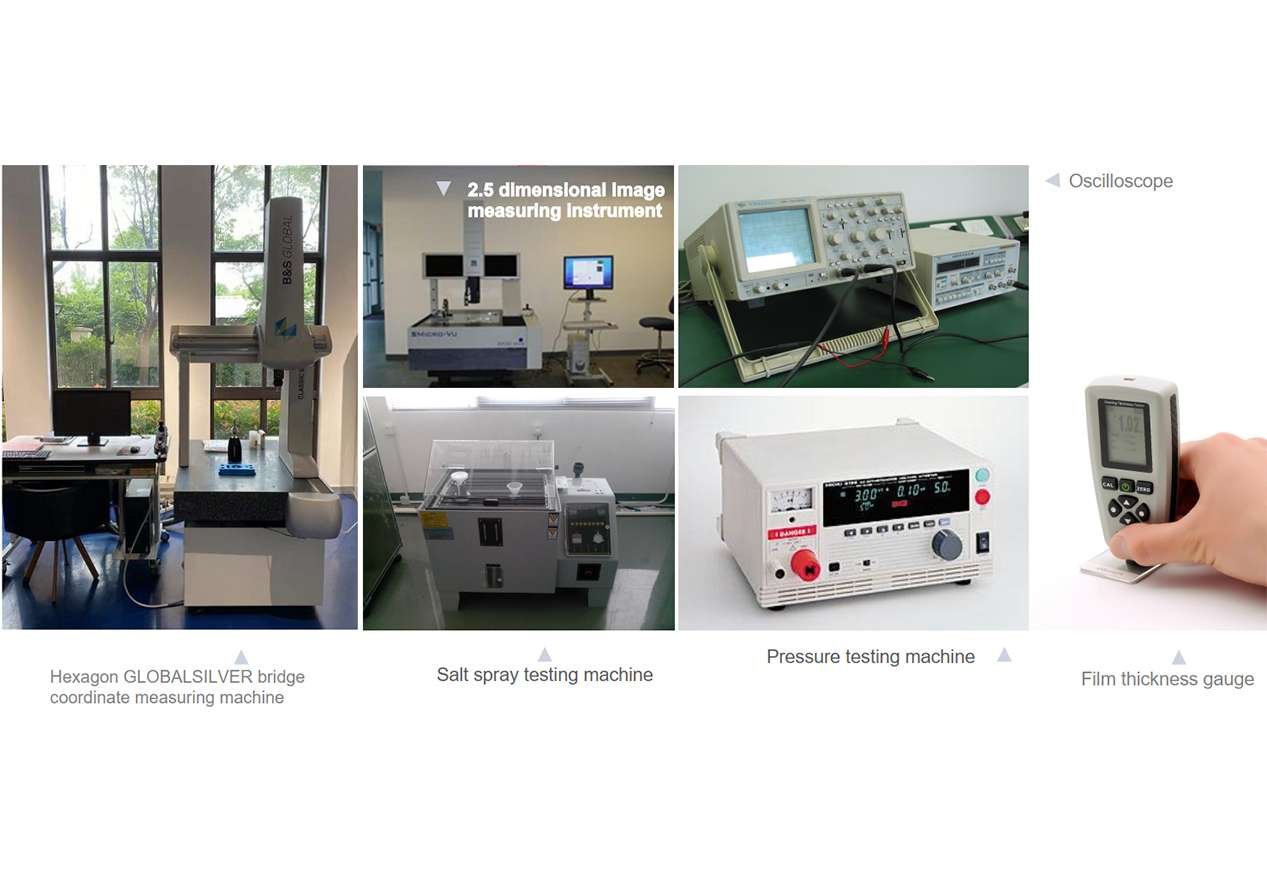
Machines used for Stamping Die Manufacturing
- Precision Surface Grinder
- Large Surface Grinding Machine
- Wire EDM Machine (Slow Speed)
- CNC Machining Center
- Milling Machine
Machines used for Sheet Metal Assembly
- Automated Assembly Conveyor
- Automated Assembly Plate Conveyor
- Fixed Assembly Workstation
- Riveting Machine (PEM)
- Bolt Welding Machine
- Fixed Assembly Workstation
- Press Riveting Machine
- Standalone 4E Riveting Machine
Machines used for Plastic Injection
- Plastic injection machine 90T
- Plastic injection machine 120T
- Plastic injection machine 200T
- Plastic injection machine 300
- Plastic injection machine 500T
Machines used for Sheet Metal Inspection
- Hexagon GLOBAL SILVER
- Bridge-Type Coordinate Measuring Machine
- 5D Video Measuring System
- Salt Spray Tester
- Pressure Testing Machine
- Coating Thickness Gauge
- Oscilloscope
- Custom Inspection Fixtures
Explore Our Precision Sheet Metal Fabrication Equipment
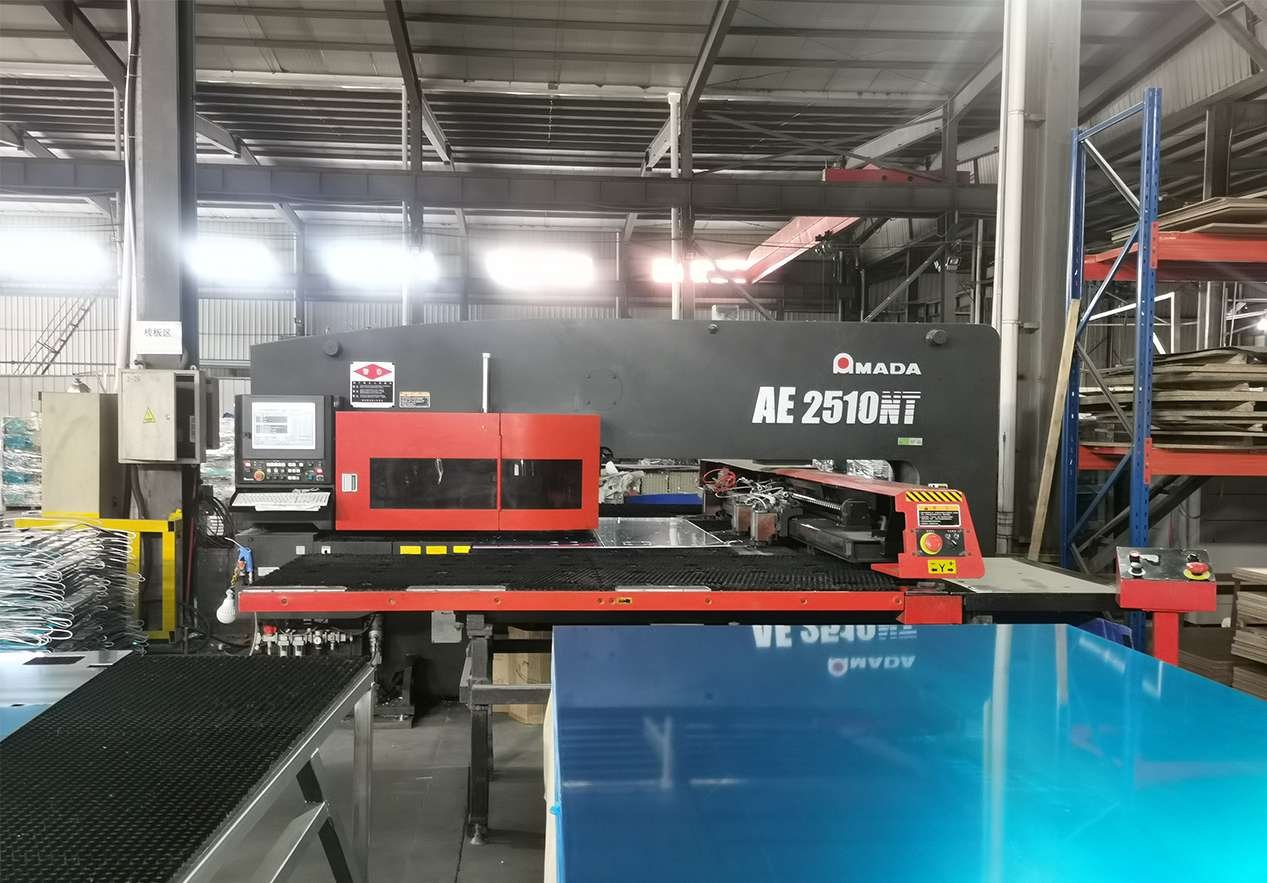
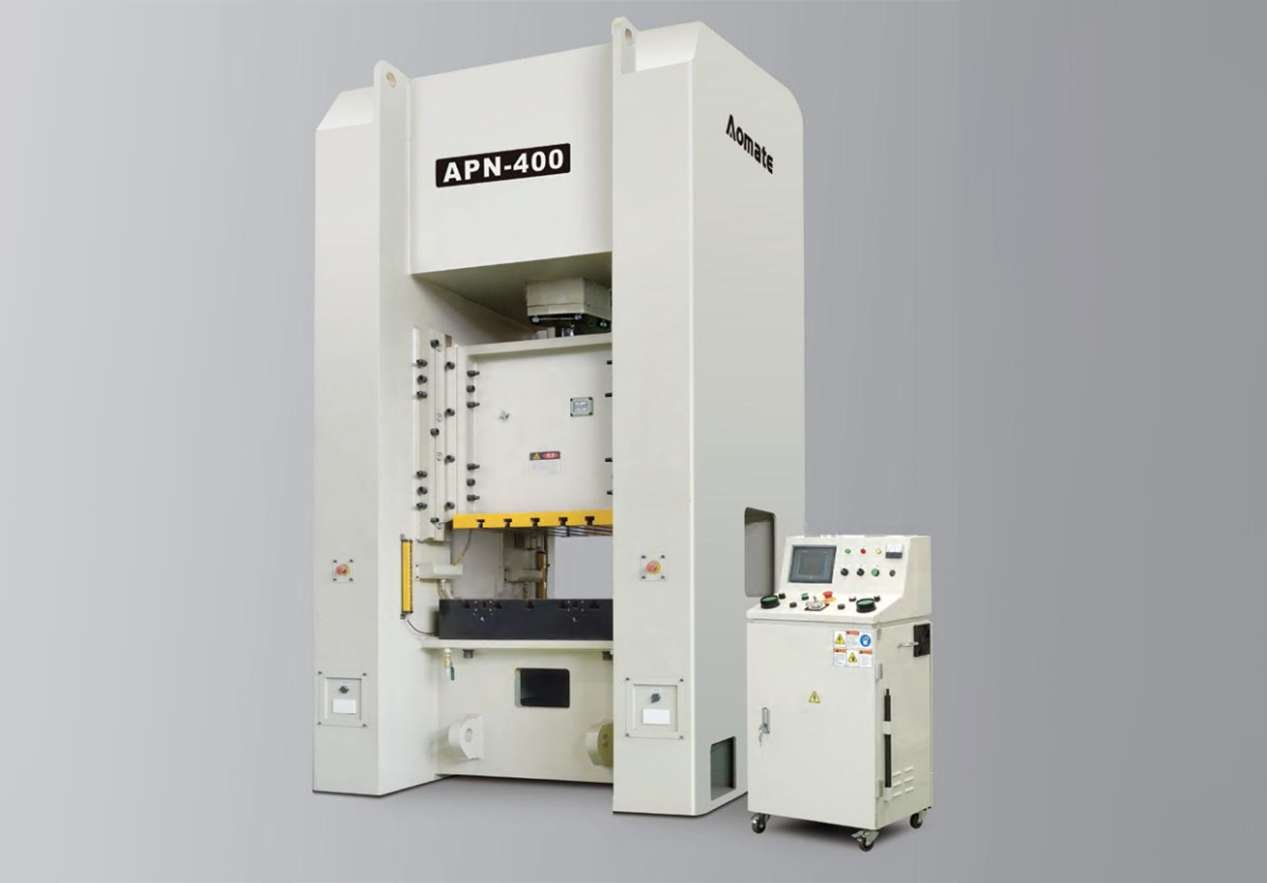
NCT Turret Punch Press
- Speed: X-axis 100m/min, Y-axis 80m/min
- Precision: ±0.1mm
- Range: 2500*1250mm
- Maximum Sheet Thickness: 2mm
- Punching Force:47 tons
400T Press
- Maximum punch force: 400 tons
- Stroke length: 300mm
- Maximum slider stroke: 200mm
- Punch adjustment stroke: 100mm
- Punch adjustment speed: 10mm/s
- Punch stroke count: 20-60 strokes/min
- Punch precision: GB/JS class 1
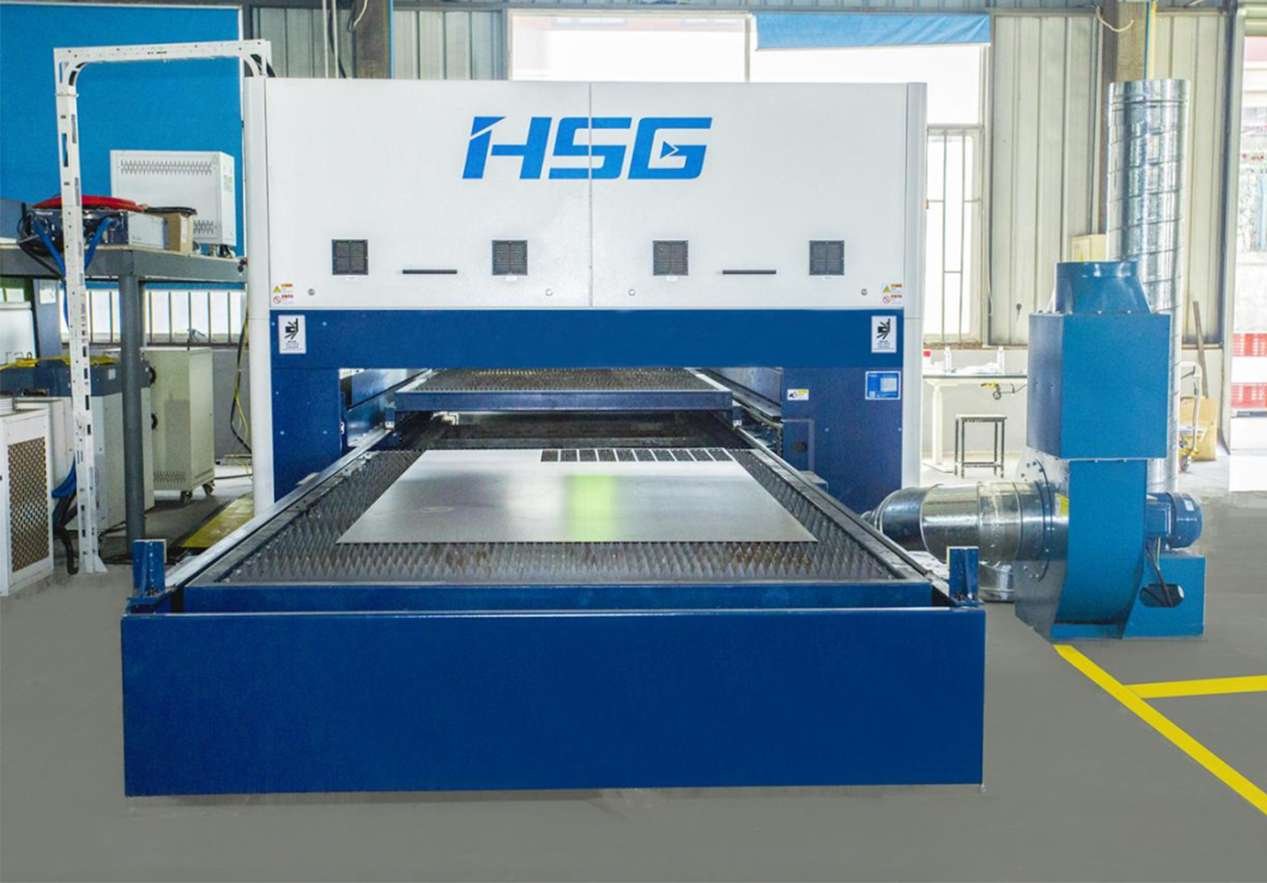
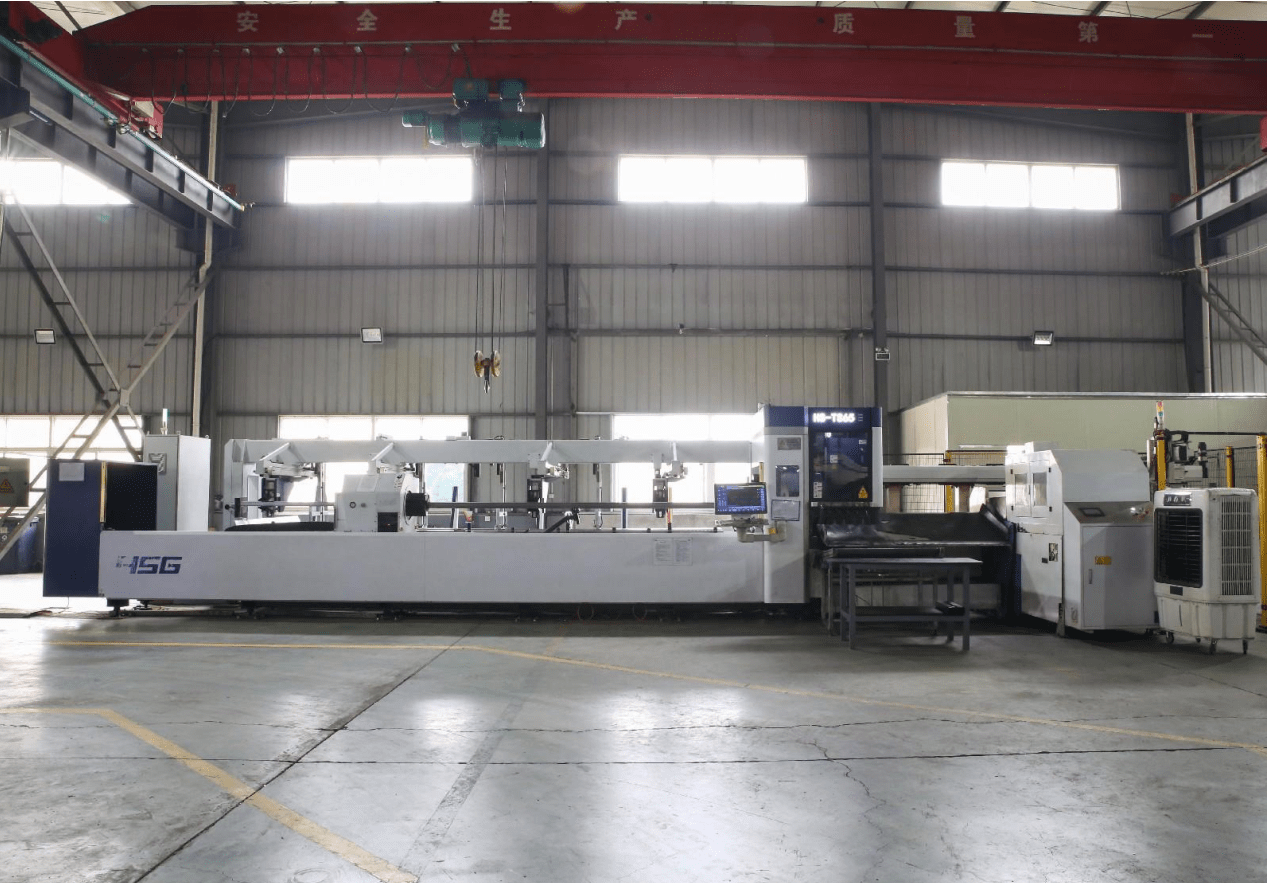
Laser Cutting Machine
- Speed: Maximum 13m/min, Minimum 5m/min
- Precision: ±0.05mm
- Range: 3050*1525mm
- Cuttable sheet thickness: 8.0mm
Metal Tube Laser Cutting Machine
- Power: 3000 watts
- Can process square tubes: 20mm x 20mm to 100mm x 100mm
- Round tube diameter: 20mm to 100mm
- Wall thickness: 0.8mm to 5.0mm
- Can also process various shaped tubes
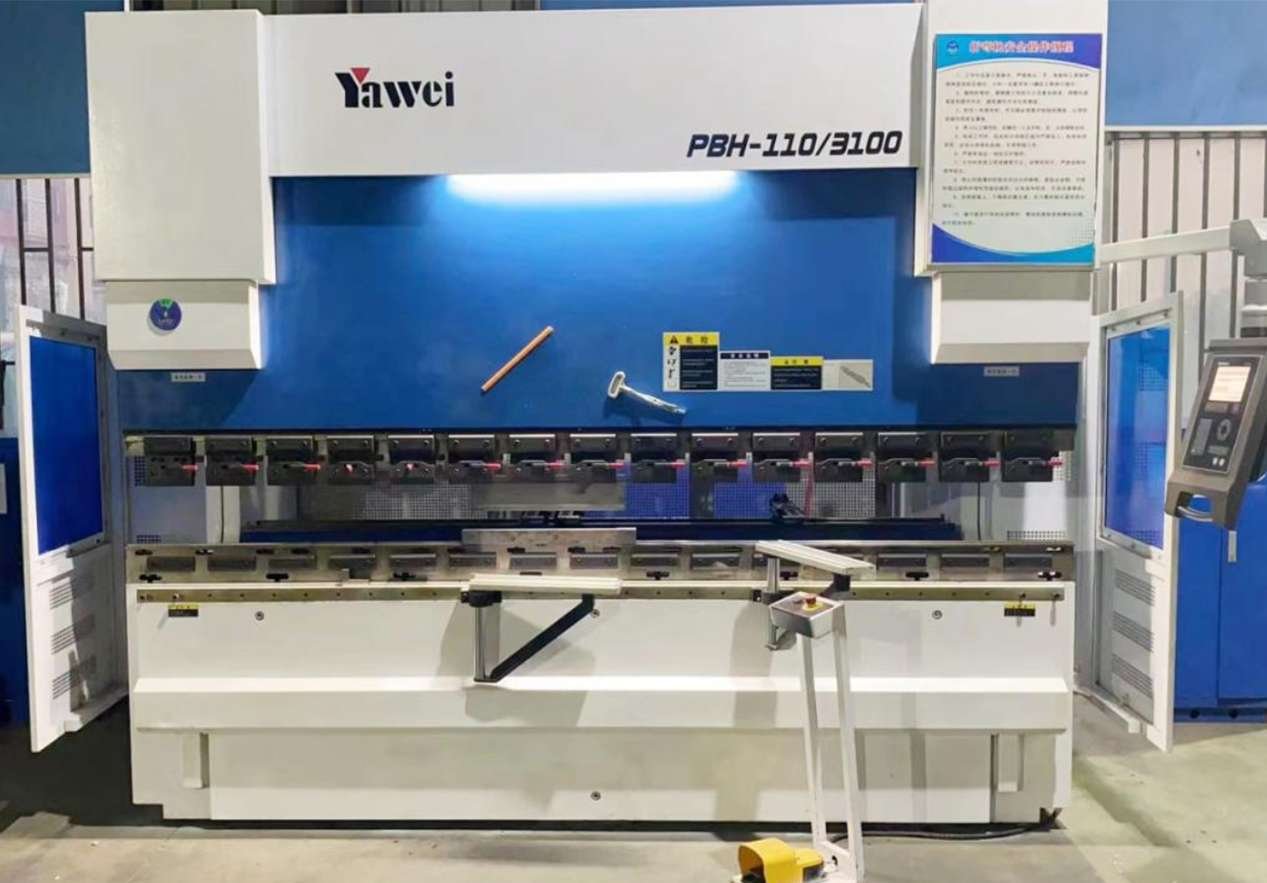
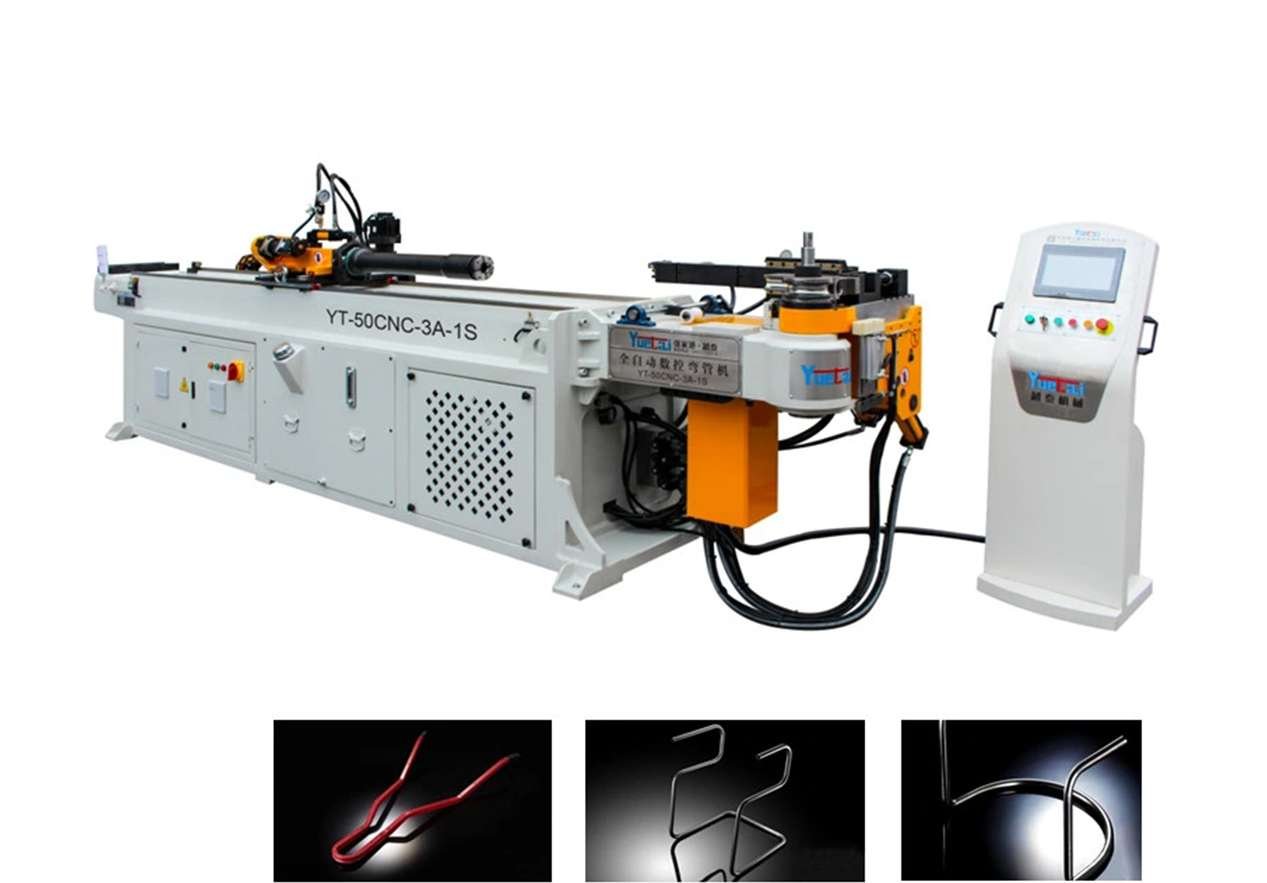
CNC Bending Machine
- Speed:
L axis: 30 m/min
Y axis: 90 m/min
Z axis: 20 m/min
- Maximum pressure: 110 kN
- Maximum bending width: 2600 mm
- Maximum bending range: 1770 mm
- Precision: ±0.1 mm
CNC Tube Bending Machine
- Bending Degree: 0-190°
- Bending Radius: 30-300mm(for machine)
- Min Bending Radius: R≥1.4D(for pipe)
- Bending Speed 80°/s
- Rotating Speed 180°/s
- Feeding Speed 800mm/s
- Bending Accuracy ±0.1°/±0.05°
- Rotating Accuracy ±0.05°
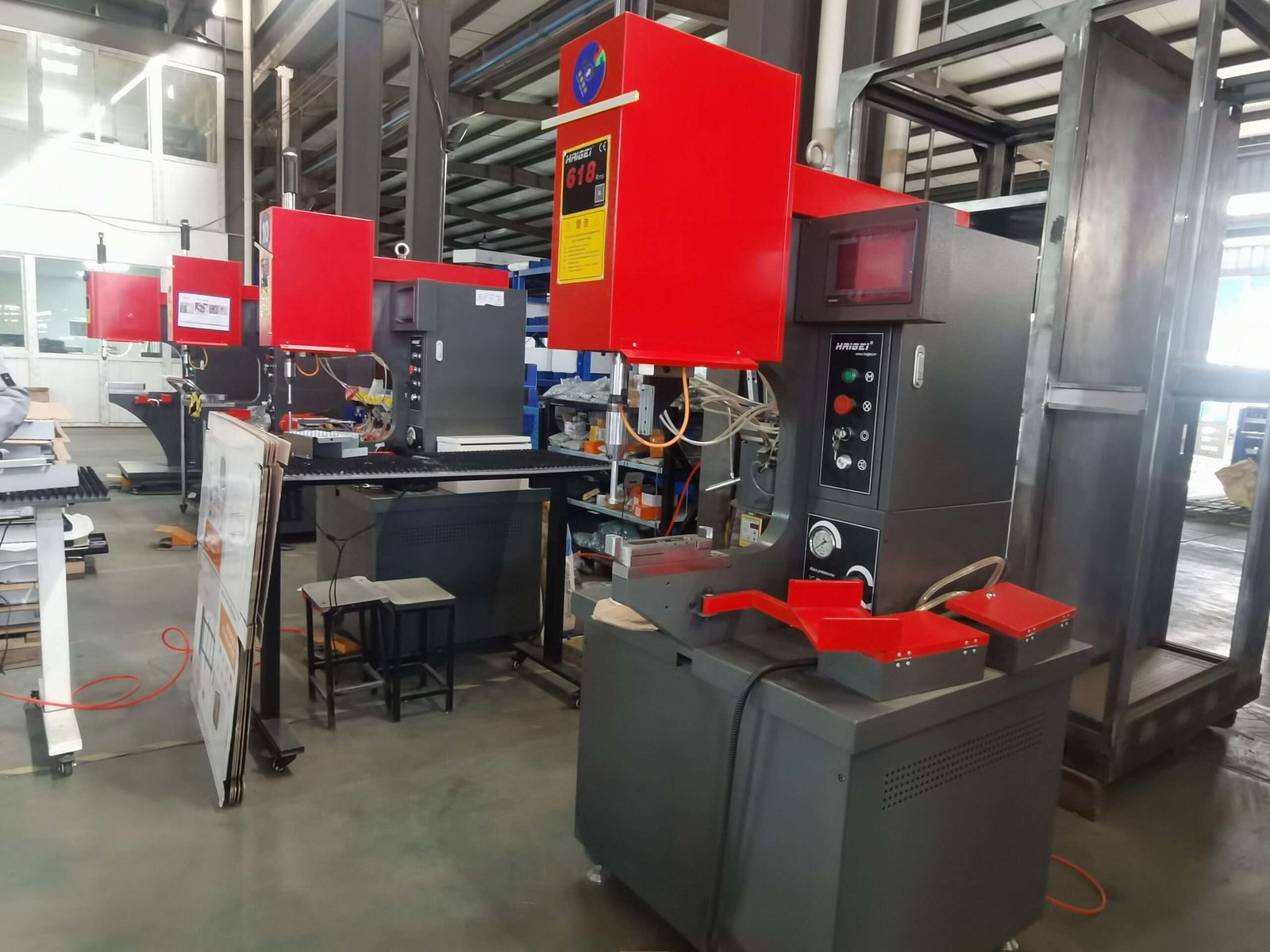
-scaled.jpg)
Haeger Riveting Machine (Fastener Riveting System)
- Stroke Range: 800 lbs (3.6 kN) to 12,000 lbs (53 kN)
- Riveting Range: M2 to M8
Haeger Standalone 4E Riveting Machine (Fastener Insertion System)
- Riveting Force Range: Adjustable from 225lb (1 kN) to 16,000lb (72 kN). Optional modification for 20,000 pounds (90 kN).
- Speed: Up to 2000 insertions per hour.
- Range: Handles fasteners ranging from 0.256 to 1/2 inch (M2 to M12).
- Tool Changing System: Masion is equipped with a 4-position automatic tool-changing device. This can be fast and easily installed on the 4MAS 350 modular automatic feeding system.
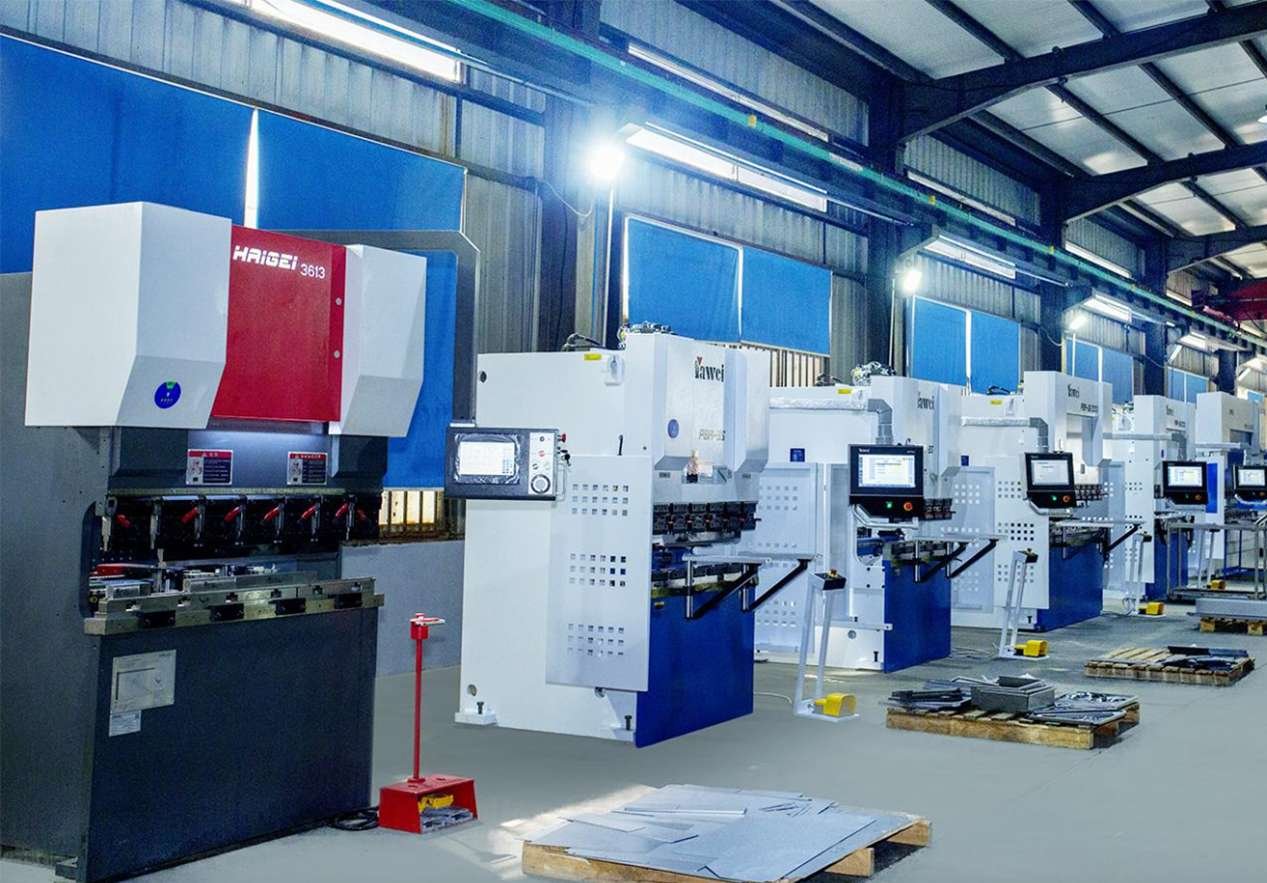
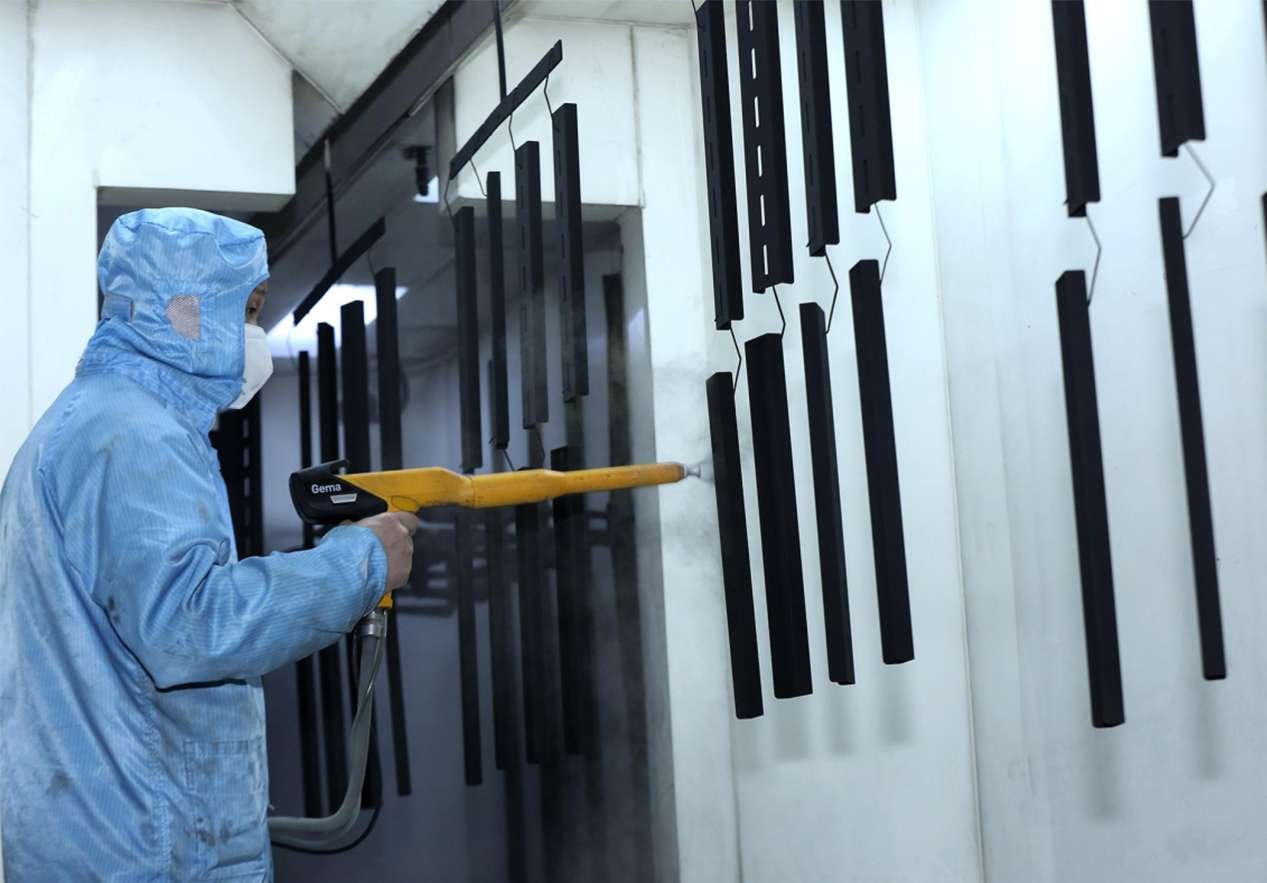
Servo-Controlled CNC Press Brake
- Speed:
●L axis: 15 m/min
●Y axis: 45 m/min
●Z axis: 10 m/min - Maximum Pressure: 110 kN
- Maximum Bending Width: 3000 mm
- Maximum Bending Range: 500 mm
- Accuracy: ±0.15 mm
Haeger Standalone 4E Riveting Machine (Fastener Insertion System)
- Line speed: 4-5 meters per minute
- Single point hanging weight: 50 kg
- Maximum workpiece hanging dimensions:
- Line A: 1200*600*1400 mm
- Line B: 600*400*1400 mm
Why Choose Masion For All Sheet Metal Parts?
Masion is one of the best sheet metal manufacturing factory with 17 years of experience in this field. We; ‘re here to serve you with the best client projects in various industries. These may include Geely Auto, Bull Group, CRRC, etc. Besides this, we deal with both small and large-scale projects with the same care.
DFM Design Support: In case you lack design drawings, then our friendly and competent R&D team will help you prepare them. We give practical and realistic design solutions, improve sheet metal designs, minimize the manufacturing process, and decrease your expenses.
Advanced Sheet Metal Processing Equipment: We adopt comprehensive automatic loading robots, welding robots, laser cutting machines, bending machines, and other high-efficiency sheet metal processing equipment. These offer strong backing for sheet metal manufacturing, thus making the flow of the production of your project smooth.
Skilled Technical Engineering Team: We have a competent team of R & D, Manufacturing, Moulding personnel, skilled Inspectors, Sheet metal production operators, and assembly workers. Right from the design, sample manufacturing, inspecting the sheet metal, designing fixtures and molds, and mass production to assembling your sheet metal parts, we guarantee on-time and quality delivery.
In-House Vertical Integration: The company has a special management of sheet metal processing work, which combines all stages of work in one contractor and organizes all subsequent work with sheet metal, its cutting, stamping, bending, welding, riveting, metal surface treatment, and final assembly. Every production process is monitored and recorded from the beginning to reduce or even eliminate the possibility of having a product with no trace as to how it was made.
On-Time Delivery: Techniques in production and tracking also permit proper management of the flow plan and enable the delivery of your sheet metal parts as planned within the project time frame.
Strict Quality Control: Regarding the quality our factory obtained the international quality management system certificates of ISO9001-2015 and ISO16949. Each operation in the sheet metal processing workflow is tightly regulated, quality checks are conducted, and records of the processes and inspections’ tracking information are provided.
Mold Design and Manufacturing: The in-house mold engineers and R&D team at our company are capable of creating different stamps such as the ones below. The mold changes can be tracked and modified immediately in real-time to enhance communication and cut down on your mold expenses in line with the quality of sheet metal processing.
Flexibility and Versatility: The materials that we can process include stainless steel, aluminum alloy, cold-rolled steel, copper and titanium alloy, etc. Regardless of the scale of your order or the number of batches, it’s identical and we assist you in overcoming the obstacles.
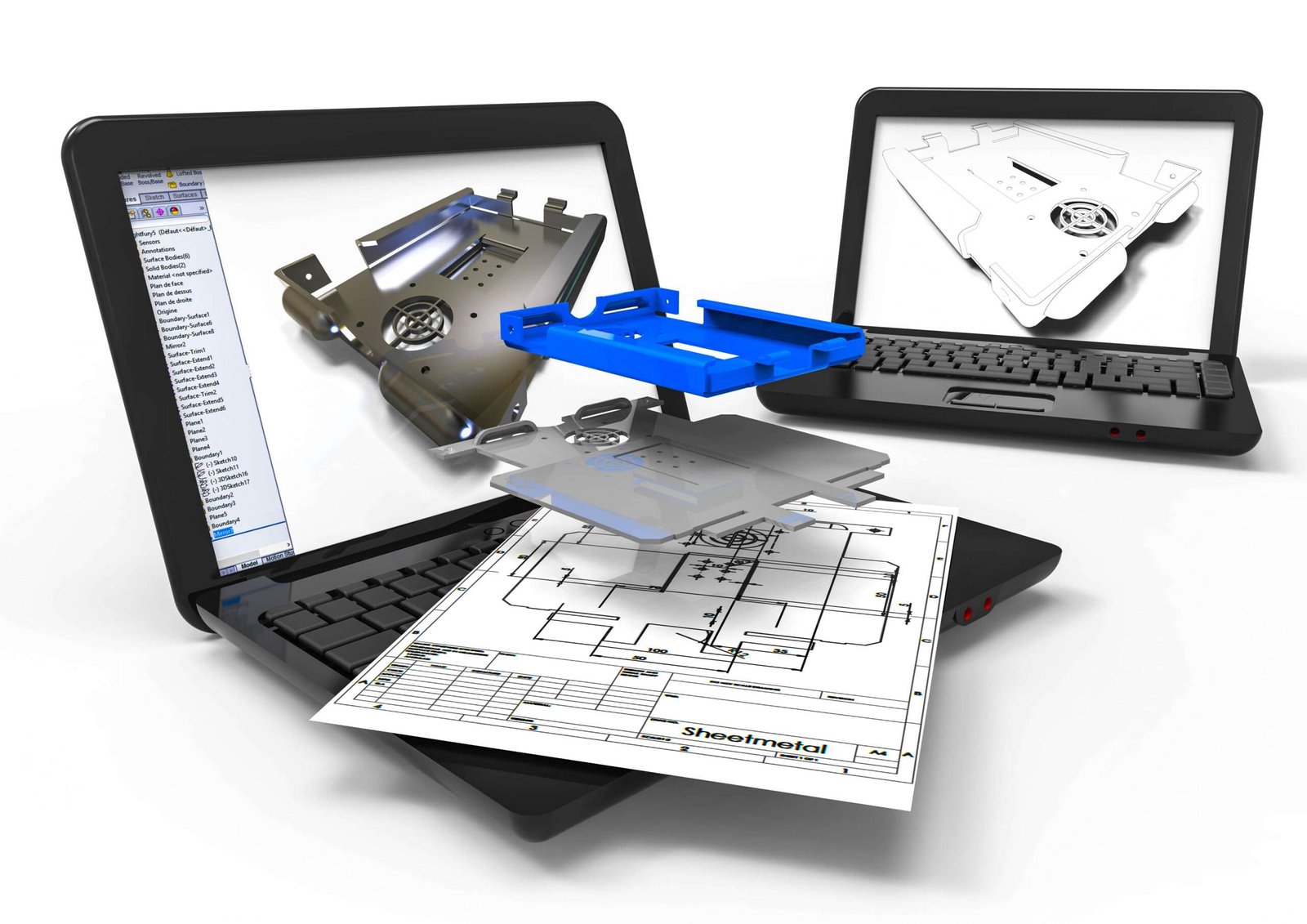
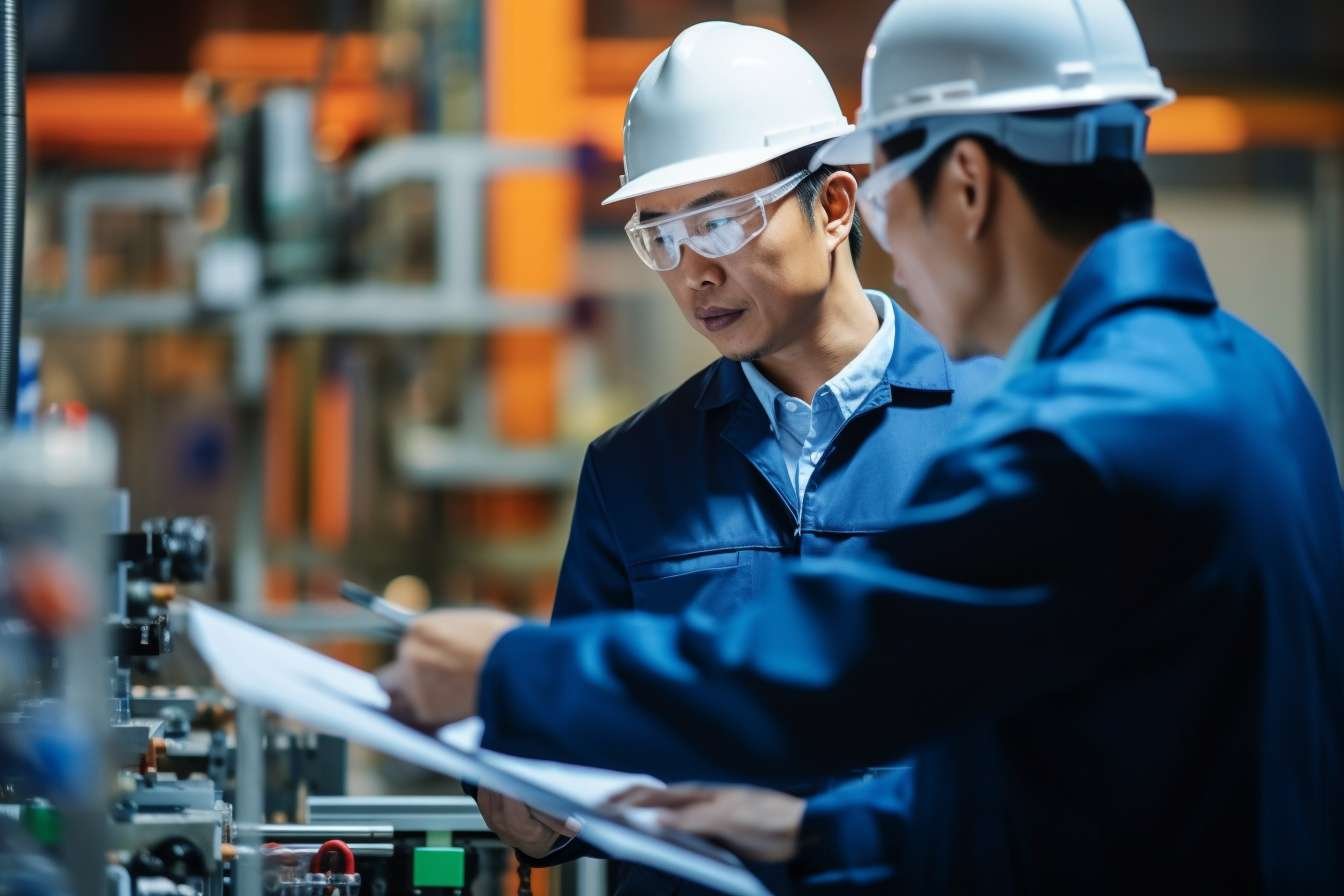

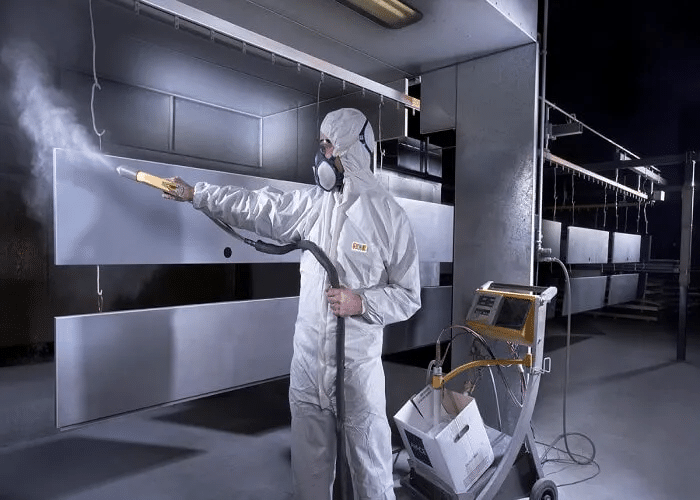
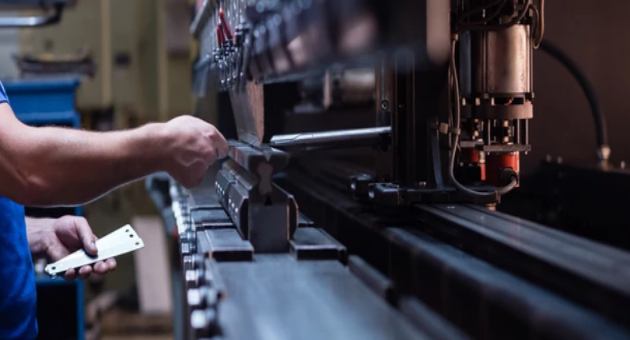
Our Certifications
Masion has 17 years of experience in sheet metal manufacturing. We always make sure to comply with high-quality standards. Our certificates are testimonials of our expertise in this field.
- ISO9001 Quality Management System
- ISO14001 Environment Management System Certification
- TS16949 Automotive Industry Quality Management System
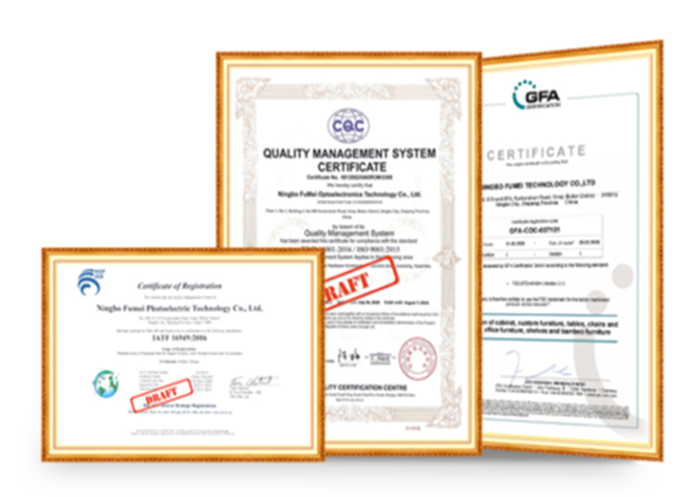
Explore Our Range of Products
Frequently Asked Questions
Yes, we offer professional Design and Engineering services by our professional R & D Design and Manufacturing Engineering team. Here’s what we offer:
- DFM (Design for Manufacturability) Support: We help improve our designs according to the blueprint and provide practical solutions for the manufacturing of sheet metal designs and products, cutting the overall costs while improving on production and quality of the products.
- Custom Design Services: If blueprints are unavailable, our R & D design team can help in the design work help in production solutions, and help to modify the sheet metal design for easy production and less cost.
- Advanced Engineering Support: The mold engineers, manufacturing engineers, and professional R&D engineers make them very competent in product development. They promptly diagnose and solve problems, to see that your projects conform to the necessary quality standards.
- State-of-the-Art Manufacturing Equipment: The facility to manufacture sheet metal includes the following; Automatic loading and welding robots, Laser cutting machines, Bending machines, CNC punch machines, Riveting machines, Assembly lines, and Spraying lines inclusive. This makes sure that the quality of your products is excellent and that you deliver most of your products on time.
- Vertical Integration Production: All the processes involved in sheet metal processing such as cutting the metal, stamping, bending, welding, riveting, surface treatment, and assembly are conducted in-house. This makes vertical integration valuable in cutting down the time taken to transfer items and the quality of the products which makes tracking of each production process efficient.
The sheet metal that our equipment can process is vast and cuts across many categories. If you require laser-sliced sheet metal parts, laser-sliced tube components, or diverse stamped components, you will find them easy to come by with us. We also offer our services in bodyline manufacturing of auto industry sheet metal parts. Some of the sheet metal products we manufacture include:
- Computer Case
- Computer Charging Cabinet
- Defibrillator Cabinet
- Electric Vehicle Charging Station
- Electrical Panel Enclosure
- Energy Storage Cabinet
- Fire Cabinet
- First Aid Cabinets
- Gun Safe
- Industrial Computer Cabinet
- Kiosk Enclosure
- Machine Enclosure
- Medical Enclosure
- Metal Mailbox
- Metal Pop Display
- Metal Storage Cabinets
- Power Cabinet
- Server Cabinet Enclosure
- Tool Cabinet
- X-ray Cabinets & Enclosure
Our equipment can be used in a variety of industries and it is possible to produce to different requirements and guidelines. Should you have any special demands or require more comprehensive information about our sphere of specialization, please do not hesitate to contact us. We promise to provide you with the best quality and finest of sheet metal fabrication services.
HSG 3000W Laser Cutting Machine
- Cutting Speed: Frekvens 0,25Hz, Maximum 13m/min, Minimum 5m/min
- Precision: ±0. 05mm
- Cutting Range: 3050mm x 1525mm
- Maximum Cutting Thickness: 8. 0mm
HSG 6000W Laser Cutting Machine
- Cutting Speed: L-axis at 30m/min, Y-axis – 90m/min, Z-axis – 20m/min
- Maximum Pressure: 110 kN
- Maximum Bending Width: 2600mm
- Maximum Bending Range: 1770mm
- Precision: ±0. 1mm
Bending Machines
- Yawei CNC Sheet Bending 110T 3+1 Axis: Yawei CNC Sheet Bending 110T 3+1 Axis:
- Bending Speed: For the movement of the cutter along the plane the traverse speed is set at the L-axis 15m/min, Y-axis 45m/min while the up and down motion of the cutter is Z-axis 10m/min.
- Maximum Pressure: 110 kN
- Maximum Bending Width: 3100mm
- Maximum Bending Range: 500mm
- Precision: ±0. 15mm
Yawei CNC Sheet Bending 63T 3 Axis:
- Bending Speed: L-axis is at 15m/min while the Y-axis is at 45m/min and the Z-axis is at 10m/min.
- Maximum Pressure: 63 kN
- Maximum Bending Width: 2050mm
- Maximum Bending Range: 300mm
- Precision: ±0. 15mm
Other Equipment
- Automated Assembly Conveyors: In the situation of optimum programmed production lines.
- PEM Riveting Machine: For safe sheet metal riveting.
- Bolt Welding Machine: For the Welding of high-strength bolts.
- Press Riveting Machine: General application for installation of press rivets.
Production Capacity
- Punch Presses: Currently we have 74 punch presses with the tonnage capacity of 45T to 500T where among them 25 presses are of 1100T, 14 are of 800T and 10 are of 1600T.
- Automation Equipment: purchased 20 units of robotic auto-feeding machines, and 20 welding robots to boost up its production line.
- Precision Processing Equipment: Equipment such as NCT Turret Punch Presses, CNC machines, laser tube/plate cutting machines, pipe benders, bending machines, punching machines, etc, and deburring machines.
Inspection Equipment
- Hexagon GLOBAL SILVER
- Bridge-Type Coordinate Measuring Machine
- 5D Image Measuring Instrument
- Salt Spray Tester
- Pressure Testing Machine
- Coating Thickness Gauge
- Oscilloscope
- Custom Inspection Fixtures
Stainless Steel:
- Common Grades: Such as 201, 304, and 316.
- Applications: Applied where strength and resistance to corrosion is highly desired.
- Aluminum:
- Includes Alloys: Like the 6061, 5052, and 7075.
- Applications: Applicable to applications that require lightweight structure with high interaction with corrosive agents.
Brass:
- Various Grades: It is inclusive of H58, H59, H62 and all such other codes.
- Applications: Applied in products that need good electrical and thermal conductivity.
Copper:
- Various Grades: C11000, C86100, and the rest.
- Applications: Applicable to electrical and power industries or where there are components in electrical and power devices.
Cold-Rolled Steel:
- Examples: SPCC, SPCD, SPCE, and so on.
- Applications: Applied mainly in common cutting and those parts that are to be in contact with surface treatments.
Hot-Rolled Steel:
- Includes: Other subgroups include the HR steel and other structure steels.
- Applications: Ideal for applications where the load-bearing capability of the electronic product is a critical factor.
Galvanized Steel:
- Examples: GI, GA, etc.
- Applications: Applicable to those products that are to be given some form of corrosion protection.
Titanium Alloys:
- Examples: TC4, TA1, TA2.
- Applications: Applied in aerospace, Medical, and automotive industries and other premium markets.
This versatility of our equipment makes it possible for us to meet different manufacturing requirements for different materials.
Laser Cutting Machine
- Thinnest Material Thickness: 0. 1 mm
- Thickest Material Thickness: To get all these completed I had to divide the above tasks between two operators while the following tasks were assigned to one operator
- To operate a pantograph of 20 mm thickness.
Bending Machine
- Thinnest Material Thickness: 0. 5 mm
- Thickest Material Thickness: 10 mm
- Punching Machine
- Thinnest Material Thickness: 0. 2 mm
- Thickest Material Thickness: Eight millimetres.
Welding Equipment
- Thinnest Material Thickness: 0. 5 mm
- Thickest Material Thickness: 12 mm
- The size of our equipment enables it to take different thicknesses of the manufacturing materials as the case may be.
Yes, it is possible to have a processing capability on the pages we want to capture as per the specifications of the clients. Here is a brief custom process:
Send Inquiry
In case you have sheet metal design drawings then you can directly bring them to us. When it comes to establishing a production plan based on the design drawings, our R&D department will study its viability, while the sales department will give you a cost estimate. In case of no design drawings, you may describe your vision to us, and based on that, we will make design drawings for your idea and they are then converted to AutoCAD for your approval.
Rapid Prototype Sample Manufacturing
We create the rapid prototype samples using the sheet metal design drawings to obtain the samples that meet the specified design and functional specifications, thereby providing competitive edge to Your Company.
The major difference between Small Batch and Mass Production is that while the former deals with a limited number of products or a small set required for a specific production run, the latter deals with producing a large number of products at a time.
- Send a Request: Once you approve the samples, we go to mass production of the particular batch. Every project that we undertake is unique and we have the capacity, and skills in the creation of sheet metal parts regardless of the size of the project.
- After-Sales Service: Regarding the sheet metal parts in this case, if one has a complaint after delivery, then one can dispute it with us. In terms of technical or quality discrepancies, we shall give output and appropriate recommendations immediately.
- Mold Design and Manufacturing: If your sheet metal parts call for Mold development, based on your design drawings, we can develop and manufacture molds for them to enhance productivity and part quality.
Of course, we can consider issuing small lots of products. Whatever your project, small or large, whatever material you need for your item, we can fabricate it for you and offer you first-rate and accurate sheet metal parts.
The tolerance value that is acceptable for our laser cutting machine is mostly about ±0.1mm , which satisfies most of the requirements for sheet metal cutting accuracy most of the time. If more accuracy in cutting is required then please contact us.
The specific model of our bending machine is Y1-110, its maximum bending length is 3100mm, and its maximum tonnage is 110 tons, which can meet various general sheet metal bending needs. For longer bending or higher tonnage bending, please call us directly.
Thus, the accuracy of our standard CNC punch press is tenths of an inch, plus or minus. 1mm. For progressive die stamping the level of accuracy can be as far as ±0. 05mm. This is to meet various requirements and standards of sheet metal punching.
Our company works according to the ISO16949 or ISO9001-2015 quality management systems, where we perform deep audits of sheet metal products. Cited below are some of the inspection processes which are conducted.
Incoming Material Inspection
- Material Verification: We confirm the material grade, size, characteristics, and chemical makeup through the material quality report.
Also, X-ray detectors are employed to verify the material content and confirm that the material received meets real material quality since any supplier’s offered material should conform to the specified specifications and standards.
- Other Inspections: The examination of the material means its assessment according to the requirements of the design drawings in terms of dimensions, appearance, performance, and functionality.
First Article Inspection (FAI)
- Inspection Content: Through the first sample of the sheet metal, we establish that all important features, sizes, materials, and functions of the product conform to design standards for the production line.
- Report Records: It is wise to observe the measuring activity, recording measurement values, the type of inspection equipment used, and the name of the inspector besides other related performances and material results.
In-Process Inspection
- Process Monitoring: At the end of each operation, the controlled parameters of the steps that took place during a specific part of the production process are measured in real time through several sensors and methods.
- Operator Self-Inspection: Product operators conduct checks during development phases to have a reference point as to whether production is standard to the intended processes and sizes.
Intermediate Inspection
- Dimensional Inspection: Calipers, micrometers, and coordinate measuring machines (CMM) are devices used by inspectors to conduct patrol inspections on the important dimensions in the course of production to control and check on the dimension accuracy of the process.
- Function Testing: For semifinished goods notable functional and performance checks are conducted, not always, but whenever it is required to check if they are conforming to the design stipulated.
Final Product Inspection
- Full Inspection and Sampling: End products made from sheet metal are checked fully or randomly depending on the complexity of the product and/or the customer requirements.
- Performance Testing: Additional tests, if required, include pressure tests, salt-spray tests as well as other appropriate tests agreed upon with the client.
Pre-Packaging Inspection
- Appearance Inspection: Assuring that there are no scratches, deformities, missing corners, and generally no flaws on the exterior of the products.
- Quantity Check: Confirm the quality of the product before it is packed in the appropriate amount.
Inspection Before Shipping
- Final Review: The quality control department also does an end-of-process check that makes sure all records of past and current inspections are traceable to the items.
- Quality Report: Producing a certificate of quality inspection, and registering all the data of the inspection process.
- Our factory has state-of-the-art automated sheet metal manufacturing equipment that has been proposed to help increase efficiency and product quality. This equipment includes, but is not limited to;
- Automated assembly conveyors
- Automated panel conveyors
- Computers used for Welding using robots (for example YASKAWA, FANUC, PANASONIC).
- Robotic arms for loading and unloading the boats
- Laser cutting machines include; Laser cutting machines 3000w and 6000w.
- CNC bending machines
- Automated coating lines
- Other aspects also include an automated production line This line of production assures efficiency and accuracy in production processes. This includes:
- Automated Loading and Unloading: Feeding and discharging of the materials. It is done automatically through robotic arms and conveyor belts as a means of automation.
- Automated Cutting and Welding: Laser cutting and welding operations are carried out with the help of laser cutting machines and welding robots.
- Automated Assembly and Inspection: This helps in setting up the products through the automated assembly equipment and the online inspection systems which warrant accuracy and quality.
- Automated Control Systems We utilize advanced control systems to manage and monitor the production process
- ERP Production Supply Chain Management System: Visibility of the production plan, inventory, and order status at a glance in real-time.
- MES Manufacturing Execution System: In this case, the status of production equipment, production data, and improvement of the production processes.
- Quality Control System: For purposes of quality assurance, constant overview of quality inspection data and registration of various quality inspection processes about quality standards in the production process.
- Highly Automated Processing Equipment We have a variety of highly automated processing equipment, including:
There are cutting machines such as the automatic pipe cutting machines and the angle pipe cutting machines.
- NCT turret punch presses
- CNC pipe-bending machines
- Automated riveting machines and riveting systems.
With this equipment and technique of system the efficiency of sheet metal production, as well as the quality is increased and the cycle time reduced. This in turn has empowered us to provide high-standard, relatively cheaper, and rapidly fabricated sheet metal parts & solutions to customers. Our goal is to give our customers the best in sheet metal products and services at reasonable prices and within the shortest time possible.