Sheet Metal Deep Drawing – In Detail Guide
Table of Contents
ToggleSheet Metal Deep Drawing has now become an essential process. It enables you to make different metallic parts and metal structures. These Metallic parts are highly in demand in many industries. They have found vast applications in various sectors, such as packaging, automobile, aerospace and marine. Not only at large scales, they play significant roles in smaller industries and serve several purposes. So, it’s very important to understand how this deep drawing process works.
This article will give you a complete guide to this process. We will discuss its applications, pros and cons, limitations and alternative solutions available in the giant market of sheet metals.
Sheet Metal Deep Drawing – Understanding Definition
Deep drawing lets you convert the sheet metal into a curved structure or part. This part usually has a smaller diameter as compared to the already curved details. Firstly, the flat metal piece, known as blank placed between the holder and the die. Then, the punch pushes it into the die. Here, it deforms and gets the shape of a die.
Check this Video, it will help you better understand the workings of this whole process.
Deep Drawing Sheet Metal Process
So, here is the step-by-step of the Deep Drawing process;
Preparation of design drawings and manufacturing processes
Sheet metal deep drawing process starts with the development of drawing for proposed design. Here, you specify the dimensions, shapes, tolerance and other features of the metal parts. These drawings work as a building block for the rest of the process. Moreover, They also finalize the manufacturing procedure and sequence of the process. So, make sure to avoid mistakes here. Otherwise, you can waste the material and time on it.
Design Making of the parts
Make plate forming mould – Die Manufacturing
Just after the design part, another step is to make plate-forming moulds. This is also known as die manufacturing. This die is usually made up of tool steel or some durable material. This is precision machined that match the desired shape of any part. So, the die comprises two major components, i.e. punch and die. The punch allows the push of the metal sheet in the die cavity. While the die gives the metal sheet, an appropriate shape.
Die Manufacturing
Lay the plate and adjust the mould
After die preparation, the flat sheet metal is placed in the blank holder. Then it laid onto the die. This die gives proper alignment and clearance between punch and dies components. This adjustment deals with the shape of the part and prevents it from wrinkling. So, make sure to avoid any mistakes at this point.
Placement of Metal Sheet in Blank Holder
Pull sheet material to achieve sheet forming
Once, you place the flat sheet between punch and die. Now, the process begins. The mechanical or hydraulic press inserts force on the punch. Then this punch presses the sheet metal into the die. Then this metal is drawn into the die cavity and gets its shape. The depth of the metal part is usually controlled by the stroke length and die design.
Sheet Forming
Machining surfaces and edges
In sheet metal deep drawing process after forming sheet the metal part undergoes additional machining. So, you can refine its surface and edges. This process includes the trimming of excessive material attached to the part. Additionally, you need to remove the sharp edges and machine the surface to get the required tolerance and surface finishes.
Cutting Excessive Material
Perform subsequent cutting, stamping, and welding
Some additional operations need to be carried out depending on the design and requirements of the final products. These may include cutting, stamping, bending, or welding, They help to add features and join components with the final part. Moreover, the final part gets refined more to meet the particular aesthetic requirements.
Cutting and Welding of Metal Sheet
So, it gives different shapes and geometries of metal parts.
- Deep Drawing of Cylindrical Metal Parts: Here, the punch and die set gives a cylindrical shape to metal. Hence, the metal is stretched and formed into the required cylindrical geometry.
- Flanged Cylindrical Parts Deep Drawing: It is the combination of cylindrical shapes and flanges. These flanges provide structural support. Moreover, they connect the components.
- Deep Drawing of Stepped Cylindrical Parts: This includes making steps with cylindrical parts. They can have varied lengths. This shape usually helps attach the multiple components.
- Conical Parts: This includes the deformation of a metal into a conical shape. It has wide applications in making various components, such as funnels, cones, and tapered tubes.
- Spherical Parts: It includes a spherical shape. This method is widely used in producing shapes like domes, hemispheres, and spherical containers.
- Deep Drawing of Paraboloid of Revolution Parts: This includes the conversion of a metal sheet into a parabolic form. It is usually used in optical devices, antennas, and reflectors.
- Deep Drawing Forming of Low Square and Low Rectangular Boxes: Here, the sheet metal deep drawing forming converts the flat sheet into low-profile squares or rectangles. They are generally used in the packaging industry.
- Deep Drawing Forming of High Square Boxes: Just like the previous one, it converts metal sheets into taller square boxes.
- Deep Drawing Forming Method for High Rectangular Boxes: Just like above., it is a formation of square boxes with rectangular geometry. It is widely used to make large size rectangular boxes.
Inspection and surface finish
So, the last step is the thorough inspection of the metal pieces. Here you check, if the dimensions, quality standards, and tolerance of the metal part meet the requirement or not. After inspection, you can do painting, plating, or coating of the part. Hence, your product is now ready to meet the customer expectations and market standards.
Surface Finishing of Material(Powder Coating)
Deep Drawing Sheet Metal Forming – Essential Design Tips
You need to pay attention to sheet metal deep drawing forming process considerations to achieve precise end results. So, here are some tips you can follow to get efficient results.
- Material Selection: The right Material always leads to an efficient design. So, select the appropriate material. Here the the important factors, you should keep in mind are; ductility, tolerance, strength, and formability. The common materials used are aluminum, stainless steel, and several alloys.
- Geometry and Symmetry of Shape: Make sure, you design your parts with uniformity. They must have the same thickness and even distribution of material during the whole process. Avoid sharp edges and corners. They can lead to wrinkling and tearing of the material.
- Incorporate Draft Angles: These angles give formed parts from the die. Generally, the draft angle of 1-2 degrees/slide is enough to avoid tearing issues.
- Rounding Edges: The round edges reduce the stress load. Moreover, they minimize the risk of tearing during the forming process.
- Tolerance: Make sure to consider the tolerance. it gives dimensional accuracy to the final parts. if the tolerance is tighter, it may need additional steps and increase the overall cost of the process.
Sheet Metal Stamping Deep Drawing Key Differences
So, here is a comprehensive table to get a better understanding of Stamping and deep drawing.
Aspect | Deep Drawing | Stamping |
Process | Involves pulling a flat sheet metal into a die | It involves pressing or punching metal sheets or blanks |
Forming Complexity | Suitable for forming complex, three-dimensional | Typically used for simpler, two-dimensional shapes |
Part Depth | Well-suited for forming deep parts with high | Limited in-depth compared to deep drawing |
Material Thickness | Can work with thin materials or thick materials | Typically used with thinner materials |
Equipment | Requires specialized equipment such as deep drawing presses | This can be performed using various types of stamping presses, dies, and punches |
Tooling Complexity | Requires complex dies and punches | Tooling is typically simpler compared to deep drawing |
Cost | Tooling and setup costs may be higher | Tooling costs are generally lower |
Production Efficiency | Well-suited for mass production of complex parts | Suitable for high-volume production of simpler parts |
Special Deep Drawing
Special drawing involves specialized techniques that are used in sheet metal deep drawing process. It helps in achieving particular results and handles the challenges. It is usually based on specific requirements such as part complexity and material properties. So, here are its types in detail.
Soft Film Drawing
It includes the use of lubrication film or coating on the surface of a metal sheet. This process is carried out to reduce the friction during the deep drawing. Moreover, it helps prevent the tearing or wrinkling of the metal. Hence, allows the smooth forming of difficult shapes.
Opposite Hydraulic Drawing
Here the hydraulic pressure is applied from the opposite side of the metal sheet. This technique is useful to control the material flow and distribution more precisely. Additionally, it is important for forming deep or complex shapes.
Temperature Difference Drawing
it includes heating the specific areas of the metal sheet at different temperature ranges. This heating makes the sheet area, more ductile. So, it becomes easier to deform it in a certain shape. Moreover, it also allows greater control over the forming process and reduces the risks of defects.
Pulsating Deep Drawing
This process included the implementation of intermittent or pulsating pressure during stretching. This method distributes the material more evenly. Moreover, it helps reduce the thinning and maximizes the tearing risks of complex shapes.
Radial Thrust Deep Drawing
This technique comprises applying the force from the center to the outward of the metal sheet. It also helps in the even distribution of the material and gets the forming parts with symmetrical or rounded shapes.
Sheet Metal Deep Drawing Process Features
Some features make deep drawing an attractive method of manufacturing metal parts. these features are listed below;
- Scalability and Cost-Efficiency: Deep drawing is a scaleable process. So, it is suitable for both small and large size industries. Moreover, this can easily be automated and gives efficient production at lower labor costs. Moreover, it requires minimal material waste. this contributes to overall cost-effectiveness.
- Versatility in Shapes and Sizes: Besides other features, deep drawing is a versatile solution. It is capable of making a wide range of shapes and sizes. These shapes can be simpler or difficult. Moreover, it can accommodate several materials, alloys, and even plastics. That is why, it has diverse applications in different industries.
Different Problems of Deep Drawing with Their Solutions
So, let’s discuss the different problems and solutions. We have discussed their classification, problems, simplified drawings of these problems, reasons, and their appropriate solutions.
Classification | Problem | Simplified Drawings | Reason | Solution |
Deep Drawing | The bottom is broken and has shrinkage and convexity | ![]() | Drawing friction is too small | – Increase the radius of the punch corner – Draw the river risk – Correct the concentricity of the die – Reduce force – Ensure uniformity of material |
Flange Deep Drawing | Wrinkles appear at the edges of the flange and the surface | ![]() | The sheet metal deep drawing die is too small and the blank holder force is a bit large | – Increase the fillet radius of the die – Manage the force |
Hill Deep Drawing | The wall appears convex and decorative | ![]() | No edge-holding device or the edge-holding force is too small | – Appropriately increment in the force – Apply thin and even lubricants |
Deep Drawing Edge | The edge of the mouth of the deep-drawn part is tooth-shaped | ![]() | There are burrs on the edge of the hair, too many impurities in the material, or there are gaps in the mold mouth, which are rough and not smooth | – Repair and sharpen the edge of the blank blanking die – Remove rough edges and reduce edge burrs – Improve material quality |
Surface Deep Drawing | Ripples or bulges in the mouth | ![]() | Blank placement, uneven force of holder or inconsistent material sharing, uneven gaps | – Accurate blank positioning – Consistent adjustment force – Prevent fluctuations in section thickness and uneven gaps |
Round Deep Drawing | Bubbling appears around the bottom | ![]() | Lubricant flows down and collects together, cannot be eliminated or there is no vent hole | – Apply lubricant thinly and evenly – Consider exhaust and oil drain holes in the mold structure |
Thinning Deep Drawing | Localized bulge distortion | ![]() | Lubricant is locally concentrated or foreign matter is mixed in | – Clean and eliminate foreign matter in time – Pay attention to reasonable line teaching and lubricant |
Deep Drawing Taper | Twist, short song | ![]() | Uneven deformation, unreasonable picking or ejection of parts, or uneven edge holding force | – Change the method of picking up and pushing parts – Adjust the blank holder force |
Reverse Sheet Metal Deep Drawing | Wrinkling at the mouth of the drawn piece | ![]() | The radius of the die fillet is too large, and the material breaks away from the edge ring at the final stage of the edge-pressing | – Reduce the radius of the die fillet – Use an arc-shaped edge ring as much as possible |
Panel Deep Drawing | Wall rupture. Wrinkled flange | ![]() | The blank holder force is too small or the mold gap size and corner radius are too small | – Adjust the blank holder force – Increase the die gap and fillet radius |
Rectangular Drawing | The corners of the box-shaped parts are folded inward and partially wrinkled | ![]() | The shape of the edge holder is inappropriate, the edge holder force is small, or there is less material at the corners | – Improve the shape of the blank holder – Adjust the blank holder force – Increase corner material |
Twisted Drawn Parts | Drawn parts twisted | ![]() | Excessive blank holder force, improper lubrication | – Adjust the blank holder force and strengthen the lubrication |
Bulging Bottom and Wall | Bottom and wall bulging | ![]() | Rounded corners at the step corners are too small, poor drawing performance of material, unevenly applied lubricant | – Increase the fillet at the corners – Improve lubrication and select good materials |
Step Drawing Issues | Step-shaped drawing, wrinkles and cracks | ![]() | The rounded corners at the step corners are too small, poor sheet metal deep drawing performance of the material and unevenly applied lubricant | – Increase the fillet at the corners – Improve lubrication and select good materials |
Wall Cracks | Wall cracks | ![]() | The mold cavity is rough and cracked | – Repair and polish the mold working surface |
Damaged and Crooked Parts | There is no vent hole in the mold cavity the vent hole is too small, and the ejector rod is too long, causing the deep-drawn parts to be damaged and crooked. | ![]() | The lubricant is applied too thickly, there is no vent hole or the vent hole is blocked | – Improve lubrication, clear or open vents – Clear or enlarge the exhaust hole, and shorten the ejector pin. |
Straight Wall Wrinkles | Straight wall, straight wall, wrinkled | ![]() | The corner clearance is too small and the straight wall clearance is too large | – Increase the corner clearance and reduce the straight wall clearance. |
Detached Bottom Cover | The bottom cover is pulled off and detached | ![]() | The fillet radius is too small and the material is cut off | – Increase the fillet radius at the mouth of the drawing die |
Material Rebound Distortion | Material’s rebound distortion | ![]() | Due to the high elasticity of the material, small deformation and rebound | – Increase the blank holder force and reduce the fillet radius |
Box Corner Issues | Box corner broken | ![]() | The drawing gap is too small and the corner fillet radius is too small | – Increase the gap and increase the corner fillet radius |
Edge Cracks and Lack of Flesh | Cracks, openings, and lack of flesh appear on the edges of the mouth | ![]() | The shape of the blank is wrong and too small, there is not enough material in the corner part, and there is not enough material in the straight wall part | – Increase the size of the blank and improve the shape of the blank |
Corner Cracks | Cracks appear at the corners of the box-shaped parts | ![]() | The punch radius is too small and the blank holder force is too large | – Increase the punch radius and adjust the blank holder force |
Wrinkled Flange | Wrinkled flange | ![]() | The blanking force is too small or there is no blanking, so the flange cannot offset the excessive tangential pressure, causing the tangential deformation to lose stability and cause wrinkles | – Increase the edge holder when there is no edge holder; increase the edge holder force appropriately when there is an edge holder |
Sheet Metal Deep Drawing Industrial Applications
This method can make complex shapes. So, we can find its wide applications in different industrial sectors. Let’s discuss all of these one by one.
- Automotive Industry: It has wide applications in the manufacturing of automotive parts, such as car body panels, oil pans of an engine, fuel tanks, exhaust systems, structural components, and fenders. These parts require precise dimensions and accuracy. So, deep drawing is a suitable option here.
- Electrical Appliances: Deep drawing plays a significant role in the manufacturing of household appliances. This process becomes a blessing in disguise for air-tight or water-tight containers. Moreover, we can observe its applications in appliances like cooking pots, sinks, and washing machines.
- Aerospace Industry: Deep drawing produces lightweight but strong components. So, it is crucial for aerospace applications. It helps in manufacturing aircraft parts, engine components, and fuel tanks.
- Electronics and Medical Industry: If we talk about electronic gadgets like Smartphones, Tablets, and Computers, deep drawing is the best choice for intricate shapes and structures. These shapes have precise dimensions. Moreover, they can easily accommodate the electronic parts. Similarly, in the manufacturing of medical equipment, it is one of the best options. Its applications may include surgical instruments, medical devices, and implant components.
- Packaging and Consumer Goods Industry: It has wide applications in packaging containers like cans, food containers, and aerosol cans. Moreover, in Consumer goods, deep drawing applies in the production of several consumer goods. It may include furniture parts, lightning fixtures or decorative items.
Commonly Used Materials for Deep-Drawn
Here are some most commonly used metal sheets for the deep drawing process.
Material | Grades | Applications |
Stainless Steel | 304, 316, 430, 201 | Kitchen sinks, automotive parts, cookware, appliance components |
Aluminum | 1100, 3003, 5052, 6061 | Beverage cans, automotive parts, kitchen utensils, aircraft parts |
Copper | C101, C110 | Electrical connectors, plumbing fittings, heat exchangers |
Brass | C260, C272, C360 | Hardware, plumbing fixtures, musical instruments, decorative items |
Carbon Steel | 1008, 1010, 1020, 1022, 1040 | Automotive panels, household appliances, industrial components |
Titanium | Grade 1, Grade 2 | Aerospace components, medical implants, marine equipment |
Nickel Alloys | Inconel 600, Inconel 625, Monel 400 | Chemical processing equipment, marine applications, turbine blades |
Galvanized Steel | DX51D, SGCC | Roofing panels, automotive body panels, outdoor enclosures |
How Sheet Metal Deep Drawing is Beneficial?
Industries are using several innovative ways of manufacturing. Deep drawing is also one of these. It has the following benefits.
- Fast process: Its punch moves up and down very frequently. So, no other method can combat its speed. Moreover, it is the most suitable option for large quantities of metals.
- Exclude other Assembly steps: If we talk about the shapes of products, this process makes shapes with close ends. So, there is no need to cut or weld its exterior sides.
- Highly Efficient and Accurate: As mentioned earlier, its parts have no join. So, that is why they are the best fit as a water or gas-tight container. Secondly, when these parts come out of the forming press, they are relatively consistent. Also, they are very similar to the designs. So, if you need a large quantity of the same parts, this process helps in providing similar designs accurately,
- Complex Design Manufacturing: Let’s not stop on small shapes like cans, sinks or tubes. The deep drawing method is also convenient when you need complex geometries and intricate structures, the deep drawing method is convenient for all. Thus, it has vast applications in the automobile industry.
- Robust Parts: Metals have a rigid structure. Their molecules are quite tightly packed. So, when the metal sheet is allowed to pass through deep drawing, these molecular structure moves to some extent and then their orientation becomes locked. As a result, you get the strong and hard finished parts.
Calculations for Size, Force and Reduction Ratio
Size Calculation Diagram
Sheet Metal Deep Drawing Size Calculation
1.Surface Area Calculation: Find the accurate surface area of the starting sheet metal.
Surface Area of the Blank = π (Blank Radius^2)
2. Calculations for Finish Part Area: Then calculate the surface area of the specific part.
Surface Area of the part = π (Blank Radius)^2 + 2 π (Radius of Finish part x Height of Finish part)
3.Keep Both S.A. Equal: Make sure that the surface areas of the sheet metal and the finished part are the same.
II Blank Radius^2 = π (Radius of Finish part )^ 2 + 2π (Radius of Finish part x Height of Finish part)
Blank Radius= √ Radius of Finish part(Radius of Finish part + 2(Height of Finish part))
4.Calculations for Reduction Ratio: So, the reduction ratio is needed to get the part dimensions.
DRR = (Blank’s Dia x Punch’s Dia) / Blank’s Dia
5.Force Calculation: Estimate the required force to carry out this process.
MDF = ㅠ × (dia of punch + blank thickness) × (blank thickness × Utensile strength of sheet)
Examples Of Deep Drawn Sheet Metal Parts
Deep-drawn sheet metal parts can vary widely in shape and size. Some examples include:
- Cylindrical containers
- Cups
- Boxes
- Automotive body panels
- Kitchen sink basins
- Metal housings for electronic devices
- Metal canisters or cans
- Metal tubes with closed ends
- Dome-shaped metal components
- Metal caps or lids for containers
Everything has pros and cons. Similarly, if one thing serves you in many ways. It has also some limitations, that it cannot go beyond them. So, let’s talk about sheet metal deep drawing drawbacks or limitations right in the following section.
Limitations of Deep Drawing
It is not a good option for hard or brittle materials like cast iron. Additionally, the thickness of the material is important to notice here. There are materials, which are either too thin that they might rip. While some are too thick and could not get a proper shape. Plus, this is a bit costly. So, if your system wears out over time, its maintenance is expensive as well.
Common Problems Occur During Deep Drawing Process
During the transformation of metal sheets into shapes, various issues can arise and affect the quality of products. So, it is crucial to identify these issues and address them timely. Here are some common issues;
Friction
When the punch pushes the metal sheet into the die, it rubs against the tools and causes friction. It can result in wearing out the equipment or cause scratches that can affect the overall efficiency of the process. You can overcome this friction using lubricants. Additionally, you can apply some coating between the material and the tools. You can also use materials that have lower friction.
High-temperature bonding
There are chances when the metal can stick on the die or other tools due to high temperature. It can become difficult to remove the metal part from the tool. As, a result, the whole production can be disturbed. So, if this is the case, you must apply proper cooling techniques. You can use bonding-resistant materials to avoid adhesion. Moreover, you must periodically clean and maintain the tools.
Die wear
The constant pressure and rubbing of metal sheets can wear out the die over time. It can lead to faulty parts, and less efficiency and accuracy. But, you can avoid this issue. Make sure, your die is made of durable material that can last for a long. Moreover, you can also mitigate this issue by regular maintenance and periodic replacement of dies.
Wrinkling
Just like other issues, wrinkling is also common in sheet metal deep drawing. Sometimes, you don’t pull the metal sheet tightly into the mould. So, it can fold from the corners and create wrinkles on the material. It makes your final product look bad. Moreover, it can also affect the overall performance of deep drawing.
So, if you need to tackle this issue, make sure proper stretching of the metal sheet. Secondly, optimize your tool design to avoid wrinkling. You can also use process parameters such as drawing speed and lubrication. They can minimize this issue as well.
Thinning and Tearing
When you stretch the metal sheet in areas with sharp bends or tight curves. it may become very thin and tear apart. Resultantly, it can ruin the part. So, it is important to tackle this issue timely. You can control the drawing ratio and avoid excessive stretching. Moreover, you can use proper techniques to distribute stress evenly. These techniques may include drawing beads or adding material relief features.
Defects on the Surface
During deep drawing, the metal surface can get scratched, dented or marked by the tool. In this case, it can make your final product less attractive. It can also affect its working efficiency. So, use the smoother tool surfaces and carefully monitor the process parameters. Moreover, if you perform regular inspection and maintenance of tools. It can also help in identifying and addressing the exact issue.
Earing
This issue occurs when the metal forms irregular wrinkles on the edges. It can be because of differences in the metal properties or less lubrication. Earing can make the parts uneven. It can result in problems during the fitting process.
So, fix this by using materials with consistent properties. Additionally, apply enough lubrication to the tools.
What are the Factors Affecting the Total Cost of Deep Drawing?
Many factors affect the overall cost of deep drawing, directly or indirectly. So, some of them are mentioned below;
- The more the feature requirements, the more the cost.
- Difficult or unsuitable locations need more cost.
- The greater the size of the parts, the greater the cost.
- The higher the thickness, the more material usage and lead to a more costly solution.
Difference Between Conventional Deep Drawing vs. Incremental Deep Drawing
Here are some aspects that can differentiate Conventional and incremental Deep Drawing.
Aspect | Conventional Deep Drawing | Incremental Deep Drawing |
Process Overview | Single-step process | Multi-step process |
Blank Material | Typically thicker blanks | Can use thinner blanks, reducing material cost and weight |
Tooling | Requires a single set of dies | Utilizes multiple sets of dies and punches |
Material Flow Control | Limited control over material flow | Enhanced control over material flow, reducing defects |
Forming Force | A higher forming force required | The lower forming force required |
Friction | Higher friction between blank and die | Lower friction due to intermittent contact between blank and die |
Lubrication | More lubricant usage | Reduced lubricant usage |
Tool Wear | Higher tool wear due to single step process | Reduced tool wear due to incremental process |
Surface Quality | This may result in surface imperfections | Improved surface quality due to better material flow control |
Forming Complexity | Limited ability to form complex shapes | Can form more complex shapes with greater ease |
Energy Consumption | Higher energy consumption | Lower energy consumption |
Cycle Time | Longer cycle time | Shorter cycle time |
What can be an Alternative Approach to Deep Drawing
An alternative process to sheet metal deep drawing is hydroforming. In hydroforming, the punch is replaced with high-pressure fluid. This fluid can be water or oil. So, it pushes the metal into the die and gets the required shape. You can achieve complex shapes in fewer steps. However, it requires special equipment that can last longer than deep drawing.
Why Choose Us for the Deep Drawing Process?
Sheet Metal Masion has 17 years of experience in the sheet metal industry. Our experts are well-qualified to handle everything from simple to complex designs. We have a wide range of modern equipment for deep drawing. These will help in making different parts at a large scale.
Moreover, we have a well-equipped facility in Ningbo, Zhejiang, China. Here our whole team ensure you the top results for the deep drawing process. So, if you need prototypes, quality inspection, or any design services. Just browse our name, Sheet Metal Masion and get our services today.
Besides quality work, our streamlined approach helps you guarantee the timely completion of your product. So, don’t go anywhere. Contact us today!
Conclusion
In conclusion, the Sheet Metal Deep Drawing process provides you with both simpler and complex parts and metal structures. It has three main components, blank holder, punch and die. Just place your blank or metal sheet in the holder. The punch will start pressing the material into the die. Eventually, your material starts to take the shape of the die.
This process has wide applications in different industries. So, it’s now a popular choice for the material parts. Besides its applications and wide scope, it has certain limitations as well. So, keeping both the dark and bright sides, deep drawing is quite significant in the metal industry.
So, if you want to get deep drawing services in China, Sheet Metal Masion provides you with all basic and customized deep drawing services. Get your Quote now.
Frequently Asked Questions
Q1: Which metals and alloys are commonly used in sheet metal deep drawing?
These may include stainless steel, aluminium, copper, brass, carbon steel, titanium, and various alloys. However, the selection of material is based on several factors like
required strength, corrosion resistance, and final properties of the formed part.
Q2: What factors we should consider while choosing the designing parts?
The metal can undergo wrinkles, wear and tear, and other issues. So, the following factors must be considered for designing the part, i.e. material selection, part geometry, wall thickness, fillet radii, and draft angles.
Q3: Which one is considered as best metal for deep drawing
Stainless Steel is one of the best options for sheet metal deep drawing. Because it can easily change into difficult shapes. Moreover, they are formable and are highly ductile as compared to carbon steel
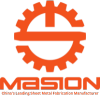
Send Your Inquiry Today



+86-18969433502