A Ultimate Guide to Sheet Metal Deburring, Its Methods, and Its Applications
Deburring of sheet metal is one of the essential requirements in the manufacturing process. Here the parts or tools are made free from burrs or sharp edges. These abnormalities happen in many processes and are applied to a material, i.e. cutting, punching, drilling, or shearing. Apart from aesthetic appearance, deburring has other significant advantages as well. It makes the metal part safe and functions well. So, in this article, we will focus on the definition of sheet metal deburring and deburring methods and their significance in different sectors.
Table of Contents
ToggleHow would you define Burrs?
Burr is an undesirable, rough surface, or a material component that stays on the part after undergoes to different processes. These processes can be cutting, drilling, milling, grinding, or stamping. Failure to do these processes can result in the burrs. These may interfere with the performance of the end product, its safety as well as its appearance.
What is Deburring
We can define deburring as the surface finishing process of removing undesirable raised edges. It is also the removal of small pieces of material that are still sticking to a workpiece after the machining process. It is important to note that these burrs can occur during any type of machining process, i.e. cuts, drills, grinds, mills, or stamps. Deburring on the other hand tends to refine these inequalities to such an extent that the metal parts are free of any roughness, point, or edges that are sharp or uneven. Moreover, this process improves the safety, usability, and appearance of the final part. It is crucial in numerous manufacturing processes. So, that makes it suitable for the subparts to fulfill design requirements.
Types of Burrs
So, here are the different types of burrs. Each burr has formed under different conditions and processes;
Poisson Burr (Shear Burr)
It forms during the shearing or cutting of material. Besides this, it undergoes some kind of plastic deformation. These burrs are generally quite thin and follow the length of the cut towards the edge. Moreover, these have numerous applications, i.e. shearing and punching where the material is displaced and nothing removed.
Roll-Over Burr
These are formed when the material is pushed out from the workpiece edge rather than being trimmed. It usually comes as a result of milling or turning. These burrs have a curved, rolled edge coming from the surface of the workpiece. So, they prove that during the machining process, some material of the workpiece was not cut out completely.
Break-Off Burr
Break-off burrs occur at the stage when the material breaks off before the completion of cutting. So, these types of burrs are typical of drills and punches. Moreover, these burrs are sharp and have a rough surface. Most of them are found at the end of the cut or the hole they have been produced.
Tear Burr
They form when the material is tearing and not shearing as per expectations. When using a sharp tool, most of them are noted in processes that are impaired by improper tool positioning or worn-out instruments. These burrs are coarse and random. Besides this, they have an appearance of tearing on the fabric.
Cut-Off Burr
Chip formation is produced at the end of a part when it is removed from the large stock. It is usually done by sawing or cutting off. These edges are hook-like and aligned parallel to the cut-off direction. Moreover, they are formed when the last piece is made, and the cut is left slightly impure.
Parting Burr
Turning or lathe was seen as accountable for parting burrs. These burrs are produced in parting operations. So, it mainly involves the detachment of a piece from a workpiece. These burrs are commonly circular or semi-circular with the surface roughness. Moreover, voids are created when the tool cuts through the material. So, it can produce another item with a rough surface.
Factors Influencing Burr Formation
- Material Properties: When more abrasive material is used. Then the burrs produced are finer and less noticeable compared to when a softer material is used.
- Tool Condition: Tools are expensive, and their worn or dull condition leads to the creation of burrs. It is because of the inefficient cutting performed.
- Machining Parameters: Some of the individual parameters like cutting speed, feed rate, and tool angle may affect the size and the nature of the burrs formed.
- Workpiece Geometry: Geometric complexity can cause higher levels of burr formation. Because it is more challenging to cut out intricate patterns.
- Cutting Method: Possible types of burrs can also be the result of the different kinds of machining. These may include drilling, milling, shearing, etc or burrs can be classified according to their size. The type of method used dictates how exactly the material is shifted and, therefore, the resulting burrs.
Importance of Burr Removal or Deburring
So, the following points will help you understand the importance of deburring
- Safety: It reduces sharp surfaces that can lead to various damages during work handling.
- Functionality: Promotes correct adaption of the various parts. So, it can decrease friction and wear of the items.
- Aesthetics: Deburring enhances the appearance of the final product. So, it makes it attractive to the consumer.
- Performance: It eventually reduces the chance of early failure of parts. It is generally because of burr-caused stress ranges that can reduce the life cycle of parts.
Difference between Wet and Dry Processes of Deburring
The following table explains the difference between wet and dry deburring processes.
Wet Deburring
Wet deburring uses water or a chemical coolant is used in deburring. So, they can smooth and clean the workpiece. The liquid assists in the removal of particles left behind by the spinning and regulation of the temperature. So, it may result in improved surface texture. However, this option needs proper treatment of waste. Besides this, it may be relatively costly since coolants are used and the process requires more tools for operating with liquids.
Dry Deburring
Dry deburring uses abrasives without the presence of any liquid at all. This method is cheaper and time-saving, unlike the other methods. Because it requires the use of coolant and its disposal expenses. It minimizes scrap and rejects material. But it compels dust collection systems and cooling as dust and heat production may occur. Dry deburring is preferred when extra cleaning or cooling that comes with wet deburring is not required.
What Types of Materials Can Be Deburred?
Here is the description of all the possible materials, we can deburr.
Material Type | Description | Typical Deburring Methods | Value/Range |
Metals | Steel, aluminum, brass, copper, stainless steel. Removes sharp edges and improves finish. | Tumbling, abrasive blasting, sanding | Surface roughness: Ra 0.2-3 µm; Time: 10-60 minutes |
Plastics | ABS, polycarbonate, nylon. Smooth edges and prevent damage. | Tumbling, abrasive blasting, manual sanding | Surface roughness: Ra 0.5-2 µm; Time: 5-30 minutes |
Composites | Carbon fiber, fiberglass. Requires careful handling to avoid damage. | Abrasive blasting, water jet cutting, hand deburring | Surface roughness: Ra 1-5 µm; Time: 15-45 minutes |
Ceramics | Advanced ceramics. Specialized techniques prevent structural damage. | Tumbling, abrasive blasting, precision grinding | Surface roughness: Ra 0.1-2 µm; Time: 20-60 minutes |
Glass | Glass parts. Techniques prevent chipping and ensure smooth edges. | Abrasive blasting, edge grinding, chemical etching | Surface roughness: Ra 0.1-1 µm; Time: 10-40 minutes |
Wood | Hardwoods, softwoods. Smooths have rough edges and splinters. | Sanding, hand scraping, tumbling | Surface roughness: Ra 0.2-4 µm; Time: 5-20 minutes |
23 Different Methods for Deburring
So, let’s describe the different deburring methods along with their significance in depth.
Mass Finishing
Mass finishing is an important technique used in finishing large quantities of parts or components. It can run operations in batch, continuous systems, and in wet or dry processes. This process takes time for materials to set for the standard finishing directions. But, it greatly saves time, costs, and production labor. So, mass finishing can be done using different tools. These may include;
1.1. Rotary Vibrators
A rotary vibrator is a machine that creates circular motion to finish or polish the required part. The parts and abrasive media are located in a bowl that shakes. So, it makes the parts move and rub against the deburring media. This method is ideal for fine-finishing many at once small to medium-sized parts. These parts may require de-burring or polishing.
1.2. Continuous Flow Installations
Continuous flow installations are systems planned for processing the parts without interruption. Such installations enable parts to move through the finishing machine continuously. In most cases, it can be on a conveyor belt. It is mostly suitable in production lines where high production rates are required. Besides this, it will favor consistent deburring without having to employ the services of a human expert.
1.3. Drag Finishing Machines
Drag finishing machines move the parts through a container housing abrasive material. The parts are mounted on a feeder carousel or fixture. It helps translate them to the desired speeds and angles across the media forms. So, this method is useful for complex shaped or thin-walled and delicate parts. Because it can control the desired amount of deburring on the product.
1.4. High-Energy Disk Systems
High-energy disk systems use high-speed rotating disks to produce centrifugal forces. They would move the parts and media to engage with each other. This is much faster than the vibratory techniques and recommended for deburring small to mid-size components. Here, the motion with high energy is a fast and forceful finishing motion. So, it helps bring down the processing time.
1.5. Tub Vibrators
A tub vibrator is another piece of equipment that involves a rectangular or U-shaped tub. This tub then vibrates the parts and media. This method has many applications in big and long parts that cannot fit circular vibrators for their finishing. The tub itself can be loaded with a mix of parts and media. Then all the necessary deburring and polishing of parts’ surfaces will be equally distributed using vibration.
Manual Deburring
Manual deburring includes the use of hand-held or mechanized tools. These may include demurrers and grinders, brushes and files, and sanders. These tools help eliminate the burrs from the parts. It is a localized operation that does not involve the whole part. But it is applied where there are large tolerances for size. Deburring is vital for precision work for slow operations and parts formation. Deburring tools, i.e. scrapers, are widely used to scrape off burrs from most surfaces and grinders. These manual deburring tools may include;
2.1. Abrasive Paper
Sandpaper is a form of abrasive paper where the abrasive materials can be in different grits. It has to be employed to smoothen surfaces and edges of the metal. So, these burrs are rubbed off. If gentle friction is made on the metal surface using paper with the rough side facing the metal surface. Then the sharp edges are filed away or small pieces of metal are wiped off. This method is appropriate where the area to be coated is small and easily accessible and for ‘seamless’ finishing of the edges of metal parts.
2.2. Deburring Tool
These are specific hand tools commonly used for deburring. Besides this, they come with a handle and a cutting blade. So, it can either be rotated or fixed. This tool is dragged over the edge of the metal, with the blade trimming the burrs. This makes it versatile in shape. As for deburring, straight edges as well as holes with elaborate shapes require more precise control of the burr.
2.3. Files (Manual/Pneumatic)
Files are of an elongated shape. Here, some are straight or curved and have coarse teeth used for cutting metal. Turning files include hand files that are used with hand to slide across the metallic surface. So, it can scrape off burrs while the pneumatic files have the feature of power through compressed air. Moreover, they are forceful and fast. Files are recommended to be applied in detailed intricate jobs as well as hard-to-reach areas, for both small and large burrs.
2.4. Oilstone Deburring
An oilstone is another stone used to sharpen and smoothen metal. This type of stone has a fine grain. The metal part is sliding against the oiled surface of the stone. In the same manner that a carpenter uses sandpaper the tiny grains of stone are like blades. They shave off burrs and leave behind a smooth edge. Oilstones are most suitable for finishing and putting a sharp edge on the blade. So, they will offer a very smooth surface.
2.5. Blades Deburring
Scrapers are usually hand-held like the cutter which may be similar to a utility knife or deburring knife. While the thin, sharp part of the scalpel is used to shave burrs or any other rough protruding located on the metal. This method helps to remove burrs within a short period depending on the area to be deburred. Besides this, it can only be applied on flat or slightly curved surfaces where the individual has full control of the tool.
2.6. Steel Wool/Steel Balls Deburring
Steel wool is made of the fine wiry structure of steel. Here steel balls of small spherical and abrasive. Both are frictions against the shiny metallic plate to correct and smoothen the rough edges or burrs. Steel wool has more of an abrasive feel to it, whereas steel balls give quite rigorously higher abrasion. These tools are appropriate for the last grinding and polishing of the metal surface. So, they can eliminate any burr that may be on the surface.
2.7. Grinding Abrasive Discs Deburring
Abrasive discs are used on grinder machines and come in a variety of grit and material types. When pressure is exerted on the metal surface of a workpiece, a spinning abrasive disc grinds and burrs off. This method is most desirable when working on large surface areas that need a lot of mass removal or edges. Besides this, it may need serious material reduction and is normally applied in both industrial environments as well as workshops for enhanced deburring.
Semi-Automatic Deburring
3.1. Belt Sander
A belt sander is a portable piece of equipment that employs a long strip of material. This strip is abrasive and turns in a loop around two wheels. The rotating belt is applied in contact with the metal part. Then its abrasive surface abrades the edge and the surface, which removes the burr. This method is very effective in leading to the deburring of flat surfaces and straight edges. Besides this, it takes the shortest time possible and equal measures.
3.2. Grinding Wheel
A grinding wheel is a system in which a flat disc that is a ‘’sponge’’ of specified hardness is charged with abrasive particles. The metal part is brought close to the wheel. Then the face of the wheel works on the burrs and sharp edges of the steel. The blending process utilizes grinding wheels to remove the large burr and employs different shapes and sizes of wheels on the metal. So, it can complete the needful by removing a larger amount of material than another process in use.
3.3. Hand Drill and Grinding Head
A setup stems from holding a grinding head on the hand drill. This head has some kind of a small abrasive wheel or bit in it. When the drill is switched on the grinding head can rotate and be applied to the metal surface to cut off burrs. This method is more controllable and preferred where large machinery cannot access the area that needs to be cleaned.
3.4. Handheld Grinder
A handheld grinder is a kind of power tool. It is generally equipped with an abrasive disc or wheel. The grinder is hand-held and slid along the surface to reduce sharp edges and bumped surfaces also known as burrs. Handheld grinders can also be used on numerous kinds of metal parts and shape them with versatility.
Brush Deburring
Brush Deburring is a brushing process, done with the help of specific brushes for the deburring purpose only, and it removes burrs. These brushes are of different shapes and include circular, bowl-shaped, wide, side grinding, bottom grinding, linear, curved, and brushes in flexible holes. These brushes can be used both dry and wet, depending on the task that is to be accomplished. These are specially constructed to follow the curvature of the workpiece. So, it is good for deburring curved surfaces and corners. Moreover, the flexibility and the availability of the types of brushes help deburr the complex and non-uniform shapes.
Punch Press Deburring
Punch Press Deburring incorporates the use of a punching machine with different die to knock off the burr in the metal parts. The tools are classified into rough blanking dies tool, fine blanking demise tool, and sizing demise tool. This method is quite efficient when a large number of parts have to be worked on as the punch press can trim burrs at a fast rate. But complex-shaped parts required a specific die.
Magnetic Polishing Deburring
MD is a deburring process that uses a magnetic field to position small stainless steel pins that polish and deburr the metal parts. They are most suitable when working with complex parts. In particular, the magnetic field movement also makes pins rotate gently. So, it enables the brushes to pass across the surface in a polishing manner even if the place is hard to reach. This method is most suitable for accurate processes and accurate finishing of fragile parts.
Thermal Deburring
Thermal Deburring requires placing parts in a closed controlled environment where a combustible gas is burned. It does not support combustion such as methane and an oxidant like oxygen This causes a high-temperature reaction which removes burrs on the parts. This process is fast and perfect for degassing internal and external burrs. However, it has drawbacks that it needs delicate control and proper washing of the components after treatment. So, it can eliminate the ash from the burning process. It is especially useful where it is difficult to get easy access to the interior of the part for traditional mechanical deburring.
Abrasive Flow Deburring
- Jet Type: This method involves spraying a high-pressure abrasive substance on the surface of the parts to remove any burrs. The abradant typically in the form of a slurry is projected at high velocity against the surfaces. This surface contains the burrs and they are washed away.
- Fluid Extrusion Type: This method includes directing a thick liquid that is loaded with solid grain at a part either through it or around it. The pressure and the abrasive nature of the fluid lead to the removal of burrs as the fluid goes through the component’s interior channels or exterior surfaces. Both methods are equally good in deburring parts that have intricate shapes and blind holes.
Cryogenic Deburring
Cryogenic Deburring includes the use of liquid nitrogen to freeze the parts and thereby make the burrs break. After the part has been frozen a mechanical method like tumbling or blasting is applied to remove the now spongy burrs. It is especially suitable for the deburring of rubber and plastic parts. As the elasticity of the mentioned materials reduces at low temperatures. Therefore, the burrs are easier to remove without affecting the rest of the part.
Electrolytic Deburring
Electrolytic Deburring uses certain electro-chemicals with which burrs dissolve. They are immersed in a solution known as electrolyte, to which electric current is passed through. When the electrical current passes through the liquid the burrs become dissolved in the solution to get rid of them. This method is accurate and is highly preferred for deburring of also complex geometries and areas that are very hard to reach. Moreover, it gives an allowance for a high level of control throughout the deburring process so that the parts will not be overburdened.
Plasma Polishing Deburring
Plasma Polishing Deburring uses ionized gas or plasma. So, it can remove burrs and polish metal surfaces. The high-energy plasma is directed at the parts, where it smooths and refines the surfaces and removes burrs in the process. This method is effective for achieving a high-quality finish and is suitable for parts that require a smooth and polished appearance. Plasma polishing deburring can handle intricate and delicate parts without causing damage. So, this makes it ideal for components that require both deburring and surface finishing.
High-Pressure Water Deburring
High-Pressure Water Deburring includes the use of water jets to remove burrs with extremely high pressure applied on the parts. This method is especially useful for large and intricate shapes, which water jets can get to better than other methods. Moreover, they can disperse into the interior spaces of the shape. Furthermore, free from abrasive particles that may contaminate the surface, this method delivers gritty and preciseness on the workpiece, especially where cleanliness is paramount.
Ultrasonic Deburring
Ultrasonic Deburring applies high-frequency sound waves for cleaning media to remove burrs from parts. This process’s sound waves cause the formation of bubbles in the liquid which collapse with huge force to clean and deburr the peeled part. It is also relatively mild and thus appropriate for usage on fragile and complex components. These parts may be damaged by heavy deburring procedures.
Mirae Powerful Ultrasonic Deburring
MPUD is a concentrated high-power ultrasonic deburring for additionally more rigorous deburring applications. This method applies higher ultrasonic power to tackle hard, caked, burr, and stronger materials of different Kindles. It integrates the feature of ultrasonic deburring with enhanced power to result in the cleaning and deburring of the parts that may require higher energy.
Tumbling Deburring
Tumbling Deburring puts the parts into a tumbling machine that has abrasive media. To achieve the necessary equability, the parts, and the media ‘dance’ in the casing and polish the surfaces as well as knocking out the burrs. This process is used for mass deburring of numerous components during one cycle and it is specifically suitable for the attainment of smooth and round edges of the work pieces. The tumbling action also means that there is uniformity when treating a large number of parts.
Vibratory Deburring
Vibratory Deburring is a process in which a container full of abrasive media vibrates to remove burrs from parts. The vibration compels the parts and the media to mix over time. So, it can smooth and deburr the parts’ surfaces. This method of deburring is ideal for tender and intricate components because the action that is exerted is not only wea. But it penetrates areas that cannot be reached by other forms of deburring. It also enables the programmer to achieve minute control over the degree of deburring together with the time taken to achieve this.
Sandblasting Deburring
Sandblasting Deburring operation utilizes a pressurized abrasive substance including sand. It is sprayed at the surface of the part to eliminate burrs. These particles act on the surface of the parts by gashing off the burrs with the abrasive material. This method is very useful for quick and efficient relieving of small roughness and cleaning of the surface. But it is very aggressive on soft materials, that can be gouged. It is most appropriate for rough products as it applies abrasion force on the material.
Shot Blasting Deburring
Shot Blasting Deburring requires that the surface of the parts be projected with a shot, which is small steel pellets. The force that strikes the surface of the parts is adequate to knock off burrs and clean the surface. Hence, this is useful where the operations require heavy deburring and cleaning of the surface to have a uniform texture. It is often supplied to components made of hard materials that are capable of withstanding the force of the pellets.
Engraving Machine Deburring
Deburring All processing is done with engraved precision to cut or engrave the material to remove the burrs. The use of this method provides higher accuracy and results in better control. So, it makes this method suitable for parts that need keenness on the de-burring. These tools can be set in such a way that only the burrows will be shaved off without affecting the size and other attributes of the part. Besides this, it helps improve its finish.
CNC Ceramic Deburring
CNC Ceramic Deburring uses computer numerically controlled ceramic deburring tools that delicately de-bur the parts. The CNC Machine deburring process is reliable for the production of parts with close tolerance and polished surface finishes. Because the CNC system is accurate and consistent. Precisely, the usage of ceramic tools enables fulfilling the deburring tasks with highly automated and accurate degrees on various kinds of materials. Moreover, its durability makes it possible to avoid frequent replacement.
Robot Arm Deburring
Robot Arm Deburring involves the robotic arms that have the occupancy of deburring tools. It gives accurate results because the parts are held by the robotic arms. So, once certain paths are set, the pressure that is applied is also predetermined. Robot arm deburring is more beneficial in the case of complicated geometrical shapes of the parts. Here deburring can be done systematically and continuously. It also improves production efficiency because deburring is partly mechanized. Thus it minimizes the number of workers who get to engage in the production process. At the same time, it guarantees that all the products that are produced in large quantities will be of high quality.
Mechanical Deburring
Mechanical deburring utilizes machines to perform the basic deburring on workpieces. It has a level of control over the operation. So, these operations can be done using different tools. They may include:
21.1. Barrel Tumbling
It may include placing parts into a chamber with abrasive media and special compounds. Barrel tumbling is of two types, i.e. wet barrel tumbling and dry barrel tumbling. Wet tumbling on the other hand employs the use of water. Because it acts as an intermediate that washes the residues. Dry tumbling uses dry media such as sand or other organic materials to take the residues from the surface.
21.2. Centrifugal Tumblers
It can be installed on a turret. It’s one set that revolves in one direction while the other one revolves in an anticlockwise direction. So, the abrasive forces are doubled cutting the deburring time.
21.3. Vibratory Deburring
Like barrel tumbling, here, the chamber vibrates. So, it can create motion and agitate the contents for the required finish.
Waterjet Deburring
Waterjet deburring adopts high-velocity water jets to grind burr and contaminant from a work surface. It is far more non-aggressive than waterjet cutting. Besides this, it does not require any high pressure and is not harmful to the material. The waterjet deburring can remove thin and loosely attached burrs. It also guarantees the final product is free from oil contamination and other residues.
Sheet Metal Deburring Machine
The abrasive cloth wire wheel run through high-speed rotation (self-rotation) for scraping, grinding, and polishing the 90-degree edges of sheet metal parts(2-5mm thickness). This equipment utilizes the self-rotation and revolution of the abrasive cloth wire wheel to uniformly remove burrs on the same face or nearly the same face of the sheet metal parts. The slight friction applied to the edge after deburring will not affect the product dimensions, thus enabling efficient and precise processing of the sheet metal parts.
Different Tools Used in Deburring
Here are certain tools that are specifically used in deburring;
Hand Deburring Tools
- Deburring Blades and Knives: These are handheld tools that are great tools for deburring. So, they offer great results when it comes to removing burrs from edges as well as from holes.
- Files: Manual files are made of metal and they are utilized to level the freshly cut edge. They exist in various forms and can be used in various capacities.
- Abrasive Pads and Brushes: These are tools for deburring light burrs and can as well be handled by hand and are used in fine finishing.
Mechanical Deburring Tools
- Rotary Deburring Tools: Among these are electric or pneumatic tools that are utilized with rotating deburring bits or abrasive wheels. They are employed in large area de-burring or in materials, that are harder than the ones for fine de-burring.
- Vibratory Tumblers: Components are put into an ultrasonic tank full of abrasive particles and this causes them to descale and polish through oscillation.
- Centrifugal Disk Finishers: Some of these machines utilize centrifugal force to handle parts and abrasive media, as well as to accomplish high-speed deburring as well as polishing.
Automated Deburring Tools
- Robotic Deburring Systems: Deburring tools integrated into robots are capable of dealing with intricate parts. This ensures that they are treated uniformly to the highest standard with low levels of manual input.
- CNC Deburring Machines: These machines incorporate deburring techniques into cnc narrowing centers to provide for deburring in the course of manufacture.
Thermal Deburring Tools
- Thermal Energy Method (TEM): This process involves passing through combustible gas that is raging through. It helps in burning burrs and other harsh geometric features that may be hard to abrase from the part without affecting the part in the process.
Electrochemical Deburring Tools
- Electrochemical Deburring (ECD): This one employs the use of electrochemical reactions to delouse work-piece sur faces of burrs. The part is put into an electrolyte and an electric current is induced a process that dissolves the burrs.
Ultrasonic Deburring Tools
- Ultrasonic Deburring: Air ultrasonic cleaning with abrasive grain involves the application of high-frequency sound waves in water. So, it can eliminate burrs on sensitive parts and subassemblies.
Water Jet Deburring Tools
- High-Pressure Water Jet: It uses a focused and high-pressure water jet to remove burrs from the surface of the part most especially the compound surfaces.
What are the Different Deburring Media?
Deburring Media | Description | Typical Applications | Values |
Ceramic Media | Durable, aggressive, and often mixed with compounds. | Heavy deburring, large burr removal. | Grit sizes: 10-240 |
Plastic Media | Softer, less aggressive, versatile. | Light deburring, polishing delicate parts. | Grit sizes: 10-320 |
Steel Media | Durable, reusable, provides a burnishing effect. | Heavy-duty deburring, metal polishing. | Grit sizes: 30-180 |
Organic Media | Includes walnut shells, and corn cob grit. | Light deburring, polishing delicate materials. | Grit sizes: Coarse to fine |
Abrasive Slurry | Abrasive grains in liquid, customizable. | Fine deburring, surface finishing. | Concentrations: 1-10% by volume |
Dry Powder Media | Includes sand, and fine particles. | Light deburring, non-liquid environments. | Grit sizes: 20-120 |
Pre-formed Shapes | Various shapes for improved contact. | General deburring, part-specific finishing. | Shapes: Cylinders, stars, triangles |
Aluminum Oxide | Hard, sharp-edged, aggressive. | Heavy deburring, surface preparation. | Grit sizes: 24-600 |
Silicon Carbide | Very hard, sharp, aggressive. | Heavy-duty deburring, cutting hard materials. | Grit sizes: 40-1000 |
Zirconia | Extremely durable, often combined with other abrasives. | Heavy-duty deburring, grinding tough materials. | Grit sizes: 30-600 |
Glass Beads | Spherical, peening effect. | Cleaning, light deburring, surface strengthening. | Sizes: 50-800 microns |
Polyurethane Media | Soft, flexible, minimal material removal. | Polishing, light deburring of delicate parts. | Grit sizes: Fine to medium |
Synthetic Media | Man-made, specific characteristics. | General deburring, surface finishing. | Varies by formulation |
What is the difference between Deburring and Tooling
Tooling and deburring are two different processes. Here is the table that will showcase the difference between them.
Aspect | Deburring | Tooling |
Definition | Removing burrs, sharp edges, or rough spots from materials | Creation and use of tools, molds, and equipment for manufacturing |
Purpose | Improve surface finish, ensure safety, enhance functionality | Produce tools and molds for shaping, cutting, forming, or assembling materials |
Methods | Tumbling, Abrasive Blasting, Manual Sanding, Water Jet Cutting, Thermal Deburring | Machining, Casting, Forging, Injection Molding, Stamping |
Materials | Metals, Plastics, Composites, Ceramics, Glass, Wood | Metals, Plastics, Composites, Ceramics, Wood |
Stage in Manufacturing | Post-processing step to perfect parts | Initial stage to set up manufacturing processes |
Objective | Remove burrs to improve finish, safety, and functionality | Create tools and molds for manufacturing parts |
What is the difference between Tumbling and Finishing?
Here is the detailed table for the difference between tumbling and finishing
Aspect | Tumbling | Finishing |
Definition | Rotating the drum with abrasive media smooths the parts. | Techniques like polishing and sanding enhance surface quality. |
Process | Parts and media tumble together to remove burrs. | Various methods improve appearance and smoothness. |
Suitable For | Batch processing of complex shapes. | Custom surface finishes and high-quality results. |
Output | Removes burrs and sharp edges. | Improves surface appearance and smoothness. |
Typical Media | Ceramic, plastic pellets. | Polishing compounds, sandpaper, beads. |
Applications | High-volume deburring. | Precision surface enhancements. |
Applications of Deburring
So, let’s discuss its applications in different fields;
- Automotive Industry: Deburring enables the clean and effective functioning of parts. These parts are used mechanically and incorporated within an engine. They may include gears and other important parts of an engine.
- Aerospace Industry: The need that can be over-emphasized is the deburring of aircraft parts. These are turbine blades and structural parts.
- Medical Devices: Surgeries, instrumentation, implants, and almost all orthopedic instruments and devices also need deburring. So, they can avoid invasions and unfathomable functioning.
- Electronics: Deburring helps eliminate shorting out in printed circuit boards (PCBs) and other items in this category.
- Metal Fabrication: It reduces the sharp edges of the metal parts. Besides this, it increases the safety, handling, and quality of the part.
- Plumbing and Pipe Fittings: Appropriate deburring guarantees that there will be tight flanges, and no leakage in the plumbing and the pipe fittings.
Advantages and Limitations of Deburring
Advantages
Here are some benefits of deburring; i.e.
- Improved Safety: Disabling sharp edges minimizes the chances of injuries while handling and or using the products.
- Enhanced Performance: Deburred parts show better performance than other parts. Besides this, it also possesses greater durability.
- Better Surface Finish: Deburring increases the beauty or design and improves the part efficiency.
- Prevents Machinery Damage: This enables reducing burrs that cause wear and tear of machinery and other working tools.
- Ease of Assembly: Components assemble more accurately and easily into other parts after deburring.
Limitations
So, the following are the limitations of sheet metal deburring;
- Increased Costs: Deburring generally adds to manufacturing costs.
- Time-Consuming: It can take time to complete the parts. Besides this, it is used in creating complex parts, it may take even longer.
- Over-Processing Risk: If deburring is done incorrectly. Then it will alter the dimension and functionality of the concerned part.
- Equipment Wear: Equipment and other machinery used for deburring can be prone to wear. Moreover, it may require higher maintenance expenses.
- Skilled Labor Requirement: Some of these methods are difficult to use. They may need skilled workers, which in turn increases the operation expenses.
Conclusion
In conclusion, sheet metal deburring is one of the crucial steps contributing to manufacturing. It plays a vital role in the safety, functionality, and product appearance. So, there are several methods of burr removal. They may range from the traditional methods to the complex robotic and electrochemical procedures. These methods can fit the production requirements and difficulty level. When appropriate deburring techniques and materials are chosen, the manufacturing company can produce high-precision and reliable parts. These parts tend to meet the design and operational needs and requirements. Moreover, they will ultimately enhance the efficiency of the product.
Frequently Asked Questions
Q1. What types of materials can be deburred?
Deburring can be done on all types of materials. But it mainly encounters metallic or plastic surfaces. Deburring can be done in virtually all material types inclusive of metals. These may include steel, aluminum, brass, plastic, glass, and composites.
Q2. How do I choose the right deburring method for my parts?
It depends on the two things, i.e. the material and size with detail of the part. Besides this, it also depends on the surface finish and the number of parts. So, whatever method you choose, it is advisable to consult a deburring specialist.
Q3. What are the benefits of deburring?
Deburring increases part safety by eliminating sharp edges and increases functional performance. Besides this, it reduces or increases mating tolerance, and improves the part appearance.
Q4. Can deburring be automated?
Yes, deburring can be mechanized with the help of machines and equipment. This may include tumbling barrels, vibratory finishers, and robotic deburring machines. They make the process much faster and more accurate especially in mass production.
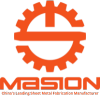