TOP 21 Sheet Metal Assembly Techniques For Sheet Metal Parts
Table of Contents
ToggleSheet metal assembly technique is important and common in many diverse areas of the working world. These areas may include the automotive industry, aerospace engineering, and manufacturing. Out of all of these options, riveting can be reliably spot out as a diverse and number one way of joining the sheets of metal. Moreover, it offers many advantages riveting has high strength and high durability. Besides this, it protects against vibrations. So, in this article, we will discuss the 21 riveting techniques that are common many in operations involving sheet metals.
What Does Sheet Metal Assembly Mean?
Sheet metal assembly means grouping separate parts that assemble together to make sheet metal. So, it can make integrated and complex structures from them. This often requires the employment of numerous techniques, i.e. riveting, welding, adhesives, or mechanical fasteners. So, it can achieve constructive interconnection of the two sheets. These types of assemblies are popular in the automotive, aerospace, construction, and manufacturing industries. They fit best where you often need light, strong, permanent, and economical structures..
21 Most Commonly Used Riveting Sheet Metal Assembly Techniques
So, here are the most common sheet metal riveting assembly techniques, which are common in sheet metal assemblies. Let’s discuss all these in detail.
Sheet Metal Screw +Tapping Assembly
In this technique, we use sheet metal screws and nuts to hold two sheet metal parts together. It is usually completes in a way that forms a continuous thread on the exterior of the joint. One of these two parts likely has a thread hole. The second part has a through-the-hole. in this way, you can easily pass the sheet metal screw through it and is also screwed into the next part having a threaded hole. Thus, fastening the two parts together.
Advantages
- Ease of Disassembly: They are easy to dismantle and replace when you need.
- Adjustability: Enables modifications to be made in case the size of the component,
- Strength: It provides greater holding power and you can use it in all kinds of loading conditions.
Disadvantages
- Vibration Sensitivity: This can be loose over time because of vibrations that are usually present in the surrounding environment.
- Corrosion: It rusts quite easily if you do not well handle it in terms of the treatment to be given to the metal.
- Complexity: The holes must align with each layer – a process that could take time especially when working with many layers.
1.1 Sheet Metal Hole Flanging + Self-Supplied Screw Assembly
In this method, out of the two sheet metal parts, one will have holes with internal threads prepared on it. You can manufacture it using threading. The threading forms interlaced threads inside the hole. So, it can engage the screw easily. The other part usually has a through hole in it as a result. Now, you can pass the screw through hole and it will screw onto the threaded hole. These are threaded fasteners. So, as the screw is turned to bring two objects together, create threads in the other part to interlock them firmly.
Advantages
- Strong Hold: Offers the client an through a reliable link.
- Ease of Use: Easy to apply in comparison to other methods of assessment and feedback.
Disadvantages
- Thread Wear: There are areas where you can use thick threads which may get wearying with time thus having low tensile strength.
- Vibration Sensitivity: Variations deform it easily and requires a rigid frame to minimize these effects.
1.2 Sheet Metal Hole Flanging + Tapping + Screw Assembly
Here one part is drilled through and the other part is drilled with the screw thread hole. However, in this case, you make the threaded hole through a tapping process. This means that the metal is first drilled to make a hole. So, then we need to create a thread by passing a tap. Tapping is a process that uses a tap which is a tool requires to cut threads in the material. So, it can facilitate the requirement of threading by the self tapping sheet metal screw. After threading, you pass the screw through the hole. After that, it is screwed into the threaded circular hole to hold both parts together.
Advantages
- Strong Connection: The wireless technology provides a temporary or permanent connection that is stronger and more dependable.
- Cost-Effective: It is usually less costly as compared to other approaches or strategies.
Disadvantages
- Time-Consuming: Incorporates prerequisite drilling and tapping processes into the structure that is implanted.
- Tool Dependency: Requires individual implements for threading and tapping.
1.3 Screw and Nut Assembly
In this assembly method, we use screw and nuts and bolts. Both the sheet metal parts have through holes in them for bolt passage. A screw penetrates through a hole in one part. Then, you can fasten it on the other with the help of a nut. So, it has a thread area that you can use as a means through which the screw can grip onto the nut. So, it can hold it securely in place. This makes it very convenient for assembling and disassembling. Thus, it makes it ideal for use where often maintenance or changes of certain settings are necessary.
Advantages
- Ease of Assembly: Cons – Ease of assembly – The process of assembly particularly when engaging lem producers is very easy.
- Reusable: It is also easy to disassemble them and reuse the main components or subassemblies and assemblies that have been put in place.
Disadvantages
- Vibration Sensitivity: Nuts can come unscrewed over time when you use them.
- Requires Access: Requires access to both surfaces for its construction.
1.4 Double-thread Screw + Nut Assembly
You can use double thread screw if one of the assembled components is thicker. So, you can further process it through the hole. In this style, one part of the stud has external threads. While the other part is threaded on the other side of the nut. So, you attach the part of the shaft with the threaded hole by tapping it. The stud is then screwed into the hole. On the other end of the stud, there is a nut which is then tightened to join the two parts. Moreover, the presence of studs is advantageous. So, it creates a stronger fixing for applying high force during assembling.
Advantages
- Strong Hold: Most appropriate where strength could be an issue.
- Reusable: This means that once you reach the end of the cycle, you can reuse the product’s parts and subassemblies.
Disadvantages
- Complex Assembly: It’s easier to say than to do, and then you screw up the nuts.
- Requires Precise Alignment: You need to position and orient the holes properly so they work correctly when you assemble the sandwich.
Sheet Metal Hole Flanging +Press Riveting Assembly(Sheet Metal Self-Riveting without rivets )
It uses both hole flanging and press-fit riveting techniques to assemble two or more sheets of metal. The process involves creating a flanged hole on one metal sheet and a regular hole on another sheet. The metal sheet with the flanged hole is you insert into the sheet with the regular hole. A round punch can be use to tightly press the flanged edges of the first sheet onto the second sheet, securing them together firmly.
Advantages
- Strong Joint: You don’t need any rivets; this provides a very strong and dependable junction.
- Durable: It works well in conditions characterized by vibrations or dynamic loads.
- High efficiency: Using round punch molds for riveting ensures high production efficiency.
Disadvantages
- Complex Process: Frequently needs x-ray sectioning and separation of flanges and subsequent riveting.
- Special Tools Needed: Usually needs special tools or possessions to have to efficiently complete the job.
- Quality control:Quality is difficult to control.
- Disassembly:One-time assembly, not detachable.
Sheet Metal Blind Rivet and Swaged Pin Assembly
This category comprises procedures for fastening two or more parallel flat surfaces of sheet metal through the use of rivets, nuts, or a combination of both. The main objective is to make the structural connection between the two members as firm and sustainable as possible to different forces and stress.
Advantages
- Strong and Durable: Forms a durable and lasting bond between the two joints to be joined.
- Cost-Effective: Generally inexpensive.
Disadvantages
- Permanent: Not easily disassembled.
- Tool Dependency: This has to be riveted in the right place and must be done using some explicit tools.
3.1. Blind Rivet Assembly
As are called pop rivets or blind rivets, which a rivets designed to be inserted from one side of the workpiece This type of riveting is particularly suitable where access is limited to one side of the assembly only. Here’s a detailed breakdown of the blind rivet assembly process: Here’s a detailed breakdown of the blind rivet assembly process.
The process involved in Blind Riveting
1. Hole Preparation Process
- Drilling: A small hole is made to pass through the sheets of metals to be joined and the centers of this hole should be perfectly aligned and these holes are slightly larger than the diameter of the rivet.
- Deburring: The edges of these holes are smoothed over to eliminate angularities or sharp edges that may hinder the integration.
2. Insertion of the Rivet Process
- Placement: A blind rivet passes through the respective holes in the sheet metals with their projecting ends lined consecutively.
- Mandrel: The rivet was divided into two parts which include the body of the rivet and the mandrel (a pin runs through the body of the rivet).
3. Setting the Rivet
- Rivet Gun: A rivet top or a handheld tool is used to remove the mandrel from the rivet body by pulling it through the body. There is a re-forming of the blind end as the mandrel is pulled and this results in the formation of a tight rivet joint.
- Breaking the Mandrel: After the individual head expands and fits securely around the other sheet to join the two metal pieces, the mandrel breaks off at a specific length to leave the body of the rivet to complete the connection.
Advantages
- Ease of Installation: Said to be relatively easy to install and may not need special training to operate.
- Versatility: This type of cutter can cut through most material types and thickness levels in the market.
Disadvantages:
- Limited Strength: In general, they are less effective than solid rivets since the fastening takes place outside the plates.
- Not Reusable: Rivets once inserted cannot be as differing from other approaches of fastening, it once installed cannot be reused.
3.2. Swaged Pin Assembly
Specifically, ring groove nut assembly employs lockbolts that are ideal for delivering strong, and anti-vibration joints. This assembly is quite popular due to its resilience in performance and the construction of rugged, long-lasting parts.
So, it uses the following processes.
- Hole Preparation: The former holes should be drilled through the sheet metal but they should match the diameter of the lockbolt.
- Bolt Insertion: The lockbolt is passed through two holes one of which is lined up with the other to lock the pieces together.
- Setting the Bolt: A collar is fitted at the end of the bolt that protrudes beyond the side on which the nut is screwed.
Advantages
- It offers superior and highly reliable interconnection points for the various components.
- Good quality of antivibration /dynamic load characteristic.
Disadvantages
- Complex Assembly: Some designs may require very accurate hole placement in the tool, creating potential problems for use in other applications.
- Special Tools Needed: It often cannot be carried out using common equipment or with just the bare hands.
Pressure Riveting Sheet Metal Assembly Technique
Pressure riveting technique involves the use of pressure to deform the rivet or fastening component, ensuring a tight and secure fit within the sheet metal. This method is commonly used for its efficiency and reliability in creating strong joints.
4.1 Pressure Rivet Assembly
Pressure rivet assembly is a process where rivets are pressed into the sheet metal under high pressure. This method ensures that the rivet securely attaches the sheets by deforming the rivet material to create a tight fit. So, here are pressure riveting processes;
- Hole Preparation: Here you first drill or punch the holes through the sheet metal parts. So, they can join easily.
- Rivet Insertion: Place the rivets in the holes you made.
- Pressure Application: A press or riveting machine applies pressure to the rivets. Then it deforms them and secures the joint.
Advantages
- Creates strong and permanent joints.
- Efficient for mass production with consistent results.
Disadvantages
- Special Equipment: This work needs special riveting machines.
- Not Reusable: Rivets are used and fixed permanently when used on a certain surface or structure, they cannot be reusable.
4.2 Riveted Press Nut + Screw Assembly
So, here are the pressure nut assembly processes;
- Hole Preparation: Holes are drilled or punched into the sheet metal to match the nut’s outer diameter.
- Nut Insertion: Nuts are placed in the prepared holes.
- Pressure Application: A press or riveting machine applies pressure to the nuts, causing them to embed into the sheet metal. So, the nuts may have serrations or knurls that bite into the sheet metal to prevent rotation.
Advantages
Strong Threads: Offers rigid and concrete themes that can be used again.
- High Resistance: Good extracting power and applied torque.
Disadvantages
- Complex Process: Demands correct pressure application that is sometimes very tricky to achieve.
- Special Tools Needed: Required equipment for insertions must be special.
4.3. Clinching Stud+Nut Assembly
In this technique clinching is a process of joining sheets of metal for industrial usage that does not require heat forming and the use of extra hardware to bind the metals together. This process entails bending the material to create a locking ability between the components, hence ensuring a compatible bond
Here are some processes;
- Component Alignment: Organized structure: sheet metal components are oriented for construction in a particular type of configuration.
- Pressing Operation: A clinching machine that is provided with the necessary die and /or punch is employed to provide force at the Jointing zone on the metal bodies.
- Forming Process: The material in the joint area overlaps and fits one into another with enhanced stiffness to produce a strong joint that does not require the use of other hardware or heat.
- Completed Assembly: The additional metal pieces are now interconnected and reinforced with each other in such a way that they are tightly bonded together.
Advantages
- No Additional Fasteners: Reduces material and assembly consumption: because it does not need any rivets, screws, or welding rods to join the pieces.
- Cold Forming Process: It does not impose heat on the material to ensure that elements are not distorted or harmed because of heat.
- High Strength: Establishes a stable connection between materials and ensures their ability to sustain mechanical loads and vibrations.
Disadvantages
- Tool Dependency: Has to be clinched with special tools that are not easy to get.
- Limited Applications: It is not recommended to use all kinds of materials and all thicknesses.
Pressure nut assembly involves embedding a nut into the sheet metal using pressure. This creates a threaded insert that can accept a bolt or screw, providing a strong, reusable fastening point.
Rotary Riveting Technique
The sheet metal rotary riveting assembly is an apparatus used to fasten thin sheet metal using rotary riveting and assembly. Rotary riveting is a method of assembly where the user rotates a tool that places rivets into preformed holes to join two or more sheet metal pieces. This is a production technique often used in industries such as automobile industries that necessitate high-velocity and even mechanized assembly.
.
So here are its processes
Hole Preparation: The specific locations at the metal components are drilled or punched to make space for rivets ;
- Rivet Insertion: Rivets are installed in the drilled holes at the touching parts of two intersecting metal parts.
- Rotary Riveting Tool: The rivet heads are then installed and a rotary riveting tool is brought into contact with the rivet heads and operated.
- Deformation and Joining: When the heads of the rivet protrude on the surface, the flow and pressure force the metal pieces to fit together forcefully. The rotation of the tool helps apply an equal amount of pressure in all directions to dome the heads of the rivet and join all the assemblies uniformly.
Advantages
- Speed: Inexpensive, lightning-fast production that suits mass production best of all.
- Uniformity: It ensures that the quality and strength of joints are consistent between different parts so that failures and loose joints are minimized between them.
- Strength: Offers excellent performance, ensuring the connections are stiff and strong to fit various applications.
- Automation: Suitable for use in automated assembly line applications where labor costs can be minimized while the efficiency is greatly improved.
Disadvantages
- Tool Dependency: Resembles a hub but must be assembled using special rotary riveting tools.
- Permanent: Not easily disassembled.
Rivet Assembly and Sheet Metal Self-Piercing Assembly (SPR)
Sheet metal self-piercing assembly (SPR) with rivet assembly is a process of assembling two or more metal components where self-piercing rivets will be employed to join. This working technique proves useful as it ensures that the joints that are produced will be extremely firm and rigid and there is no need for pre-drilled holes or other hardware to be used.
So here are some processes it follows
- Component Preparation: Metal parts are placed in the correct orientation for treatment in a value-added way that would enable their assembly.
- Self-Piercing Rivet Placement: Self-piercing rivets are conical-shaped metal parts inserted in the joint zone and include the rivet body and the mandrel.
- Pressing Operation: To reach the desired forces, a hydraulic or mechanical press is usually applied to the rivet heads and the mandrels get activated.
- Mandrel Break-Off: On completion of the flow of the rivet material around the mandrel, the surplus material is severed at various status locations to produce the rivet heads.
- Completed Assembly: Ended jointed metal members guarantee that the mechanical parts are strongly connected and can sustain heavy loads.
Advantages
- High Strength: Establishes highly stable joints, mechanically reliable, and able to support mechanical loads and vibrations.
- No Pre-Drilled Holes: Cuts the necessity of pre-drilled holes which contribute to the saving of time and money during production.
Disadvantages
- Tool Dependency: Neo-adaptive information systems have specialized self-protection requirements called SPR tools.
- Permanent: Not easily disassembled.
FDS (Hot Melt Self-Drilling Drill) Assembly
It is a type of drill that contains a system of reinforcing refunds using heat melting and also it is a driving device that is used in the manufacturing industry.
FDS or hot melt self-drilling drill is a process that is employed to fasten the sheet metal components by drilling and threading the screw in the same pass. This method has the following benefits: It allows making perfectly tight joints, capable of bearing the load; There is no need for preliminary boring of holes and other fasteners.
Process;
- Component Alignment: Electroformed metal sheets are arranged in the fashion that is planned for their use in the mechanical process.
- Drilling and Fastening Operation: The self-drilling screw fitted in the FDS tool is placed above the joint section of the two metallic parts. The tool performs the function of creating a pilot hole and making the self-drilling screw to be held on the material being joined.
- Screw Installation: One such fastener is the self-drilling screw that drills through the upper metal part creating threads on the adjoining lower part to secure the connection.
- Completed Assembly: Both sets of metal pieces have now been successfully soldered and they tightly fit and complement each other, producing a rigid construction.
Advantages
- No Pre-Drilled Holes: Saves time and money given that one does not have to drill holes at the sides of the components to be joined before assembly.
- High Strength: Develops strong and long-lasting bonds conducive to withstanding Mechanical loads and vibrations.
Disadvantages
- Tool Dependency: This needs to be done with FDS-specialized tools.
- Complex Process: This is very dependent on heat and pressure, which must be tightly regulated.
Sheet Metal Snap-On Assembly
Sheet metal snap-on assembly is a fastener part that is used in joining sheet metals where tabs and slots are extended to enable the creation of an interlocking pattern so that one part would automatically engage the other. This method makes it easier to disassemble and readably assemble again without requiring any other fixings or implements
Here are some of its processes
- Component Alignment: Sheet metal parts are arranged in the particular manner as required in assembling about the core component.
- Snap-On Connection: Consistently, localized bulging (protrusions or snaps) can be created on top of one component while recesses (receptacles) on the other component. Thus, the final connection includes the components being assembled, and the snaps lock into the receptacles for a tight snap fit.
- Completed Assembly: The joined sheet metal components are secured with a variety of fasteners so that in the assembled condition the parts are well-fixed and can easily be disconnected if required.
Advantages
- Ease of Assembly: Ease of construction they can dismantle and assemble within a short time and have a simple design.
- Reusable: Products are easily separable for recycling and there is provision for examining each part.
Disadvantages
- Limited Strength: Do not need to be used where high loads are required.
- Alignment Required: Care should be taken to ensure that the adherent and the impacted area have the right shape and size so that the adherent fits properly.
Welding Sheet Metal Assembly Technique
Welding sheet metal assembly is one of the most effective joining methods that targets to joining sheet metal parts by applying force and heat to produce a butter end and permanent union between the metals. This technique has the following benefits: It produces highly rigid and robust connection systems that enable structures to resist mechanical loads and vibrations.
So, let’s have a look over its processes;
9.1. Manual Welding Technique
As earlier explained in automatic welding, manual welding requires a professional welder to move a welding torch to the area of the joint and then apply heat and pressure to melt the base metal as well as the filler material to form a weld bead. Manual welding as the name suggests is superior in flexibility and accuracy since operators can readily put into practice different working conditions of welding for different material thicknesses and joint types.
Advantages:
- Flexibility: applicable materials and joints For and suitable types of.
- Precision: High precision for the welders to operate since the pieces to be joined require intricate operations.
Disadvantages:
- Labor-Intensive: There is strictly a demand for skills leading to higher expenses.
- Slower: Customizable and takes longer time as compared with other forms of automated welding technology.
9.2. Robot Welding Technique
Robot welding sheet metal welding technique also known as automatic welding implies the use of welding robots together with welding torches to carry out some welding activities. It provides reliable output through its ability to maintain uniformity and accuracy in the welded product and it also cuts down on labor expense as compared to human-operated welding processes.
Advantages
- Consistency: Ensures that the weld made is uniform and certain in its dimensions.
- Efficiency: The cars are produced in high quantities with little or little utilization of the workers.
Disadvantages
- High Initial Cost: Difficult to establish as fixed assets and demands a lot of funds to install and maintain.
- Limited Flexibility: More suitable for repetitive tasks and further not very suitable for complex or Customer-specific tasks.
9.3. Spot Welding Sheet Metal Welding Technique Assembly
Spot sheet metal welding is a procedure adopted in most manufacturing companies for spot welding thin sheet metals. These manufacturing company uses spot welder. The steps include applying force and electricity to the area where the pieces of metal have to join, and thus, the two are welded. Here’s a breakdown of the process along with its advantages and disadvantages:
Process
- Preparation: Before the welding process, the metal sheets that are bonded are first required to undergo a cleaning process in other to remove any form of interference with the welding process.
- Alignment: The sheets are positioned correctly to have interpolation at controlled intervals as it welds.
- Electrode Placement: Test probes, generally from copper-based alloy, are placed at two sides of the joint area.
- Application of Pressure: In this case, pressure is also applied to the joint area to make the electrode have the right contact with the metal sheets.
- Passage of Electrical Current: At the joint area of the metal sheets, a high current runs through them and the electrodes. The current creates anti-stress through heat build-up and in melding the metal, a weld nugget is produced.
- Cooling: When the current is shut off, both the base metal and filler metal cool and solidify putting more pressure and hence coming up with a strong joint.
Advantages
- Fast and Economical: This is particularly beneficial because spot welding can be carried out in a short period, and therefore would be suitable for example in automotive manufacturing industries where there is a requirement to join metal sheets in large quantities.
Disadvantages
- Shape Limitations: While spot welding is possible only given specific shapes and parts configurations reduce the scope of its use. Indeed, it should be implemented with caution especially when designing these two-mark spaces.
- Heat-Affected Zone: This high level of concentration greatly heats the spot-welded area and creates a heat-affected zone around the weld region where the properties of the metal can be compromised.
9.4 Aluminum Stud Welding Sheet Metal Assembly Technique
Aluminum stud welding is the process of putting the end of an aluminum alloy stud on the surface of an aluminum plate, establishing the arc, and applying certain pressure on the stud. So, it can help perform welding after the contact surface of the stud is melted.
The aluminum stud welding process mainly includes four stages. These include; loading, pre-tightening, fusion, and withdrawal.
Advantage: Aluminum stud welding is efficient, economical quick, and flexible.
Disadvantages:
But it offers some drawbacks as well, i.e. weak interlocking strength.
Comparing the connection strength, aluminum stud welding of the same type and specification is relatively weaker than steel stud welding. It is preferably applied to fasten wiring harnesses, pipes, and clamping arrangements on stamped aluminum blanks.
Hinge Technique:
Sheet metal Hinge technique is a technique through which hinges can be bolted or welded to the sheet metal parts and be designed to provide movement around a central axis. This technique is most commonly used with different kinds of doors, cabinets, and access panels.
So, here are it’s some of the processes;
- Hinge Installation: Two connecting edges are prepared and marked on the corresponding positions of the sheet metal components to facilitate the assembly process of the product.
- Fastening Operation: Screws or rivets, for example, are used to fasten hinges to the body of a vehicle or any other structure that is made of sheet metal.
- Hinge Functionality: When used in sheet metal construction, the hinges allow the parts to swing or rotate in a frictionless manner, all the while displaying utility including, but not limited to, door or panel operation.
Bite Technique
Bite technique is a first part interlock that is a mating joint that is formed by cutting teeth or serrations on the two sheets of metal and then interlocking them securely. This technique of fastening relies on the force exerted by the teeth to avoid disengagement of the joined components to enhance the mechanical type of strength as well as the rigidity of the assembly.
So, the following are its processes
- Teeth Formation: Spinning or cutting of teeth or serrations on the peripheral edge or the side surface of the sheet metal components is done using specialized gear or equipment.
- Interlocking Action: The teeth of the interlocking sheets are engaged by placing the sheet metal components correctly, and bringing the teeth as close as possible.
- Completed Assembly: Once the sheet metal components are assembled, they create a large-force interlocking mechanism due to the teeth interlocking, thus offering resistance and a force that cannot easily be exerted to pull the components apart.
Advantages
- Versatility: Recommended for use on doors, panels, and parts that undergo motion frequently.
- Durable: It is a durable type of connection, which guarantees good synergy between two connected devices.
Disadvantages
- Alignment Required: Basically, a high form of coordination must be in place for systems integration to run as required.
- Complex Assembly: After other forms of fastening techniques; however it is more refined than other techniques.
Expansion Technique
Sheet metal expansion technique is a fastening technique that applies the principle of expansion of at least one, but preferably two or even more sheet metal members to securely engage with the respective counterparts or accessories. This technique utilizes the expansion force provided by the specific tools or devices to fasten the components into the desired position.
So, here are some of its processes;
- Component Preparation: The sheet metal parts used in the assembly are cleaned and made ready to ensure that the final product does not have unwanted features such as rust or any other component that is unwanted in the final product.
- Expansion Operation: Appropriate tools or expanders called mandrels or hydraulic presses are utilized to ooze one or more sheet metal parts.
- Fixture Alignment: After the shaping operation, the sheet metal components are mated right and positioned along their corresponding mating parts of fixtures for the final assembly.
Advantages
- Strong Interlock: Yield major strength as compared to other connexion types due to material strength and geometry.
- No Additional Fasteners: Reduces material costs as such materials and components do not need to be purchased or manufactured.
Disadvantages
- Complex Process: Departments that demand rigorous precise formation and alignment of the teeth in the dental cavity.
- Permanent: Not easily disassembled.
Adhesive Sheet Metal Assembly Technique
Adhesive sheet metal assembly is the process of bonding sheet metals whereby bonding agents or adhesives are used to fix sheet metal members. The benefit of this technique is that it allows the making of sound and quick sticking through without requiring the use of fasteners or welding methods.
So, here are its processes;
- Surface Preparation: Before the assembly is done in the sheet metalworking factory, the surfaces of the sheet metal components to be bonded are cleaned and prepared to guarantee that the bonding will be successful.
- Adhesive Application: The adhesive or bonding agents supplied to the prepared sheets of sheet pieces of metal are placed on the components using specially made applicators or dispensers.
Advantages
- Strong Connection: Most of them offer a safe and secure grip with a firm hold on their object.
- Versatility: May be used in many different locations and any material.
Disadvantages:
- Tool Dependency: It has its specific expansion tools that must be utilized to achieve the desired result.
- Permanent: Not easily disassembled.
Mortise and Tenon Joints
In this technique, a circular or oval hole is cut into one sheet and a matching projection or tongue, is formed on the second sheet. mortise and tenon sheet metal joining is a conventional approach to joining sheet metals that has been adopted from the woodworking industry and requires the formation of an interlocking interface between the two pieces of sheet metal. This technique means that in one piece there are cuts or holes called mortises while in another piece there are tabs or protrusions called tenons whereby they fit to complement the other.
So, let’s check the processes:
- Mortise Creation: One of the sheet metals is drilled with the formation of holes or slots referred to as mortises.
- Tenon Formation: Blanks for forging are produced using cutting, bending, or stamping processes while tenons or tabs are formed on the other sheet metal component.
- Interlocking Assembly: One part fits into the other using a tongue and a groove on another part employing tenons and mortises.
Advantages
- No Heat or Tools: Reduces the complexity of the phase.
- Flexible Application: Applicable for almost all types of fabrics.
Disadvantages
- Curing Time: Take time for this material to cure or attain its maximum strength.
- Limited Load Capacity: In most of their applications, they offer less pulling power than mechanical fasteners.
Guide Rail Assembly
Guide rail assembly pertains to the process of fitting guide rails on mechanisms, which can be in the form of rail-like structures usually metallic, and provides a means for guiding or restraining the movement of another part of a machine. These rails determine the accuracy of movement and positioning and therefore are critical in most applications of machinery and gadgets.
Here are some of its processes
- Rail Installation: Guide rails are secured or placed on the intended surface or structure through the use of fasteners such as screws, bolts, or rivets.
- Alignment: The guide rails are placed in the proper position depending on the directions aimed or requested so that they are straight and parallel to each other in their direction of movement.
- Attachment of Moving Components: Typically, sliding parts or moving mechanisms like sliders, carriages, or gantries, are incorporated or bolted onto the guide rails.
Advantages
- Strong Interlock: Ensures long-lasting connectivity between devices or equipment in use due to its high efficiency.
- No Additional Fasteners: Refuse disposal also impacts material costs as it minimizes the use of available materials and resources.
Disadvantages
- Complex Process: Civil church architecture demands very accurate mortise and tenon formation.
- Permanent: Not easily disassembled.
Metal Pin Assembly
Metal pin assembly is a process by which two or more sheet metal components are joined using metal pins or dowels as the joining media. These pins are fitted through holes of the corresponding controller in a matched array as a convenient method of connecting them.
So, its processes are;
- Hole Preparation: In sheet metal parts, there is usually a specific location where the pin is inserted to connect them, and the holes are drilled, punched, or otherwise made to form the connecting point.
- Pin Insertion: This is done using metal pins or dowels, whereby the corresponding holes are drilled to fix the mating pieces in place by inserting the pins into the holes.
Advantages
- Strong Connection: It will give a strong and stable joint.
- Precision: This makes it possible to have each component fit well within the other, thus having right angles to ensure an accurate fitting.
- Flexibility: Versatile with all types of materials and can accommodate different thicknesses. The holes can also be cored using several techniques.
Disadvantages
- Time-Consuming: Preparing holes is another process that takes much energy and may take too much time to do.
- Vibration Sensitivity: These can become loosened over time due to the vibrations or the dynamic loads exerted on the structure.
- Alignment Requirement: This gives a clear indication of why holes must be formed in the right position to ensure that they fit appropriately.
Metal Key Assembly
Metal key assembly is usually achieved through the use of metal keys or by providing keyways which ensures that the components in sheet metals are well aligned and connected. They are fitted into grooves or recessed on one or both members, in a fashion that guarantees that they won’t come out easily.
So, let’s check its processes
- Keyway Machining: Using cutting or milling tools, keyways or slots are prepared or cut out directly on the faces or surfaces where the sheet metal members connect.
- Locking: These may be reinforced by techniques such as welding, riveting, and well as adhesive-bonding to minimize movement or the possibility of closing the locks.
- Testing: The individual parts were examined to confirm the assumption that keys offer the right amounts of alignment and connection.
Advantages
- Strong and Secure Joints: This offers a strong and stable connection and allows the performance of most activities in a short time.
- Precise Alignment: This plays a big role especially when matching parts that need to meet certain mechanical standards.
- Durability: With keys being utilized, there is a robust connection that may undergo noteworthy loads.
Disadvantages
- Tool Dependency: Specific needs for preparing the slot and subsequent insertion of the key.
- Wear and Tear: Some of the other components of a key and slot configuration are prone to wearing out and may result in looseness or failure.
Hemming Assembly
Hemmings assembly also referred to as hemming is a process of sheet metal working, whereby the extended edge of a sheet metal component is folded over to give that component a smooth round edge. There are several advantages of this technique, some of which are related to the safety of the component and its appearance, besides the mechanical properties of stiffness.
So, here are some of its processes.
- Edge Preparation: Hemming involves folding the edge of what has to be hemmed and for this to be effected, the edge of the sheet metal component, is cleaned and prepared for better adhesion.
- Hemming Operation: During the preparation of the edge, one has to fold or bend it back onto itself with the use of hammers, hemming tools, dies, and other related machinery available in the market.
- Sealing and Finishing: This edge is again tightened through welding, adhesive bonding, or the use of mechanical fasteners so that the folds do not open up or unroll.
Advantages
- Improved Safety: Non-sharp corners and shapes help avoid contact with sharp surfaces or at least minimize how often one comes into contact with such an edge.
- Increased Stiffness: Flaps as such offer support to the component such that the edges are folded.
- Protection: In this design where the edges are folded, they can shield the interior material against rust and wear.
Disadvantages
- Specialized Equipment: Lacks the appropriate tools and equipment necessary for the performance of hemming operations.
- Potential for Material Damage: Incorrect cutting and pressing of the hems can cause the formation of seams or thinning of the cloth.
- Time-Consuming: It can take quite some time to model the part and may take even longer to portray rather intricate shapes.
Clinching Assembly
18.1 TOX Assembly
This versatile transient interconnection architecture is also referred to as the TOX sheet metal stamping connection technology or the rivetless riveting. It does not use welding to make the connections but instead applies cold press working and plastic deformation of the sheet metal to make the connections.
So, here are some of its processes
- Cold Extrusion: The operation is then carried out by positioning the sheet metal components to be joined on the TOX gas-liquid booster cylinder stamping connection device. TOX connection die is then placed over the sheets.
- Stamping and Deformation: A simple punch pushes two connected halves of the TOX connection die inwards against a piece that has been inserted into the die. Another force brings pressure to the material in the die and as the material moves outwards, there is an alteration of the geometry of the sheet metal.
- Formation of Connection Points: Producitio pladit products circular contact area, to the sheet, free from edges and burrs. These points are interconnected and fused tightly with one another which creates a strong mechanically interlinked structure.
18.2. BTM Riveting Assembly
BFX riveting assembly included the riveting technique. It uses the blind rivets and these are inserted from one surface of the part. It is mostly used where only the tapes of the joint are visible.
So here are some of its processes;
- Hole Preparation: Blind holes which are small in the sheet metal are drilled at a point where the rivets are supposed to be inserted.
- Rivet Insertion: It is used to fasten blind holes, these are put into holes drilled in advance. It is attached to a mandrel, which passes through the center of the rivet.
- Rivet Setting: The most effective tool employed here is a rivet that is pulled through the mandrel through the rivet body which forces the components to be held together. Once the rivet is fully set, mandrels are easily removed for disposal and do not hinder further use of the manufactured product.
Advantages
- Accessibility: Perfect for situations where it is possible to address only one side of the joint, Therefore, this fastener is adequately suitable for various assembly scenarios.
- Ease of Use: Substantial economies of scale because it doesn’t have a very complicated installation process that needs training.
- Strong and Reliable: It offers a secure and durable joint that is capable of handling a good deal of force.
Disadvantages
- Tool Dependency: It needs special triggering tools to bring the mandrel and set the rivet for the airplane.
- Material Limitations: Only suitable in conditions that do not have very thick materials or when the load is not overly powerful.
Threaded sleeve assembly
It’s a standard part that meshes into the aluminum alloy casting via an external thread. It provides the external connector with a thread that can be meshed into an internal thread. A threaded sleeve makes it possible to get the high-strength connection of low-strength metal materials. Besides this, it has been practically possible according to the findings of more than 40 years.
This threaded sleeve is made from top-quality stainless steel material. Then the internal thread is installed and embedded in the cast aluminum part of the car body. Here the mounting tail disconnects at the cutout or preset disconnection point.
There are two types of threaded sleeves, i.e. ordinary and self-locking. The ordinary threaded sleeves are produced using a coil with a precisely shaped diamond cross-section. It compresses a commonplace internal thread that can be applied on both sides.
The self-locking type has the same technical benefits as a typical threaded sleeve. Moreover, it contains an internal thread-locking zone comprising one or more turns of the polygonal coil. So, it can fix the thread of the mounting screw through the creation of a lock on the screw.
Threaded sleeves are frequently applied to the aluminum castings. It provides connecting points to important components. These may include subframes, power batteries, and bodies of chassis hard points.
Internal Thread Sleeve assembly
Internal thread sleeves are composed of 7 series special aluminum with internal threads. Their connection strength is relatively high. Moreover, depending on the double string length, the load can satisfy the force of the PC10 level.
Additionally, the sleeves use the cold connection to fit the two end faces of the profile. So, the two end faces of the profile share the internal thread sleeve.
Advantages:
Besides this, they have the following features; reliable connection, high torque, and ease of assembly.
Disadvantage; it is expensive and the cross-sectional size of the profile beam should match suitable for the application.
Aluminum alloy sleeve nuts are mainly used for important installation points on aluminum profile body parts. These parts may include subframes, suspensions, motor assemblies, power batteries, other important hard points, and seat belt installation points.
Conclusion
From the conventional ways of screwing two pieces of metal or nut-bolt combination to new generation ways like ultrasonic riveting. Every technique has its advantages and its application in manufacturing. It is very important to understand that which technique is appropriate for an assembly will depend on the material properties. Besides this, it also depends on the level of joint strength required, cost factors, and volumes of production. Subsequently, future studies on sheet metal assembly techniques will define the way to apply fusion methods for developing innovative manufacturing possibilities. So, it can increase productivity, sustainability, and competitiveness.
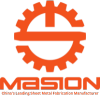