All You Need To Know About Sheet Metal Assembly Rivets | A Complete Guide
Sheet metal assembly rivets are used as an essential input in a variety of fields. Hence they can be considered as the backbone of strong connections used in different processes. So, this article provides an all-encompassing overview of sheet metal assembly rivets by describing the various categories of these fasteners. Besides this, we will discuss the features of their design, the benefits of using sheet metal assembly rivets, and the industries they are useful. Additionally, we will learn how to choose the most suitable rivets for a specific job, and how to install them optimally.
What Do Sheet Metal Assembly Rivets Mean?
Table of Contents
ToggleSheet metal assembly rivets are fasteners that are especially suited for securely assembling sheet metal components. So, some of the kinds are commonly used in industries, i.e. blind rivets, solid rivets, and tubular rivets, even though there are others. However, the type of rivet to be used is determined by the specialty of the industry and the type of joint required. Therefore, rivets are essential in joining sheet metal parts. Since they offer ultimate holding forces or permanent hold without damaging the material.
Components of Sheet Metal Assembly Rivets
Sheet metal assembly rivet components enable the successful fastening or joining of two or more sheets of thin metal. So, let’s discuss these components of sheet metal Assembly Rivets in detail.
- Head: Headed rivets also have their head designed to function as the load-bearing surface. So, they can spread the load applied on the joint. Moreover, these come in various forms including dome, countersunk, and large flange to fit the varied needs of applications.
- Shank: The shank is the middle cylindrical section or the rivet which gets inserted through the materials to be joined together. Some of the cross-sectional shank shapes include grooved, knurled, and threaded types. All these shapes provide a higher level of engagement and pull-out resistance in certain uses.
- Mandrel: It is a cylindrical bar. The mandrel is an important tool utilized during the installation of the blind rivets. It is about rolling the body of the rivet into the position that enlarges the body. So, that it can form a strong joint afterward and remove from the structure.
Considerations for Selecting the Right Sheet Metal Assembly Rivets
Here are some considerations that will guide us in choosing the right sheet metal assembly rivets.
1. Material Compatibility
This remains an important evaluation of whether a rivet material is suitable for the components being joined or not. So, this includes assessing aspects like the likelihood of forming unwanted couples, conducting thermal analysis, and determining mechanical fit. Because different metals show different behavior and characteristics when joined together through welding.
2. Joint Strength Requirements
It means finding out what levels of contact pressure would be necessary for the decided joint strength. So, it can enable the selection of appropriate rivets for loads. This includes the tensile tests, shear tests, and wear tests. So, it can check, if the riveted joint satisfies the necessary performance suitable under various conditions.
3. Environmental Conditions
It is important to check these conditions when deciding to apply a riveted joint in an assembly. Some of the reasons include temperature variation; variation in moisture content, corrosive atmospheres, and effects of UV light on the riveted joint. There may be some environmental effects while selecting rivets.
4. Industry Standards
It is also important to consider industry standards, i.e. relevant for compliance with safety standards. Specifications from ASTM, ISO, and SAE help define the performance characteristics of rivets. The materials and appropriate practices also help us to determine appropriate rivets for particular uses.
5. Installation Method and Tooling
The choice of the installation method needs to be checked before selecting the rivet. There are manual, pneumatic, or hydraulic rivets that need corresponding installation tools. The selection depends on the product manufacturing capacity, the required accuracy, and other factors.
6. Aesthetic and Design Considerations
When it comes to aesthetics, it is vital to consider the kind of head style on the rivets, as well as the finish on them. Factors that may have to be taken into consideration are the aesthetic appeal of the rivet heads. Besides this, it is also important to check the required number of places that may be visible after joining the object.
Top 16 Types of Different Rivets
So, the following are the types of sheet metal assembly riveting;
1. Solid Rivets
Solid rivets depend on mechanical interlocking, which is either brought about by their deformation or interference fit for fastening of the two parts. It is produced with different materials typically including aluminum, copper, iron, zinc-coated, and stainless steel. It is mostly used in tools and factors, cutlery, locks, car parts, suitcases, washing machines, and other home appliances. These types of rivets give a challenging and enduring joint but they demand certain instruments for application.
Applications
Its uses include aircraft, bridges, vehicles, and structures that demand high-grade steel products in steel structures.
Advantages
- Very strong and durable
- Ideal for high-load applications
- No material waste
Disadvantages
- To ensure that adequate documentation of inputs to the simulation model is obtained, it is necessary to allow access to both sides of the assembly.
- More labor-intensive to install
2. Tubular Rivets
There are two types of tubular rivets
i. Full Tubular Rivets
Full tubular rivets are rivets with hollow shafts intended for specific rivet guns; however, these are challenging to use and require special tools. They construct a rivet with an enlarged tail area, offering a dependable means of joining in fastening. Full tubular rivets can be widely applied in apparel and footwear, garment and leather industries, etc., to meet the needs of industries for fastening with high working efficiency and high aesthetics.
ii. Semi-tubular Rivets
They are similar to full tubular rivets but they differ in the fact that the back side of the semi-tubular rivets is much smaller as compared to the full tubular rivets. It is commonly made from wire material that is hardened, and one can find them in uses such as in safes, travel bags and also in military uses. Viewed from this consideration, semi-tubular rivets fall in between these two families from an aspect of both strength and weight and can be used practically almost anywhere a fastening technique is needed.
Applications:
It is used in hinges, lids, brakes, and numerous other metal parts used in this or that kind of luggage.
Advantages
- Their applications are less tedious to do than that of the solid rivets
- Hold good for moderate loads
Disadvantages
- High-load operations and large databases cannot be effective while relying on this system.
- Explain this as a means of demanding appropriate hole size and rivet size
3. Blind Rivets
Blind rivets are those pop rivets that are tubulated in shape and are made up of a rivet and a mandrel. These are for cases whereby one side of the workpiece is accessible for cutting or drilling.
Types of Blind Rivets
Open-End Dome Head: It also comes in a recessed or flattened type and the most prevalent type, the domed head type. Due to its versatility, it can be used on virtually any material.
Open-End Countersunk Head: Has a recessed head to suit surfaces with the level plane, commonly used for applications when the head of the screw is required to blend neatly with the surrounding surface.
Closed-End Dome Head: Comparable to the head of the open-end dome but with the end being sealed thus not permitting the flow of liquids or gases through the head.
Closed-End Countersunk Head: Works in conjunction with both the countersunk head that provides the flush surface and the closed-end configuration that provides the sealing parameter.
Advantages:
- Efficient single-sided installation
- Versatile for various applications
- Good for use in places that are not easily accessible like the inconspicuous areas in a car.
Disadvantages:
- This aspect is associated with material wastage arising out of the mandrel.
- Expensive compared to other rivets some coming with relatively lower prices.
- Requires specialized riveting tools
4. Flush Rivets
Flush rivets are utilized when there is the desire to have a flat surface on both the jewelry surfaces that are being riveted. They are a favorite in aerospace, automobiles, and marine engineering since the aesthetics or aerodynamic nature of the units are important considerations. Flush rivets give a neat and seamless look since the crown of the rivet is hidden where it is set on the surface of the second piece thereby forming a very strong bond.
Applications
Applicable in areas where the liner has been applied and where a smooth surface is necessary for aircraft skins and automotive body panels.
Advantages:
- Provides a smooth finish
- Reduces aerodynamic drag
Disadvantages
- Is associated with stringent hole countersinking specifications
- More challenging to install
5. Split Rivets
Split rivets have a bar-shaped body, one end is formed with the head whereas on the other end, it has a split or bifurcated portion. The most versatile applications of these fasteners are in joining leather, fabrics, and thin metal foils. Split rivets work based on having the split end of the rivet passed through the materials to be joined and then expanded to produce the necessary hold. They are therefore well suited for creating a lightweight fastening system where quick installation can be easily accomplished.
Applications
Applied only in open textured material such as leather, fabric, or soft or foamed plastics.
Advantages
- Easy to install
- Offers good clamp in flexible fabrics
Disadvantages
- For hard materials, this position is not ideal.
- Suitable for those cases where the back of the rivet is hidden or not exposed to show.
6. Self-Piercing Rivets
Self-piercing rivets are fasteners that are peculiar for joining or fastening objects without the requirement of preliminary drilling. They have an incorporated self-piercing mechanism thus eliminating the need for drilling in producing the frame. Some of the key features of self-piercing rivets include; whereby application of self-piercing rivets can be from alloy steel, versatility of the technique where it can work on two dissimilar materials that may have different characteristics or finishes such as corrosion resistant coat, reliability and consistency of the joining process, and there is least smoke produced in the process. Besides, they have lower energy demands compared to welding processes such as MIG, MAG, or SMAW welding.
Applications
Often used in situations where there is a need to join dissimilar operations and in automotive industries where welding cannot be done.
Advantages
- The idea of having to drill a hole before this process is not necessary.
- Can effectively attach to an extensive list of materials, including both coated and high-strength metals.
Disadvantages
- Requires specialized equipment.
- Restricted to undergraduate investigations using only those materials which will not crack when pierced.
7. Friction Lock Rivets
Friction lock rivets otherwise called friction-grip rivets or the HuckBolts® are structural or mechanical rivets applied in applications that demand exceptionally high strength as well as applications that are prone to exposure to vibrations since they afford permanent connection. They comprise a pin, and collar that is placed into operation by hydraulically or pneumatically driven tools.
Applications
Friction lock rivets are well-applied in industries where higher-end, strong, and effective fastening is correlated. This includes:
- Automotive Industry: For the construction of automobiles such as automobiles, vehicles such as trucks, and trailer vehicles.
- Construction: Specially applied in constructional purposes like the construction of buildings bridges and other structures where strong joints are needed.
- Transportation: Used in the construction of other forms of transport, including those for manufacturing and maintenance purposes as well as transport infrastructures.
- Machinery Production: Used in mechanical production tasks that involve the construction of machines as well as equipment.
Advantages
- High Tensile and Shear Strength: Somewhat constructed in a way that enables them to carry large loads and stresses, thus appropriate for high usage.
- Vibration Resistance: These include locking the sides of the rivet so that it cannot be removed easily under vibration or fatigue hence making it a permanent fastener.
- Ease of Use: It can be fitted directly but it does require certain tools that may not be easily available to the general public.
Disadvantages
- Specialized Installation Tools
- Higher Initial Cost
- Complex Removal Process
- Material Compatibility
- Potential for Installation Errors
8. Drive Rivets
Drive rivets are suitable for use using a hammer in that one only has to place the rivet and hammer on it then hit and it automatically fixes itself. They have a tubular-shaped body and a mandrel, which is inserted into the rivet body making it expand on to obtain its required size.
Applications
Primarily intended for use in bonding applications wherein one of the substrates being bonded is a metallic surface and the other is a nonmetallic material and is particularly popular in the automotive and white goods industries.
Advantages
- Quick and easy installation
- Suited for applications that require usage in relatively softer material.
Disadvantages
- Lesser strength than what is possessed by strong solid rivets
- Only suitable for use in areas that can be banged by a hammer
9. Shoulder Rivets
It is a kind of fully-faced rivet where shoulder rivets have a larger diameter shaft under the head creating a spacer.
Applications
For applications where there is a need for a clearance that can be achieved between moving parts or pivot points of specific mechanisms or machinery.
Advantages
- Built-in spacer simplifies assembly
- Provides consistent spacing
Disadvantages
- Limited to specific applications
- Requires precise hole sizing
10. Large Flange Rivets
These rivets are claimed to have a size larger flange than the standard ones to offer a better load distribution and grip.
Applications
Designed for applications where greater contact area is needed and usage of larger plates of materials is possible including plastic and metallic slender sheets.
Advantages
- Penalises usage of a large area by distributing the load over a Larger Area
- Minimizes the likelihood of deformation of materials.
Disadvantages
- May not be suitable in all applications because of the larger head
- Can be more apparent on the different layers of the surface.
Applications
Usually applied in the apparel and shoe manufacturing industries as well as the leather trade.
Advantages
- Lightweight
- Poppet rivets are easier to set compared to solid rivets.
- Suitable for non-metallic materials
Disadvantages:
- It is however not as sturdily built as the other type of solid rivet.
- Limited to low-load applications
11. Expansion Rivets
Expansion rivets are another type of design that is used when the parts need to be held firmly because the use of expansion rivets results in them being embedded into the part. They are intended for use in cases where a rigid and firm connection is required on the joint point and especially where there is restricted access to the workpiece on both sides.
Applications:
- Automotive Industry: Applied in participating panels, trims, and other components where extreme vibration is undesirable.
- Aircraft and Aerospace: Suits the connection of light materials and is perfect for creating strong joints that cannot move during vibrations.
- Construction: Especially to fasten panels, cladding, and other components that require little or no manipulation once fixed.
Advantages
- Vibration Resistance: The expansion mechanism offers great performance which has the characteristic of small vibration between the connected parts.
- Single-Sided Installation: It can be installed only from one side making it useful for blind locations.
- Strong Grip: This expansion affords a firm grip on the materials being combined.
Disadvantages
- Specialized Tools Required: It generally calls for special tools for installation, and these can augment the overall cost.
- Limited Reusability: Commonly not portable when fastened or set up.
- Cost: This can be costlier compared to other rivet types due to the configuration of the rivet and the material consolidation.
12. Thin Wall Blind Bolt
Thin Wall Blind Bolts are intended for hole combination when access to one side of the assembly is not permitted. They are useful where the thickness of the structure cannot accommodate a bolt and nut member group standard or for thin-walled structures.
Applications
Popular with the aerospace, automotive, and construction trades where the frequency of installation and component durability are important factors.
Advantages
- It can be installed by formatting its face from one side (blind form).
- High shear and tensile strength of the matrix
- Suitable for thin materials
- Normally have one or more features that allow its fasteners to be locked to the structure to prevent unscrewing.
Disadvantages
- Limited Load Capacity: Not suitable for situations that compromise high load.
- Complex Installation: To perform these operations may require specialized or more specific tools and methods.
- Material Restrictions: not very effective for very thick and hard carved items of work.
Cost: The material costs are generally slightly higher than the cost of other fasteners.
13. Swaged Pin
A Swaged Pin is a fastener that is fixed in any other place by inserting it and making use of the swaging process. It ensures that it fits tightly. Specifically, the installation style involves placing the pin into a hole and swaging compressing, or deforming one or both elements. So, it can achieve a desirable level of intimacy and interconnection between the two parts.
Applications
Commonly employed in spacecraft construction as well as in car manufacturing and in most other large machinery constructing products or goods where high strength, as well as everlasting clamping process, is required.
Advantages
- Forms a tough, permanent nexus since the resins used harden on exposure to heat and chemicals such as solvents and acids.
- High shear strength
- Give the highest levels of precision and accuracy.
Disadvantages
- Specialized Equipment: Would require special swaging machines which are expensive.
- Material Damage Risk: Possible harm that may be occasioned in case of wrong installation of the Hub.
- Limited Adjustability: It must be noted that during the installation of the matrix, the alignment must be extremely
14. Taper-Lok Fastener
Taper-Lok Fasteners are fasteners with high clamping force and a high tolerance for the taper to create an interference bearing between the fastener’s external surface and the tapped hole. All of them are notable for outstanding fatigue and load-bearing characteristics.
Applications
Predominantly employed in aerospace applications mainly in aircraft construction and parts that undergo high stress.
Advantages
- High fatigue resistance
- Excellent load distribution
- Results in a positive and secure interference fit
- Suitable for high-stress applications
Disadvantages
- High Cost: Pricier than the standard-built homes due to the precision that characterizes the designs of the homes.
- Complex Installation: It follows that a high degree of accuracy is necessary in the manufacture of the respective parts and components of the firearm, as well as the utilization of appropriate tools.
- High Precision Requirement: Require a high level of preparation in making the holes as well as realigning them properly.
15. Nameplate Rivet
These are used to hold together two plates permanently. For rame plates, rivets provide the most suitable means of fastening. They hold the bond firmly, and for long they offer a long-lasting connection especially when used in areas that need most of the connection strength. These rivets may be sourced from aluminum, steel, or stainless steel. Additionally, they have to correspond with the specific use of the rame plate environment.
Applications
- Manufacturing or fabrication of rame plates used in various industrial machines.
- Positioning and fixing of rame plates in assembly line in car manufactures.
- Instructor’s use in load-bearing structures such as residential buildings and bridges.
Advantages
- They have high shear and tensile strength so they’re used in chemical and petrochemical industries.
- Corrosion-resistant materials are available.
- Applicable to both thick and thin plates of the workpiece
Disadvantages
- Permanent Installation: The rivets cannot be easily removed once fixed. This will cause some sort of damage to the components being joined. So, they’re difficult tasks to disassemble.
- Special Tools Required: Another disadvantage of using rivets is that the installation may need specialized equipment, i.e. rivet guns
- Limited Reusability: Rivets are fasteners that cannot be reused once they are removed from one component of an assembly.
16. Barrel Bolts (Sex Bolts)
Barrel bolts also referred to as sex bolts, are a type of fastener that has a barrel portion (female end). It is normally combined with a bolt portion (male end). These bolts are made to work as fasteners securing two pieces of material. Additionally, they are used in applications where the joined surfaces need to resemble a smooth finish. This provides enough contact area.
Applications
- Furniture assembly and repair.
- Architectural installations.
- Fixing panels in exhibitions/trade fares.
Advantages
- Poses less threat of snagging or fraying and allows for a smooth, polished appearance
- It is easy to perform installation and or uninstallation of this software.
- They come in different sizes with different lengths and diameters for the tube or pipe.
- They have been made out of metal and other strong materials including brass, steel, and aluminum among others.
Disadvantages
- Installation Complexity: They need a longer time in the installation process.
- Cost: They are generally costlier than standard bolts and screws
- Limited Load Capacity: They tend to be less durable when pressure is applied or when load is placed on the surface than other types of fasteners.
How to Remove a Rivets?
Rivets can be easily removed through operations like depinning where structures require to be disassembled or repaired. The process typically involves two main steps: deburring the deformed head of the rivet and pixelating the residual rivet shank that is retained in the material. Here’s a detailed explanation of each step: Here’s a detailed explanation of each step:
1. Drill Out Rivet Head
This procedure is performed to have clearance at the location of the rivet head. The remaining portion of the rivet can be popped out easily.
Tools Needed: Drill, an appropriate bit for the holes, preferably the same size or slightly smaller than that of the rivet hole.
Procedure:
- Select the Drill Bit: Select a drill bit that is slightly larger than the length of the body part of the rivet to be used in making the hole. However, care has to be taken to ensure that the correct size is selected to prevent an increase in the size of the original rivet hole.
- Secure the Workpiece: To drill the workpiece safely, make sure that it is well secured so that it does not move when drilling is being processed.
- Drill the Head: Position at the tip of the drill bit in the center of the rivet head. Begin drilling with light speed to mark the position correctly and then increase speed. Continue drilling straight through until the rivet head and the shank are severed. This is always the case when you get to a point of drilling through most of the head thickness of the bolt.
- Remove the Head: After the removal of the rivet head, there may be a small shelf of material left along the other side. Locate the seam where the head is connected to the rest of the body If the head does not come off easily, use a small flathead screwdriver or a tool that is similar in shape to gently pry it off.
2. Punch Out Remaining Rivet
It is used for its dowel removal of the remaining shank of the rivet from the hole.
Tools Needed: Punch—this is a tool in the shape of a cylinder which is marginally smaller in diameter in comparison to the shank of the rivet, or hammer.
Procedure:
- Select the Punch Tool: However, it should be noted that the punch tool chosen should have a diameter that is slightly less than that of the rivet shank to prevent the cutting out of material around the shank.
- Align the Punch: Align the punch tool on the surface of the remaining shank of the rivet with precision. Make sure it is in line to give a clear punch and not bend or damage the punch tool that accompanies the cutter.
- Strike the Punch: Wear safety gloves to hold and with force hit the punch tool with your hammer. Deliver force in fast, equally spaced impacts until the rivet shank is driven out of the hole. Remember to be gentle when using the vise and not press on the workpiece too hard for fear of damaging it.
- Inspect the Hole: On removal of the rivet shank, check the hole for any burrs or damages that might hinder the function or cycling of the element. More details of hole preparation to install a new rivet if needed as per the process of hole cleaning that has been observed earlier.
Different Types of Rivet Inspections
Indeed, inspection activities are extremely important in guaranteeing that rivets are of high quality and reliable. So, here we will discuss the various types of inspections that are required. So, we can ensure that the rivets are suitable for particular applications.
1. Appearance Inspection
This assessment includes a visual examination of the rivets. So, we can identify if any of the outer features is flawed or substandard in any way. So, this step typically includes the following checks;
- Surface Finish: Assessing the quality of the rivet surface, particularly to checks, bumps, rough edges corroding signs, and other defects.
- Head Shape and Symmetry: Verifying the proper shape of the top of the rivet and its maximum sharpness.
- Dimensional Accuracy: Check the dimensions of the rivet, if they meet the standards or not.
- Coating and Corrosion: Determine if there is any form of corrosion or any defects in any form of protective coating, applied on the rivet.
2. Shear Force Inspection
Shear force inspection checks its ability to hold forces that can potentially cut through the rivet and pull it out of use. So, it is an important test to check the sheer strength and durability of the rivet. The inspection process generally involves the following steps;
- Sample Selection: Picking a random batch of rivets to be tested from the whole production lot.
- Testing Apparatus: Applying shear load on the rivet by using a gadget of a particular design till the rivet offers to pull apart.
- Data Collection: Measure the force applied to remove the rivet.
- Analysis: Compare the actual shear force with the specified requirements to ensure compliance.
What are Rivets – inspection methods and criteria
Here are the detailed inspection methods and criteria for rivets
Sr. No. | Test items | Quality Importance | Sampling Level | Validation Tools | Requirements and Inspection Methods | Qualification Criteria | Based on the Information |
01 | Packaging and labeling | General | Level I | Visual inspection | 1. Packaging and labeling completeness; 2. Labeling details | Meet order requirements and consistency; Clear logo on the package | Order Requirements |
02 | Exterior | General | Level I | Visual inspection/touch | Visual and tactile smoothness; Surface defects | No cracks, scratches, plating, or other defects affecting use | Order Requirements |
03 | Material | Critical | S-1 | Spectrometer | Outsourced testing; Supplier-provided reports | The material meets national standard requirements | GB/T 3190, GB/T 699, GB/T 3206 |
04 | Size requirements | Critical | S-1 | Vernier caliper |
Dimension tolerances |
Nail body diameter: -0.1mm/+0.1mm; Length: -0.3mm/+0.3mm | Drawings/orders/national standard requirements (GB/T 12615/ 12616/ 12617/ 12618) |
05 | Geometric Tolerances | Critical | S-1 | Angle ruler/Vernier caliper |
Verticality; Coaxiality |
Meet specified tolerances | Drawing/Order Request |
06 | Coating thickness | Important | S-1 | Coating Thickness Gauge | Coating properties; Thickness measurement | The coating meets thickness and properties; Corrosion resistance | Drawing/Order Request |
07 | Salt spray test | Critical | S-1 | Salt spray test machine | Surface treatment; Test duration | Meets protection and appearance level requirements | Order Requirements |
08 | Tensile test | Critical | S-1 | Universal material testing machine | Test procedure | Tensile load meets national standard requirements | GB/T 3098.18-2004, GB/T 3098.19-2004 |
09 | Shear test | Critical | S-1 | Universal material testing machine | Test procedure | Shear load meets national standard requirements | |
11 | Online trial installation test | Important | S-1 | Riveting Machine | Sampling in the factory for riveting test | No cracked or broken rivets | Company request |
Installation Techniques for Sheet Metal Assembly Rivets
Rivets play an important role in maintaining the quality of the assembled components. So, it requires some techniques to ensure they are installed correctly during construction. There are various methods of installation. But choosing the right one depends on the scale of the project and the tools used to install it. They may include manual, pneumatic, hydraulic, etc. So, let’s discuss all the techniques in detail.
1. Manual Installation
Manual installation is appropriate for those projects that are not massive and also in case of repairs. They are a good option where there are not a lot of rivets to be installed. Here, we use the form of hand tools,i.e. hammers and various types of bucking bars are used.
Step-by-Step Guide to Manual Installation
- Preparation: Clean the surface where the plates will be joined and make sure that the holes are aligned.
- Insert Rivet: Pass and position the rivet over the aligned hole.
- Position Bucking Bar: Place an instrument termed the ‘bucking bar’ against the tail of the rivet.
- Hammering: Hammering takes place when the head of the rivet has to be extruded. It ensures that the tail is delivered on the other side of the joint. So, it can hold the position firmly.
- Inspection: Examine the formed head for any anomaly. Besides this, make sure that it meets the desired standard.
2. Pneumatic Installation
Pneumatic tools are for mid to large-scale operations. Additionally, its results are better and uniform in comparison to any manual operation.
Step-by-Step Guide for Pneumatic Installation
- Preparation: First, clean and align the surfaces to be joined.
- Tool Setup: Hold the pneumatic rivet gun on the two surfaces that need to be joined. Then connect the air compressor.
- Insert Rivet: Position the rivet in the gun and check if it fits the holes properly in the metal plates.
- Activation: Pull the trigger to fire the gun which withdraws the mandrel. Then it opens up the tail of the rivet.
- Mandrel Removal: This removes the mandrel automatically.
- Inspection: Ensure that the formed rivet is correctly positioned depending on its function in the construction project.
3. Hydraulic Installation
Hydraulic tools are used where strength and accuracy are required.
Step-by-Step Guide to Hydraulic Installation
- Preparation: Check for dirt or any waste that may be on the faces of those components.
- Tool Setup: Link the hydraulic rivet gun to the hydraulic power unit.
- Insert Rivet: Embed the rivet into the gun and make sure it fits properly over the holes.
- Activation: Power the hydraulic system by placing pressure on the structures and squeezing the rivet into shape.
- Mandrel Removal: Remove the mandrel after the rivet has been deformed.
- Inspection: Check if the installation of rivets adheres to specifications.
General Safety Precautions while Installing Rivets
Here are some safety precautions on can do while installing the rivets.
- Training: Before selecting an installation tool, make sure that the operators are trained in the use of the tools. Besides this, they are aware of the installation process.
- Maintenance: Check that tools are checked often and are in good working condition. So, they can minimize issues like the breakage of tools.
- Work Area: It is essential to maintain cleanliness and tidiness of the working environment. So, it can minimize the risks of future mishaps.
- Emergency Procedures: Make sure you are aware of emergency plans and always ensure that you have an emergency kit for use, i.e. ‘First Aid Kid’
Operation Process Guidance
1. Rivet Nut
It is also called by different names such as pull nut or instant pull nut. This part is useful in many fastening of metal plates, pipes, services manufacturing companies, and industries. As a solution to some of the concerns regarding the welding of nuts for thin plates and pipes, rivet nuts do not have to drill internal threads. They come with a highly efficient and easy riveting process.
1.1. Rivet nuts classification
- Nominal Diameter of the Thread: M3 to M12
- Head Shape: Flathead, Cylindrical head, Countersunk head
- Hole Type: Blind holes and through holes
1.2. Rivet Nut Operation Guidance
- Material Preparation: Finally coordinate the model and specifications of the rivet nut as per the drawing standard.
- Confirmation of Base Material Plate Thickness and Bottom Hole Size: More specifically, make sure that these dimensions are right for the bottom hole size.
- Adjusting the Rivet Gun: Inspect the air pressure to make sure the pull rod and pneumatic rivet gun can be connected easily. Also, check that the insertion length and stroke may require some adjustment.
- Riveting: Place the rivet nut into the target hole at the lower stage manually, on the right side.
1.3. Inspection
- Detect the Shrinkage Length of the Rivet Nut: Specifications of the sensors are described in this table.
Thread Specification | Contraction Length (mm) |
M3 | 1-2 |
M4 | 1.4-3.2 |
M5 | 1.5-4 |
M6 | 1.8-4.5 |
M8 | 2.2-5.5 |
M10 | 2.5-5.8 |
M12 | 2.8-6 |
M16 | 3-8 |
- Detect the Torque of the Rivet Nut: Some of the torque values according to the material and thread specification are distinguished in the following table.
Thread Specification | Cylindrical Head (N.m) | Flat Head/Countersunk Head (N.m) | Aluminum Substrate Cylindrical Head (N.m) | Aluminum Substrate Flat Head/Countersunk Head (N.m) |
M3 | 0.5 | 0.4 | 0.25 | 0.2 |
M4 | 1 | 0.8 | 0.9 | 0.7 |
M5 | 2 | 1.5 | 1.5 | 1.2 |
M6 | 4.5 | 3.5 | 3.5 | 2.5 |
M8 | 5.5 | 4.5 | 5 | 4 |
M10 | 11 | 8.5 | 6.5 | 5 |
M12 | 30 | 24 | 21 | 16 |
2. Self-Clinching Nut
Self-clinching nuts are used when the desired part is thin plates or thin sheet metals. So, compared to traditional machines that often weld components together, they use embossed teeth and guide grooves. So, they can fit snugly into the appropriate material.
2.1. Material and Model Description
- Self-clinching nuts are normally alloyed with fast-cutting steel or stainless steel and range up to M2 to M12 size.
- Details of self-clinching nuts are outlined in the table below The specifications are as follows:
2.2. Operation Specifications of Clinching Nuts
- Confirm the Rivet Nut Specifications: Always refer to the drawing specifications to avoid making mistakes in the use of the same.
- Confirm the Bottom Hole Size: Make sure that the bottom hole size in the plate is satisfactory.
- Adjust the Equipment: Choose the right type of rivet head, and ensure that pressure is applied properly.
- Install the Rivet Nut: Place the rivet nut into position and tighten with undercutting of the hole.
2.3. Inspection
- Appearance Inspection: Make sure that no deformation or imprints are left around the rivet nut.
- Torque Detection: Ascertaining that the torque value complies with the designated specifications.
3. Blind Rivets
The blind rivets employ yet another principle called Hooke’s law. According to this, the metal collar is flexed into the bolt groove to make a snug fit.
3.1. Classification Of Blind Rivets
Based on the blind rivets’ type they are closed type, open type, or floating type. On the other hand, the shapes of the blind head are flat head or umbrella head.
3.2. Specifications and Dimensions
For general dimensions and thickness of the material used, you can follow this table;
Rivet Type | Diameter (mm) | Length (mm) | Head Diameter (mm) | Head Height (mm) |
Open-type flat-head rivets | 2-10 | 5-50 | 4-20 | 1-3 |
Open-type umbrella-shaped rivets | 2-10 | 5-50 | 6-22 | 1-3 |
Closed-type flat-head rivets | 2-10 | 5-50 | 4-20 | 1-3 |
Closed-type umbrella-shaped rivets | 2-10 | 5-50 | 6-22 | 1-3 |
3.3. Rivet Installation Steps
- Pre-installation Preparation: Identify, if the air pressure needs to be checked for the cutting tools. Also check, if it’s necessary to clean the tools or verify the hole sizes.
- Rivet Installation: Insert the rivet in the right manner. So that, it fits ahead of the hole and makes sure that the gaps between two parts are minimal.
- Post-riveting Inspection: Make sure that no gaps, burrs, or any other foreign substance exist in the mounted sample.
3.4. Inspection
- Appearance Inspection: Guarantee that the interface suits the devices in terms of size and shape. Also, check that there are no lumps out of place.
- Shear Force Test: They should carry out tests from time to time. So, it can conform to the barest minimum shear force needed.
Applications of Sheet Metal Assembly Rivets
So, here are some applications of sheet metal assembly rivets.
1. Automotive Industry
Typically, sheet metal assembly rivets are employed in automotive applications for joining automotive body panels, chassis parts, and structures. So, they supply firm and lasting joints that do not fail under the stress typically placed on vehicles. Additionally, they also offer the safety and efficiency of automobiles.
2. Aerospace Industry
Essential for aircraft construction, SMC sheet metal construction rivets are inarguably functional They offer efficient, durable, and strong joints in important structural connections. They are strong and stable for large structures or mechanical parts that make up an aircraft. So, they prevent failure due to the forces experienced during flight and meet the high standards of safety requirements.
3. Electronics Industry
In the electronics industry, some of the SCMH products, i.e. sheet metal assembly rivets are used in the assembly of enclosures for electronics products. So, they provide physical protection for delicate parts. They guard against any conditions that are detrimental to their contents such as humidity, dust, or moisture. Moreover, they allow for proper heat dissipation which is important for the proper functioning of several pieces of electronics.
4. Construction Industry
Rivets used in assembling sheet metals are very popular in constructing commercial buildings and structures. So, they are commonly used in rigs, i.e. facades, roofing structures, and even structural frameworks. Riveted joints are mechanically fastening systems. So, they are ideal since they offer durable and long-lasting connections despite the prevailing environmental conditions.
5. Marine Industry
Also forging purposes, sheet metal assembly rivets are also widely applied in the marine sector of industries. They are used in shipbuilding and off-shore structures. Such functions include anti-corrosive protection. So, they can increase the durability of equipment and the structural rigidity of vessels and offshore installations.
What are the Advantages of Sheet Metal Assembly Rivets?
The benefits of using sheet metal assembly rivets include;
- High Strength and Durability: Bolted joints that use sheet metal assembly rivets are strong. They can take fixed loads for long periods. So, they offer their maximum resulting in structural strength. It makes them ideal for use in places where strength and reliability are of top concern.
- Resistance to Vibration and Corrosion: The rivets also offer durability, especially through their resistance to vibration or corrosion. So, it makes them ideal for use in rough scenarios. They guarantee that the joints continue to be stable and operational several more times.
- Ability to Join Dissimilar Materials: Riveting also gives the factor of being able to fasten different materials together. So, it opens up a wider range of uses across the industries. This feature makes it possible for engineers to design complicated assemblies. So, it can be made using various materials. So, it can improve the functionality and effectiveness of the same assembly.
- Cost-Effectiveness Compared to Alternatives: Riveting is an economical type of joining strategy when compared to other procedures. i.e. welding or adhesive bonding. So, it is ideal for mass production because of its numerous advantages. Additionally, it can be produced in large quantities at a lesser cost in terms of money and time.
- Ease of Inspection and Maintenance: Riveted joints can be easily checked for signs of wear, fatigue, or failure compared with other methods of Joining. So, this helps to take control and act before impending problems. Otherwise, they may cause assemblies to degrade in performance or compromise safety.
- Enhanced Aesthetics and Surface Finish: Rivets can play a part in the aesthetic design of the final products. Here they can become popular in architectural metalwork or automobile manufacture. Additionally, there are models in terms of head designs and types of finishes using various materials. They also provide chances to modify the heads according to design needs and make a professional appearance.
Why Choose Masion for All Sheet Metal Assembly Riveting?
Mansion – A premier solution for all sheet Metal Assembly Needs. So, if you are looking for sheet metal assembly rivets. We’re here to serve you. Besides this, we have multiple other techniques. So, if you need any kind of riveting process. Just visit our website and get your quote today
Conclusion
In conclusion, sheet metal assembly rivets find versatility in reaching various industries. They provide a cost-effective and steadfast method of fastening the joined sheet metal parts. Therefore, it is beneficial for staying informed about innovations in the field of riveting technology. It allows for the production of output and efficiency through the manufacturing challenges of the modern world. Therefore, by recognizing the peculiarities of sheet metal assembly rivets, industries are set up to keep benefiting from riveting holds for effective assembly processes. Because they offer strength and durability.
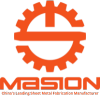