Sheet Metal Assembly, It Methods, Types and Applications
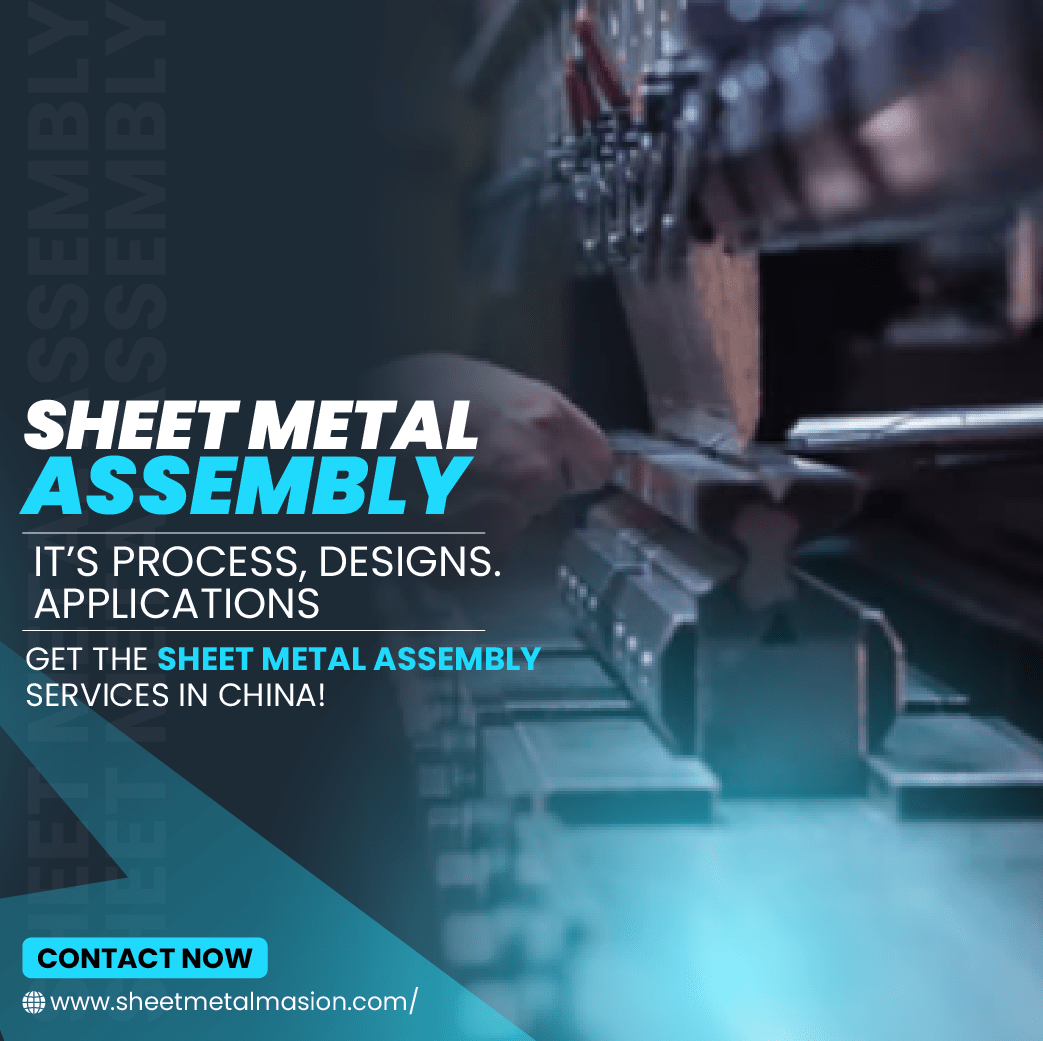
Sheet metal assembly refers to the method of joining various components. These are thin sheets of metal. So, you can use them in car manufacturing, aerospace, construction, and electronics industries. Here various sheet metal components manufactured and connected into a single unit to form structures or products. So, it is quite a simple process. So, in this article, we will discuss the details of carrying out our sheet metal assemblies. We will go for an analysis of its techniques, and the tips for increasing work efficiency.
What Does Sheet Metal Assembly Mean?
In its real sense fabrication process entails the linking or joining of single or distinct sheet metal components. So, it can form a single complete piece or part. You can make them by cutting processes such as: cutting, bending, and shaping from flat stock metal. Additionally, the most common Assembly methods are welding, riveting, clinching, and adhesive bonding. So, the choice of method depends on the requirements of the design and application.
Step-by-Step Sheet Metal Assembly Process
So, let’s discuss the step-by-step process in depth.
Design Phase
Sheet metal design for assembly has many types and it is the first phase of the sheet-metal working assembly process where engineers and designers come up with ideas and then develop the plan. So, they can meet the desired product or a certain part. This stage involves several key considerations:
- Material Selection: It becomes the responsibility of engineers to know the right sheet metal material. They select it after determining factors like strength, corrosive resistance, and cost. The three most common materials are steel, aluminum, and stainless steel. While each has its characteristics regarding its usage.
- Part Geometry: The shape or the geometry of the sheet metal parts is important for both functioning and manufacturing. So, engineers also have to consider optimization parameters of part geometric dimensions. These may include the size, shape, and complexity of the component features. So, the parts can meet specifications for ease of manufacturing.
- Assembly Methods: Manufacturers choose the best among metal assembly techniques for assembling different parts depending on some aspects. These may include the part geometry, the quantity of production, and the expected performance of the final product.
- Design for Manufacturability (DFM): It helps engineers address issues related to component manufacturing and improve a design. Here the engineers consider two aspects, i.e. manufacturing ease and cost. So, you can do it by reducing the complexity of the geometries involved in product parts, reduction of material usage, and creating forms that are easy to assemble in production.
Sheet Metal Fabrication and Assembly
Fabrication is the process of converting raw material into shaped sheet metal parts by cutting, bending, punching, and other related processes. So, the key aspects of the fabrication stage include
- Cutting: To transform sheet metal, it you can cut into the right forms, by several methods, i.e. shearing, laser cutting, or water jet cutting. All the methods have their privileges depending on the speed of computations. Besides this, they also depend on the precision and complexity of the part.
- Bending: Among the operations performed on sheet metals, bending is one of the most common. It serves to create three-dimensional shapes like angles, curves, and enclosures. So the precision bending may include press brakes. So, bending ensures a proper angle as well as the pertinent dimension of these brakes.
- Punching: Punching entails making impressions on metal sheets, which include holes, slots, and curved or angular sloths. With the help of punch presses or turret punch machines you can achieve perfect punching. This is a crucial step in making precise slots for attaching bolts, dowels, and connectors as well as progression for ventilation.
- Forming: Operations for forming sheet metal include stamping and deep drawing. So, it can achieve various shapes and angles in metal parts. These include the use of dies and presses to shape the workpiece into the required shapes. Additionally, it also depends on the cross-sectional thicknesses of the metal part.
You can get fabricated sheet metal assemblies at Masion.
Metal Parts Assembly/Joining Phase
Assembly or joining is the step that involves the formation of the final product or a particular component. Here several other small sheet metal parts join to form a single component. Various
assembly techniques you can choose including i.e. joint strength, accessibility, and production volume. So let’s discuss them all in detail.
- Welding: Welding is the process of metal parts assemblies by using heat and pressure. So, it can make a strong connection as irreversible as possible. However, they are mainly belongs to Spot welding, TIG welding, and MIG welding. These welding processes have varying efficiencies based on speed, precision, and the quality of the joint they form.
- Riveting: Riveting is a process of joining metal parts through the use of threads or mechanical fasteners, known as assembly rivets. Here the rivets undergo deforming to bring two parts into contact. They provide high tensile requirements for joining the two parts permanently,
- Clinching: Clinching is a type of cold-forming method where metal sheets feature bonding together without using any insert, rivet, or any other material and without heat. So, this method ensures the manufacturing of very firm and quite stable joints. Additionally, it does not affect the material properties.
- Adhesive Bonding: Adhesion refers to the process of joining two or more parts of metal through the use of adhesives. It offers even pressure distribution by having good surface contact and protection of the bonded joints against moisture and other contaminants. So, make sure the underlying surface and the adhesive material are clean before selection. So, you acquire efficient bond strength and service duration.
Inspection Phase
Inspection is an important stage in the metal assemblies process through which the products undergo various checks to meet requirements. These checks may include dimensional, surface finish, and structural standards. So, the key aspects of the inspection stage include;
- Dimensional Accuracy: They ensure that the sheet metal parts conform to the recommended measuring sizes. Besides this, they are within their acceptable tolerance limits. Calipers and micrometers are employed for measuring geometric dimensions. On the other hand, coordinate measuring machines and gauges are used for dimensional inspection.
- Surface Finish: Final inspection helps to confirm that sheet metal products possess the correct surface finish in the absence of defects, i.e. cracks, marks, indentation, or rust. Surface roughness and Surface form/shape are both measured and assessed through visual inspection and surface profilometers respectively.
- Structural Integrity: Nondestructive testing is carried out regularly to look for possible damages like cracks, weld discontinuity, or flawed material that affects the overall assembly. Ultrasonic testing and magnetic particles help inspect flaws that are hidden in the respective material without causing any harm to it.
Surface Finishing Phase
It’s the last step of the assembly in sheet metal working where other types of finishing touches are provided. So, it can enhance the appearance of the material and also increase the corrosion. Common finishing techniques include:
- Painting: Painting as a surface treatment method refers to the act of applying a coating on sheet metal parts. So, it can improve its appearance or prevent corrosive effects. Spray painting, powder painting, and electro painting are some examples of the painting methods. These methods are selected according to the purpose and requirements of a given part.
- Powder Coating: It is another form of dry finishing where the powder is electrically pre-charged. Then it is coated on sheet metal parts. After that, the heat is applied to form an integrated layer. So, this method renders excellent anti-corrosion features. Additionally, it also offers solutions to environmental challenges.
- Plating: The process of Plating consists of depositing a thin layer of a metal like zinc, nickel, or chrome on the sheet metal parts. It uses either electroplating or electroless plating methods. So, this process increases surface hardness. Besides this, it increases its ability to perform in corrosive environments.
Commonly Used Materials for Metal Parts Assembly
Here is a detailed list and properties of materials and alloys that can be used for sheet metal assemblies.
Category |
Material |
Description and Properties |
|
Steel |
Strong, corrosion-resistant |
Aluminum |
Lightweight, corrosion-resistant. |
Copper and Brass |
Copper: Excellent conductivity. Brass: Acoustic properties, aesthetic appeal. |
Titanium |
High strength-to-weight ratio, – corrosion-resistant. |
Nickel Alloys |
Excellent corrosion resistance, and high-temperature stability. Used in chemical processing, aerospace, and power generation. |
Common Alloys and Their Properties
|
Aluminum Alloys
6061-T6, 5052-H32, 7075-T6 |
6061-T6: Balanced properties. 5052-H32: Formable, corrosion-resistant. 7075-T6: High strength. |
Stainless Steel Alloys |
– Corrosion-resistant. – Chloride-resistant. – Good formability. |
High-Strength Steel
HSLA, AHSS |
HSLA: Strong, lightweight. AHSS: Excellent strength, and ductility. |
Titanium Alloys
Ti-6Al-4V |
High strength, lightweight, excellent corrosion resistance. Used in aerospace, medical, and marine applications. |
Nickel Alloys
Inconel 625, Monel 400 |
High strength, corrosion-resistant, good high-temperature performance. Used in chemical and marine industries. |
Coatings and Finishes
|
Galvanization |
Zinc coating for corrosion protection. Used in construction, automotive, marine. |
Anodizing |
Oxide layer on aluminum for durability, and appearance. Used in aerospace, electronics, and consumer goods. |
Powder Coating |
Durable, protective polymer finish. Used in automotive, appliances, and outdoor equipment. |
Discover the forming of Material of metal parts assemblies
What Tools and Equipment are Used in Sheet Assembly?
Here is a detailed description of different tools and equipment used in assembly of sheet metal.
Cutting Tools
Sheet metal is usually cut into different shapes and geometries. So, here are some tool and their types that are abundantly used to cut metal sheets.
Shears
The shears are either mechanical or hydraulic tools. They are primarily used for cutting sheet metals for accurate measurements. They employ a blade that they use to exert force. This force acts in parallel to the surface of the metal. It cuts the metal properly.
Types of Shear
- Mechanical Shears: It is powered to work with an external source. So, it can move across the workpiece. It gives more appropriate results when used in lighter gauge materials and accurate cutting.
- Hydraulic Shears: These are more forceful and efficient when handling thicker or denser materials. Additionally, they use hydraulic power to cut the sheets.
Applications
Use to produce straight cuts and to make metal sheets table for further processing.
Laser Cutters
High-powered CO2 lasers are used in laser cutting. They burn or melt away material by precisely defined paths. Additionally, they offer high accuracy and can shape more complex elements and minute features.
Types of Laser Cuts
- CO2 Lasers: They are ideal for cutting, engraving, and boring a range of different materials. It is not limited to metals only.
- Fiber Lasers: Available in larger sizes, hold up higher efficiency and precision. They are best suited for cutting metal sheets that have elaborate patterns.
Applications
It is commonly used in industries where accuracy and intricate machinery are vital. These industries are mainly automotive, aerospace, and electronics industries amongst others.
Water Jet Cutting
Water jet cutting utilizes a high-pressure water jet to cut mainly sheet metal. So, here sometimes the water is mixed with garnet abrasives.
Types of water jet cutting
- Pure Water Jet: It works underwater only and is most effective if only soft fabrics are to be printed.
- Abrasive Water Jet: Use an abrasive material to remove harder materials, i.e. metals by grinding them between the abrasive surfaces.
Applications
Most suitable for materials that shrink at higher temperatures and for creating clean edges without affecting the properties of the material.
Bending and Forming Equipment
Let’s explore how the bending and forming tools work.
Press Brakes
Press brakes are tools that form, cut or bend sheet metal generally applying pressure using a punch and die. So, they may be hydraulic or mechanical in type.
Types
- Hydraulic Press Brakes: These can exert an efficient controlled force and are used for bending thick or difficult materials.
- Mechanical Press Brakes: They come with mechanical drives for better operation speeds. But generally, they offer less flexibility compared to hydraulic varieties.
Applications
Solely fitted for making bends and angles, especially in the structure of sheet metal parts. Mostly, they are used in the manufacturing of automobiles and construction materials.
Roll Forming Machines
Roll forming machinery is a type of progressive metal forming process where the metal sheet from the furnace goes through a series of roll forming stations.
Types
- Standard Roll Forming: Specializes in manufacturing easy-to-produce merchandise like angles and channels.
- Complex Roll Forming: It can stamp out simple shapes and bends or the more complex and deep bends that are desired in a piece.
Applications
Applicable for manufacturing large pieces of metal member parts for example metal roofings, conduits, and automobile parts among others.
Joining Techniques
So, let’s discuss the different joining techniques we can use in metal sheet assembly.
Welding
Welding is the process whereby various metals are joined by applying heat and pressure to produce a strong and permanent union. Different methods of welding are adopted depending on the necessity of the particular field.
Types
- Spot Welding: Also called welding; the process utilizes electrical resistance to heat and fuse the metals; at certain joints. So, it is suitable for attaching thin metal sheets for applications in automobile production or manufacturing of various domestic appliances.
- TIG Welding (Tungsten Inert Gas): It utilizes an expendable tungsten electrode to produce an arc and fuse the base metal in its orbit. So, it is popular for owing tight tolerances and has applications in different industries. They mainly include aerospace engineering and pipework industries.
- MIG Welding (Metal Inert Gas): They use a continuous feed wire as the electrode and filler material. It feeds into the weld zone to replenish itself. Moreover, it permits high-rate welding and it is applied in building constructions and the production of heavy machinery.
Riveting
This process involves the use of mechanical fasteners referred to as rivets. Here the combination of compression and hammering techniques are used to ensure that the parts being worked on are joined permanently.
Types
- Blind Rivets: Mechanically fastened joints where access is only possible from one side of the workpiece.
- Solid Rivets: There must be access from both sides, thus the basic interior joints must be strong and can resist adverse conditions.
- Huck Bolts: Heavy-duty rivets meant for tough usage such as those for use in heavy vehicles like trucks or railway cars.
Applications
They are mostly employed in aerospace applications, automotive engineering, and structural applications.
Clinching
Clinching is the industrial process of joining two or more sheets of metal at distinct points via cold working without the use of filler materials or heat.
Types
- Mechanical Clinching: Actually, it involves the application of mechanical force to bring about changes in the shape of the material.
- Pneumatic Clinching: A pneumatic clinching process uses compressed air to run the clinching tool.
Applications
The application includes use in the manufacturing of automobiles and other appliances whereby heat produced during welding might be a nuisance.
Inspection and Quality Control Tools
To inspect and control quality, it has been important to employ several tools. So, let’s discuss them in detail.
1. Coordinate Measuring Machines (CMM)
CMMs are precision instruments that are used to examine and verify the dimensions and geometric properties of various sheet metal parts. So, they can conform to the designs and standards set at the initial design.
Types
- Bridge CMMs: Standard machine with fixed gantry and feed table suitable for medium to large sizes of the workpiece.
- Portable CMMs: Can be utilized when it is hard to wash large components or those that cannot be moved.
Applications
It is used to inspect machined parts specifications in automotive, aerospace, and Manufacturing.
2. Non-Destructive Testing (NDT)
NDT methods refer to the ones in which the characteristics of a material, a component, or a system are assessed. It is done without causing any harm to the area under test.
Techniques
- Ultrasonic Testing: This method also works by directing high-frequency sound waves onto the object. So, it analyzes the reflected sound waves to determine flaws within the object.
- Magnetic Particle Inspection: Used in non-destructive observation for the identification of faults or flaws on the surface or at a shallow depth in ferromagnetic materials.
Applications
Common in aerospace manufacturing, big automotive industries, and construction projects to check the validity of the materials.
3. Optical Inspection Systems
Optical inspecting systems employ the use of cameras along with sensors to visually inspect for surface finishes, weld coating joints, and assembly tolerances.
Types
- Machine Vision Systems: Robotic systems that capture and analyze images of surfaces and objects for flaws in the materials and workmanship.
- 3D Scanners: Develop large-scale models in 3D that would allow visibility of the part to check for defects carried out.
Applications
In electronics, automotive, and precision manufacturing where close tolerance is required to ensure a high-quality product.
Effective Design Tips for Sheet Metal Assembly
Here are the most effective design tips that will help you make the sheet assembly efficient. So, let’s discuss them in detail.
Design Consideration
|
Problem
|
Cause
|
Solution
|
Simplified Drawings
|
Reduce the Part Count
|
High assembly time and cost. |
Excessive number of individual parts. |
Minimize the number of components by combining parts and eliminating redundant ones. |
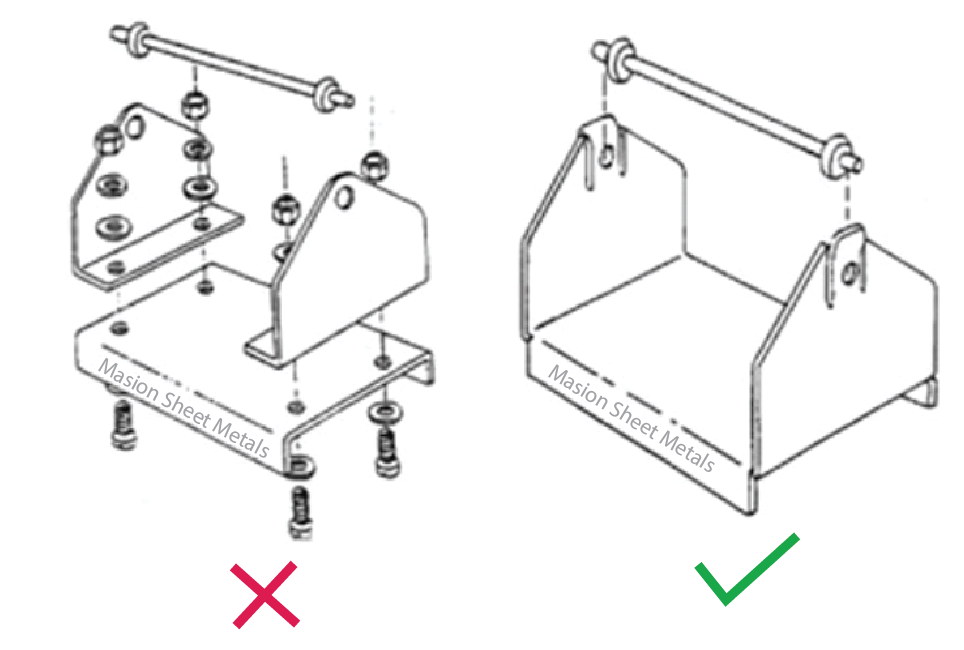 |
Simplify Assembly
|
Difficult and time-consuming assembly process. |
Complex parts and a high variety of fasteners. |
Design parts for easy positioning and alignment. Standardize and reduce the number of fasteners. |
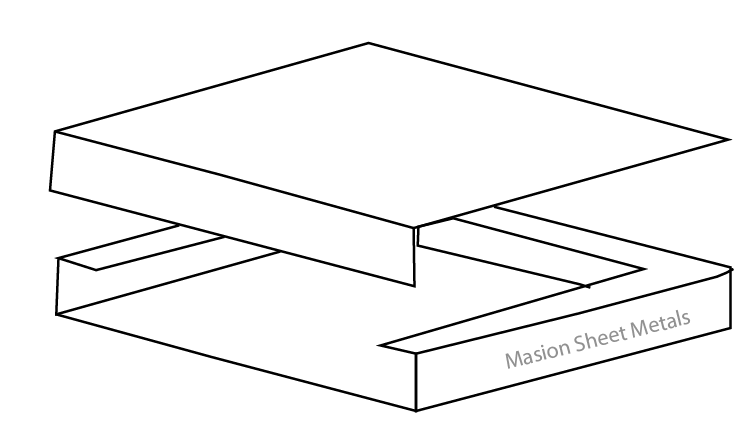 |
Integrate Parts
|
Increased part count and complexity. |
Separate components performing individual functions. |
Merge parts to perform multiple functions, reducing overall part count and simplifying the design. |
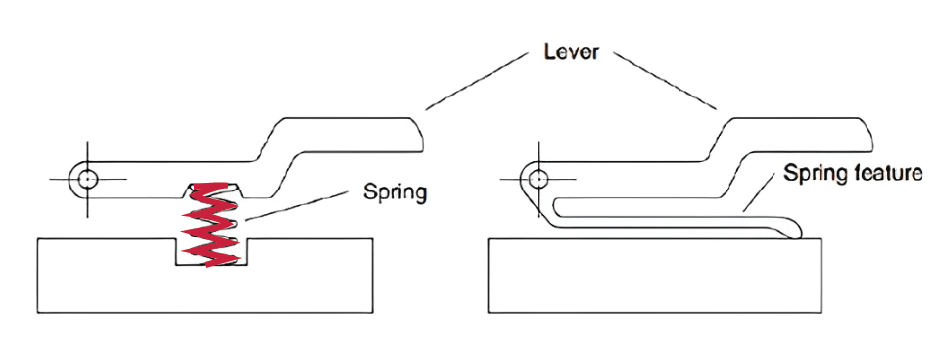 |
Innovate with Fastening Methods
|
Slow assembly process and potential for fastening errors. |
Reliance on traditional fasteners like screws. |
Replace traditional fasteners with integral elements like snap-fits, tabs, or catches to simplify assembly and reduce errors. |
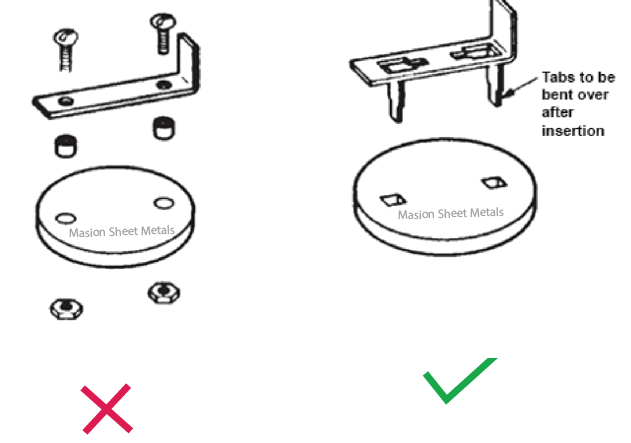 |
Polarize Parts
|
Incorrect assembly orientation leads to assembly errors. |
Parts can be assembled in multiple orientations. |
Design parts to fit together in only one correct way, ensuring proper orientation during assembly. |
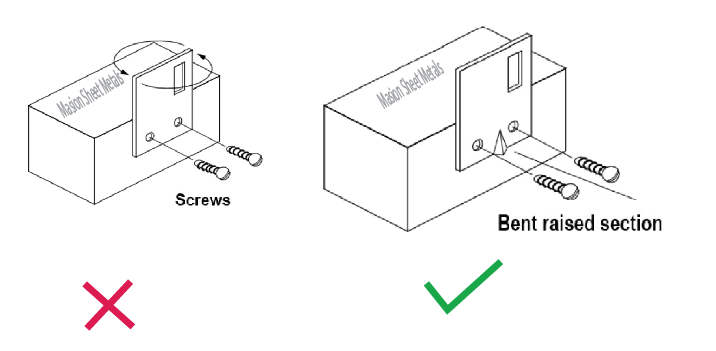 |
Ease of Location and Alignment
|
Misalignment of parts during assembly, increasing assembly time and errors. |
Lack of features that aid in part alignment and positioning. |
Include features like self-aligning tabs, tapered ends, or oblong holes that facilitate easy and accurate alignment of parts during assembly. |
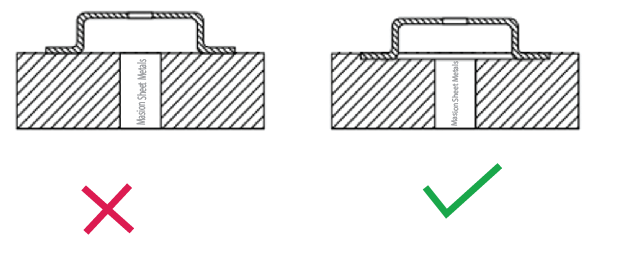 |
Ease of Fabrication
|
Manufacturing challenges and increased costs. |
The design does not consider manufacturing constraints or handling ease. |
Design parts with manufacturing constraints in mind, ensuring they can be easily fabricated and handled with available machinery. Consider splitting large parts into smaller, more manageable sections. |
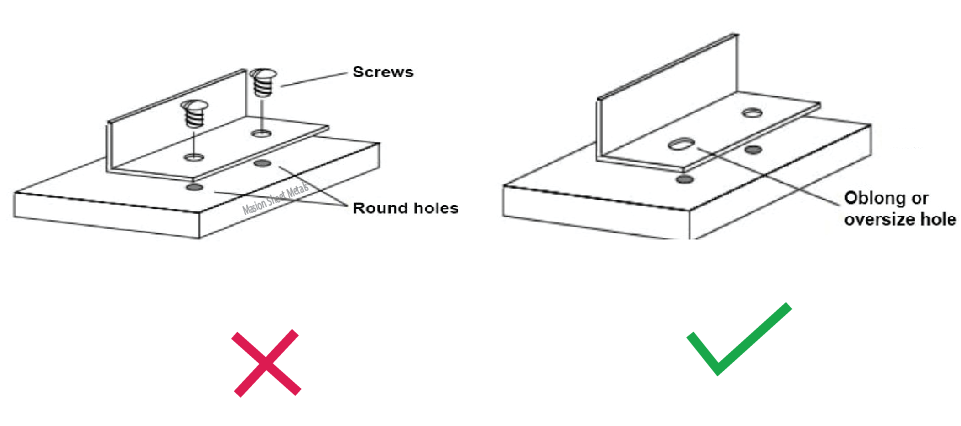 |
Fastening Methods
|
Assembly delays and increased costs due to improper fastening methods. |
Inappropriate selection of fasteners or reliance on welding. |
Choose fasteners that suit the specific function and installation process, considering material and cost. Minimize welding where possible, but plan for it when necessary. |
 |
Automation and Robotics
Robotic technology and automation have vast applications in the area of assembling sheet metals. They need shrinkage of labor costs, better security, and efficacy. Additionally, they allow for the creation of products at a faster rate. So, they mainly produce durable and accurate parts. Besides this, they also help to save floor space. But there are also disadvantages, of course. They include high initial costs to set up the system. The requirements for skilled technicians to program and maintain the robots. Moreover, they face issues regarding the safety of individuals in the vicinity. However, they have limitations as to the type of operation of a manufacturing process they can handle. But since they bring more efficiency and productivity to the business. They cannot be overlooked in many manufacturing industries.
Challenges and Solutions
Sheet metal assembly is the joining of separate pieces of sheet metal through various processes. It is done with the aid of fasteners and joining methods to create complex features and shapes. But it faces many challenges. Let’s discuss them here.
Challenges
- Warping and Distortion: This is a result of heat influence resulting from welding cutting, and forming stresses. It also occurs due to the use of thin materials.
- Tooling Wear and Maintenance: It occurs due to unreasonable usage, working with hard materials, and with a misaligned spindle. So, these all aspects can cause the tool to wear out and /or fail very quickly.
- Quality Control Issues: Variations in dimensions can lead to inconsistency in the part’s quality and structural weakness or cracks on the body surface. On the other hand, welds can also affect the quality of the part.
Solutions
- Preheating and Controlled Cooling: Reduce the thermal stresses because of subsequent warping and distortion of sections.
- Clamping and Fixtures: This should be done while processing the material to ensure that it maintains its shape and is very secure.
- Regular Tool Maintenance: The following are the possible objectives of conducting periodic inspections and replacement of wear-out tools to prolong tool life:
- Tool Coatings and Lubrication: To cut down on wear and improve the performance of the tools, they are required to.
- Statistical Process Control (SPC): Supervise various complex activities in the production line to promote uniformity.
- Automated Inspection Systems: It means the ability to detect defects using optical and CMM systems at the micro level as early as possible.
- Operator Training: Introducing enhancement in the handling and processing methodology that will help in reducing the formation of defects.
What are the Advantages and Limitations of Metal Sheet Assembly
Here is an appropriate table to discuss the benefits and limitations of metal sheet assemblies
Aspect |
Advantages |
Limitations |
Material Properties |
High strength-to-weight ratio, good corrosion resistance, versatile and durable |
Susceptible to deformation, requires protective coating for corrosion |
Manufacturability |
Easy to fabricate using standard processes, cost-effective for large production runs |
High initial setup costs for tooling, limited to certain thickness ranges |
Design Flexibility |
Easily modified and customized, suitable for a wide range of applications |
Complex designs may require multiple fabrication steps, limited to 2D shapes with some 3D forming |
Assembly |
Allows various joining methods, quick and efficient assembly processes |
Welding can cause warping and requires skilled labor, assembly methods can add weight and cost |
Cost |
Relatively inexpensive material, economical for mass production |
High cost for small production runs due to setup and tooling expenses |
Recyclability |
Fully recyclable material contributes to sustainable manufacturing practices |
The recycling process can be energy-intensive and requires the separation of coatings and contaminants |
Precision and Tolerances |
High precision achievable, consistent quality in mass production |
Precision can be affected by material properties, tight tolerances can increase costs |
Weight |
Lightweight compared to other materials like steel, reduces transportation and handling costs |
May not be suitable for very high-stress applications |
Why to Rely on Masion for Sheet Metal Parts Assembly Company?
- The top providers of sheet metal manufacturing for more than 17 years and have professional research and development.
- We organize our production facilities around 6 modern production lines. They are equipped with robotic technology to increase precision production.
- High-quality standards were achieved through obtaining several certifications, i.e. ISO9001-2015, ISO16949, ISO4001, and FSC.
- It has a square meters of 30000esters and has the capability of manufacturing plus than seven million parts for large orders to be delivered on time.
Conclusion
Sheet metal assembly is a vital technique in development. It focuses on the process of cutting, bending, and joining of the sheets. Besides this, it also deals with quality assurance to deliver standardized products. Moreover, challenges like warping, tool wear, and quality control problems can be tackled by this method. It uses heat treatment and cooling, proper tool upkeep, cutting and inspection technology, and better tools. As businesses grow where new technologies and quality improvement systems define their future. The sheet metal assemblies play their role in growth and competitiveness quest. It provides versatility and flexibility. So, the product parts can meet the ever-rising customer demands. Want to get your sheet metal assembled get quote from best in class metal parts assembly company.
Frequently Asked Question
Q1. What materials are commonly used in metal assembly?
Materials can be steel-carbon/wrought, stainless/galvanized; aluminum; copper & yellow/brass; and titanium/nickel alloys which have various characteristics as strength, corrosion, conductivity, etc.
Q2. What are the main methods for cutting sheet metal?
The three most common ones are mechanical cutting, which is different from laser and water jet cutting, chosen according to the thickness of the material, the level of precision needed, and the type of shape that the materials will have.
Q3. How is quality controlled in sheet metal assembly?
- CMM is used to measure and check dimensions and surface finishes.
- NDT is for checking the structural integrity of products by assessing surface flaws and cracks
- Optical inspection system used to measure and inspect surfaces for quality.