Progressive Die Stamping – Comprehensive Overview
Progressive die stamping is an advanced technique to produce highly precise metal parts. It optimizes the efficiency of the whole process throughout the production. So, it has wide applications in different industries. These may include the automotive and electronics industries. Thus, progressive die metal stamping is playing a significant role in the metal fabrication industry. So, in this article, we will look at the scope of its applications, advantages, limitations, and possible alternatives available in the market.
Table of Contents
ToggleDefining Progressive Die Metal Stamping
The metal stamping dies facilitate in manufacturing of the accurate and precise metal parts. It includes feeding of a metal strip through many dies. These dies feature series attachment and perform specific tasks, i.e. punching, bending, or forming, sequentially. Moreover, this process completes multiple operations in one continuous cycle. So, it gives precise parts repeatedly. It has wide scope in different industries, such as automotive, electronics and appliances. So, it is suitable for batch production.
Difference Between Progressive Die Stamping and Traditional Die Stamping
Both processes are popular for the manufacturing of metal parts. But they have different advantages and considerations. So, here is a comparison of traditional metal stamping and progressive die metal stamping . Understanding your needs will help you choose the right process.
Characteristics | Progressive Die-casting | Traditional Metal Stamping |
Process Type | Casting molten metal into dies | Shaping sheet metal with dies and press |
Material | Non-ferrous metals like aluminum, zinc | Sheet metals like steel, aluminum |
Production Rate | Slower due to casting and cooling | Faster with high-speed press operations |
Tooling Cost | Higher due to complex molds | Lower compared to die-casting |
Surface Finish | Excellent with minimal post-processing | May require additional finishing |
Strength and Durability | Excellent for parts | Good, especially for high-strength metals |
Components of Progressive Die Metal Stamping
So, let’s discuss its major components;
- Die Set: It provides a complete framework that holds all components of the die. Moreover, it gives support during the stamping process.
- Button Die (Bushings): It is located inside the die set. So, it gives alignment and support for the punches and other components of the machine.
- Punches: It is a kind of tool, that helps cut the required shape.
- Punch Holder: It holds the punches appropriately. Also, place it inside the die set.
- Plate (Section): It’s a separate component in the die set. So, it is used for metal forming and bending.
- Pins: It has many functions. They may include the alignment of different sections.
- Slug Clearance: It manages the removed material (slug) that whole process generates.
- Stripper: It is the best part to strip the finished part from the punches. It is usually done after each stamping cycle.
Progressive Die and Tooling
Types of Dies Used
Blanking Die
Blanking die cuts flat pieces (or blanks) of metal in the desired outline from a sheet of metal. It basically defines the initial size and the initial shape of the part before the rest of the operations are done. Blanking with precision reduces maverick behavior downstream.
Piercing Die
Piercing dies merely punch holes or slots in the metal strip leaving it in the coil. These are often the holes which guide alignment for the next stations. Avoid burrs and defects, clean piercings are important.
Forming Die
This forms dies bend or reshape the flat metal without cutting it forming flanges, curves or embossments. In this process the geometry of the metal is changed, but the thickness is kept the same. The structural features are commonly handled by it.
Drawing Die
Drawing dies deform the material so that it is stretched to an extent that will result into deeper cavities without tearing. They are used to make things such as cups, enclosures or hollow forms. There are lubrication and material flow control.
Cutting-Off Die
After all required operations are complete this die separates the final part from the continuous strip. It is normally the last stage in the progression. Cutoff is accurate so no damage to the finished parts.
Trimming Die
Forming or drawing is followed by trimming dies which remove unwanted material or refine edges. They give a clean, well defined finish and improves parts appearance. This is a very important part of final tolerance control.
Tooling Components Used
Die Set
The working dies and punches are housed in an upper and lower plate that comprise a die set. It keeps each press stroke well aligned and structurally supported. It must be set to withstand repeated high pressure impacts.
Punches
Hardened metal tools that press into or through the workpiece to shape or cut it are punches. The punch fits exactly into a corresponding die opening. Part quality cannot be achieved without proper punch wear monitoring.
Strippers
Strippers assist in the removal of the workpiece from the punch following each cycle so that it does not stick. They help maintain smooth material flow and proper press operation. There are two types: fixed and spring loaded.
Pilots
At each station, pilots fit into pre punched holes to guide and align the metal strip. They guarantee that accurate registration is obtained through the die. Cumulative misalignment without pilots could amount to scrap.
Bushings and Guide Pins
The upper and lower sections of the die are aligned with high precision by these components. Preventing tool shifting and repeatable positioning in each press stroke. They have a longer lifespan if they are properly lubricated.
Including Springs and Shims
Springs apply pressure or return parts to position and shims fine tune die height or gap spacing. In combination, they help balance the tool performance. Small corrections can be made without a full retooling by adjusting shims.
Progressive Die Stamping Process – Step-by-Step
So, here is the detail of the process that die stamping involves.
Designing Metal Part
The first step involves making the designs for the metal parts that you want to manufacture. So, the engineers consider several factors, i.e. intended function of the parts, dimensions, tolerance, material requirements, and any special features. Moreover, these designs need high accuracy and precise measurements. So, they are usually designed on advanced software like Computer-aided design (CAD). This software can design the metal part more precisely.
Stamping Die Design
In progressive sheet metal stamping, the multiple stations are present in sequence, inside a single tool. So, when the metal strip moves through the stations, they perform some specific operations on it. Here die plays an important role in carrying out each operation accurately. These operations may include geometries, precision machining, and heat treatment processes. So, the die must be designed with high accuracy and precision. So, it can manufacture durable tooling, that can tolerate high forces and repetitive use.
Metal Selection
Different metals have different properties. So, their application varies based on these properties. So, it is important to understand the material you choose to make your metal parts. This material selection depends on different factors, i.e. mechanical properties required for the part, cost considerations, corrosion resistance or conductivity. So, the common materials that progressive die stamping feature are steel, aluminium, copper, and alloys. Moreover, the material is injected into the machine as coils and sheets.
Cutting the Material
The first process involves the cutting of material. Here the metal sheet is fed into the press. Then the material is cut into blanks. The blank size is usually large than the requirement. So, it can tolerate stretching and deformation during the forming operations. Here are some steps that are involved in cutting the material.
- Shearing: It uses a pair of opposing blades to cut the edges of the metal. So, place the metal between these blades and apply downforce to cut it
- Punching: it includes a punch and die to cut the metal. Moreover, the punch applies force to the metal. The die supports it and defines the shape to cut the metal.
- Blanking: Here it uses blank dies to cut the outlines of the metal part. So, it retains the required shape and discards the excessive material.
Forming Operations for Metal Stamping Dies
The main goal of this step is to perform specific shaping operations. Ensure that you carry out these operations carefully. Otherwise, the issues may lead to problems, such as wrinkles, cracks, or string back. So, these operations may include.
- Bending: A metal part may require multiple bends to get the required shape. In this case, a bending punch and a die set are used to bend the metals.
- Drawing: In progressive die stamping the stretching of metal into a cavity refers to drawing. So, it can create protruding features. This process is usually used to produce cups and shell-like shapes.
- Coining: This is a process of giving the fine details to the metal part. Here the metal is compressed between two dies to give perfect surface finishing.
Piercing and Hole Making:
Sometimes you need to create holes in the metal. In this case, a piercing operation is used in custom metal stamping dies. This operation may include.
- Punching: It uses a punch and die to cut the holes and shapes of the metal. These punches are usually different shapes, i.e. square, round, or rectangular shape.
- Piercing: This process may include piercing the metal to create holes without removing the material. So, apply a localized force to carry it out.
Trimming and Shearing:
A trimming operation helps remove the excessive material attached to the edges of the metal part. So, it must be performed with precision, so you can avoid damage to the final part. Here are some operations involved in it.
- Shearing: This operation cuts the excessive material with the help of plates and cutting tools. It may include trimming the edges and unwanted features of the part.
- Notching: If you need small cuts or notches in the metal, this operation facilitates you.
Inspection of Metal & Quality Control
The quality control in progressive die stamping possesses an immense importance. It helps to evaluate whether the parts meet the required standards or not. So, these operations in it may include.
- Visual Inspection: It helps in identifying any defects in metal parts, such as imperfections, scratches, or discolorations.
- Dimensional Accuracy: Precision and accuracy are the first requirements of metal parts. So, dimensional measurements reflects if the part meets dimensional tolerances and specifications. Moreover, the checking tools used in this process are calipers, micrometers, or CMMs.
- Functional Testing: It ensures if the parts meet performance requirements like strength, durability, or fit with other components.
- Quality Control Measures: These measures helps identify and address any possible issues. Additionally, it reduces scrap and gives high-quality parts that are ready for shipment.
Stamping die design Process?
Designing progressive die metal stamping needs several key considerations. These factors can increase the efficiency and accuracy of the whole stamping dies process. So, these factors are enlisted below.
- check the requirements for the stamp part. These may include dimensions, tolerances, material specifications, and volume expectations. These considerations will help you in smooth flow. of entire progressive custom die metal stampings.
- The main purpose of the stamping die is. efficient manufacturing. So always consider features like uniform ball thickness, and smooth transitions, and avoid the sharp corners. These issues can cause tooling defects.
- Progressive die stamping is suitable for the simple geometries. So, always design the tools with fewer undercuts and no internal threads. Otherwise, they may complicate the stamping process.
- Always choose the material that has high strength, formality, and low cost. These materials may include aluminum, copper, and various alloys.
Tips to Design Main Components of Multi-station Progressive Die
Effective design of the main components gives accurate stamping tools. So let’s discuss designing of each component in detail.
Punch
Punches are used to cut and form the metal to get the desired shape. So, it must be accurately designed. It can increase the durability of the process and provide smooth and continuous flow. The stamping process can be of different types. Moreover, it may need different types of punches for effective performance. You must choose a material that can bear forces and high pressure. Here is a typical design for Punch
Concave Mold
It is the counterpart of the punch. It is used to shape the material as it is pressed against it. Additionally, the mold can be of different shapes and structures. These may include integral, block, or embedded block. These structures depend upon the complexity of the part. So, it must be designed for efficient material flow and smooth part formation. So, below is the typical; design for concave mold.
Guide and Positioning System
It helps to give accurate moments and positioning to the material throughout the progressive die stamping process. Moreover, guide pins and side blades are commonly used for initial positioning. On the other hand, guide plates and strips are used to control the position and feeding distance. So, choose the material, which has low friction and high wire resistance for guide components.
Belt Guide and Supporting Device
These components help with the appropriate feeding of the strip. Sometimes the material deforms during the stamping process. Here these components play a key role. They allow the curved parts not to interfere with the die cavity wall. This mechanism can be optimized using floating support devices and guides. So, choose the material and configurations that can help in the prevention of material deformations.
Unloading Device
This component is used to perform specific operations. These may include pressing, unloading, and protecting the metal stamped part. Moreover, it has a segmented assembly structure. It helps in the installation of upper mold using discharge screws. To design this component, you can use different features like segmented assembly and discharge screws. They will help in easy installation and adjustment.
Limiter
The limiter is responsible for the installation, debugging, storage, and transportation of the mold. It gives a reference point to align and secure the mold components in multi-station progressive die stamping. You must add features like reference points and a locking mechanism. They will help in securing the positioning.
Machining Direction Conversion Mechanism
It is used to convert the machining direction within the die. It allows more complex stamping operations. These may include a wedge slider mechanism or a lever mechanism. To design them, You must consider space treatment and compatibility with different components in the die assembly. Here are some Typical designs for different Mechanisms.
Micro Adjustment Mechanism of Forming Punch
This mechanism adjusts the forming punch position. Moreover, this is responsible for. precise part formation and minimizing the defects. So, you can add features like alignment, clamping, and attachment of other die components in its designing part.
Overview of the Classifications of the Progressive Metal Die Stamping Process
After discussion, here is the table that will give you a small overview of the classifications of the Progressive die stamping process.
Process | Description | Geometry | Simplified Shapes |
Cut | The plate part cut on blank, resulting in bending. | Varies | ![]() |
Trimming | Excess material cut off the edge of the semi-finished product after drawing or forming. | Varies | ![]() |
Bending | In progressive die stamping, Mold bends material into a specific shape (V/U/Z-shaped). | V, U, Z | ![]() |
Rounding | The ends of the sheet are rounded. | Circular | ![]() |
Twist | One part of the plate twisted at an angle relative to another. | Helical | ![]() |
Deep drawing | The sheet is pressed into the hollow workpiece, maintaining wall thickness. | Cylindrical, Spherical | ![]() |
Thinning and Deepdrawing | The size of the hollow part changed by reducing the diameter and increasing height for the required thickness. | Conical, Cylindrical | ![]() |
Hole flanging | The edge of the hole on the sheet or workpiece turned into the upright edge. | Circular | ![]() |
Outer edge flange | The outer edge of the workpiece is turned into an arc or curved vertical edge. | Arc, Curved | ![]() |
Reducing themouth | The mouth of the hollow piece is reduced. | Circular, Oval | ![]() |
Expanding | The mouth of the hollow piece expanded, often for pipes. | Circular, Oval | ![]() |
Waving | Ribs, patterns, or text embossed on a sheet or workpiece, thinning the entire area. | Textured | ![]() |
Curling | Edge of hollow piece rolled into a specific shape. | Rolled, Curled | ![]() |
Bulging | Part of the hollow piece expanded radially, forming the convex shape. | Convex | ![]() |
Spinning | Rods or rollers are used to press the sheet blank into the desired shape. | Conical, Cylindrical | ![]() |
Shaping | In progressive die stamping, correcting and shaping contribute to accurate shapes of workpieces. | Custom | ![]() |
Levelling | Uneven surface or bend flattened. | Flat | ![]() |
Imprinting | The thickness of the workpiece changed, and text or patterns were embossed on the surface. | Textured | ![]() |
Forward extrusion | Metal blank undergoes plastic deformation, extruded from the die hole in the punch movement direction. | Extruded | ![]() |
Reverse extrusion | During metal extrusion, plastic flows in the opposite direction of punch movement. | Extruded | ![]() |
Compound extrusion | Combination of forward and reverse extrusion. | Extruded | ![]() |
Overview of the Classification of the Die Stamping Process
Structural Composition of Multi-Station Progressive Stamp
The multi-station progressive dies are composed of upper and lower molds. The upper mold has components, like the upper mold base, backing plate, punch fixing plate, discharge back plate, and discharge plate These all parts feature connections with the press via a T-shaped screw block. While the lower die is composed of a die base, pad, and concave die fixing plate. Moreover, they are fixed with a press workbench.
The multi-station die is categorized into the following processes.
Fixed Guide Plate Multi-Station Progressive Stamping Die
This die has no additional guide pillar between the templates. It only uses a medium-precision standard mold base. Moreover, the fixed guide plate is used to position and unload the strips. This kind of die is suitable for the specific raw material thickness, batch production, and product accuracy requirements. Here is a schematic diagram of the fixed guide plate die.
Semi-Elastic Plate Multi-Station Die Stamped
Semi-elastic die uses a pressure plate. It simplifies the structure and reduces the cost of production. Moreover, it uses a mold base with medium to high precision. So, it is suitable for raw material thickness, bulk production, and product accuracy with stability.
Integral Elastic Plate Multi-Station Progressive Stamping
This die is divided into type A and type B. So, it uses integral elastic pressure plates for guiding throughout the stamping process. It is structural properties may include a high-precision standard mould base. So, it has specific applications based on raw material thickness, production volume, product precision, and mold stability. It is a design principle focused on a precise connection and downward bending. So, here is a schematic diagram of an integral elastic plate.
Segmented Elastic Plate Multi-Station Stamping Die
This mold is designed for higher stamping speeds and improved efficiencies. It is mainly used for independent units which have high-grade precision mould bases, guide columns, elastic pressure plates, and precise positioning mechanisms. It has wide applications in Ultra-large batch productions and high-pressure requirements. Moreover, it also has a scope of application in rapid production replacement and ultra-speed stamping.
Comparison of Progressive Stamping Die vs Other Stamping Methods
Metal industries have wide options of methods to convert the metal into desired parts. Every method has its pros and cons. In this aspect, progressive die metal stamping is also popular. It has a wide scope of applications in different industries. There are some alternatives to progressive stamping die . So, let’s discuss the functioning of the methods available in the market.
Progressive Die Metal Stamping – Table of Comparison
Aspect | Progressive Die Metal Stamping | Single-Stage Stamping | Transfer Stamping | Four-Slide Stamping |
Operation Complexity | Multiple operations performed in a single die | The single operation performed in one stroke | Multiple operations performed in multiple dies | Multiple operations performed using sliding tools |
Tooling Complexity | Highly complex, with multiple stations in a single die | Relatively simple, with one set of dies | Complex, with multiple sets of dies and transfer mechanisms | Complex, with multiple sliding tools |
Setup Time | Longer setup time due to the complexity of the die | Shorter setup time as only one set of dies is required | Longer setup time due to multiple dies and transfer mechanisms | Moderate setup time, depending on the complexity of the part |
Material Utilization | High material utilization as multiple parts can be produced from a single strip of material | Moderate material utilization as only one part is produced per stroke | Moderate material utilization as scrap material between operations may occur | High material utilization as the material is fed continuously |
Production Rate | High production rate for high-volume production | Moderate production rate | Moderate to high production rate, depending on the number of transfers | Moderate to high production rate, depending on the number of slides |
Tooling Cost | Higher initial tooling cost due to the complexity of the die | Lower initial tooling cost | Higher initial tooling cost due to multiple dies and transfer mechanisms | Higher initial tooling cost due to the complexity of the tooling |
Flexibility | Lower flexibility for changes in part design or production volume | Higher flexibility for changes in part design or production volume | Moderate flexibility for changes in part design or production volume | Moderate flexibility for changes in part design or production volume |
Scrap Generation | Minimal scrap generation as parts are closely nested on the strip | Moderate scrap generation due to the separation of parts | Moderate scrap generation due to the separation of parts and the transfer process | Minimal scrap generation as parts are closely nested on the strip |
Comparison Table for Progressive Die Metal Stamping and Other Processes
What are the Advantages of Progressive Die and Stamping?
Progressive die & stamping is an advanced method to make highly precise metal parts. So, it has wide applications in different industries. Let’s explore the benefits of this process;
- High Efficiency. It allows the simultaneous execution of multiple operations in a single press cycle. So, it gives high production rates. Moreover, it is more efficient than the traditional stamping method.
- Cost-Effectiveness: Progressive stamping dies operates multiple operations at a time. So, it cuts the labour cost and cycle time. It gives lower per-part cost for bulk productions.
- Consistent Quality: This process gives a consistent part-to-part quality and dimensional accuracy. So, it has a precise nature. Moreover, it results in fewer defects and rejections and improves the overall production quality.
- Complex Geometries: Progressive die metal stamping can accommodate complex parts and intricate geometries which are difficult to achieve. So, this is versatile and gives greater design freedom and innovation.
- High Precision: It allows tight tolerance and excellent reputability, so it. just stand part meets specific dimensional requirements with accuracy.
- Reduced Secondary Operations: Manufacturing of metal parts requires secondary operations like machining, welding and assembling, but in stamping die, multiple operations are integrated sequentially in the same tooling system. So, it reduces both the time and manufacturing cost.
What are the Disadvantages of Progressive Stamping Metal Die
As a stamping metal die has many advantages. It has some limitations as well. So let’s discuss its disadvantages here.
- It has a high initial tooling cost for setup.
- This process requires regular maintenance and occasional replacement of dies.
- Some complex geometries and materials are difficult to handle.
- If an error appears during the process. It can lead to scrapped or defective parts.
- Although this technique is suitable for bulk productions. However, it is not cost-effective for small quantities.
Applications of Progressive Stamping Die Process
Progressive die stamping is quite famous for its versatility and efficiency. It is a mostly used method to produce complex metal parts. So, it has various applications in the industry. These may include.
Automotive Industry
It is frequently used in this sector for the manufacturing of components, i.e. brackets, clips, connectors, and structural parts. These parts are important for the vehicle assemblies. They have high strength to offer. They are durable and have precise fitment.
Electronics and Electrical Appliances
The progressive stamped die method is used to produce components like connectors, terminals, and shields for electronic devices. Moreover, they have wide applications in the manufacturing of electrical appliances like housings, enclosures, heat sinks, etc.
Aerospace and Aviation
This process is important when it comes to precise and complex geometries. So, it has wide applications in the aerospace innovation sector for the manufacturing of components.
Consumer Goods
This process is famous for producing various consumer goods like kitchen appliances, furniture, hardware, and decorative items. Moreover, it is quite cost cost-effective manufacturing process and can create complex designs with precise dimensions.
Medical Devices
Progressive die metal sheet stamping has various applications in the production of medical components and equipment. These components may include surgical instruments and implantable devices. It is also used to manufacture diagnostic tools or equipment that require high precision and biocompatibility.
Renewable Energy
One of the most important applications of progressive die sheet metal stamping is the production of complex metal parts for renewable energy systems. These systems may include solar panels and wind turbines. Additionally, the components required in these systems are bracket brackets, frames, and structural supports.
Choose Masion for Progressive Stamping Die Design Services
Masion provides advanced progressive die stamping services for manufacturing metal parts. We have a well-equipped facility with highly experienced staff. Moreover, we deal with different types of metals. So, if you are looking for design consultation, tooling fabrication, and high-volume production. Masion is here to cater for your all requirements. Regardless of size, we take a minimum order of one part and produce parts in bulk. So, do not go anywhere. Contact us now!
Conclusion
In conclusion, progressive die metal stamping effective process for the manufacturing of metal parts. It gives accuracy and uniformity in every design. Progressive stamped die is comprised of multiple processes. They work within a single press cycle and streamline production. This process is beneficial for high-volume outputs and producing highly complex shapes.
Progressive die and stamping has a wide scope of applications in different industries, such as electronics, electrical appliances, aerospace aviation, and automotive industries. Besides its advantages, there are some limitations of progressive metal dies and stamping. For example, it is not cost-effective for low-volume productions.
Frequently Asked Questions
Q1. What materials are suitable for the progressive die metal stamping process?
It commonly uses materials with specific properties, i.e. strength, conductivity, corrosion resistance, and machinability. They may include steel, aluminium, copper, and brass.’’
Q2: What is the difference between die stamping and die cutting?
Stamped Die is the shaping of a metal sheet into a specific form. It generally uses a press and a die. while die cutting is the cutting of material like paper, cardboard, or fabric into specific shapes. It generally uses sharp-edged tools, known as die.
Q3: How would you define a progressive stamping press?
It is a machine that is used to convert the metal into a specific shape. Progressive die stamping press is comprised of multiple Stations that are aligned inside the tooling system. This machine produced highly accurate and precise metal parts.
More Sources:
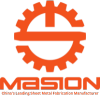
Send Your Inquiry Today



+86-18969433502

sales@sheetmetalmasion.com