A Comprehensive Guide to High-Speed Stamping, Its Process, and Application
High-speed stamping is an important process in manufacturing. It allows the production of quite a large amount of highly precise parts in less time. So, this technique is critical in industries, i.e. automotive, electronics, and aerospace industries. Due to sophisticated equipment and practices typically applied in high-speed stamping, its turnaround time, as well as the cost of production, can be considerably minimized. Besides this, it always maintains the quality levels. So, in this article, we will discuss high-speed stamping, its processes, uses, advantages, and disadvantages.
Table of Contents
ToggleDefine High-Speed Stamping
High-speed stamping is a metal forming technique that involves the usage of a stamping press. So, it can create or cut a material especially metals, at very high rates. In many ways, the high-speed stamping press is distinct from traditional stamping. Because they work at a slow speed. However, high speed can make several hundred or even thousands of strokes per minute. As they work at a very high speed, Manufacturers can make many parts in a relatively short time. Besides this, the process is very useful in large production runs.
Components of High-Speed Stamping Press
High-speed stamping presses are made up of the following components to accomplish fast and accurate stamping. These include:
Frame
The applied frame is an important component of the high-speed stamping press system. It maintains the integrity of the press. Besides this, it also takes up the loads and forces of the stamps during the stamping operations. It is a prerequisite that the frame be rigid during stamping to ensure precision. Moreover, it helps avoid or minimize variation in the stamp produced.
Flywheel
The flywheel can be a means for storing energy created by the motor of the press. This energy is essential because it makes the stamp strike. Consequently, the energy that was stored previously is also released slowly. As a result, the ram hits the metal with the required force and velocity.
Crankshaft
The crankshaft is one of the mechanical parts that converts rotatory motion into linear motion of the flywheel. It operates as a converter converting the circumferential movement of the flywheel into the to-and-fro movement. So, it is ideal for the ram to apply the right amount of force for stamping.
Ram
Ram is the reciprocating part of the press that applies the stamping force on the metal workpiece. It rises and falls in a very orderly manner mainly. It usually happens due to the up-and-down motion of the crankshaft. The moving of the ram is very sensitive and fast to ensure that it provides accurate and consistent stamping.
Die Set
The tooling is made of the upper punch called an upper die and the bottom punch or lower die. These two stamps move oppositely. Here, the upper one goes down to press the lower one, and the latter forms or cuts the metal sheet. Die layout and setup are important when it comes to the quality and the details of the stamped parts.
Automation Systems
High-speed stamping presses benefit from automation systems. It helps improve the effectiveness of carrying out processes. They include feeders that transport the metal sheets to the press area, and transfer systems that move the formed parts through the production process. Besides this, sensors help regulate the forming process. They create flow, constant flow, and minimize handling. So, the change creates interruptions in these systems.
What are the Types of High-Speed Stamping Press
Here are different types of high-speed stamping presses. Let’s discuss them briefly:
Mechanical Presses
The mechanical presses are again faster and more accurate. Besides this, they use mechanical interconnections of linkages along with flywheels to produce stamping force. They work rather fast, sometimes at a rate of several hundred strokes per minute. So, they are perfect for large-scale manufacturing. Due to their reliable and constant results, such instruments have applications in automobiles, electronics, and the consumer durables industry.
Hydraulic Presses
Hydraulic presses help generate force using hydraulic cylinders which has numerous applications. These applications can require both, the force and the speed at which the force is applied to be controlled to a large extent. These presses are not as fast as the mechanical presses. They generally come with the flexibility of use and can carry out the forming and drawing formations. They are suitable for such sectors as the aerospace and automotive industries. These industries may require the formation of complex and strong parts.
Servo Presses
The servo presses employ servo motors. So, they can achieve better speed and accurate control. So, they are more like both, the mechanical as well as hydraulic presses. It presents programmable motion profiles that make movement adjustments during stamping. Servo presses are energy efficient and used in industries involving high accuracy. These sectors can be medical equipment, automotive, and electronics.
Suitable Materials for High-Speed Stamping
So, here are some materials that are widely used in the high-speed stamping process. Let; ‘s discuss them in detail.
- Low-Carbon Steel: Easy to work on due to its formability and ductility, low-carbon steel is cheap. So, it has several applications in industries that produce large quantities of complex products.
- Stainless Steel: High tensile strength and also has corrosion resistance but, it is harder. It has fewer applications in purposes and practices where strength and protectiveness from the environment are needed.
- Aluminum: Aluminium is relatively light, highly ductile, and can be easily shaped. So, it is useful where weight concerns are important, i.e. vehicle construction and similarly in aircraft.
- Copper: It has outstanding conductivity and ductility but can be deformed easily. So, it has numerous applications in the electrical and thermal industries.
- Advanced High-Strength Steels (AHSS): Has better strength and mechanical properties than aluminum. Besides this, it is suitable for high-strength requirements, i.e. vehicle structures.
What are High-Speed Stamping Processes?
Here is the step-by-step process of high-speed stamping.
Step 1: Material Preparation
So, the preparation of materials is the first significant factor in the high-speed stamping process. It envelops the proper choice of raw material. So, it is mostly in metal sheets or coils with a particular characteristic of the final product in mind. This selected aluminum may vary from steel or copper depending on strength flexibility and conductivity. The material selected is in coils, then it is stripped off and straightened for feeding to the press. Afterward, this process erases any bends or kinks that may interfere with the stamping process in the manufacturing line. In addition, the material passes through a washing process. So, it may allow the removal of dust, oil, or whatever oxidation is present. This guarantees a clean surface and helps avoid the formation of defects on the stamped parts.
Step 2: Feeding the Material
Feeding the material is the second step of the process. It involves the preparation of the cloth before it is immersed in the dye. So, here the prepared material is then forwarded to the high-speed stamping press system through an automatic feeder. This system provides the benefit that material is accurately and consistently located. It ensures that this is crucial to sustaining the press’ high operating rate. Sensors and guides perform intensive work in this stage. Here, the material needs to be correctly positioned along the line of the dies for each stroke. This alignment is important in confirming that the position of the die is correct to give the right stamping for the parts without any mistakes.
Step 3: Stamping Process
The framework of the operation takes place in the stamping process. Here the flywheel operated using an electric motor stores the mechanical energy in terms of rotation and utilizes the same in stamping. It uses the crankshaft to do this; the crankshaft translates circular motion into linear and lets the ram go up and down. The ram then pushes the upper die onto the material on top of the lower die. Afterward, this part trims extrudes, bends, or molds the material into the required shape. In this step, emphasis is put on speed and precision which is the strength of pressing. It helps ensure the production of numerous parts with very close tolerances.
Step 4 – Removal and transferring of the part
Here, we use tools for the stamping process. The parts have to be removed and shifted to other areas for further work. Moreover, the release system ejects the finished parts out of the die area as soon as they are produced. Afterward, conveyors transfer the finished parts out of the press area, for further processes. There is also automated transfer, which is important for prolonging the functionality. It also increases the process rate to avoid long breaks between stamps.
Step 5: Quality Control and Inspection
Quality control and inspection processes help verify that the stamped automotive parts match specific standards and quality. These are in some cases incorporated into the production line. So, that there is constant monitoring for defects or variations. They also satisfy the level of compliance for each component of the systems to the expected high levels. Further, end-of-line checks whether by hand or through automatic means. For traceability and improvement of the process, workers keep the proper record. They also make sure that quality is maintained in the stamping process.
Step 6: Secondary Operations (if needed)
In addition, some operations are performed after the initial stamping called secondary operations. Some of these are as follows; deburring is the process of removal of sharp points or edges to make them safe for use and of high quality. It can also help improve material properties, i.e. tensile strength and hardness through controlled heating and or cooling. Also, some other operations that create a coating for the parts may be involved in it. They help enhance the looks and performance of the parts. These secondary operations make the final parts ready for the intended applications.
Step 7: Packaging and Delivery
The last and the most important operation in high-speed stamping is the packing and delivery of the produced items. Some of the major production and business perks of stamped parts include the fact that parts are packed carefully. So that, they should not be harmed in any way before they are delivered to the customer. It entails aspects, i.e. the use of tags with efficient information including part numbers, quantities, and destination. When produced, such final products are packed and supplied to a customer or the next processing center. This step is the final process of production and provides stamped parts with desirable qualities.
Design Tips for High-Speed Stamping Process: Problem, Cause, and Solution
Tip | Problem | Cause | Solution |
Material Selection | Inconsistent stamping quality | Poor material ductility or varying thickness | Choose materials with good ductility and consistent thickness to ensure smooth and efficient processing. |
Optimize Part Geometry | High defect rates and slower production speeds | Complex shapes and intricate features | Simplify part designs to minimize complex shapes and intricate features, reducing the risk of defects and ensuring higher production speeds. |
Die Design | Inaccurate or inconsistent stamping results | Poor die design, misalignment, or insufficient clearance | Design dies with high precision and durability. Incorporate features like guide pins, alignment tools, and proper clearances to maintain accuracy and consistency. |
Lubrication | Increased wear and friction, leading to tool failure | Inadequate or inappropriate lubrication | Ensure adequate and appropriate lubrication to reduce friction, prevent wear, and enhance the longevity of dies and tools. |
Tooling Maintenance | Downtime and reduced tool performance | Lack of regular maintenance and inspection | Implement regular maintenance schedules for tooling to prevent downtime and maintain optimal performance. |
Tolerances and Clearances | Burrs, fractures, and material deformation during stamping | Incorrect tolerances and clearances in die design | Accurately determine and maintain proper tolerances and clearances to ensure clean cuts, prevent material deformation, and maintain part integrity. |
Advantages & Disadvantages of High Stamping Stamping
Benefits
- Increased Productivity and Efficiency: These tools can make as many as 2000 strokes in one minute or even more. So, it drastically increases production and shortens lead time.
- Economical Solution: Cost reduction and shortened time-to-market are two key drivers in the current modern and advanced economy. Thus, high-speed stamping offers the potential to reduce the costs of manufacturing and shorten the time to market for new products.
- Punctuality and accuracy: High-speed stamping also minimizes variations in the dimensions of the metal parts. So, it is important in the optimization of quality in large-scale manufacturing.
- Operate with a range of materials: It can be used on metals, plastic, and composites. So, it makes high-speed stamping, applicable in many fields.
- Environmental Benefits: Energy conservation and operational changes in high-speed stamping show the possibility of minimizing material and energy consumption. So, it has negative effects on the environment compared to other methods.
Limitations
- High-speed stamping needs complicated machinery and automation systems. So, these are capital-intensive in the first place.
- The solution also provides only a limited freedom of design for the stamp.
- High-speed stamping particularly applies in the mass production of identical components. It is less flexible for delivering particular or intricate models.
- It includes power operations at very high speeds, and this exposes the workers to certain risks if not well controlled.
- There is a high need for safety measures and training that are sufficient to handle crises in the field.
- The operators and the maintenance personnel must undergo special training. So, they can enable them to work on complex equipment and high-speed stamping
High-Speed Stamping vs. Traditional Stamping Processes
Aspect | High-Speed Stamping | Traditional Stamping |
Production Speed | High (several hundred to thousands of strokes per minute) | Moderate to Low (fewer strokes per minute) |
Productivity | High | Moderate to Low |
Precision and Consistency | Very high due to advanced automation and precise control | Variable depends on machine type and operator skill |
Initial Investment Costs | High due to advanced machinery and automation systems | Lower compared to high-speed stamping equipment |
Flexibility in Design | Limited, best suited for standardized high-volume parts | Higher flexibility, suitable for custom and complex designs |
Material Utilization | Efficient use of materials, minimal waste | More material waste compared to high-speed stamping |
Maintenance Requirements | Regular and specialized maintenance needed | Less frequent but still requires regular maintenance |
Operator Skill Level | Requires specialized training | Requires skilled operators but less specialization |
Applications | Ideal for high-volume production (automotive, electronics) | Suitable for low to medium-volume production |
Environmental Impact | Lower, due to efficient material use and energy consumption | Higher, due to less efficient processes |
Cost Efficiency | High over the long term due to reduced production costs | Variable depends on production volume and complexity |
Safety Concerns | Potentially higher, requires robust safety measures | Lower compared to high-speed operations |
Maintenance of High-Speed Stamping Presses
It has become important to maintain high-speed stamping presses to increase its useful life as well as to get the best out of it. This includes:
- Routine Inspections: Routine inspections of the components and systems to determine if they have worn out, or not.
- Lubrication: Check and make sure that all sleeves, rods, shafts, and gauges that need to be lubricated to reduce their frictional force and constant friction wear are lubricated adequately.
- Calibration: Adjustment of the press for familiarity and accuracy to get regularly.
- Replacement of Parts: Making minor repairs periodically especially when noticing that some parts of the machine are likely to break down.
Factors to Consider When Choosing High-Speed Stamping
When choosing a high-speed staking machine the following factors have to be taken into consideration:
- Required Production Volume: High-velocity stamping is suitable for substantial production. If the production requirements meet its description, then incorporating this process can be feasible.
- Other Complications: Determine the level and configuration of the subassemblies you are going to manufacture. High-speed stamping, in that case, is ideal where there are standardized many parts.
- Available Budget and Resources: Think about the cost that will be required at the time of purchasing, and maintaining the equipment, training employees on how to use the equipment. FPS is a heavy investment process. However, it can lead to tremendous cost savings over the asset’s life cycle.
High-Speed Stamping Applications
High-speed stamping is widely used across various industries for producing components such as;
- Automotive Parts: Such as brackets, connectors, and structural parts.
- Electronic Components: Including for example connectors, terminals, and any other parts used in circuit boards.
- Medical Devices: These can be employed in the production of parts such as precision parts of surgical instruments and diagnostic equipment.
- Consumer Goods: Like metal used in the construction of housing of goods, metallic fasteners as well as trinkets among others.
Tolerance Ranges for High-Speed Stamping process
Here is a detailed table for the tolerance ranges required in the speed stamping process.
Part Feature | Tolerance Range | Explanation |
Material Thickness | ±0.05 mm to ±0.1 mm | Ensures consistent thickness for uniform part quality and performance. |
Die Clearance | 10% – 20% of material thickness | The gap between punch and die for clean cuts and minimal deformation. |
Hole Diameter | ±0.05 mm to ±0.1 mm | Precision in hole size for proper fit and assembly. |
Part Dimensions | ±0.1 mm to ±0.2 mm | Ensures parts fit correctly in their application. |
Edge Radius | ±0.1 mm to ±0.2 mm | Smooth edges to reduce stress and prevent cracks. |
Flatness and Parallelism | ±0.1 mm to ±0.2 mm | Maintains part accuracy and proper fit. |
Angular Tolerance | ±0.5° to ±1° | Ensures accurate alignment of features. |
Surface Finish | Ra 1.6 µm to Ra 3.2 µm | Smooth finish for appearance and function. |
Flatness Across a Large Surface | ±0.2 mm to ±0.5 mm | Prevents warping in larger stamped parts. |
Corner Radii | ±0.1 mm to ±0.2 mm | Smooth transitions to avoid sharp edges. |
Stamping Complexity and Design Considerations
So, the following are the design considerations for high-speed stamping
Stamping Complexity
Stamping complexity deals with the degree of difficulty of the contour and dimensions of the part design. The formability of high-speed stamping is versatile when it comes to making designs. However, complexity does influence certain characteristics of production.
Geometry
- These may include;
- Complex Features: The models with complicated shapes, spikes /edges or undercuts, and recessed areas /features may be difficult. So, they may need sophisticated toolings and dies.
- Simplification: Simplifying the geometry of part can improve the rate of the process and also decrease the rate of defects. So, always prefer making parts of equal structure and less curvature as far as possible.
Tooling and Dies Precision
High-speed stamping involves the use of too many tools and dies. Therefore, the two have to be well-designed. Complex parts may require special tooling, i.e. die that has features such as guide pins and alignment tools.
Durability
Tooling must be sufficiently strong to withstand the high-speed operation mainly for the complicated shape of the mold. So, it may produce a high force on the dies.
Material Flow
This may include;
- Uniform Flow: When a piece consists of numerous different components and subsystems, it may cause low uniformity. If the part has complex shapes or if the wall thickness of the plates changes. These are the areas where material flow is disrupted leading to defects.
- Design for Flow: Stopper parts should be designed such that there are smooth changes in thickness and contour. Otherwise, they may cause problems in stamping.
- Production Efficiency, Cycle Time: Complex parts may promote the cycle time and as such they will slow down the production process. They must find adequate ways of providing a design complex enough to accommodate the desired functionality. But, they must be simple enough to be produced rapidly.
Automation
Automation systems such as feeders and transfer mechanisms should be integrated. So, they can guarantee control of the difficult parts and at the same time increase the production rate.
Cost Implications and Initial Investment
Some designs integrated call for expensive tooling and die preparations. So, it may increase the overall cost features.
Maintenance
Complex tooling may also need more maintenance. Because of its robustness, it eventually affects the overall efficiency in the long run.
Conclusion
In conclusion, High-speed stamping includes the design making to meet specific objectives. So, it can support efficient production processes. It is always essential to address such small profile part geometries. Besides this, it is equally important to provide feasible tooling and die designs to get accurate fast production. Here, make sure to reduce product complexity as much as possible. Also, standardize the material flow, and incorporate higher levels of automation. It will ultimately help improve the product’s production efficiency and decrease the defect rate.
Frequently Asked Questions
Q1. What are the basic Classification of High-Speed Stamping Presses?
There are Mechanical Presses, Hydraulic Presses, and Servo Presses. Mechanical presses can produce at a very fast rate and hydraulic presses offer more control of force. Besides this, servo presses take advantage of both, being precise and fast.
Q2. Which material is ideal for high-speed stamping?
Some of the suitable materials are low-carbon steel, stainless steel, aluminum, and copper.
Q3. What are the main differences between high-speed stamping and other types of stamping technologies?
Traditional stamping is somewhat different from high-speed stamping in that the latter usually runs much faster, increasing productivity. At the same time improving accuracy. This also improves the production of complicated parts compared to the conventional methods of production.
Q4. What factors should be given the attention they conducting design of parts on high-speed stamping?
Some of the principal concerns are reduction of part complexity, proper selection of the tools and die, control of material and its flow, productivity enhancement, and cost aesthetics.
Q5. What maintenance do High-speed stamping presses require?
Maintenance includes systematic inspections of the worn-out parts and replacing them. It also involves greasing of every moving part, and examination of the die and the tool in use. This is something that has to be done regularly to confirm that the equipment is running optimally and to avoid costly breakdowns.
Q6. What are the benefits and drawbacks of high-speed stamping?
Among the benefits of high-speed stamping, one can distinguish the increased rate of production, reduction of expenses, and nuts-and-bolts accuracy. But they also have disadvantages like prohibitive setup costs, restricted versatility, potential for risks, and a professional’s necessity for expert skill.
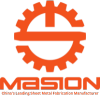