Deep Drawn Metal Stampings – Everything You Need To Know
Deep drawn metal stamping is thus a flexible technique that you can employ to make numerous sheet metal products. This guide contains all the information that you would want to know about deep draw stamping. You will get to understand its advantages and disadvantages, materials to use, and the procedures involved. Well, without further ado, let’s immerse yourself and get acquainted with all the necessary information.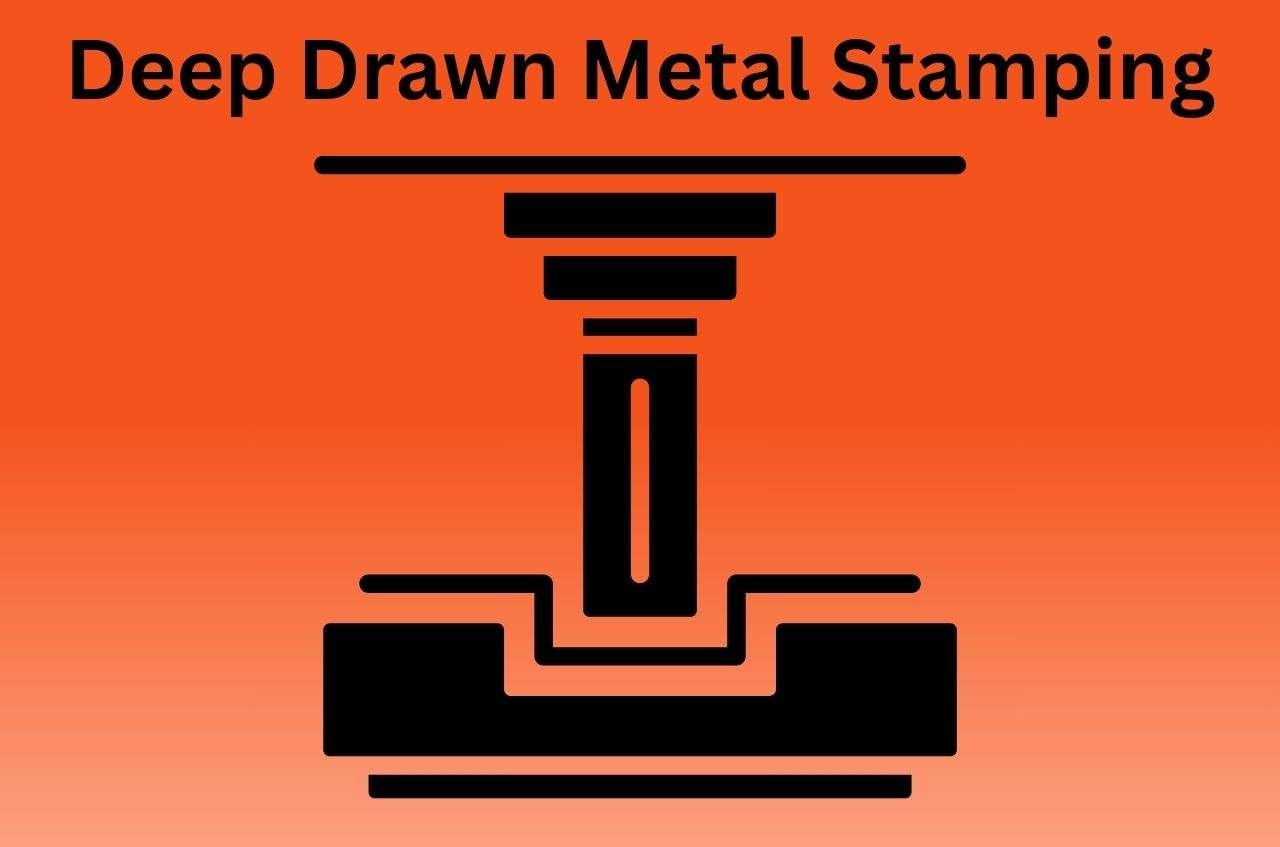
Table of Contents
ToggleUnderstanding Concept Behind Deep Drawn Metal Stampings
Metal stamping through deep drawing is a technique where sheet metal is formed into a cavity, cylinder or cup with the help of tensile or compressive forces. This makes it possible to build complicated forms of great accuracy and rigidity. The process involves forming a flat sheet of the metal and making it assume the required shape and size without compromising its strength.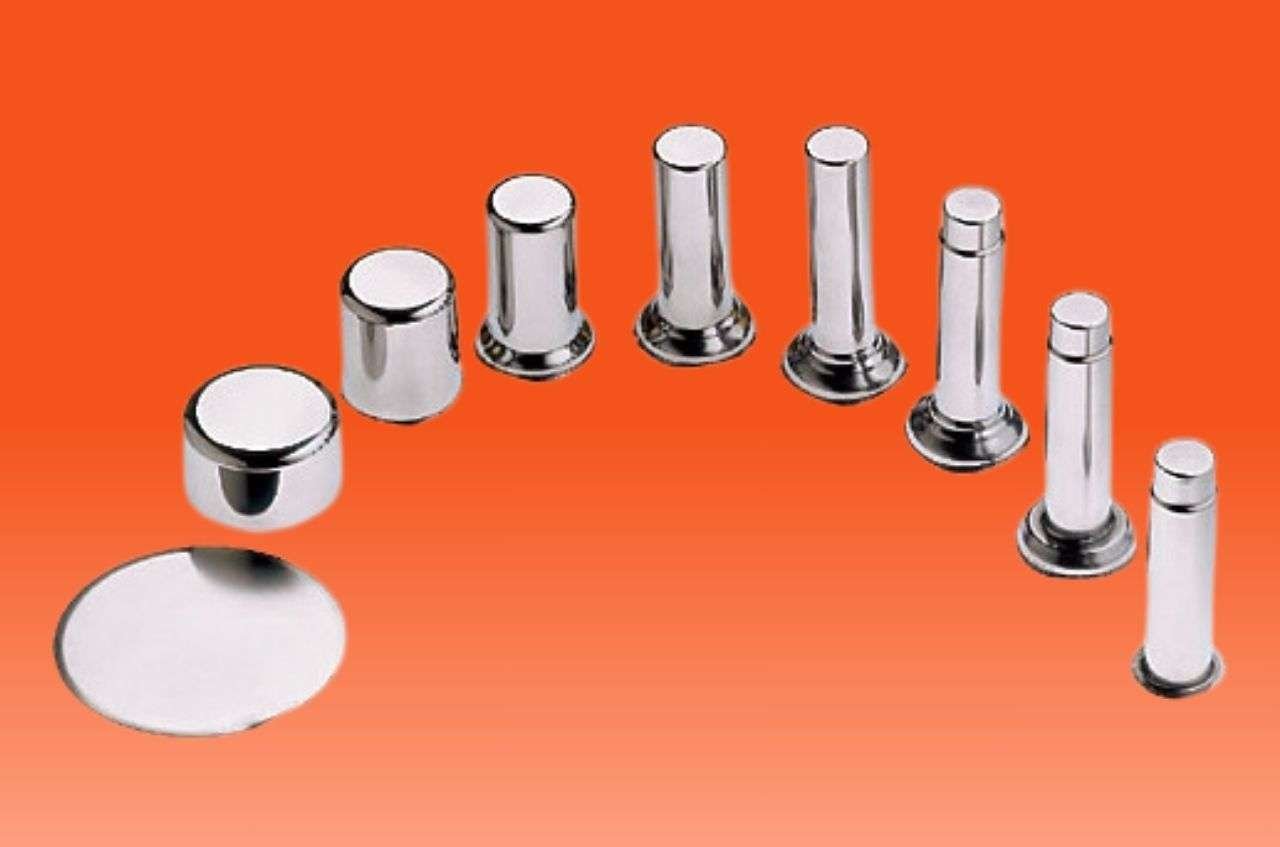
Benefits of Deep Drawn Stampings
High Production Speed
Deep drawing enables you to create many of a kind products at a fast pace. This also helps you to save time and enhances efficiency of your manufacturing lines. The speed of production enables one to meet any high demand while at the same time producing quality products.Seamless Assembly
The deep drawing process does not require welding or cutting. This leads to smooth products that one does not have to go through the process of assembly again. Therefore, you save yourself the costs of extra work and possible weak links in your products.Gas-Tight and Waterproof Products
Deep draw metal stamping helps to make end products watertight and airtight. This makes it ideal for applications where these properties are important, for instance, automotive and aerospace industries. It is therefore possible to depend on the product’s quality when exposed to different conditions in the environment.High Tolerances
Deep drawing process results in dimensional accuracy of the deep drawn parts. Tight tolerances also help in maintaining overall quality and consistency of your product. It is particularly important for components that need to interconnect seamlessly in assemblies, thus minimizing the instances that may require further refitting or fine-tuning.Complex Shapes
One of the advantages of deep drawing is that the structures can be created complicated. This means that you can be able to design in many ways which is very essential in creating new designs for the products. It also implies that you can acquire specific design requirements without having to negotiate on structural performance.Durability
Products formed through deep drawing are extremely strong and can withstand high levels of pressure. They do not deteriorate quickly due to tear and wear hence can last longer. This results in many advantages such as the fact that you will not need to replace any parts for quite some time.Drawbacks of Sheet Metal Drawing Stamping
Stress Issues
Higher radial and compression stresses can lead to crack, fracture and wrinkle formation in the material. These stress issues can influence the quality of products and thus proper material selection and control of process must be taken.Cost
Deep drawing is not economical when used in small scale production. Higher expense and skills needed make it less feasible for low-volume applications. For your individual needs, you have to decide whether the advantages significantly outweigh the disadvantages.Material Restrictions
Deep drawing is not possible with all materials. This limitation limits your choices of material you can use while designing your products. This may require some tradeoffs in terms of material properties or search for other manufacturing techniques.Tooling Costs
It is also important to take into consideration the initial tooling costs that are associated with deep drawing. This can be a limitation for some projects especially if they have limited funds to work with. These are costs that you must consider while organizing your production so that it is compatible with your capacities.Design Constraints
Complex shapes may need several stages to draw. This leads to an increase in the production time and the costs because each of the steps contributes to the process. These are constraints that you should take into consideration while designing the products to ensure that the products that are designed are not very complex to manufacture.Deep Drawing Manufacturing Process – Stepwise
Wondering how to draw a metal? It is important to understand the deep draw process to get most out of it. For deep drawn metal parts stamping the process is as follows: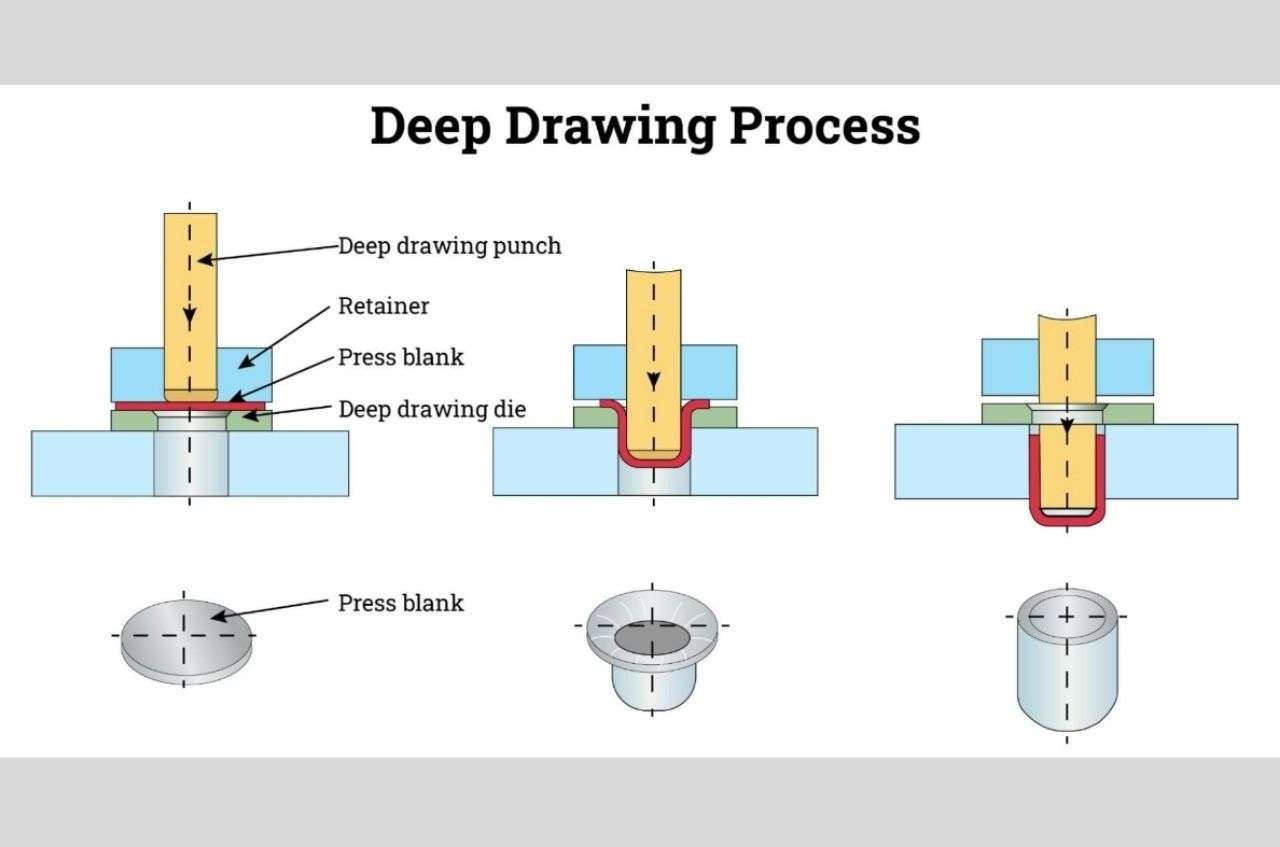
Step One: Anchoring the Metal Sheet
The process starts by positioning a metal sheet on the die or blank holder. To achieve uniformity in placement to minimize production mistakes. In order to get the right results, proper alignment is extremely important.Step Two: Punching
The punch with a certain amount of force is applied on the metal sheet. This action forms a cavity, cup, or irregular shape. The force applied has to be measured to ensure that the drawn material is not damaged.Step Three: Getting the Product
Continue punching until you get the desired end product. Take it out from the die and check for its quality. It also ensures that the product goes through the right processing in order to make it ready for use.Listing Differences Between Deep Drawing and Stamping
Comparing deep drawing with the standard stamping enables you to determine the most suitable process for your deep draw metal forming project.Deep Drawing
- Process: It is the process through which you change the shape of metal by passing it through a die. It involves the process of pulling the metal as an opposing force as that of hammering.
- Accuracy: Deep drawing has high accuracy. They allow you to get great dimensions with very small deviations.
- Surface Finish: This process gives a good finish and does not require additional operations which are time-consuming. The surface of the metal does not get scratched or tarnished in any way.
- Production Cost: It is more expensive since it involves the use of hi-technology and skilled manpower. It requires experienced operators and precise equipment.
- Thinning: Even more thinning is observed during deep drawing. This can alter the properties of the material, such as it becoming thinner and possibly less strong in certain areas.
- Bend Tightness: Tight bends are not possible with deep drawing. This limitation applies to the design where specific shapes and curves might not be possible.
- Strength: Deep drawing operation results in higher strength products. These are ideal for demanding applications where durability is crucial.
Stamping
- Process: In sheet metal stamping process pressure is applied to the metal sheet through force to make it assume the required form. This is done through hammering, beating or forging the metal.
- Accuracy: Stamping is a less precise process than deep drawing. There are likely to be fluctuations in the size of the final product more often.
- Surface Finish: Stamping also needs some post-processing steps to smoothen the surface. There is always a requirement for deburring or polishing of the metal.
- Production Cost: The cost is lower because the equipment and the processes involved are less complex. You can use simple equipment and low wage earners.
- Thinning: The metal stamping parts process entails lesser thinning hence retains the original properties of the material. The metal has better levels of thickness reduction loss.
- Bend Tightness: Stamping can be used to make very sharp bends. This results in more flexibility in terms of the shapes that can be formed, as the shapes can be more complex.
- Strength: Stamping is not as effective in creating strong products. These are suitable for low duty applications where high and constant wear and tear is not expected.
Basic Guidelines to Follow While Designing Sheet Metal Deep Drawing Products
The following are the sheet metal deep drawing products:Material Thickness:
Make sure the material is thick enough to accommodate the drawing process. Thicker material are less prone to tearing and wrinkling. Ensure you have checked the material requirements before commencing the project. Thin sheet may not be capable of withstanding the stress in drawing. Check the thickness using a gauge and select a material according to your design requirements.R and N Values:
Determine the R (ratio of the blank diameter to the die diameter) and N (reduction ratio) for your project. These values determine how effectively the metal can deform. Choosing the right R and N values will prevent such problems as tearing or excessive thinning. It is recommended to perform calculations or use the software to obtain these values before beginning the process.Blanks’ Shape and Size:
Steer clear of employing large or complicated shaped blanks. Big empty spaces can cause issues with grasping and positioning. This is because complex shape may result in uneven flow of metal and other imperfections. However, you must use blanks that are as close to the final shape and size as possible. This approach also helps to minimize difficulties that may occur during the drawing process and improve the quality of the final product.Lubrication:
Use the right lubricants to minimize the friction between the metal and the die. Proper lubrication also assist in easy metal flow and also will reduce sticking. Select lubricants which are in harmony with your material and process. This step enhances surface finish and minimizes the amount of wear and tear on your tools. Make sure to monitor the condition of the lubricant and reapply it whenever it is due.Press Speed:
Ensure that the press speed does not exceed certain limits. High speed can lead to non-uniform flow of metal and defects. A slow speed may cause some inefficiencies to arise as well. Pay attention to the press speed and depend on the material and the drawings required. Even speed is important since it will help in maintaining a high quality on the end product.Spacing:
Ensure there is a proper gap between the post and the blank. Lack of spacing may result to thinning of the material or conversely make it too thick. Take a measurement to ensure the distance between the various elements is correct according to the design. This way of placement allows for uniform deformation and minimizes the probability of defects occurring. Check spacing settings from time to time during the process.Resistance Management:
Minimize resistance during blank forcing to prevent failures. Too high friction can result in issues such as tearing or uneven drawing. Techniques to control and contain resistance: Supervise the process and control the parameters in order to achieve similar outcomes. A good resistance management plan leads to a smoother and less interruption-prone drawing process.Best-in-Class Metals for Deep Drawn Stamping
Different metals can be used in deep drawn stamping with each metal possessing its own characteristics. undefined- Brass: Demands low maintenance and provides high protection against corrosion and good electrical conductivity.
- Titanium: Its specific features include high strength and low density, which makes it suitable for aircraft and medical industries.
- Stainless Steel: Stamped steel parts offers durability and protection against corrosion, used in different sectors.
- Precious Metals: Employed in specific applications that call for elevated conductivity and resistance to corrosion.
- Cold Rolled Steel: Has high tensile strength and smooth surface finish and is suitable for car and industries product.
- Aluminum: Low in density and highly resistant to corrosion, ideal for uses in deep drawn aluminum transport and consumer products.
- Copper-Based Alloys: Famed for their electrical & thermal conduction aptitudes ideal for electronic products.
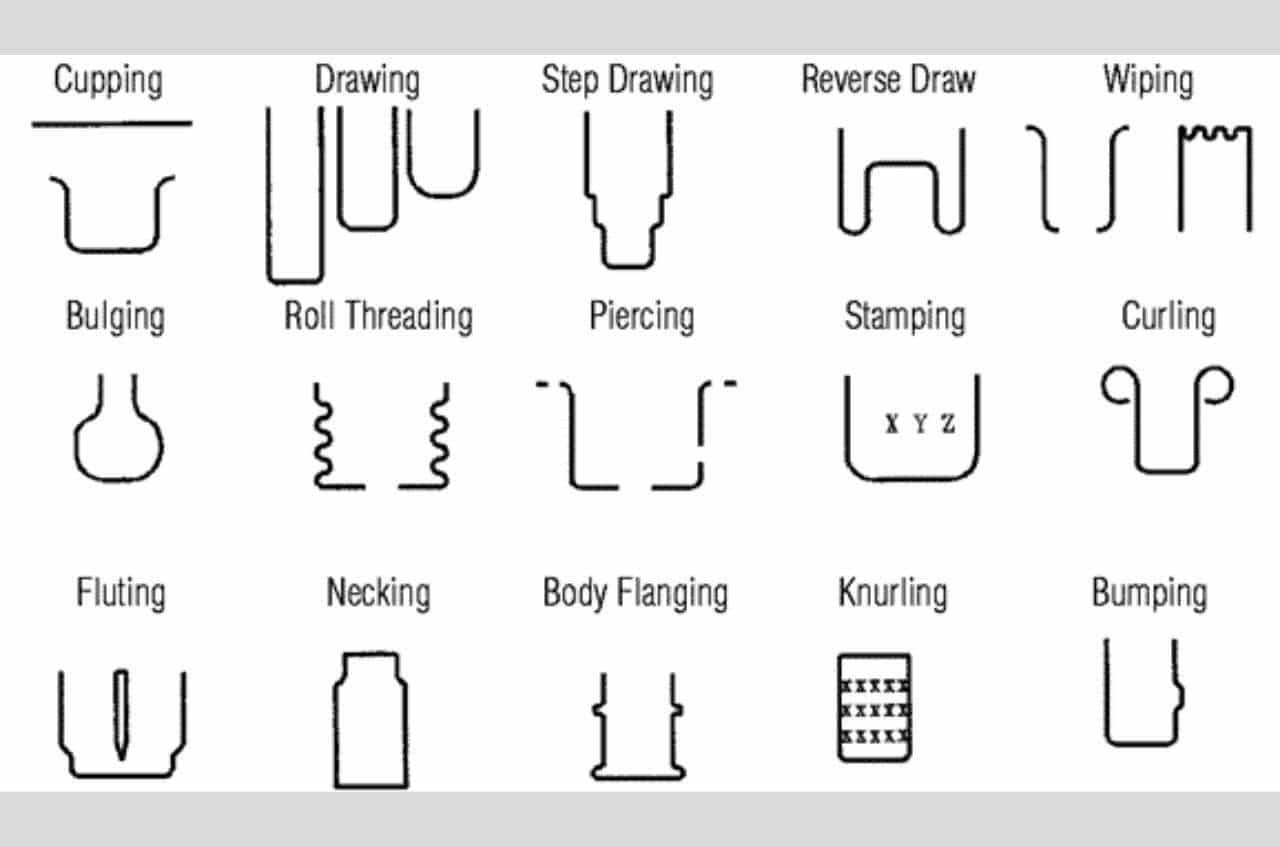
- Cupping: Suits creation of vainer and cylindrical forms.
- Drawing: Suitable for creating thin or intricate designs.
- Step Drawing: More specifically, it entails several drawing phases that culminate in the target form.
- Reverse Draw: Used for making shapes with opposite curvature.
- Wiping: Its forms edges and flanges on the metal sheet.
- Bulging: Enlarges some portions of the metal sheet.
- Roll Threading: Forms grooves on the metal surface.
- Piercing: Creates a pattern or outline on the metal sheet.
- Stamping: Bending and forming of the metal sheet to any desired shape.
- Curling: Creates curled edges for added strength.
- Fluting: Forms ornamental or utilitarian channels.
- Necking: Has the effect of decreasing the diameter of a cylindrical portion of the workpiece.
- Body Flanging: Molds flanges on the body of the part.
- Knurling: Introduces roughness to the gripping area.
- Bumping: Used to produce complex curves and shapes.
Common Deep Drawn Metal Parts
A number of stamped metal parts used in a variety of industries can be created through deep drawing.- Automotive Body Parts: Crucial for car production, as it contributes to body and trim.
- Bathtubs: Strong and withstands abrasion, ideal for home utensils.
- Sinks: Sturdy and resistant to corrosion, ideal to be used in the kitchen and bathroom.
- Yogurt Cups: Used in the food industry Light in weight and is safe to use for food products.
- Cooking Pots: Strong and heat resistant which can be used for making cooking utensils.
- Plastic Buckets: They are long-lasting and can be utilized for both domestic and commercial uses.
- Faucets: It is resistant to corrosion and possesses high durability, which is useful in plumbing.
- Soda and Beer Cans: Non-pulp and recyclable material used commonly in the production of beverages.
- Fuel Tanks: Strong and resistant to corrosion; used in car manufacture and other heavy industries.
Industry Applications of Deep Drawing Sheet Metal
Deep drawing is applied in many fields since it is flexible and profitable. undefined- Automotive Industry: Manufactures body panels, fuel tanks and other related parts.
- Communication Industry: Manufactures casings and shells for electronic equipment.
- Construction Industry: Creates long-lasting and rust-free components for constructing various structures.
- Military Industry: Specializes in manufacturing strong and dependable parts for the defense industry.
- Medical Industry: Manufactures surgical tools and medical device enclosures.
- Aerospace Industry: Creates lightweight and super-strong components for aircrafts and spaceships.
- Electronics Industry: Manufactures boxes and parts for electronics.
Conclusion
It has become imperative to understand the importance of deep drawing metal stamping in various industries because of the efficiency it offers in creating complex and high-precision drawn metals. Knowing the process, benefits, limitations, and design tips of this technique allows you to apply this tool to improve your production. Among deep draw stamping companies sheet metal Masion stands out from the rest. This is mainly because of qualitative components, comprehensive toolings, strict inspection process and compliance with global standards. If you want to enquire anything relating deep drawn metal stamping feel free to reach out. More Useful Resources: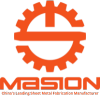