Utilizing Dacromet Coating, for Safeguarding Industrial Assets
Table of Contents
ToggleOverview;
The detrimental effects of corrosion and environmental elements on metals have led to a decline in their performance rendering them unsuitable for applications. Hence it is imperative to shield these metals to uphold their long term functionality. Different coating techniques are employed to create a film on metal surfaces enhancing their resilience against environmental factors. Nevertheless the introduction of dacromet coating has revolutionized the industry by providing resistance to corrosion, rust and hazardous substances.
If you’re interested in delving into the realm of dacromet coating you’ve come to the place. This guide will delve into details about dacromet coating shedding light on its composition, attributes, application process, variations, benefits and practical uses.
What is Dacromet coating, exactly?
Dacromet coating is a protective layer designed specifically for a broad spectrum of metal surfaces aimed at shielding them from corrosion rusting chemical exposure and more. This innovative technology was originally pioneered by Dacromet Corporation renowned for its properties in combating corrosion wear and tear as well, as chemical challenges.
This protective layer includes zinc powder, aluminum powder, chromic salts, deionized water, dispersion agents and other substances. Known for its versatility it finds applications, across sectors such as automotive, aerospace and more.
Dacromet Coating Composition;
When discussing composition the dacromet coating comprises aluminum powder, zinc powder chromic salts, deionized water, dispersion agents, pH adjusting agents and film coalescence aid. Each component possesses characteristics and collaborates to enhance the effectiveness of dacromet coatings.
Zinc powder aluminum powder and chromic salts notably enhance the corrosion resistance of surfaces. They provide protection against wear. Offer cathodic protection to metals. Moreover deionized water serves as a solvent by dissolving the coating components. PH adjusting agents assist in maintaining the required pH level for a coating process. Meanwhile
dispersing agents play a role, in distributing and mixing all components efficiently for coating application.
In addition, to the components mentioned earlier dacromet coating also includes additives like anti foaming agents, UV stabilizers and wetting agents. The specific compositions of these additives vary depending on the application they are designed for. The combination of these elements plays a role in ensuring that the coated metal surfaces are versatile, durable and perform efficiently.
Properties of Dacromet Coating;
Let’s delve into the characteristics of dacromet coating.
Outstanding Corrosion Resistance;
Dacromet Coating corrosion resistance is one of the standout feature. The inclusion of zinc powder and aluminum powder in the coating contributes significantly to its corrosion properties. By forming a layer on metal surfaces it shields them from environmental elements thus preventing rusting and extending their lifespan.
Superior Adhesion;
Dacromet coating is renowned for its adhesion properties. This refers to its ability to bond effectively with surfaces and maintain this bond over time without wearing off. This not ensures longevity. Also provides long lasting protection, to the coated metal surfaces.
Furthermore it eliminates the need, for metal coating.
Excellent chemical resistance stability;
Dacromet coating is widely known for its resistance to chemicals due to its high chemical stability. As a result chemicals cannot harm the metal surfaces coated with this type of coating. This characteristic makes it ideal for environments where continuous exposure to chemicals is expected, ensuring performance and durability.
Strong weather resistance;
In addition to corrosion and chemical resistance dacromet coating offers protection against environmental conditions. Regardless of the weather conditions this coating will safeguard the surface. Maintain optimal performance. Its resilience to weather patterns makes it a preferred option for components exposed continuously to varying climates.
Effective friction resistance;
Dacromet coating demonstrates friction properties by forming a smooth thin layer on the metal surface being treated reducing friction levels. Its ability to minimize friction makes it suitable, for applications where low friction’s essential.
Eco friendly nature;
Dacromet coating is highly valued for its properties as all components of the coating are non toxic and harmless.
The Dacromet coating has no effects, on people or the environment making it environmentally friendly and non polluting.
The Application Process of the Dacromet Coating
The process involves steps to ensure an high quality finish. Let’s delve into each step of the dacromet coating process for an understanding;
Metal Surface Preparation;
To start the Dacromet coating process the metal surface is meticulously cleaned to eliminate any debris, contaminants or impurities. This thorough cleaning is crucial for enhancing adhesion and facilitating a coating.
Pre Treatment;
Following the cleaning stage the prepared metal surface undergoes pre treatment processes such as pickling and chemical cleaning. Pickling involves using solutions, like nitric acid, sulfuric acid or hydrochloric acid to remove impurities, oxide layers and other materials from the metal surface.
This solution effectively removes all sorts of dirt from the metal surface. It assists in readying the metal by eliminating rust, corrosion and layers of oxide.
Chemical cleaning:
Another technique utilized for preparing the metal is chemical cleansing, also known as degreasing. During this process residues or impurities are eradicated using cleaning agents or solvents. The cleaning agent is spread on the metal surface. Left for a duration. This action eliminates all filth, grease, grime, oil and other impurities from the metals surface resulting in a spotless finish. These preparatory steps are crucial since neglecting them can lead to adhesion causing resistance, to corrosion rusting and chemicals.
Coating Application;
Following the cleansing and preparatory steps comes the application of coating onto the designated metal surface. Various techniques are employed for applying dacromet coating. Common methods include spin coating, spraying and dipping which cater to conditions and desired outcomes. These procedures facilitate the creation of a layer on the metal surface, with robust adhesion.
After the application of the coating the coated metal provides protection, against corrosion, rust, chemical degradation and friction. These processes are environmentally friendly as they do not generate any waste gases or water.
Curing and Baking
The next step involves baking and curing the metal surfaces. Baking is essential for eliminating moisture and solvents by heating the metal at a temperature in controlled conditions. The heat causes the evaporation of moisture and solvents enhancing the properties of the Dacromet coating.
Following baking the coated metal undergoes curing at a temperature to baking in a controlled atmosphere. Once curing is complete the coated parts are allowed to cool. The final product exhibits resistance to corrosion good temperature tolerance, improved wear resistance, chemical durability and strong adhesion.
Types of Dacromet Coating:
Dacromet coating comes in types categorized based on their properties. Lets explore one of its types;
BASECOAT
BASECoat, an element of the Dacromet coating system acts as the safeguard and a base layer, for subsequent coatings. It offers benefits by forming an initial shield against corrosion and creating a foundation that enhances the adhesion and effectiveness of later coatings. By prepping the substrate surface it ensures bonding and improved performance of the coating system. Its role in maintaining an consistent coating across the surface helps preserve the layers integrity. When combined with topcoats BASECoat is designed to complement Dacromet layers enhancing protective properties. BASECOAT consists of zinc aluminum flakes along, with silver colored binders.
It’s particularly effective, for smoothing out the imperfections found on metal surfaces. Moreover it creates a surface for applying a coat and improves adhesion as well as resistance to corrosion.
Dacromet 500 Coating;
This coating is made of hexavalent chrome based zinc aluminum. Its known for its performance and self lubricating properties. Dacromet-coated fasteners, clamps, springs, nuts, and hoses are widely used in construction and automotive industries due to their low friction coefficient, strong wear resistance, excellent corrosion protection, and ability to withstand high temperatures.
Dacromet 500 a type of Dacromet coating known for its exceptional performance features excels in providing superior corrosion protection particularly in challenging environments exposed to chemicals, seawater or harsh weather conditions. This variant ensures lasting protection against rust and degradation for components thereby extending their lifespan significantly. Suitable for applications involving heat exposure, like automotive machinery it retains its attributes even at high temperatures. Compared to coatings Dacromet 500 stands out as a friendly option as it does not contain chromium VI. The thin coating maintains the dimensions and mechanical characteristics of the components to achieve performance, without alterations.
To enhance the effectiveness of the base Dacromet coating further additional topcoats can be added. These topcoats can improve corrosion resistance increase lubrication properties enhance appeal and provide chemical resistance. Popular topcoat options include finishes like epoxy or polyurethane and inorganic finishes like silicate based coatings. The choice of topcoat depends on
Geomet 321;
This zinc aluminum flake coating is highly versatile and based on silicates. It does not contain any chromium. Finds applications in industries such as oil & gas construction, marine operations, automotive sector, aerospace due, to its enhanced durability, adhesion strength, low friction coefficient as well as superior wear and corrosion resistance.
Geomet 321 coating, which is based on zinc flakes is highly respected, for its ability to resist corrosion and its friendly nature. Its robust protective layer can withstand conditions making it a top choice for automotive uses that require durability. This coating offers heat resistance making it ideal for parts exposed to temperatures and it complies with environmental regulations by being chromium VI free.
Geomet 320/360;
This is an advanced silicate based zinc aluminum flake metallic surface coating with a high aluminum content and no chromium. It is particularly useful, for brake discs due to its resistance to temperatures and heat. Similar to Geomet 320/360 coatings, zinc flake coatings are designed to enhance resistance against corrosion and wear. They perform well in salt spray tests making them suitable for environments, like maritime settings. These coatings are also environmentally friendly. Do not contain chromium VI aligning with the qualities of Geomet 321.
Dacromet 310/320;
A hexavalent chrome based zinc aluminum coating used in clamps, springs, fasteners and hoses to enhance properties like corrosion resistance, temperature resistance, chemical resistance and durability.
Geomet 720;
A silicate based zinc aluminum flake coating without chromium that finds applications in construction, automotive industry, springs, hoses, etc. thanks, to its properties.
The availability of these types allows for tailoring Dacromet coatings to suit the requirements of various industries and applications. By selecting the type users can achieve performance while adhering to environmental regulations.
Benefits of Dacromet Coating;
Dacromet coating provides advantages in industries worldwide. Let’s explore its benefits.
- One notable advantage of Dacromet coating is its enhancement of the corrosion resistance of the metal surface it covers. With a thickness ranging from 4 8 micrometers this coating is remarkably more effective, than coatings offering 7 10 times protection against corrosion. It shields the metal surface from corrosion ensuring longevity and durability.
- Moreover it enhances the heat resistance of parts improving their ability to withstand temperatures without melting or deforming. Dacromet coating demonstrates permeability easily penetrating into crevices and deep holes on the metal surface to provide a uniform coat.
- Unlike some coatings that may lead to hydrogen embrittlement, Dacromet coating does not pose this risk making it a reliable choice for components under stress. The combination of zinc and aluminum flakes in Dacromet forms an barrier against corrosion. This results in lasting protection for metal components in challenging environments, like marine or industrial settings.
- Dacromet coatings have the ability to endure temperatures of, up to 300°C without deteriorating which makes them ideal for use in situations where heat exposure’s common such as in automotive engine parts and exhaust systems.
- The shift towards chromium and chromium free formulas is a response to concerns about the health impacts linked to hexavalent chromium. Furthermore Dacromets water based composition positions it as a alternative when compared to coatings that rely on solvents.
- Although the initial cost of applying Dacromet may be higher than some competing coatings, the extended lifespan and durability of Dacromet coated parts can result in cost savings over time by reducing the need for replacements or upkeep.
- Dacromet can be applied onto a variety of materials including steel, cast iron and different alloys making it a versatile solution suitable for materials and applications.
- It boasts adhesion properties by bonding with metallic surfaces due to its exceptional binding force with the metal matrix.
- The entire process of dacromet coating does not generate any waste or chemicals. Therefore it is a process that does not produce pollutants.
These combined benefits position Dacromet as a choice for industries seeking long lasting protection, against corrosion. The value of its performance, environmental friendliness and cost effectiveness makes it a versatile choice, for uses.
Limitations of Dacromet Coating;
Despite its benefits there are some drawbacks to the dacromet coating process that are outlined below.
- Some types of dacromet coatings contain hexavalent chromium, which can pose risks to the environment and human health if not handled properly. These coatings do not offer conductivity making them less suitable for components requiring electrical connections.
- Dacromet coatings may not offer the level of wear resistance as coatings like hard chrome plating. The energy consumption during the dacromet coating process is high due to processing times and high sintering temperatures.
- The thickness of the coating is typically limited to 4 8 microns, which may not be adequate, for applications needing coatings. Improper cleaning or pre treatment of the metal surface can lead to dacromet coating results.
- Traditional Dacromet formulations containing hexavalent chromium environmental and health hazards. While the industry is leaning towards options these alternatives may not yet fully measure up to the formulations.
- The process of applying Dacromet involves steps such, as preparing the surface applying the coating letting it dry and allowing it to cure. Each step demands handling and specialized tools which can make the process more complex and costly.
- 6.Initially the cost of using Dacromet coating may be higher compared to methods. This cost includes expenses for surface preparation, application tools and curing procedures.
- 7.One drawback of Dacromet coating is its color range as it typically comes in gray tones that may not suit all aesthetic preferences. Additional topcoats can be applied for colors. This adds complexity and cost.
- The effectiveness of Dacromet coatings in terms of adhesion and performance heavily relies on surface preparation. Inadequate preparation can result in adhesion leading to reduced corrosion protection.
- There are alternative coating systems that might provide performance in specific scenarios. The choice of coating depends on factors, like application requirements, environmental aspects and budget limitations.
To make informed decisions, about using Dacromet coating understanding its limitations is essential. By considering the pros and cons individuals can assess whether Dacromet is the choice for their requirements.
Is Dacromet Superior to Galvanized Coating?
Both Dacromet and galvanized coatings are ways to safeguard metal surfaces from corrosion but they differ significantly in performance and characteristics.
Dacromet coating typically offers corrosion protection compared to coating. It can endure up to 1000 hours of salt spray testing without developing rust, which’s significantly better than traditional galvanizing methods by 7 10 times. Additionally Dacromet exhibits heat resistance withstanding temperatures of up to 300°C.
One key benefit of Dacromet is its resistance to hydrogen embrittlement making it suitable for strength and elastic components. Furthermore Dacromet coatings adhere well to the substrate. Can be easily reapplied if needed.
On the hand galvanized coatings have their advantages. They are suitable for both outdoor settings in humid conditions providing durable protection, for metal materials. Galvanized coatings are often more cost effective when compared to Dacromet.
When it comes to looks Dacromet has a finish resembling paint while galvanized coating often gives off an appearance, like frost on a window. Dacromet typically comes in color options with silver gray being the choice.
When deciding between Dacromet and galvanized coating factors like the environment of use, cost, expected lifespan and appearance preferences should be taken into account. Dacromet is commonly preferred for applications needing top notch corrosion resistance, performance under temperatures and good adhesion. Like in parts and aerospace components. On the hand galvanized coating might be more suitable for projects prioritizing cost efficiency and durability. Such as building structures or pipelines.
In summary while Dacromet offers corrosion resistance and high temperature performance compared to coating the selection between the two depends on specific application requirements and balancing performance cost considerations and appearance.
Uses of Dacromet Coating
Dacromet coating finds use across industries where protection against corrosion is crucial;
Automotive Sector;
In the sector Dacromet is widely employed for components like fasteners, brake discs and parts, under the hood.
Dacromets excellent resistance, to corrosion and heat makes it a great choice for components that face conditions and high temperatures.
Building Sector;
Dacromet shields steel, Dacromet-coated bolts, and other construction parts from corrosion, ensuring their durability and strength when used outdoors.
Aviation Sector;
In aviation Dacromet is applied to fasteners landing gear elements and crucial parts that demand reliability and resistance to corrosion.
Maritime Sector;
Components like Dacromet-coated screws, bolts, and fittings in the marine industry are coated to combat the damaging effects of saltwater environments
Agriculture and Heavy Machinery;
Dacromet coatings safeguard machinery components like tractor parts and tools from rust in challenging settings.
Clean Energy Industry;
Wind turbine fasteners and similar elements exposed to weather conditions benefit from the enduring protection offered by Dacromet coatings.
Chemical Processing Plants;
The resistance of Dacromet shields components in chemical processing facilities from substances they encounter.
The various uses of Dacromet coating showcased here underscore its adaptability and efficiency in providing protection against corrosion, in sectors.
The durability of the coating, in conditions along with its advantageous qualities makes it a popular choice for important parts.
Summing Up
Dacromet coating signifies a progression in the realm of preventing corrosion. Its distinct composition, which includes zinc and aluminum particles within a binder delivers resistance to corrosion, heat and environmental factors. Despite the application process that guarantees effective coverage resulting in a strong and trustworthy protective coating.
The range of Dacromet coatings such as variations improved topcoats and chromium free options cater to diverse applications and performance needs. Despite drawbacks like hexavalent chromium in traditional forms and the complexity of application procedures the benefits of Dacromet coating make it an appealing choice across various industries.
From aerospace sectors to construction and marine fields Dacromet coating offers protection against corrosion that enhances the longevity and functionality of metal parts. With industry advancements towards eco friendly formulations Dacromet is positioned as a prime solution for corrosion protection well, into the future. By comprehending the nuances of Dacromet coating industries can make informed choices to capitalize on its advantages for safeguarding components and ensuring enduring dependability.faste
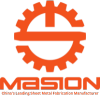
Send Your Inquiry Today



+86-18969433502

sales@sheetmetalmasion.com