Aluminum Sheet – Everything You Need To Know About
Aluminum sheet, an adaptable and comprehensively used material in various organizations, offers a lot of advantages inferable from its fascinating properties and qualities. From its uncommon solidarity-to-weight extent to its corrosion resistance and formability, sheet aluminum fills in as an establishment in flight, vehicle, improvement, and customer items divisions.
Understanding the nuances of sheet aluminum is basic for specialists, manufacturers, and makers, highlighting its abilities in various applications. In this thorough web article, we jump into all that you want to know about aluminum sheets, covering their properties, creation techniques, and applications to enable you with the data vital for structure-taught decisions and see the complete capability of this astonishing material.
Alt tag: sheet overview
What is Aluminum Sheet Metal?
Table of Contents
ToggleSheet aluminum metal implies a level piece of aluminum that has been moved into a lean & thin flat sheet. This kind of metal is known for its lightweight properties, astounding corrosion obstruction, and extraordinary solidarity-to-weight ratio. It is really adaptable and can be used in a variety of businesses over various particular purposes.
Process of Sheet Fabrication
The production of sheet aluminum metal could be an exhaustive process that incorporates various moves and tools toward converting crude sheets into final parts. Each step of the fabrication process is essential as it impacts the product’s overall appearance and can’t be ignored. Here is a layout of the typical techniques that are essential for aluminum sheet creation:
● Cutting
The essential move toward sheet creation is slicing the material to the ideal shape. You can use various procedures relying upon the precision and size of your project, counting:
● Forming
This step incorporates framing the cut sheet into its last shape without removing material. The following are a couple of normal molding methodologies:
- Bending: Makes definite overlays and focuses using press brakes.
- Drawing: Broadens the sheet metal into a needed shape utilizing a punch and die.
- Rolling: Shapes the sheet into twisted shapes using rollers.
- Stamping: It finishes off specific shapes from the sheet via die to punch.
● Riveting
Riveting is a typical system for joining sheet aluminum without dissolving the base material. It incorporates putting bolts (metal pins) through pre-penetrated holes and after that deforming the bolt to keep the sheets intact. Riveting is particularly well known in applications where welding may not be suitable, for example, inside the avionic business where warm curves should be limited.
● Welding
- Welding Welding could be an essential step for various aluminum make adventures, especially when a strong bond is indispensable. Aluminum welding can be trying because of its tall warm conductivity and oxide layer. These techniques are used:
● Surface finish
Erosion resistance, advancing the appearance or surface hardness of aluminum products, can be achieved through various finishing structures, for example,
- Anodizing: Enhance corrosion resistance and grant shade to the aluminum a particular tone.
- Powder Covering: Gives a strong, wear-safe layer in a wide variety.
- Sandblasting: Cleans the outer layer of the metal and gives it a uniform matte finish.
● Assembly
Assembly is a definitive move toward sheet metal. This step incorporates consolidating different parts to make a complete design or product. Assembly might be achieved through additional welding, riveting, or the use of clasp and adhesives. In a couple of cases, mechanical assembly strategies like screws, nuts, and shocks are used to supply vital structural integrity and perception.
Each step inside the sheet aluminum-making process should be executed with great precision to ensure a final product meets all requirements & specifications. This multi-step approach ensures making really modified and complex parts fitting for various mechanical applications.
Types of Sheet Aluminum Metal
Aluminum metal comes in various sorts, each with specific properties and applications. Here is a list of some popular sheet metals.
Alt tag: types of aluminum
1 .Pure Aluminum Sheeting
Additionally known as CP (commercially pure) aluminum, this sort contains at its smallest almost 100% aluminum and offers incredible usefulness, formability, and conductivity. It’s ideal for applications requiring incredible electrical conductivity, like warm sinks or busbars. In many cases, pure aluminum has lower quality than other alloy blends.
2. Perforated aluminum sheets
These sheets have stamped or holes punched in various shapes throughout the material. They offer advantages like ventilation, upheaval reduction, filtration, and decorating style. Applications of this include designing cladding, speaker grilles, and separately separated security regions.
3. Chequered sheets
Besides being known as a valuable stone plate or caltrop plate, this sort contains a raised diamond jewel molded design on one or two surfaces. It gives extraordinary slip obstruction, making it ideal for ground surfaces in mechanical zones, walkways, or truck beds.
4. Brushed aluminum sheets
These sheets have a brushed wrap-up made by precisely rubbing the surface with a wire brush. This gives a matte, uniform appearance that hides away minor scratches and fingerprints. Brushed aluminum is routinely used to improve applications in contraptions, devices, and furniture.
5. Composite sheet
This sort involves aluminum with different materials like plastic or a fire-retardant focus. The composite construction offers central focuses like extended quality, inflexible nature, sound insulation, and lighter weight contrasted areas of strength with sheets of a similar thickness. Applications integrate building facades, cladding sheets, and signage.
6. Anodised Aluminium Sheets
Anodising is an electro-substance process that makes a guarded oxide layer on the aluminum surface. This layer further develops corrosion-resistance, advances wear obstruction, and can in addition, be shaded for color enhancement. Anodized aluminum is extensively used in building materials, trim, and adorning applications.
7. Embossed Sheet
This type includes a raised or planned design pattern crushed or pressed onto the surface. Embossing incorporates an inflexible nature, hides away surface flaws, and makes an ostensibly captivating surface. Applications integrate improving sheets, machine parts, and signage.
8. Mirror aluminum plate
Besides being known as a cleaned sheet, this type includes a significantly smart surface equivalent to a mirror. It’s cultivated through a cleaning process that makes a smooth and shimmering wrap-up. Mirror aluminum is used for savvy surfaces, upgrading trim, and primary cladding.
9. PS sheet
This kind of sheet metal integrates a painted finish associated with the midst of the production process. It offers additional protection from corrosion, further develops style, and gives a different variety of decisions.
Alt tag: aluminum sheets production process
10. Pained/Coated sheet aluminum
As indicated over, this kind of sheet metal highlights a paint or other covering applied to the surface. The covering can be for feel, corrosion obstruction, or advanced wear properties.
11. Alloy sheet
Ordinarily, the chief normal kind of aluminum sheet metal. Aluminum blends join aluminum with different parts like copper, magnesium, or silicon to improve its quality, machinability, or different properties. There are various unmistakable blend tasks, each with specific qualities appropriate for various applications.
12. Aluminum-covered aluminum plate
This can be a composite material where a lean layer of high-virtue aluminum is invigorated to a thicker focus for an error-free aluminum combination. This blend offers the advantages of the two materials, like the incredible disintegration opposition of faultless aluminum on a superficial level and the quality or sensibility of the middle mix.
13. Honeycomb Aluminium plate
This kind of sheet metal includes a hexagonal honeycomb structure sandwiched between two lean sheets. The honeycomb community gives incredible quality and resoluteness keeping up a lightweight profile. Honeycomb sheet aluminum are used in applications like aircraft improvement, primary cladding, and lightweight portions.
What are the Common Types of Aluminum Grades?
1XXX Series:
Every grade is significant and has its own significance. Simply put, 1370 and 1200 demonstrate excellent performance and comprehension of the material. These grades frequently assist individuals with getting into great projects they need.
Going down the scale, 1100 and 1070A still areas of strength for show, however there might be some opportunity to get better. These grades show difficult work and exertion, which are great characteristics in any field.
The grades in the middle range, such as 1060 and 1050, demonstrate some skill but may require some improvement. Despite the fact that these grades may not immediately catch attention, they nonetheless demonstrate a high level of comprehension and achievement.
The lower grades of 1050A and 1035 may indicate that the student is having trouble fully comprehending the material. Nevertheless, these grades also indicate opportunities for improvement. They highlight areas where extra effort and assistance can make a significant difference.
2XXX Series
Known for their high quality and wearing resistance. Used in flying and aircraft applications where quality is fundamental. It has excellent erosion resistance properties for watery projects. Alloys like 2A12 and 2A14 are notable for their solid quality and are much of the time utilized in airplane structures and other high-stress circumstances.
The plan for 2A16 and 2A20 calls for making adjustments to increase the aluminum’s wear resistance and quality. Aluminum alloys like 2A12, 2A14, 2A16, and 2A20 are frequently utilized in aircraft and other high-stress settings due to their reputation for being extremely strong for their weight. Each of these grades has unique characteristics that make them suitable for parts that need to be strong, wear-resistant, and simple to weld.
Even though not many people talk about it, the 2816 review suggests focusing on particular alloying elements to change how strong materials are. The grades 2014 and 2024 are extremely durable and are frequently utilized in aircraft, military vehicles, and other significant items where durability is crucial.
Similar to a smaller version of the 2024 model, the 2124 model is many times picked on the grounds that it is more solid and has better highlights. A2219 is great for rockets, boats, and other places where it gets really hot because it stays strong in high temperatures and doesn’t get damaged by sudden heat.
The fact that aluminum can be used in a variety of construction applications is demonstrated by the fact that each of these grades contains the appropriate proportions of silicon, magnesium, copper, and both. The 2816 could allude to an exceptional metal or item that has extraordinary characteristics for specialized utilizes. Without additional information, it might not be very well known.
Moving into the 2000s, as in 2014, 2024, and 2124, these materials are known for being major areas of strength for extremely are utilized in planes and vehicles since they are lightweight however exceptionally amazing. Alloy A2219 is extremely strong and expands a lot. It is ideal for use in spacecraft because it can withstand high temperatures and wear and tear.
3XXX Series:
The aluminum types 3003, 3004, 3005, 3A21, 3105, and 3103 are all important for the 3000 series. They are stronger than pure aluminum because they are mixed with manganese, but they can still be easily shaped and resist corrosion. Review 3003 is good for making pots and pans, chemical equipment, and other items used for a variety of purposes because it is strong and easy to work with.
Moving on to 3004, a superior type of metal that is frequently used to make cans, buildings, and other materials due to its rust resistance and ease of shaping. The 3005 review is frequently used to produce high-end appliances, equipment, and siding because it raises the quality of the materials. They become stronger and more resistant to rust as a result. The 3A21 is like the 3003 by they way it’s utilized and what it’s like. When slightly improved mechanical properties are required, it is frequently utilized.
The grades 3105 and 3103 are well-known for their resistance to damage and erosion. Grade 3105 is involved a ton in home siding, trailers, and downpour drains. Both 3105 and 3103 are excellent for wrapping and molding since they are not difficult to work with and can be welded without any problem. These grades show, taken together, how the 3000 arrangement can be used to strengthen aluminum without compromising its qualities.
4XXX Series:
Because of their excellent flow properties and resistance to corrosion, the aluminum grades 4A01, 4A11, 4043, 4043A, 4047, and 4047A are frequently utilized in welding and brazing. The grades 4A01 and 4A11 are uncommon and typically used for specific industrial applications. They have unique characteristics like increased strength or heat conductivity.
Because they contain silicon, the 4043 and 4043A grades are popular for welding because they make the weld smoother and lower the risk of cracking. This makes them incredible for welding comparable or various kinds of aluminum. Furthermore, 4043 is favored in light of the fact that it is less delicate to weld breaking and has high intensity conductivity.
However, the surfaces of 4047 and 4047A are smoother and contain more silicon. They are frequently utilized for brazing in light of the fact that they dissolve at a lower temperature than other aluminum combinations and function admirably. Because of this quality, 4047 is very important for making machined parts have stronger joints and better finishes. These grades demonstrate how successfully aluminum blends can be utilized for challenging welding and manufacturing tasks.
5XXX Series:
The aluminum alloys 5056, 5053, 5251, 5005, 5019, 5182, and 5186 are diverse mixtures of aluminum with various properties that are suitable for specific applications in various industries. The aluminum alloys 5056 and 5053 are extremely robust and can withstand damage from water and air. 5251 is known for being easy to weld and shape, and it is commonly used in car panels and building parts due to its good properties.
5005 has similar properties to other materials, but it is better at resisting erosion. These materials are good for use in boats and planes when they need to be very strong. It is in many cases utilized in designing and embellishing applications, as well as in making domestic devices. 5182 and 5186 are preferred because they are excellent for welding and shaping objects, and this review is excellent for use in airplanes and automobiles where dependability under pressure is crucial.
They are involved a ton for making refreshment jars, vehicle parts, and bundling materials since they are solid and simple to work with. By and large, each kind of aluminum has novel characteristics that are custom fitted to explicit mechanical requirements. This demonstrates how adaptable and adaptable aluminum is to various applications.
6XXX Series:
The 6000 series is made up of the aluminum varieties 6A02, 6B02, 6061, 6063, 6063A, and 6070. They are famous for strength for exceptionally, to weld, and impervious to erosion. Along these lines, they are utilized in various enterprises, from development to cars. Beginning with 6A02 and 6B02, these grades are basically utilized in making things, and they are really great for molding complex shapes and profiles.
6061 is an entirely adaptable and generally utilized sort of metal. It is well-known for its strength, ease of use, and ease of welding. Since it is easy to shape and has a smooth surface, 6063 and its variant 6063A are ideal for building airplanes, boats, and buildings. They are normally utilized in development and design for things like window outlines, entryway casings, and furniture.
6070, on the other hand, isn’t as common as 6061, but it has similar characteristics. It is top notch and simple to work with. It very well to utilized in making vehicle parts and mechanical hardware. In general, the various properties and applications of aluminum alloys are demonstrated by the grades in the 6000 series. Because they are adaptable and effective, they can be used for a wide range of engineering applications.
Consolidates 6061 and 6063 aluminum mixes. Known for their astonishing extrudability and formability. They offer extraordinary corrosion obstruction and weldability. Extensively used in architectural, vehicles, and auxiliary applications.
7XXX Series:
The sorts of aluminum 7A04, 7A09, 7005, 7050, and 7075 are in the 7000 series. They are frequently utilized in important aviation, military, and other applications due to their lightweight strength. Beginning with 7A04 and 7A09, these grades are extremely durable and hard to break. They are perfect for fundamental plane parts and high-stress additional parts where being trustworthy is generally significant.
Review 7005 is well-known for its high quality and ease of welding. 7050 aluminum is superior to other types because it is stronger and more resistant to erosion. It is frequently utilized in the production of bicycle frames, automobile parts, and sporting equipment, rocket parts, and airplane parts. Notwithstanding, the 7075 combination is the most grounded and most broadly utilized sort of aluminum.
7075 is a great metal that is not difficult to work with and can endure a ton of power. It is many times utilized in planes, military stuff, and elite execution machines since it is truly dependable, particularly in extreme circumstances. Together, these grades show that the 7000 series is known for areas of strength for making that are utilized in a large number of ventures. This demonstrates how adaptable and flexible aluminum can be in various designs.
Integrates 7075 aluminum blends. Known for their high solidarity-to-weight extent. Offers astounding quality and strength, particularly in aeronautics applications. They are not erosion-resistant but suitable for various applications.
8XXX Series:
The aluminum alloy 8090 is renowned for its lightness and strength. It stands out due to unique mechanical properties. This is many times utilized in avionics and vehicle ventures, where lightweight materials with excellent are significant for making fuel go further and further developing execution. 8090 is comprised of zinc, copper, and magnesium.
It can oppose disintegration and is not difficult to work with. It is useful for a lot of things, like car panels, sports equipment, and parts for airplanes. Its significance in advanced engineering applications is highlighted by its capacity to withstand extreme conditions while maintaining basic intelligence. In simple terms, it is very important in fancy engineering because it can work well in difficult circumstances. In general, the highest point of aluminum alloy innovation is 8090, which pushes the limits of quality, strength, and flexibility.
AL1050:
AL1050 is a sort of aluminum that is practically unadulterated and pure, with 99. 5% aluminum. It is one of the most over-the-top, purest aluminum compounds you can get. It’s exceptionally impervious to rust, conducts intensity and power well, and can bend & twist without breaking. These characteristics make it great for applications like chemical hardware, food industry use, and reflective signs. Further, It is twisted and molded easily, making it ideal for ornamental and architectural design.
AL1060:
AL1060 has more aluminum than AL1050, around 99. 6%. It has many similar characteristics, such as being great at not rusting and moving intensity, but rather, it’s somewhat better at leading power. AL1060 is excellent for things that need lead power, similar to busbars and transformer windings. It is exceptionally valuable for electrical applications. It is additionally utilized in food and compound enterprises where it is vital to be extremely spotless.
AL5052:
AL5052 is a blend of aluminum and magnesium and is generally used in assembling. It is solid, opposes getting worn out effectively, can endure consumption, and is not difficult to weld. It has high strength for extremely pungent water, so it’s frequently utilized for boats and different things in the sea. Likewise, it tends to be effectively molded and utilized in making gas tanks for airplanes, streetlamps, and electronic nooks. The blend of metals is likewise frequently utilized for making slight sheets and for things that need strength against the harsh climate.
AL5083:
AL5083 is great for involving the sea since it doesn’t get harmed effectively via seawater. An extraordinary choice of things is utilized in the water, similar to boats or moors. It has aluminum, magnesium, and a tad of manganese and chromium, which assists it with opposing harm from rust, particularly in plants and by the ocean. This kind of metal is high-strength and exceptionally durable, even after being welded. It is normally used to assemble ships, rail vehicles, vehicle bodies, and strain vessels. The metal’s capacity to lead heat well and be solid additionally makes it really great for fireproof compartments and boards. “
A1100:
A1100 is a sort of metal made generally of aluminum, which is great at opposing rust and is a decent transmitter of intensity and power. It is exceptionally valuable and typically comes in level sheets. It is great for making shapes since it solidifies more leisurely than different metals. Individuals frequently use aluminum for building outsides, cooling gadgets, and cooking devices. This metal combination can be painted or anodized to make it appear more appealing and safeguard its surface.
Aluminum Alloys | Key Features | Applications |
Aluminum 6061 | ● Weldability ● Excellent strength ● Corrosion-resistant ● High machinability | ● Fuselages ● Wings ● Control surfaces ● Aircraft structures ● Engine components |
● Aluminum 7075 | ● Good fatigue resistance ● Wear resistance. ● Exceptionally high strength | ● wing spars ● high-stress components ● Landing gear |
● Aluminum 6063 | ● Good strength ● Weldability ● Excellent strength | ● Extrusions ● Tubes ● Aircraft skins ● Structural components |
● Aluminum 2024 | ● Good fatigue resistance ● Exceptionally high strength ● Weldability ● Good forgings | ● Control surfaces ● Fuselages, ● Aircraft structures ● Wings ● Stringers ● Bulkheads |
● Aluminum 7050 | ● Fracture toughness ● High strength | ● Wing spars ● Ribs ● Critical components ● Landing gear |
● Aluminum 2017 | ● Weldability ● Good fatigue resistance | ● Critical assemblies ● Joining aircraft structures |
● AL1050 | ● Corrosion-resistant ● High machinability | ● chemical hardware, ● food industry use, ● and reflective signs |
● AL1060 | ● Weldability ● Good forgings | ● busbars ● and transformer windings |
● AL 5052 | ● Good fatigue resistance ● Exceptionally high strength ● Weldability | ● gas tanks for airplanes, ● streetlamps, ● and electronic nooks |
● AL 5083 | ● Good fatigue resistance ● Wear resistance. | ● ships, ● rail vehicles, ● vehicle bodies, ● and strain vessels |
● AL1100 | ● Weldability ● Excellent strength ● Corrosion-resistant | ● building outsides, ● cooling gadgets, ● and cooking devices |
Alt tag: aluminum sheet different grades
Understanding the sheet aluminum Metal Gauge
The gage system, also known as the American Wire Gage (AWG) structure, is generally used to grade the thickness of sheet metal, counting aluminum. In this system, the higher the gauge number, the more slim the sheet. On the other hand, the lower the gage number, the thicker the sheet.
Aluminum sheet metal is accessible in different standard measures, with normal thicknesses going from 0.025 inches (22 gauge) to 0.125 inches (8 gauge). Be that as it may, speciality compounds or custom orders might veer off from these standard thicknesses.
Aluminum Metal Properties
Define Aluminum sheet properties
Mechanical Properties
Aluminum’s weight solidarity makes it an ideal material for space, automotive, and aeronautical applications. The most significant advantage of CNC machining is the production of lightweight parts that enhance airplane performance and fuel efficiency and reduce material waste.
● Versatility and Design Freedom
Many aluminum alloys can be machined utilizing CNC. This opens up a wide range of design options and allows components to be customized to meet specific requirements like increasing strength, resisting heat, or protecting against corrosion.
Cutting Properties
- Shearing: Ideal for straight cuts and ordinarily used for mass sums.
- Laser Cutting: Gives precision cuts for complex shapes and fine points.
- Waterjet Cutting: Used when materials can’t endure other cutting systems’ warmth, publicizing no HAZ (heat-affected zone).
- Plasma Cutting: Fitting for thicker sheets, known for speed regardless of the reality less accurate than laser cutting.
Bending Properties
Aluminum’s impressive adaptability makes it a superb contender for bending & bowing:
- Cold Bending: Aluminum can be bowed and bent at room temperature without breaking, which is ideal for making exact shapes.
- Press Brake Bowing: Generally used for bending aluminum sheets, giving sharp and careful turns without requiring high pressure.
Weldable Properties
- TIG Welding: Ideal for additional thin sheets, giving superior grade, precise welds.
- MIG Welding: Sensible for thicker sheets, faster than TIG welding; however, it may not be as spotless.
Stamping Properties
The sensitivity and adaptability of aluminum make it spectacular for stamping, which incorporates molding plans by getting the metal into a die. Aluminum doesn’t break or tear as easily as harder metals, which makes it ideal for convoluted stamped plans.
Deep drawing properties
Aluminum is appropriate for significant drawing, a process where sheet metal is radially brought into a molding die by the mechanical action of a punch. Normally, it is used comprehensively in cooking wares, holders, and other empty parts. Aluminum’s ability to expand without crashing and burning might be a crucial benefit in this process.
Pros of Aluminum Metals
This ensures high accuracy, consistent performance, and adjustment to the strict security prerequisites vital for airworthiness.
Alt tag: aluminum cnc machining advantages
● Helps in Precision Aerospace Parts Manufacturing
Using computer-controlled tools, CNC machining achieves unparalleled accuracy and precise tolerances. This helps to ensure optimal performance and safety in challenging conditions by ensuring that crucial parts meet exact specifications.
● Produces High-Performance Aluminum Components
When ingesting aluminum, CNC machining ensures strength, resistance protection, and lightweight attributes. As a result, it produces long-lasting, robust parts that can bear unpleasant and harsh conditions.
● Consistency in Production
In contrast to manual machining, CNC guarantees consistency and repeatability throughout the production run. This builds unwavering quality and reduces the opportunity for failure by disposing of disparities and ensuring that each part aligns with the requirements and necessities.
● Complex Geometries and Intricate Designs
CNC machining succeeds in creating complex geometries and perplexing shapes that conventional technologies view as troublesome. As a result, cutting-edge, lightweight designs that maximize performance and efficiency are now possible.
● Lightweight and Strength
Aluminum’s weight solidarity makes it an ideal material for space, automotive, and aeronautical applications. The most significant advantage of CNC machining is the production of lightweight parts that enhance airplane performance and fuel efficiency and reduce material waste.
Aluminum sheet metals advantages
● Versatility and Design Freedom
Many aluminum alloys can be machined utilizing CNC. This opens up a wide range of design options and allows components to be customized to meet specific requirements like increasing strength, resisting heat, or protecting against corrosion.
● Efficiency and Automation
CNC machining makes manufacturing faster and cheaper by using machines to do the work instead of people. The
& automotive industries can compete better because they can save money, grow quickly, and work faster.
Cons of Aluminum Metals
- Though aluminum offers extraordinary quality for its weight, it has lower quality contrasted with steel, confining its use in applications requiring phenomenal strength and burden-bearing limits.
- Aluminum is milder than steel, making it more prone to scratching and mutilation underneath the influence, which might impact its snappy appearance.
- Even with the way that aluminum is consistently savvy contrasted with different metals, it can be more expensive than steel, especially in high-volume age or concentrated applications. Though high warm conductivity can be significant, it can prompt speedier warm trade, which may not be appealing in specific applications where cover is required.
- Aluminum surfaces are powerless to scratching and scratched spots, which can lessen their appearance over the long haul if not genuinely gotten or finished.
- Aluminum can be more difficult to weld contrasted with steel because of its higher warm conductivity and the game plan of an oxide layer, requiring particular welding systems and equipment.
- When in touch with dissimilar metals inside the closeness of an electrolyte, aluminum can contribute to galvanic disintegration, which might require careful material assurance and surface treatment.
- Aluminum mixtures may include creep, which is the ceaseless bending underneath a consistent stack after some time, particularly at raised temperatures. This restricts its use in high-temperature applications where slither obstruction is fundamental.
Alt tag: aluminum sheets disadvantages
Uses of Aluminum Sheet Metals
Sheet aluminum metals are fundamental since they offer solid, lightweight solutions for the industrial, automotive, and aerospace industries. These parts, which engineers make with high accuracy, support the strength and integrity of airplane structures. CNC machining ensures the production of mind-boggling structures and profiles, satisfying the demanding details of design principles for everything from fuselage components to wing parts. Below are some generic components.
Alt tag: uses of aluminum metal sheets
Structural Components
- Wing spars:
- Fuselage frames:
- Landing gear parts:
- Bulkheads:
- Main Struts:
- Empennage:
- Torque Links:
Engine Components
- Compressor blades and cases
- Turbine blades:
- Pistons:
- Engine housings:
Alt tag: application of aluminum sheet metal in different fields
Interior Components
Interior parts are among the primary components made of aluminum that has been CNC-machined. These interior parts include instrument boards, seating sections, and other significant airplane and vehicle lodge cabins.
- Seats:
- Brackets and control panels:
Other Applications
Besides primary and interior parts, engineers machined the aluminum to track down many different purposes in the business. These applications could include, yet are not limited to, landing gear parts, motor parts, etc. Such as Sensors, actuators, and instrumentation components.
- transmission housings
- suspension parts
- brake components
- Computer chassis
- PCB enclosures
- prosthetic components
- implantable devices
- medical equipment enclosures,
- Smartphone frames
- camera mounts
- audio equipment parts
What is The Basic Price of Aluminum Metal Sheeting
The fundamental expense of aluminum sheet metal can move comprehensively contingent upon a couple of factors like the blend alloy, thickness, size & measure, price, and market prices. Basically, aluminum metal costs normally run from $1 to $4 per pound for standard grades like 3003 or 5052. Special mixes or custom sizes might order greater expenses. It’s judicious to check with metal suppliers or online commercial centers for current assessing information in light of your specific necessities.
Conclusion
All in all, aluminum sheet remains a foundation material in current assembling and development, offering unmatched flexibility, strength, and accuracy & execution. With its excellent properties, including high solidarity-to-weight proportion, erosion obstruction, and pliability, aluminum keeps on upsetting industries going from aviation to shopper gadgets. By understanding the complexities of sheets, from their manufacturing procedures to their far reaching applications, architects and planners can open boundless opportunities for development and headway. As we plan ahead, aluminum stays at the very front of material science, driving advancement and molding our general surroundings with its unlimited potential.
FAQs:
Which type of sheet aluminum is best?
Deciding the “best” sort of sheet relies upon the particular necessities of your application, including elements like strength, erosion opposition, formability, and cost. So it’s fundamental to assess your necessities cautiously and select the most appropriate alloy in like manner.
What can aluminum metal be used for?
Sheet metal is used in various fields like construction, medical, marine, aviation, aerospace, industrial, and consumer goods to make diverse types of products.
How much weight can an sheet hold?
The weight that an aluminum can hold relies upon different variables, including its thickness, alloy type, and manufacturing technique. Thicker sheets and certain aluminum composites can uphold heavier burdens, while more slender sheets are reasonable for lighter applications.
Can an sheet be bent?
Indeed, aluminum can be bowed utilizing different strategies, including press brakes, roll framing, and pounding. The simplicity of twisting relies upon the thickness and combination of the sheet, as well as the ideal curve range and point.
Can an sheet be welded?
Aluminum an be welded utilizing strategies like TIG welding or MIG welding. In any case, welding aluminum requires explicit gear, mastery, and methods because of its high warm conductivity and the arrangement of an oxide layer on its surface.
Can an aluminum be cut?
Aluminum Sheets can be cut using different strategies, including shearing, laser, waterjet, and plasma cutting. The decision of cutting strategy relies upon variables like the thickness of the sheet, the ideal accuracy, and the intricacy of the cut.
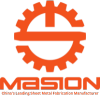
Send Your Inquiry Today



+86-18969433502

sales@sheetmetalmasion.com