What is Melting Point of Copper: A Comprehensive Guide
Copper is flexible and serves many different functions in different industries. This is important for CU melting temperature to be observed in certain situations. Awareness of melting point allows for its manufacturing, recycling and metallurgy. Keep reading and uncover the facts on what is melting point of copper, methods to melt copper, applications, and much more. Let’s get started!
Table of Contents
ToggleWhat is the Melting Point of Copper in Celsius?
The copper melting point is a transition from solid phase to liquid state that occurs at some particular temperature. This temperature is crucially important for industrial purposes.
Sr. No. | Key Material | Melting Point (°C) | Cu Melting Point Fahrenheit (°F) | Melting Point Kelvin (K) |
1 | Copper | 1,085 | 1,984 | 1,357 |
Importance of Melting Point Of Copper Metal in Industrial Applications
Understanding the copper melting point is crucial in several industrial applications:
- Metallurgy and Alloy Production: Copper decides formability or malleability and is used to produce the still widely appreciated alloys like bronze and brass.
- Electrical Wiring and Components: The melting point in the case of copper wire is relatively high and this makes the electrical systems very durable.
- Manufacturing and Casting Processes: This makes it possible to model delicate parts with copper’s high melting point.
- Thermal and Heat Applications: They main reason for using copper is because of their high temperature conductivity which is conspicuous in heat exchanger and radiators.
Factors Impacting Cu Melting Point
- Presence of Alloying Elements: It can effectively change the melting ability by adding elements to it such as zinc or tin into the mix.
- Environmental Conditions: States of pressure, and degree of atmosphere can also influence melting point.
Melting Point of Pure Copper
Pure copper melts consistently at 1,984°F (1,085°C). This makes it quite valued in many industrial applications since it behaves predictably under heat. It has a relatively high melting point indicating its potentiality to withstand huge thermal stresses without losing its structural integrity.where it must withstand significant thermal stress without losing its structural integrity.
Melting Point of Copper Alloys
Bronze is primarily made up of copper with tin that melts at about 1,742°F to 1,832°F (950°C to 1,000°C). In general it can be said that addition of elements causes reduction in melting temperature as seen in copper.
Sr. No. | Alloy | Melting Point (°C) |
1 | Pure Copper | 1084.62 |
2 | Brass (varies depending on zinc content) | 870 – 950 |
3 | Bronze (varies depending on alloying element) | 830 – 1040 |
Atmospheric Pressure Vs. Copper Melting Temperature
Put differently to say the least atmosphere significantly influences the temperature at which copper would melt. At normal atmospheric pressure level copper has a melting point estimated at around 1984 F (1085 C). This mineral’s melting point might shift depending on the pressure. For example one may lower or increase if there is a decrease or increase in pressure respectively.
How Impurities Influence Melting Point of Copper?
Impurities in copper also affects greatly its own melting points and those of other metals for that matter too. Sulfur harmful impurities such as lead or oxygen also bring down metal’s melting temperatures besides changing some physical properties it could have taken.
Understanding Copper Grain Size
Annealed Copper Grain Sizes
Heat treated copper with the purpose of reducing internal stresses generally results in larger grain size as compared to the as rolled copper. This thus increases ductility and decreases hardness of the copper to enable it undergo through a number of processes as required in manufacturing.
ASTM Copper Grain Size
The American Society for Testing and Materials (ASTM) has standard measurements of copper grain size which in a way lessen variability in properties. The grain size standards of the ASTM are very significant in maintaining the quality of various products through production processes.
Average Grain Size for Copper
The mean grain size of copper alters with treatment and use, but it generally ranges between a few micrometers and several hundred micrometers. Small grains give high strength and hardness while large ones confer ductility.
Hall-Petch Relationship
This relationship is represented by the Hall-Petch relation which illustrates increased strength in a metal as the grain size decreases. In other words, smaller grains have more obstacles for impeding dislocations’ motion that makes them stronger as compared to larger grains. In copper for instance, the mechanical properties can be enhanced by controlling the grain size through heat treatment or cold working.
Grain Boundary Energy
Grain boundary energy is the energy at the interfaces of the grains of copper. High grain boundary energy results in high diffusion rates and reduces the melting point, thus making the material unstable at high temperatures. Controlling this energy is essential for improving the stability and performance of copper.
Microstructural Heterogeneity
Grain size variation and impurities are defined as microstructural heterogeneity in copper. It affects features including strength, malleability, and melting behaviors. Smaller grains are more effective in terms of strength while larger grains are more effective in terms of ductility. The control of this heterogeneity helps improve properties and applications where copper is most needed.
Dislocation Density
In copper, dislocation density refers to all the dislocations present in the crystalline structure. A material with higher dislocation density will be stronger but also fracture more readily under load. For example, cold working increases dislocation density while annealing lowers it. This density must be balanced, however, in order to achieve the correct level of strength and ductility.
Diffusion Rates
Diffusion rates are used to explain the mobility of atoms within the copper lattice particularly across the grain boundaries. Higher rates can reduce the melting point of copper and vary the mechanical characteristics. The control of diffusion through alloying and heat treatments helps to preserve the physical characteristics as well as the functionality of copper.
Surface Energy
Surface energy is the energy in excess of the bulk energy at the surface of the material. Reducing the surface energy improves the stability and performance of the melting point. High surface energy can cause oxidation and degradation. Decreasing surface energy with coatings or treatments enhances durability and lifespan characteristic of the material.
Stress Concentration
Stress concentration is defined as stresses at localized region in copper like around a notch or a hole. These areas can cause localized melting and failure under thermal stress. Copper’s integrity is maintained by reducing stress concentrations through design and heat treatment.
Methods You Can Employ for Melting Copper
Electric Resistance Heating
Electric resistance heating works by passing electric current through a resistive material which melts the copper. This method makes sure that the material recieves heat evenly which is very efficient.
Induction Heating
Electromagnetic field to melt/heat copper. In its working, it involves creating electrical currents in the copper which in turn heats up the material. This procedure enables accurate control of temperatures and can therefore be used in processes that demand correct temperatures for melting.
Electron Beam Melting
The high energy electrons collide with copper and transfer most of their kinetic energy into heat energy. This method is preferred for use where cleanliness is paramount for instance in aviation industry or production of medical instruments.
Laser Melting
Concentrated lasers widely melt copper in laser melting. The use of the laser makes it easy to control the heating process and reduce thermal distortions. This melting copper technique is widely used in industries like additive manufacturing and industries that require high precision.
Furnace Heating Copper
Conventional furnace heating requires the use of high temperature furnaces for the purpose of melting copper. This method is good for large scale operation and it can process large amounts of copper. It is commonly used in industries because of its dependability and potential.
Oxy–fuel Torch
The Oxy-acetylene torch is another tool that involves the use of oxygen and fuel gases to produce enough heat capable of melting copper in a matter of seconds. This method is transportable and flexible and used often in field repairing and constructions.
Salt Bath Melting
Salt bath melting involves placing copper in molten salt and this heats and melts the copper uniformly. The molten salt ensures that the thermal conductivity remains constant thereby minimizing the temperature differences in the melted copper thus improving the quality of the molten copper.
Microwave Melting
Microwave melting employs the use of microwave radiation to heat and melt copper. It provides energy efficiency and speed and is, therefore, best suited for small scale and experimental purposes. Application of special susceptors where the microwave energy is absorbed and then transferred to the copper.
Heaters Heat Copper to Melting Point
There are various options for heaters, including ceramic or metal ones which could be used to raise the temperature of copper until it gets molten. Such heaters give a steady and controlled heating value suitable for labs among other industrial set ups.
Infrared Heating
Another method used for heating copper until it melts is known as Infrared Heating. This allows fast localized heating making it good for situations like localized melting. It is widely applied in surface-treating and coating technologies.
Vacuum Melting
In vacuum melting, the actual copper is melted in a vacuum and this limits contamination and oxidation. This method yields high purity copper making it for applications in electronics and other high precision industries.
Direct Electric Heating
Direct electric heating involves passing electric currents through copper which can easily melt due to the currents. This method is rather simple and yields good results, however, it is more suitable for small scale of melt.
Suction Casting
Suction casting involves melting copper and then applying vacuum pressure to form the metal into molds. It is suitable for making intricate forms and tiny parts that are widely employed in jewelry fabrication and machine parts industries.
Plasma Arc Melting
Plasma arc welding uses plasma as a heating source that involves a plasma torch to melt copper at high temperatures and at a very short time. As the name implies, this method is quite appropriate in recycling and refining processes because a large amount of copper needs to be melted at once.
Hot Isostatic Pressing
Hot isostatic pressing entails exerting high pressure and heat upon copper to melt and shape it. Here, the characteristics of the material are improved by making it denser and less porous to meet or exceed the requirements of high performance applications.
Solar Furnace Melting
Solar furnace melting utilises concentrated solar power to melt copper. Melting chocolate in a mold using solar energy is an environment friendly and renewable way of melting chocolates as compared to other methods.
Cold Crucible Melting
Cold crucible melting carries out the melting process using an electromagnetic field in a manner that does not contaminate the copper. This method is suitable for high purity copper which is used in many electronics and modern fabrication industry.
Arc Melting Copper
Arc melting involves the usage of electric arcs that produce high heat and can be used to melt copper in the driest way possible. This is a process mostly adopted by metallurgical industries where materials are heated to high temperatures and melted almost instantly.
How to Melt Copper: Step-by-Step Process
Gather Materials and Equipment
First, assemble all related supplies and tools that would be needed for the process. To solder copper, you will require copper pieces which can be scrap copper or pure copper and you may also use flux to help in cleaning. For equipment, you need a crucible made of ceramic or graphite, heat source such as furnace, torch or induction heater, gloves, goggles and apron. A set of tongs to grab the hot crucible and a mold in case you decide to pour the molten copper.
Prepare the Workspace
Position the equipment on a heat resistant surface and ensure that all the tools and other materials are well within reach. First of all, safety comes first, so ensure that your environment is clean and prepared for the melting process.
Place Copper in Crucible
Place the copper pieces into the crucible. Make sure that before it is filled with copper, the crucible should have been cleaned well so that no moisture is retained inside it. Impurities can be eliminated using Flux if any has been sprinkled over the top of Copper. This is helpful in attaining a cleaner melt.
Preheat the Furnace or Heat Source
Preheat your chosen heat source according to instructions based on the heat source you have selected. If using a furnace, adjust the temperature for melting point of copper to the desired level, which is about 1085°C (1985°F). For torches or induction heaters, check if they are working well and if they are at the right power level. The use of preheat is important to facilitate proper melting.
Begin Heating the Copper
Heat the copper by putting the crucible into the pre-heated furnace or pointing the heat source towards the copper. Pay attention to the temperature and the condition of copper. It should start to melt as it gets to its melting point. It is important to maintain a consistency in the use of heat in order to achieve the desired melt.
Stir the Molten Copper (Optional)
You can also decide to stir the molten copper using a graphite rod or any other similar tool as the melting process proceeds. This aids in uniform melting and can mix with the flux in a better way as well. As the impurities float on the surface, you can use a ladle to skim them off to get a purer molten copper.
Pour the Molten Copper
If your mold requires preheating before use, make sure it is set at right temperature to achieve optimum melting point of copper. With tongs, pick up the crucible and pour the molten copper steadily into the mold so as to prevent splashing. At this stage, one has to take caution because it requires high amount of heat. Remember always to put on protective clothing when handling the crucible.
Allow the Copper to Cool
Allow the copper to cool and harden in the mold without removing it. This guarantees the formation of copper in the correct shape without defects. This stage requires a lot of patience to achieve the best quality final product.
Remove the Solidified Copper
After cooling, the copper should be removed from the mold and checked for any faults or impurities. A thorough examination helps determine if melting was properly done and if indeed, such copper is fit for its purpose.
Clean Up
When done, the crucible and other instruments applied in the method have to be washed. There should be no copper or flux left on the working surface. Again, clean your protective gear properly for future reuse. When your workplace and tools are clean, the achievement of right temperature for melting point of copper will be easier and safer.
Melting Point of Metals Chart and Copper – Revealing Difference
Sr.No. | Metal | Melting Point (C) | Compared to Copper |
1 | Aluminum | 660.50 | Lower by 424.12°C |
2 | Gold | 1064.18 | Lower by 20.44°C |
3 | Iron | 1538.00 | Higher by 453.38°C |
4 | Lead | 327.43 | Lower by 757.19°C |
5 | Silver | 961.90 | Lower by 122.72°C |
6 | Tin | 231.90 | Lower by 852.72°C |
7 | Mercury | -38.83 | Lower by 1123.45°C |
8 | Tungsten | 3422.00 | Higher by 2337.38°C |
9 | Platinum | 1768.90 | Higher by 684.28°C |
10 | Nickel | 1455.00 | Higher by 370.38°C |
11 | Magnesium | 650.00 | Lower by 434.62°C |
12 | Cobalt | 1495.00 | Higher by 410.38°C |
13 | Chromium | 1857.00 | Higher by 772.38°C |
14 | Molybdenum | 2623.00 | Higher by 1538.38°C |
15 | Tantalum | 3027.00 | Higher by 1942.38°C |
16 | Barium | 850.00 | Lower by 234.62°C |
17 | Sodium | 97.72 | Lower by 986.90°C |
18 | Potassium | 63.50 | Lower by 1021.12°C |
19 | Calcium | 842.00 | Lower by 242.62°C |
20 | Beryllium | 1287.00 | Higher by 202.38°C |
21 | Titanium | 1668.00 | Higher by 583.38°C |
22 | Lithium | 180.54 | Lower by 904.08°C |
Conclusion
Insights on what is melting point of copper metal and its alloys is a crucial for many industrial applications. To make copper perform better, it can depend on how atmospheric pressure influences this element along with impurities presence as well as grain size. The choice of appropriate melting methods is crucial for reaching the desired efficiency and outcome. Our first-class custom electrical enclosures ensure your copper-based systems are safe and secure with the highest possible level of protection.
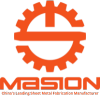