Powder Coating, on Aluminum; Exploring the Thickness, Quality Assessment and Salt Spray Testing
Table of Contents
ToggleThe process of powder coating aluminum involves the application of a flowing powder onto metal surfaces to create both a visually appealing and protective layer. This coating enhances the resistance to corrosion, durability and overall appearance of aluminum products. Due to its performance compared to liquid paint and its environmental friendliness powder coating is widely utilized across various industries such as consumer goods, automotive manufacturing and architectural design.
What is the Ideal Thickness for Aluminum Powder Coating?
Typically the thickness of aluminum powder coating falls within the range of 60 to 80 microns. Various factors come into play when determining the thickness required based on factors like intended usage, environmental conditions and performance standards. Below is an in depth overview of considerations when selecting the thickness for aluminum powder coating;
Factors Influencing Thickness
Application Type;
For applications where enhanced protection against wear impact damage and corrosion is crucial opting for a coating (approximately 100 to 150 microns) may be more beneficial, for industrial machinery and components.
Practical Uses, in Construction;
When it comes to features like window frames and exteriors a thickness ranging from 60 to 120 microns is commonly applied to ensure longevity without compromising aesthetics.
Everyday Items;
For items such as furniture and household appliances a coating thickness of 50 to 100 microns strikes a balance between protection and visual appeal.
Exposure to the Elements;
Outdoor Environments;
Components exposed to weather conditions like UV rays, rain and pollution often benefit from a coating for enhanced protection against deterioration.
Indoor Settings;
Interior surfaces with exposure to elements may require only a thin coating for adequate coverage.
Meeting Performance Standards;
Preventing Corrosion;
Thickening the coating enhances its ability to act as a barrier thereby improving resistance against corrosion.
Enhancing Durability. Wear Resistance;
Coatings with thickness demonstrate resilience, against wear and tear.
Measuring Coating Thickness;
- Using Magnetic Thickness Gauges;
These tools are used on surfaces to determine the thickness of magnetic coatings. However for aluminum surfaces eddy current thickness gauges are commonly employed.
- Utilizing Eddy Current Thickness Gauges;
Specifically designed for conductive coatings, on aluminum and other non ferrous metals these gauges provide accurate measurements without causing damage to the coating.
- Exploring Micrometers;
While commonly used for quality control micrometers can be valuable, in determining the combined thickness of both the substrate and the coating. By subtracting the substrates thickness one can obtain the coatings thickness.
- Consistent Application;
Ensuring a powder coating application is crucial to achieve the desired thickness across all parts. Mistakes, in application could lead to spots and eventual failures.
Curing Process Importance;
Proper curing is essential for the coating to reach its thickness and functional properties. Incomplete curing may result in thickness weak adhesion and reduced durability.
The typical thickness of an aluminum powder coating varies between 50 to 150 microns based on application needs and environmental factors. Accurate measurement and adherence to industry standards are key to ensuring the coating performs as expected providing protection, longevity and an attractive finish to the aluminum substrate. Proper surface preparation, application techniques and curing methods are essential for achieving the thickness and ensuring durability of powder coated aluminum.
How is the Quality of Aluminum Powder Coating Tested?
Various evaluations are conducted to assess the quality of aluminum powder coatings ensuring they meet performance standards while providing protection and visual appeal. Tests cover aspects like adhesion strength, thickness consistency, visual appearance, mechanical properties and resistance, to corrosion.
Here is an, in depth look, into the tests conducted to evaluate aluminum powder coatings;
Objective;
Confirms that the coating meets the required thickness for performance and durability.
Testing Procedures
- Solvent Rub Test;
Approach; A cloth soaked in solvent is used to rub the coating surface to assess if it softens or dissolves.
Goal; Ensures that the powder coating has achieved its resistance to chemical factors by confirming complete curing.
- Differential Scanning Calorimetry (DSC);
Procedure; Evaluates the properties of the coating to verify compliance, with temperature and curing duration.
Purpose; Provides an analysis of the curing process to ensure treatment.
- Impact Resistance Test
Using an impact tester a weight is dropped onto the surface to determine if delamination or breakage occurs.
Reference; ASTM D2794.
Aim;
Assessing how the coating withstands damage, from impacts.Various methods are utilized to assess the effectiveness of aluminum powder coating in ensuring adhesion meeting thickness specifications achieving curing and withstanding mechanical, chemical and environmental factors. These tests validate that the coating will maintain its aesthetic qualities, in conditions. Manufacturers can assure the quality and reliability of their powder coated aluminum products by adhering to standards and meticulously conducting these evaluations.
The Powder Coating Safety Protective Measure
Safety precautions to be observed when dealing with powder coating materials include the following measures;
Personal Protective Equipment (PPE)
Respiratory Protection;.
Dust Masks/Respirators;
Employees should utilize N95 or P100 respirators to protect against inhaling powder particles that may lead to issues.
Proper Fitting;
Ensure that respirators fit well are maintained properly. Are replaced when necessary.
Eye and Face Protection;
Safety goggles protect the eyes from dust and powder particles when handling and spraying substances.
Face Shields;
These offer protection, in situations where splashes or flying particles may occur.
Skin Protection;
Gloves;
Chemical resistant gloves safeguard the hands from cleaning chemicals and powders as pre treatment procedures.
Coveralls;
Workers should wear flame coveralls to protect their skin and clothing, from powders and solvents.
Screens; Utilize high efficiency particulate air (HEPA) filters, in dust collection systems to capture particles effectively.
Materials to Prevent Static Buildup;
Utilize coatings and materials that help prevent buildup on surfaces within the powder coating area.
Regular Maintenance and Inspections;
Routine Maintenance;
Conduct maintenance checks to ensure that spray guns, booths, ovens and ventilation systems are functioning properly.
Inspections;
Regularly inspect equipment, for signs of wear, damage or any potential hazards.
Awareness and Training
Use of Personal Protective Equipment (PPE) and Emergency Procedures;
It’s important to train employees on how to handle apply and store powder coatings safely.
Emergency Preparedness;
Employees should be well versed in evacuation procedures and fire drills.
Hazard Communication;.
Labeling and Signage; Clearly label containers and areas, with danger warnings and instructions.
Safety Data Sheets (SDS);
Make sure that SDSs are available, for all powder coatings and chemicals used and ensure that employees understand how to read and use them.
To avoid fires and explosions make sure to wear the protective gear (PPE) set up effective ventilation and dust control systems, handle and store equipment safely offer comprehensive training and keep an eye, on employee well being. By implementing these safety measures companies can minimize risks ensure compliance with safety protocols and maintain an healthy workplace, for all staff involved in powder coating operations.
Can the Salt Spray Test be Passed by Aluminium Powder Coating?
When applied and dried correctly aluminium powder coating has the potential to pass the salt spray test. The salt spray test, also known as the salt fog test is a method used to assess the corrosion resistance of materials. Here is a detailed explanation of how and why powdered aluminium coating can endure this test;
Understanding the Salt Spray Test
During the salt spray test the coated aluminium sample is exposed to a controlled saline mist environment. This environment replicates conditions to evaluate the protective properties of the coating. A fine mist is generated by spraying a saline solution usually a 5% sodium chloride solution in a test chamber maintained at temperature and humidity. The duration of the test can vary from 24 hours, to over 1,000 hours based on industry standards and specific coating requirements.
Factors Contributing to Salt Spray Test Results
Proper Surface Preparation;
Before applying powder coating it is essential to clean and prepare the aluminium surface. This preparation typically involves degreasing, cleaning and applying a conversion coating such, as phosphate or chromate to enhance adhesion and corrosion resistance.
To enhance the adhesion of the powder coating surface impurities can be. A textured surface can be achieved through methods, like sandblasting or abrasive blasting.
Quality of Powder Coating;
The performance of the coating in salt spray tests is significantly affected by the choice of powder material. High quality powders such as polyester or blends of epoxy and polyester provide resistance to corrosion.
The powder formulation should be able to withstand factors like moisture, salt and temperature fluctuations.
Application Process;
For coverage and optimal protection it is essential to apply the powder coating and at the recommended thickness (usually between 50 and 150 microns).
Electrostatic spray deposition (ESD) is commonly used for distribution of powder particles on the aluminum surface.
Curing Method;
Proper curing is crucial, for ensuring that the powder fuses, flows and forms a layer. Heating the aluminum to the temperature for a set duration is necessary to achieve this outcome.
The ability of a coating to resist corrosion can be affected by imperfections, in the coating, like brittleness or poor adhesion, which may stem from either curing or insufficient curing.
By following all procedures from surface preparation to curing aluminum powder coating can successfully pass the salt spray test. A passing result in this test demonstrates the durability and reliability of powder coating as a technique for protecting aluminum against corrosion. Various industries such as automotive, architectural and marine that rely on coated aluminum components benefit from the lifespan and improved performance provided by high quality powder coatings.
What Types of Powders are Used for Aluminum Powder Coating?
Types of Powders, for Powder Coating Aluminum
The process of powder coating aluminum involves using types of powders with characteristics tailored to meet diverse application needs and environmental conditions. The main types of powders commonly used for aluminum powder coating are detailed below;
Powdered Epoxy;
It is widely used due, to its properties, resistance to chemicals and ability to adhere well. These powders create a finish that can withstand impacts, abrasions and harsh chemicals. However they are not ideal for use as they may discolor and become chalky when exposed to UV light. Their protective features make them well suited for applications such as in appliances, automobiles and industrial settings.
Polyester Powders
They are preferred for applications because of their UV stability and ability to withstand various weather conditions. They help maintain the beauty and functionality of aluminum over time by offering high gloss retention and color stability. Polyester coatings are commonly used in components, outdoor furniture, automobile parts and other items exposed to weather conditions due to their flexibility and impact resistance.
Polyurethane Powders
They are combine the properties of polyester and epoxy powders. They exhibit chemical resistance, mechanical strength and outstanding UV resistance making them suitable, for use. Polyurethane coatings are frequently employed in heavy duty machinery, exterior architectural elements and automotive applications.
They provide a finish that can withstand weather related wear.
Acrylic Powders
Acrylic powders boast color retention, clarity and smoothness. These coatings are ideal, for use due to their UV resistance. They are commonly used in furniture, electronics, automotive topcoats and other applications requiring a finish. While not as long lasting as polyurethanes or as chemically resistant as epoxies they do offer a finish.
Hybrid Powders
Blending polyester and epoxy resins creates powders that combine the features of both coatings. These powders exhibit properties compared to pure polyester coatings along with enhanced adhesion and weather resistance. They are cost effective options for various interior applications, like shelves, office furniture and general industrial uses.
Fluoropolymer Powders
Polyvinylidene fluoride (PVDF). Other fluoropolymer powders find application in settings where chemical and weather resistance’re crucial.
These specialized powders are ideal, for notch coatings and demanding industrial uses due to their exceptional strength, ability to withstand UV rays and resistance to weathering effects like chalking and fading. Fluoropolymer materials are commonly applied to aluminum facades, window frames and other outdoor building parts that require lasting performance.
Triglycidyl Isocyanurate (TGIC) Polyester Coatings
TGIC is a particular kind of powdered polyester coating. They use TGIC as a crosslinker, and these coatings are strong and have a high impact resistance. They are well known for outdoor applications because of their exceptional weather resistance and offer exceptional protection against UV radiation and severe weather.
Furthermore, these coatings provide strong chemical opposition to cleansers and solvents. It guarantees durability and low maintenance to provide a long-lasting gloss, and these coatings are renowned for their exceptional adherence to aluminum and other metal substrates. Because of their flexibility, they can bear deformation without breaking, which is useful in applications of heat expansion and contraction. These coatings also offer a beautiful, glossy finish that comes in a range of colors and gloss levels.
Nylon powder coating
Powder coatings made of nylon are extremely resilient and adaptable. They are known for minimal friction and superior abrasion resistance. These coatings are perfect for high-wear applications like culinary utensils, gears, and bearings because they offer a durable, protective covering that can endure substantial wear and tear. Their low friction quality prolongs the life and improves the performance of coated objects by reducing wear between moving components.
Nylon powder coatings provide high chemical resistance and they are frequently employed in automotive and industrial settings. Nylon coatings are an adaptable option for a wide range of sectors.
When it comes to Nylon powders they excel in applications that call for resistance to abrasion and impact. Their durability makes them suitable for purposes such as tool grips, mechanical parts and conveyor rollers. Nylon coatings offer finishes that can endure rough handling and frequent use.
Antimicrobial Coatings;
They stop the development of bacteria, fungi, and other germs on surfaces. These coatings offer an additional degree of protection, which makes them ideal for places like public areas, food processing plants, and hospitals where hygienic conditions are vital. The antibacterial qualities improve safety and cleanliness by limiting the growth of dangerous germs.
It is enhancing the quality of the atmosphere and reducing the need for frequent cleaning and upkeep.
Issues with Powder Coating Aluminum
Aluminum powder coating occasionally poses a number of difficulties and issues that may compromise the finish’s longevity and quality. The following list of eight typical problems with powder coating, along with possible fixes, may help:
Defective Stickiness
The powder coating is peeling or flaking due to poor adhesion to the metal substrate.
Poor surface preparation and impurities such as filth, oil, or grease are the main causes of this issue. Ensure the metal surface is well-cleaned and degreased, and use the proper pre-treatment, such as conversion coatings for phosphate or chromate. You should confirm that the curing temperature and duration meet the requirements specified by the powder manufacturer.
The Effect of Orange Peel
The powder coating’s surface has an uneven, grainy appearance, making it look like orange skin. The main causes of this issue are Improper application methodology, differences in coating thickness and less-than-ideal curing circumstances and improper formulation of the powder.
Modify the technique and settings of the spray cannon to obtain a consistent coating thickness and ensure that the curing oven is heated evenly. Use powder formulations that reduce the amount of orange peel.
Casting Issue
The problem is that the coated surface develops tiny holes or pinholes that compromise its protection and appearance. The common reasons for this issue are gas or air trapped in the coating or substrate, an overly thick layer, contamination, or moisture. The solution is to heat the metal to release any gas or trapped air. You can use many thinner powder applications rather than one big layer. When applying, keep the area dry and clean.
Cracking or Crazing
The powder coating loses its visual appeal and protective qualities due to cracks or crazes, Inadequate or excessive curing, Incongruous powder compositions
The solutions adhere to the suggested temperature and curing schedule. You can use the proper coating thickness.
If there may be bending or impact on the substrate, use powders made for elasticity.
Differences in Color
Variations in hue or tone throughout the coated area. The main causes are differences in application methods, variations in the availability of powder or batches, and irregular curing temperatures.
Solutions are to make sure that application methods and equipment settings are consistent.
To ensure consistency, use powder from the same batch. During curing, monitor and maintain a constant oven temperature.
Chalking
The powder coating’s surface turns chalky or powdery over time, especially after being exposed to the outdoors and the causes are UV deterioration of the coating, and the wrong kind of powder used in the wrong environment, The solutions are to make use of powders that are resistant to UV light, including polyester or fluoropolymer blends. You can use a clear topcoat to offer even more UV protection.
Impulsive
The powder coating has impurities or foreign particles embedded in it, which lowers the quality of the finish. Unclean or dirty surfaces, contaminants in the application environment and storing powder improperly are the main causes of this issue.
Let’s talk about its Solutions try to keep the application area dust-free and ventilated appropriately.
Make sure the surface is properly prepared before coating.
Handle powder carefully to avoid contamination, and store it in a clean, dry location.
Different Thickness of Coating
Issue is differing coating thicknesses result in inconsistent look and protection and the reasons are incorrect spray gun settings, inaccurate application method and changes in the geometry of the substrate
When we look for its solutions, try to adjust settings and calibrate spray device to ensure consistent application or teach operators how to use methods consistently.
You can use many passes of powder coating to attain a consistent thickness on intricate shapes.
The quality and longevity of aluminum powder coatings can be enhanced by producers by comprehending and resolving these typical issues. To overcome these obstacles and produce a high-quality finish, it is essential to use appropriate powder compositions, optimize application methods, maintain consistency in curing times, and prepare surfaces properly.
In Conclusion
Aluminum powder coating stands out as a method for enhancing the look and function of aluminum goods. Its blend of strength resistance to corrosion, design flexibility and eco friendly advantages positions it as an option in sectors. Manufacturers can optimize the benefits of powder coating by familiarizing themselves with the process types of powders available and their applications in creating durable aluminum components.
The choice of powder, for aluminum powder coating is dictated by the needs of the application. Including environmental exposure levels desired appearance attributes and performance requirements.
By selecting the powder manufacturers can ensure that the coated aluminum parts meet the standards, for performance, aesthetics and longevity. The distinct advantages provided by each powder type enable a tailored method for aluminum powder coating that’s suitable, for a range of sectors and uses.
FAQs for Aluminum Powder Coating
- How do you prepare components for powder coating?
If you want to ensure optimum adhesion between the metal and coating, make sure components are prepared by washing the surface to remove impurities and existing paint.
- Is it possible to powder coat aluminum?
It is attainable to powder coat metal as it is a typical powder-coated surface. It delivers longevity and a range of color options.
- How long does powder coating can last?
As we know powder coatings have a importance for being more resilient and long-lasting than other coatings. It can stay bright and vivid with less fading over time.
- What type of powder coating for aluminum should I obtain?
Powder coatings come in a combination of shapes, each with unique performance characteristics. Polyurethane coatings give flexibility and hardness while polyester coatings show great external stability and performance. Hybrid coatings deliver chemical and solvent resistance. Epoxy coatings offer good corrosion defence.
- What advantages does powder coating aluminum offer?
Aluminum offers lots of advantages such as it can be powder coated for durability, erosion and abrasion resistance, a wide range of color possibilities. It is cost-effectiveness in comparison to other coating processes. It is often used in many different industries, including building, architecture, appliances, and automobile goods.
These frequently asked questions (FAQs) highlight the advantages, concerns, and powder coating process of aluminum. These questions also emphasizing its popularity and adaptability to a variety of sectors.
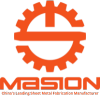
Send Your Inquiry Today



+86-18969433502

sales@sheetmetalmasion.com