Everything You Must Know About Aluminum Anodizing
Table of Contents
ToggleAluminum is a metal widely used in manufacturing products. Through a finishing process it not enhances its strength. Also improves its visual appeal.
For those seeking insights, into anodized aluminum you’ve come to the place. This article covers all aspects of aluminum anodizing, such as its characteristics, variations, surface treatments, applications, limitations and other essential information.
Properties of Anodized Aluminum:
Characteristics of Anodized Aluminum;
Let’s delve into the properties of aluminum.
Anodized aluminum boasts increased durability and strength. It provides resistance to wear and tear.
This type of aluminum is non conductive making it suitable for electronics applications as it does not conduct current.
The outer appearance of aluminum is visually appealing. Remains unaffected by harsh environmental conditions or UV exposure.
Anodized aluminum offers enhanced hardness compared to varieties.
How Does Aluminum Anodizing actually Function?
Cleaning debris or dirt from its surface is simple, with water and mild soap. Furthermore maintaining aluminum is easier than anodized versions.
Anodizing enhances the natural oxide layer of aluminum. The entire process takes place in a tank with a current.
After cleaning the aluminum components go through a treatment process to prepare them for anodizing.
Once the aluminum parts are immersed in the anodizing tank with an electrolyte electricity is applied. The choice of electrolytes used depends on the type of aluminum anodizing process being employed.
The aluminum components serve as the anode connected to the terminal of the power source while a cathode is linked to the terminal within the anodizing tank.
The anodizing process commences, by passing a current through the electrolyte from a power source. This causes electrons to depart from the surface of the aluminum leaving charged aluminum ions behind.
Simultaneously electrons leaving the cathode aid in generating oxygen ions with charges. These oxygen ions migrate towards the aluminum. Combine with aluminum ions resulting in increased durability and aesthetic appeal.
Initially a barrier layer forms on the surface of the aluminum parts, without any pores. Subsequently as layer formation progresses pores begin to appear on the surface of aluminum.
The voltage required for the anodizing process typically falls, between 1 and 300 volts DC with some instances where it may range from 15 to 21 volts. When thicker coatings are needed the voltage range is adjusted accordingly for a process. Generally the anodizing current varies between 30 to 300 amperes per meter.
Types of Aluminum Anodizing
Below are a few methods used in aluminum anodizing;
Anodized Die Cast Aluminum
Anodizing die cast aluminum involves applying an oxide layer to parts manufactured through the die casting method. The surface imperfections and porosity resulting from die casting can present challenges in the anodizing process. It is essential to clean and treat the surface before anodizing die cast aluminum to remove impurities and enhance its quality.
Modifications in anodizing parameters like voltage, current density and electrolyte composition may be necessary to suit the characteristics of die cast aluminum.
Camouflage Anodizing;
Camouflage anodizing is a technique that includes adding patterned finishes on aluminum surfaces. This method is commonly used for creating designs resembling patterns such as camouflage or custom made designs. Achieving camouflage anodizing demands control, over the process, including dye selection using masking techniques and blending colors effectively.
The result is a product that can be customized for uses, like outdoor gear, firearms and sports equipment.
Conductive Oxidation Anodizing;
Conductive oxidation anodizing, also referred to as Type II sulfuric acid anodizing is a method that enhances the resistance to corrosion and surface properties of aluminum. By immersing the aluminum part in a sulfuric acid solution and applying a controlled current an oxide layer is formed on its surface.
This process facilitates adhesion for coatings or treatments. Is commonly utilized in sectors such as aerospace, automotive and electronics.
Hard Anodizing Type III;
Hard anodizing or Type III anodizing creates an oxide layer on aluminum surfaces for increased durability. This method involves temperatures and voltages compared to anodization techniques resulting in a sturdy coating that effectively resists wear.
With its characteristics hard anodizing enhances the hardness and abrasion resistance of aluminum making it well suited for various industries. For instance defense industrial equipment frequently incorporates anodizing.
Color Aluminum Anodizing
Following the creation of an oxide layer, through the anodization process the aluminum component is submerged in a dye solution to infuse pigments into the oxide layer. Subsequently the pores are sealed to preserve the color intensity and longevity. Color anodizing provides a range of color options.
You can apply it to surfaces, design elements, products, for consumers and parts used in industries.
When it comes to large scale color anodizing the process includes adding finishes to aluminum components. This technique requires tools and techniques tailored to handle the size of the parts and achieve the desired coloring. Large scale color anodizing is beneficial, for projects, manufacturing processes and industrial environments as it improves the appearance and durability of aluminum structures.
Microarc Anodizing,
Microarc anodizing, also referred to as plasma oxidation (PEO), is a surface treatment technique that creates a thick oxide layer resembling ceramic on aluminum surfaces. This process entails exposing the aluminum part to energy discharges in an electrolyte solution, resulting in a dense and tough coating with exceptional resistance against wear and corrosion. Micro arc anodizing is applied in fields such as aerospace engineering, medical device manufacturing, and high-performance industries where top-notch surface properties are essential.
Precision Anodizing
It involves a controlled process that achieves uniform thickness of the oxide layer on aluminum components. This method requires adherence to process guidelines and quality assurance measures to ensure consistent outcomes. Precision anodizing is utilized in industries like electronics, optics, and semiconductor production, where precise dimensions and surface finish are crucial.
Dual Color Anodizing;
Also known as two-tone anodizing, dual-color anodizing is a method employed to produce contrasting colors or designs on aluminum surfaces. This technique involves masking or treating areas of the aluminum component before anodizing to achieve varied colors in specified regions. Dual color anodizing provides flexibility in design and customization options, enabling the creation of finishes for applications such as consumer electronics, custom automotive parts, and decorative elements.
Comparasion with Powder Coating about the Thickness and Salt Spray Test
When we look at anodized aluminum and powder coating, in terms of coating thickness and their resistance to salt spray tests, it’s crucial to take into account the features and performance qualities of each coating method.
Powder coatings are known for their ability to safeguard against corrosion, impact, and abrasion due to their consistency. Aluminum anodizing excels, in corrosion resistance in outdoor environments.
Anodized coatings can undergo salt spray tests (per ASTM B368) to assess their durability and resistance to corrosion, often meeting industry standards.
In comparison, powder coatings provide protection against corrosion when applied correctly on prepared metal surfaces. The thickness of the powder coating plays a role in determining its performance in salt spray tests. Powder coatings are also tested using salt spray testing standards (ASTM B117) to evaluate their durability under conditions.
One notable difference is that powder coatings generally create a layer compared to anodized coatings, making them suitable for applications where increased physical protection and longevity are desired.
Surface Preparation & Pre-Treatments:
This is done to properly clean the surface of the aluminum parts. The preparation and treatments done on aluminum involve steps.
Cleaning:
The contaminants or oils present on the surface of the aluminum parts are referred to as organic oil which are removed using suitable alkaline oil cleaners. It is important to remove the organic soil before carrying out the anodizing process. This is because the debris may interfere during the process which will directly affect the efficiency of the process. Additionally, the organic soil may start reacting with the electrolytic solution and leave marks on the anodized aluminum. Once the cleaning is done, rinse the aluminum surface with cold water.
Degreasing;
Degreasing involves the removal of the greases or oils from the surface of the aluminum using organic or alkaline solvents. During the process, the residues that are formed due to machining or touching the aluminum are efficiently removed. It is usually done by directly spraying the aluminum surface with alkaline or organic solvents. Once degreasing is done, the aluminum surface is rinsed carefully with flowing water.
Etching:
Etching is a process that is done for the elimination of roughness and the creation of an even, smooth upper aluminum surface. It is done using two ways. One is by using an acid solution while the other is done by using an alkaline solution. The non-anodized aluminum may contain small grains on its upper surface which are referred to as distributed. These grains are removed during etching to create a smooth surface, lacking any imperfections. Acid etching is done using a mixture of surfactant and phosphoric acid. On the other hand, a surfactant, caustic soda, along with a chelating agent, is required for the alkaline etching. After completion of the etching process, rinsing is done.
Desmutting:
As the name suggested, desmutting is the removal of the smuts that are the residuals of the other alloying elements present on the surface of non-anodized aluminum. During desmutting, smuts are removed using mineral inorganic acids. For this purpose, commonly nitric acid is the ideal choice. Once the smuts are removed, the aluminum is rinsed carefully with water.
Factors Affecting the Outcome of the Anodized Process:
The following are the main factors that can greatly affect the outcome of the anodized process.
- Aluminum alloys can badly affect the anodized operation. Like other metals, aluminum contains varying amounts of different alloys. These alloys can affect the anodizing process and form an uneven layer on the surface of aluminum.
- The defects on the aluminum surface can result in an undesired finish after the anodizing process.
- It affects the properties of the aluminum surface, including the density of the anodic layer.
- In addition to the concentration of electrolyte, its temperature also affects the anodizing process. On the other hand, if the temperature is high, it ends up speeding up the reaction and formation of a less durable outer coating.
- The Longer the duration, the thicker the oxide layer. However, it can lead to porosity, leading to the formation of a great number of pores on the surface of the aluminum parts.
- The voltage and electric current used in the anodizing process play a role, in its outcome. If the voltage and electric current are high, then it results in the formation of a thick oxide layer. But it can also increase the chance of the burning of aluminium, which can spoil the whole anodizing process
Anodizing Aluminum Advantages:
- It increases the durability of aluminum. It provides exceptional corrosion. As a result, anodized aluminum offers a longer lifespan.
- Aluminum anodizing is an environmentally safe process because it does not release harmful chemicals in the environment.
- Anodizing aluminum is perfectly safe for human health because it is non-toxic and never decomposes.
- The anodized aluminum offers admirable color stability. Due to anodized coating, the surface never undergoes peeling or chipping.
- This procedure improves the aesthetic importance of the aluminum parts and makes them eye-catching.
- The anodized aluminum surfaces are easier to maintain and clean compared to untreated aluminum surfaces.
- Anodized aluminum finds application in the construction sectors due to its improved resistance to weather conditions and long lasting nature.
Different Processes of Anodizing Aluminum
Type I: Using Chromic Acid;
Chromic Acid Anodizing involves immersing aluminum in a solution of acid to create a soft oxide layer, on the surface. This coating offers resistance to corrosion. Helps paint adhere well. It is commonly seen in aerospace and military uses.
Type II Treatment;
It results in a harder oxide layer compared to chromic acid anodizing delivering resistance to corrosion and durability. It finds applications across industries for decorative purposes.
Durable Anodizing
Hard Anodizing delivers an oxide layer. This layer is thicker than Type II. This process creates surfaces with corrosion resistance and high wear resistance making it suitable for demanding applications like aerospace components and automotive parts.
Precision Thin Film Sulfuric Acid Treatment
Thin Film Sulfuric Acid Anodizing is a technique within sulfuric acid anodizing that aims to achieve a uniform thin oxide layer, on aluminum surfaces.
This method is employed when a precise and controlled thickness of oxide is needed, for purposes, or when minimal dimensional alteration is preferred.
Transparent Anodizing
Transparent Anodizing, a form of sulfuric acid anodizing creates a see-through or slightly tinted oxide layer, on aluminum. This technique preserves the look of aluminum while offering protection against corrosion. It is commonly applied in decorative settings.
Phosphoric Acid Anodizing
Phosphoric Acid Anodizing utilizes a phosphoric acid solution as the electrolyte. This method is primarily used to enhance bonding by improving the adhesion of adhesives and primers to aluminum surfaces. The process generates a crystalline oxide layer that enhances surface adhesion.
Boric Sulfuric Acid Anodizing
Boric Sulfuric Acid Anodizing is a variation of sulfuric acid anodizing that incorporates a quantity of acid into the electrolyte solution. This adjustment boosts properties of the coating, such as hardness and resistance to wear. It finds application in scenarios where distinct performance attributes are necessary.
Bright Dip Anodizing
Bright Dip Anodizing serves as a chemical treatment, for surfaces that is sometimes categorized as part of the anodizing process. It entails submerging aluminum components in a chemical bath to enhance their surface appearance through brightening or polishing.
Bright dip anodizing is not intended for forming a protective oxide layer as seen in anodizing methods; rather it is primarily utilized for enhancing the appeal of the surface.
Applications of Anodized Aluminum:
Let us uncover the key applications of anodized aluminum.
- It is used for the formation of roofing, panels, door frames, windows, etc.
- In kitchenware, anodized aluminum is an ideal choice for the manufacturing of cookware and other utensils used in the kitchen because of its food-safe properties and aesthetically pleasing appearance. These commonly include pans, pots, and other food preparation equipment.
- It is a good option for the manufacturing of medical instruments such as surgical equipment.
- Aluminum anodizing is light and long-lasting. Therefore, it is used for the manufacturing or production of sporting goods such as cameras, head lamp,camping gear and, bicycle frames, etc.
- It is a great option for the manufacturing of automotive parts in the automotive industry. These include engine components, decorative elements, trim pieces, etc.
- It is greatly scratch-resistant and widely used for the manufacturing of consumer electronics such as tablets, laptops, smartphone cases, etc.
Stages in Anodizing Aluminum;
Anodizing aluminum is a method which consists of stages;
Cleaning and purification stage;
At this stage, the aluminum elements are cleaned to remove dirt, oil or impurities.
This cleaning process may involve techniques like alkaline cleaning, solvent cleaning or etching to achieve a surface.
Preparation;
Following the cleaning phase the aluminum is typically rinsed to remove any residues from the steps. This rinsing step is crucial, for ensuring adhesion of the layer.
Anodizing Bath;
The aluminum piece which has been cleaned is then submerged in a solution as an anode. A cathode is also introduced into the solution and a current flows through them.
In this process, oxygen ions being discharged to form aluminum oxide. The thickness is controlled by modifying the voltage and time of the anodizing procedure.
Coloring & Finishing Techniques:
Electrolytic Coloring:
The electrolytic coloring is specifically used to give colors to the anodized aluminum. It is done after the anodizing aluminum process is completed. Consequently, the metallic salts start filling the pores present on the surface of the anodized aluminum until they are filled properly. It provides a more UV-resistant surface finish compared to the dip coloring. The final color of the anodized aluminum depends on the type of metallic salt used during this coloring technique.
Dip Coloring:
It is the most common coloring technique. During this process, the anodized aluminum is immersed in a bath of solution consisting of organic dyes. As the anodized aluminum is dipped, the porous surface of the aluminum starts absorbing the dye.
After the anodized aluminum is exposed to water it forms bubbles on its surface causing the dye absorption process to halt.
Treatment used for Post Anodizing
After the anodizing process, we utilize post-anodizing treatments for aluminum, which are summarized below:
Sealing;
Sealing acts as an anodizing treatment strived at maintaining color of anodized aluminum.
In this method the pores, within the material are sealed through hydration. There are two processes involved in sealing;
Hot Water Sealing;
This involves immersing the aluminum in boiling deionized water typically at temperatures ranging from 96 100°C. While highly effective this method consumes energy.
This treatment seals the pores of aluminum at temperatures by using chemical additives like nickel acetate. The reaction between nickel salts and the layer of anodized aluminum results in sealing. While reducing color fading risks this approach may pose hazards due, to nickel salts presence.
Cleaning and Maintenance
Anodized aluminum needs cleaning to get rid of leftover debris. It’s important to pick the cleaning approach based on the type of finish, for a clean. Avoid using chemicals like acid or alkaline cleaners when cleaning aluminum as they can harm the surface making it rough. If you’re unsure about a cleaner test it on an area first.
After applying the cleaner and cleaning the surface make sure to rinse it with water to remove any cleaning residue that could affect the appearance over time if left behind. Once rinsed use a cloth to dry the anodized aluminum surface. Be cautious not to apply pressure while cleaning to prevent any shape alterations.
Limitations
There are some limitations with aluminum anodizing that should be noted. Achieving the color as anodized aluminum can be challenging due to variations in alloy compositions and other factors. Properly sealing the pores of aluminum is crucial, for performance, durability and corrosion resistance.
Improperly sealing pores, during the anodizing process can lead to reduced effectiveness.
It’s important to handle and dispose of the chemicals used in anodizing aluminum with care to prevent any harm.
When anodized aluminum is damaged, it’s challenging to repair as it often requires replacement, which can be both time-consuming and costly.
Summing Up
Choosing a company like Masion for aluminum anodizing services is crucial due to their expertise in working with aluminum alloys and providing customized solutions for individual needs.
Utilizing equipment and offering customer service are key factors in achieving successful anodizing results. Masion excels in professionalism, technical knowledge and meeting customer needs. Contact us today to discover our high-quality product range.
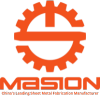
Send Your Inquiry Today



+86-18969433502

sales@sheetmetalmasion.com